The term “mechatronics” is starting to be heard with greater frequency in the packaging industry. Just last September, for instance, at the Pack Expo trade show, automation supplier Bosch Rexroth Corp. (Hoffman Estates, Ill.) heralded its booth display as illustrating “Innovation in Mechatronics.” A big part of the company’s justification for that claim was Indra Motion for Packaging control, its open control system that was being exhibited with new software. This expanded solution offers a PackML compliant, IEC61131-3 programming environment and handles precise synchronization, camming, registration, electronic gearing, collating, robotic path planning, dynamic belt synchronization and other aspects of automated packaging line operation.
Added to this was the “mechatronics training simulator,” a mobile training device that allows students to simulate a number of functions such as those connected with pneumatics, electronics and control, to create hypothetical systems in which the individual components operate synergistically to optimize the overall system. Put these and other elements of the display together, and it becomes clear that Bosch Rexroth has a pretty strong claim to the word “mechatronics.”
That said, what precisely is this concept? Most of us feel we have a pretty good idea of what mechatronics is and can recognize it when we encounter it, but if asked to define it. . .well, for many of us that’s a different story. In that respect, it is analogous to the famous description of jazz: “I know it when I hear it.”
The subject need not be so mysterious. The word was originally coined in 1969 by Tetsuro Mori, an engineer with Japan’s Yaskawa, by combining the words mechanical and electronics to symbolize a holistic approach to design. Rather than design the mechanical and electronic or control elements of a machine or system separately, why not create these elements together? The result, he maintained, will often be more robust, higher performing and more economical machines and systems.
Some four decades later, this fundamental insight remains true even though today’s machines and systems are generally much more complex than those of 1969, and the concept of mechatronics has expanded to encompass this complexity.
Listen, for instance, to the working definition used by Arun Jain, vice president of motion control business in the United States for Siemens Industry Inc., Alpharetta, Ga. “Mechatronics incorporates several fields of classic physics such as mechanical dynamics, kinematics, materials and electromagnetism, with more modern engineering fields such as control design, software programming, micro-electronics, modeling and simulation techniques.
“Mechatronics is thus the science of integrating a wide variety of concepts of the above fields, to create a new electro-mechanical design, with improved characteristics or desired behavior.”
Sounds impressive, but to what extent are packagers attuned to, and employing, the concept?
“We’re definitely seeing it used by designers and systems engineers in the packaging industry,” says Jain. He says understanding of the concept varies among industries, but he feels that the consumer packaged goods (CPG) market is relatively sophisticated in this regard. Here too, however, it varies.
“In packaging we’ve seen mechatronics used more on the high-end, high-speed machinery and not so much on the simpler machines because those are chiefly adaptations of earlier machines,” Jain says. Similarly, companies that build for the domestic U.S. market are more likely to employ the concept than companies that build primarily for export, he says. The latter are often looking primarily for low cost and simple operation.
More from existing assets
Jain observes that "end users are trying to get more out of their assets,” and many of them are employing mechatronics to help them do that, particularly in their quest for greater flexibility, improved productivity and higher energy efficiency.
Those are themes that strike a receptive chord with John Morehead, vice president of business development for Dunkermotoren USA Inc., Elgin, Ill., a supplier of fractional horsepower motion control solutions. He says his company has embraced the concept, with positive results.
“As an example, what previously may have required a large, expensive master control connected by bulky, expensive cables and connectors to motors in a system can now be controlled by master intelligence built into one motor driving other smart slave motors through a simple CANopen wire network,” says Morehead.
Morehead alludes to cost, and this is a key consideration for Siemens’ Jain as well. He says that when it comes to mechatronics, the bottom line is. . .well, the bottom line. “From my perspective mechatronics is all about economics,” Morehead says. “In the packaging industry competition is fierce. With global players and domestic players, big and small, all competing in the same space, the success of builders and/or users is tied to how they can push total cost of ownership down with greater throughput.”
Its a sentiment with which Bill Dinham, application engineer for Beckhoff Automation LLC, Burnsville, Minn., seems to be in agreement. Modern electronic motion control solutions have enabled packaging OEMs (original equipment manufacturers) to perform many functions that were previously handled by large, complex mechanical assemblies with much simpler and smaller mechatronic systems. This can lead, he says, to a reduction in parts and maintenance, to machines with a smaller physical footprint, and to lower overall costs coupled with higher performance and—extremely important in today’s environment—greater flexibility.
As a concrete example of some of these benefits, Dinham points to Koch Pac-Systeme GmbH, a Beckhoff customer in Pfalzgrafenweiler, Germany that produces customized blister pack machines. It recently introduced its KBS-KF blister machine with an integrated Delta robot for automatic product feeding and an ultrasonic cut and seal device that performs both operations in a single station. This eliminates the so-called “victim film” that had been necessary on previous models. Robotics, logic and motion control are all integrated within the Beckhoff TwinCat control platform operating with EtherCat as the fieldbus system.
The machine, which offers a fast format change and a very high cycle rate (up to 30 cycles/minute), consists of eight stations. The process starts with a film roll and a film take-off device, after which is positioned a heating station where the transparent blister film is heated. This is followed by the blister-forming station. The subsequent product-insertion section can be designed to the customer’s requirements for either manual packing or for automatic packing with the KRH-D Delta robot.
Then comes the card inserter, which places an inlay card in the blister. The sealing station, in which the cover film is drawn off the roll, fed and sealed to the blister, with a punching device that separates the sealed blister packs by longitudinal and lateral cutting, comes next. This had been two successive steps in previous iterations of this basic design.
“The integrated ultrasonic cut and seal device, which combines sealing and punching into a single process step, was developed in collaboration with Maschinenfabrik Spaichingen and is an absolute innovation in the packaging machine market,” claims Karl Kappler, engineering manager of Koch Pac-Systeme. “It makes do without the expensive victim film that previously had to be fed between the sonotrode and anvil to prevent damage to the punching tool. Around 20 to 30 percent of the consumable materials can be saved by eliminating the victim film.”
Quick changeover
The packaging machine features demanded today by customers, says Jürgen Welker, general manager and head of automation and service for Koch Pac-Systeme, “are flexibility, quick changeover times and a wide range of variants. Just-in-time production is also found increasingly in the non-food sector. For that reason,” he continues, “we must ensure, by means of mechanical engineering and appropriate automation, that the end customer can pack not just one product, but an entire range of products.”
Welker says that the company’s machines, like the KBS-KF, are designed to meet these needs through “modern control and servo drive technology, convenient operator control and the use of high-quality components. Format changes are also possible at the push of a button. The user merely enters another program number in order to retrieve a different set of parameters, which adjusts the machine to the new conditions.”
Welker points out that the integration of the Delta robot into the KBS-KF blister machine was a significant challenge. The blister film is guided through the forming and sealing station by a grab chain. Then, in the insertion zone, the robot must pick up the non-oriented item to be packed from a continuous conveyor belt running parallel to the chain and place it into the blister. Though the chain is cycled and can thus be stopped briefly for insertion into the three parallel blisters, the conveyor belt runs continuously. On the one hand, the conveyor belt must be synchronized with the cycle of the blister belt and, on the other, the precise position of the non-oriented item to be packed must be detected and its coordinates integrated into the position of the robot’s gripper.
The necessary synchronization to the conveyor belt for picking up and setting down work pieces is handled by the TwinCAT ‘Flying Saw’ and ‘Cam Plate’ software libraries. Koch Pac-Systeme uses an image processing system in order to detect the precise position of the item to be packed. As Welker notes, the image processing system is also integrated with the PC-based control and software platform. “We import the graphic data into the controller by Ethernet in order to implement the conveyor tracking, which we use with the robot. The graphic data are converted into position data in the controller, on the basis of which we can determine where the product is at that moment.” The robot then grasps the released item and places it into the blister.
Simplified setup
Mechatronics also features prominently in the design approach of automation supplier Festo Corp., Hauppauge, NY, particularly in terms of motion solutions. In part this consists of pneumatic and electric drives that are equipped with all relevant mechanical, power supply and data interfaces, ensuring that different technologies can be combined in one system.
The aim is to speed and simplify the setting up of complex material handling and positioning systems. However, John Holmes, Festo’s segment manager, food & packaging industry, stresses that his company’s commitment to the approach goes beyond motion and ranges from individual components to complete solutions. In this, he feels, they are in sync with the needs and desires of the market.
“We are certainly seeing more mechatronics-type products employed in the typical packaging facility. Nearly every aspect of machine performance is affected,” he says, “particularly flexibility.” As a prime example of this last quality he cites the products of Festo customer XPAK USA, LLC in North Brunswick, N.J.
XPAK is a packaging machine builder with a taste for innovation. Although that sounds like a marketing slogan, in XPAK’s case, it is a business strategy. “To thrive in the crowded packaging market, we knew we needed an edge,” says Juan Ortiz, vice president business development for the Americas. They believe their V-PASS product can provide that edge.
The V-PASS, or Variety Pack Assembly System, mixes bottles to create variety packs for large retailers. Previous methods could create 25 to 30 trays per minute, but the V-PASS system can create about 45 trays per minute. It can be quickly reprogrammed to create different variety pack combinations, and it is priced within the range expected by most contract packagers who perform this type of work.
Interestingly, the V-PASS, and a subsequent robotic system designed to process different sized bottles in the same production run, represents a collaborative design effort across the supply chain. So, not only does it benefit from XPAK’s efforts at mechatronic design, it also incorporates designs—in some cases mechatronic—from a variety of supplier-collaborators. Festo, for example, provided the variable gripper for the new system’s robot. “This approach has allowed us to create more productive and more flexible systems while still keeping costs under control,” says Ortiz.
Collaborative design across the supply chain. Is that the next stage in mechatronics? That may seem to be stretching the boundaries of the concept, but as Arun Jain observes, “Its boundaries are not well-defined, and some may say they are unlimited.”
Greg Farnum is a Contributing Editor for Automation World.
For more information:
Beckhoff Automation www.beckhoff.com
Bosch Rexroth www.boschrexroth-us.com
Dunkermotoren USA www.dunkermotoren.com
Festo www.festo.com/us
Siemens Industry www.usa.siemens.com/packaging
Sponsored Recommendations
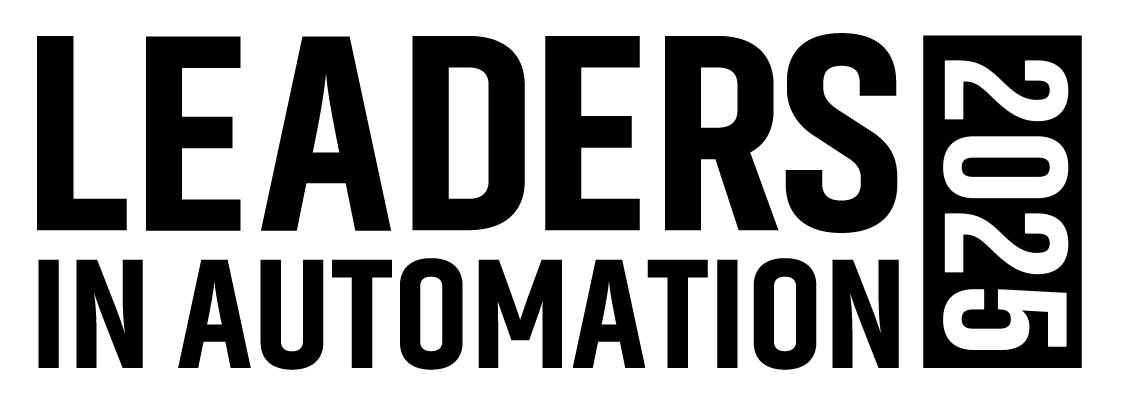
Leaders relevant to this article: