But gaining that visibility has its challenges. Typically, manufacturers rely on historian software to capture process data from plant floor controllers. However, limitations of size and speed in traditional historians have forced manufacturers to make difficult choices about what information to gather. For slower processes, pulling data points off a machine every second may provide adequate visibility. When it comes to high-speed processes, such as during certain chemical flashing, metal manufacture, paper or packaging processes, a manufacturer can’t afford to compromise between the speed of data capture and resolution.
Machine-level historian applications like the FactoryTalk Historian ME module are capable of capturing every event on a machine, at high-speed and at full resolution. The module is designed to stand alone, with a limited software footprint and no server connections, and it features a backplane that can gather information from up to four controllers. As a result, the module provides critical coverage with no impact by potential server or network disruption.
Get it Right When it’s Regulated
Access to uninterrupted coverage is a significant opportunity for any manufacturers seeking operational improvement – but for regulated industries, that visibility is mission-critical. Retaining documentation of a range of process variables is deemed so important, to both human health and environmental safety, for example, that manufacturers must provide documentation of certain process variables to secure regulatory approval.
Pharmaceutical manufacturers live and breathe these types of requirements. A pill manufacturer must be able provide the FDA with proper documentation or risk throwing out millions of dollars of product.
“Anything we can do to minimize risk in our business impacts our bottom line. Even if our product passes all of our own very stringent quality tests, we have to be able to provide regulators all the information from our processes,” says Jim O’Brien, the Director of Quality at a North American pharmaceutical company. “A unit that captures every single event – time, temperature, moisture – on our machines, minimizes the risk that we’ll fall short of that regulatory requirement.”
Similar regulations apply to tracking and reporting on a range of industrial processes that impact the environment. Losing greenhouse gas emissions data could result in substantial fines and potential profit losses. In a water/wastewater processing plant, operators must be able to provide proof that water quality properties are being constantly monitored. Implementing a reliable system for data capture is critical, but the environment of the plant often makes it difficult to guarantee the level of reliability needed.
One West Coast desalinization plant has overcome this challenge using a machine level historian application. The plant pumps salt water at high pressure through filters to remove the salt. The filters need to be changed on a regular basis, and operators must track variables like pressure, back flush, and motor or power faults. The multiple pumping stations operated using a wide network, which struggled with limited bandwidth capacity and intermittent network coverage.
“We had a lot of data to track and a system that goes offline a lot,” said Dale Evans, plant manager. “In order to improve our process, provide the right documentation, and lower the cost of system maintenance, we needed a solution that would virtually eliminate downtime. That’s why we chose the FactoryTalk Historian ME application. It provided the uptime and reliability that we couldn’t achieve with a PC-based historian.”
Make Your Best Guarantee
But it’s not just regulators whose demand a constant stream of reliable information. It’s not uncommon for a customer to ask an OEM to provide an uptime guarantee. This can be a challenging proposition when the OEM doesn’t have the ability to control or monitor the use and maintenance of its machine in the end user’s facility. Embedding a machine-level historian into products can help prevent this issue.
The technology allows for high-speed, granular data collection needed for preventative and performance maintenance. It also provides accurate data capture – a prerequisite for creating the performance analytics that enable an OEM to provide excellent warranty and customer service.
Recently an OEM to the medical technology industry replaced multiple machine-based chart recorders with a FactoryTalk Historian ME application. The historian module was used to track time-series information from more than 1,000 sensors. Compression and reporting features enabled by the historian application provided plant managers with data faster and with more granularity than they were ever able to achieve previously – all with zero data loss.
“Our customers really need both speed and pinpoint accuracy in processing their products,” said Tim Mahoney, plant manager. “If a line goes down because of an error or malfunction, it can cost them millions of dollars in production costs, not to mention the damage it can do to their reputation in such a highly-regulated industry.”
In addition to providing ink and paper cost savings, the application allowed the OEM to demonstrate significantly better results in speed, reliability and performance to its customers. Mahoney’s staff was also pleased with the speed and ease with which they were able to install and configure the machines onsite, saving their customers a significant amount of downtime. And, since the module is not server or network connected, Mahoney knew he could guarantee customers 100% uptime – a key factor in his ability to meet his customer’s needs.
Take it to the Extreme
Manufacturing operations don’t always occur in a state-of-the-art facility or a temperature-controlled warehouse. Refiners must capture production data off oil rigs in the middle of the ocean. Mobile barges run process controllers in environments too extreme for most plant-floor infrastructure. However, capturing accurate information reliably at those remote locations is no less important to such manufacturers than to a peanut-processor in Georgia or an automobile manufacturer in Tennessee.
FactoryTalk Historian ME was built with difficult and extreme environments in mind. With a solid-state chassis, no moving parts, and a limited software footprint, the module can service sites where temperature, vibration, or distance makes it impracticable to install a server. The unit provides up to 10ms scan rates at full resolution with virtually no down-time or maintenance helping provide improved reliability in data capture, and significant savings in maintenance and installation costs.
For one North American ice manufacturer the solid-state historian unit has been an ideal solution. It configures automatically to the ControlLogix controller at the site and can withstand the vibration and temperature extremes that would destroy or burn up an onsite PC. For mobile uses, like a rig or a remote barge, the unit can then forward that information to cell towers or in harbor, enabling manufacturers to upload collate data to a centralized server on land.
Get the Right Insight
Manufacturers in range of industries are collecting, transforming and integrating their historical operational data into useable production information to gain insight into where those improvements need to be made.
For a Midwestern consumer products manufacturer, capturing motor data off its high-speed web press was critical to the quality of the finished product. In addition, the ability to make inline adjustments to process variables like paper tension or paper position would reduce machine maintenance, raw material loss, and the costly downtime associated with a paper roll breaking during production.
“Prior to the implementation of the historian module, we had trouble acquiring as much information as we needed to isolate quality issues or downtime,” said plant manager Dan Reilly. “We ended up doing a lot of shotgun troubleshooting, wasting a lot of time and money, because we couldn’t get the detail we needed. The new historian is able to handle very high speeds at the level of granularity we need to help us analyze our process.”
For more information visit http://discover.rockwellautomation.com/historian
Companies in this Article
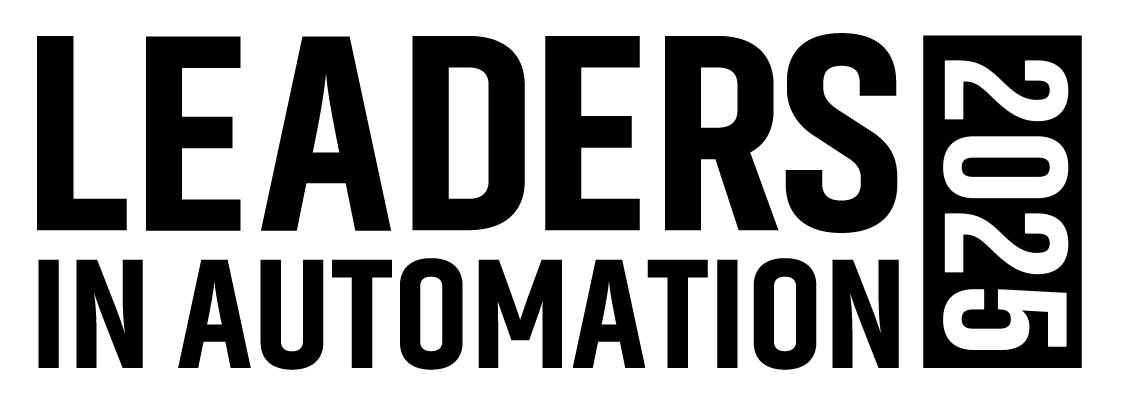
Leaders relevant to this article: