Experienced packaging professionals know that buzzwords, like rock bands, can dramatically and rapidly rise and fall in popularity. Still, the noise of publicity can sometimes obscure a strong, vitally useful signal.
Among the buzziest of today’s buzzwords is mechatronics. Originally denoting the joining of the mechanical and electronic design efforts into a single holistic approach to design, it has evolved just as automated systems have evolved, and now incorporates control architecture, software and other key aspects of automation today.
It is a concept that wasn’t much employed until about a decade ago when it began creeping into the lexicon of automation vendors, major consumer packaged goods manufacturers, and some packaging machine builders. It’s no coincidence that by then flexibility and integration had emerged as not just talking points but key concerns of packaging equipment builders and users.
Packagers were striving to meet ever increasing customer demands for flexibility, and greater integration of various aspects of an automated system was clearly seen as one of the main roads toward that end. It was then that mechatronics began to emerge as a way to move integration and its ensuing benefits from the packaging line to the design process itself.
That emergence makes perfect sense to William Henderson, business development manager for Siemens Industry, Inc. (www.usa.siemens.com/packaging), Alpharetta, Ga., a champion of the concept. He notes that an integrated, mechatronic approach to design allows all facets of the design to be evaluated and optimized. He adds that by completely analyzing the machine prior to installation, the optimization is possible during the design phase of a machine. . . as opposed to the installation phase, yielding a host of performance, time and cost benefits.
Tom Jensen, manager of OEM business development for drive and automation supplier Lenze Americas Corp. (www.lenzeamericas.com), Uxbridge, Mass., concurs. He adds, “What we are seeing today is that more OEM customers are getting on board [with mechatronics], demanding the cost savings and operational benefits of an integrated and synergistic approach to machine design.”
Jensen gives a relatively simple and straightforward example of the benefits of optimizing in the design stage. Suppose, he says, you need to put a reciprocating motion on a machine, say a load arm on a case loader. His hypothetical design team evaluates two options, a crank arm and a ball screw.
“Ball screws are nice to work with because the speed commands you give it are linear,” says Jensen. “As the motor speeds up, the attached screw moves at a proportional rate depending on the pitch of the screw.” The drawback, he says, is that these are expensive devices compared to other types of actuators, and there is no ability to roll through the end of travel to get to the home position where the next cycle would start).
Crank transformations, on the other hand, “are very simple to build, but are not easy to control speed-wise because they are sinusoidal. One revolution of a motor turning a crank causes the speed at the output to oscillate.”
Cranks vs. ball screws
Jensen postulates using a servo to control the exact position of the actuator, and software to correct, control and linearize the speed of the crank, making it functionally identical to the ball screw. The same software can be used to control the ball screw. The design team is thus left with a series of trade-offs.
In terms of power, the power transmission of a ball screw is relatively constant, whereas the power transmission of a crank is a function of the angle of the lever arm.
In terms of space, the crank occupies a fairly large area compared to a ball screw. As for initial cost, the ball screw is considerably more expensive than the crank. And then there’s the matter of roll through—in a reciprocating motion a crank can roll through to retract the actuator, saving energy and dollars on a long-term basis.
The question thus becomes, which set of characteristics best suit the needs of the target market segment and the overall goals of the OEM. He notes that using the mechatronics design approach, aided and speeded by modern design analysis software (an increasingly vital part of the mechatronics approach), can enable you to nail down your optimal design before any construction takes place.
Jensen’s mechatronics benefits mantra is faster, better, and—crucially—cheaper. As for cheaper, along with the cost factors mentioned in the example above, he says that machines created through this design methodology often cost less to produce and maintain because they typically have fewer parts. He stresses that the ability to right-size parts during the design phase is a long term cost advantage.
Frank Langro, manager of product management at Festo U.S. (www.festo.com/us), Hauppauge, NY, agrees. “By making use of integrated sizing tools components can be matched to application and performance data, eliminating oversizing and the added associated costs with that.” He adds that the mechatronic approach, aided by today’s design analysis tools, reduces installation and commissioning time as well.
Rightsizing is a central concern for Michael Cromheecke, manager, Kinetix Motion Business, Rockwell Automation (www.rockwellautomation.com), Milwaukee, Wis. He notes, “Over- or under-sized components can add unnecessary expense.” Software, or “mechatronic design tools” as he puts it, is key to solving this problem.
“Whereas in the past, analysis required to right-size system components was so time intensive it proved prohibitive, information to design and build a more efficient, cost-effective machine is now available at your fingertips.”
The energy factor
Mechatronic design tools can add needed specificity to the energy consumption calculations Jensen spoke of.
For example, using software to compute the load weight with motion profile—that is, how far and fast a load must travel, you can then compute the energy expended per axis when you input the cost of kilowatt hours (kWh) and machine uptime for one year.
He gives the following example. “Take a rotary motor machine that runs on 11 cent per kilowatt-hour energy for 50 weeks each year, five days a week, and eight hours a day. The rotary motor will cost $315 per year per axis to run. Switch the rotary motor for a linear motor and cost is reduced to $200 per year per axis”—a significant savings for machines with multiple axes.
“Strict control of energy consumption is a standing requirement for virtually all automation systems,” notes Joel Galliher, director mechatronic systems, Bosch Rexroth Corp. (www.boschrexroth-us.com), Hoffman Estates, Ill., He stresses that the mechatronic approach, coupled with mechatronic design tools, facilitates achieving a “just right” balance: “Just enough energy to accomplish a task, move a load or complete a motion cycle.”
Galliher also stresses the significance of networked communications, a factor of much less importance when the mechatronics concept first began to emerge. It’s an aspect of mechatronics that Bosch Rexroth highlighted in its recent Pack Expo 2012 exhibit, most conspicuously in the exhibit’s working demo from its OEM partner, converting and packaging equipment builder CMD Corp. of Appleton, Wis.
The demo featured a new version of CMD’s PDI Medical Combination Pouch System, upgraded through a mechatronic design effort and embodying a range of Rexroth technology, including controllers, integrated motor-drive systems, pneumatics, and human machine interface (HMI).
With the new pouch system all key sealing data, such as temperature, pressure and time data is automatically collected for each strike of the sealer. This data can be monitored in graphical form in real-time on the machine’s HMI, and the operator can adjust sealing parameters from the HMI while the machine is running. In addition, this data is stored for up to seven days within the machine’s PLC, so that the process engineer can upload the data to an Excel Spreadsheet, for full statistical analysis.
But the benefits don't stop there. As Scott Fuller, CMD’s intermittent product line manager explains, This data is fed back into the system for each strike of the sealer, so that if a deviation trend is sensed, the machine can self-correct, to maintain a stable process.
Devil’s advocate
The champions of mechatronics make a strong case, and the examples above don’t delve into some of the major potential benefits of mechatronics, such as more flexible machines, faster commissioning, and easier maintenance thanks to simpler machines with fewer parts. But playing the devil’s advocate one could ask, if the methodology is so great why aren’t more people using it?
Lenze’s Jensen replies, “The concept of mechatronics has achieved a high degree of acceptance, but the term mechatronics lags in its adoption. The difference is that many OEMs have employed the concept over the last decade without the formal introduction of the term. These OEMs have searched out the hardware and software needed for mechatronics, sometimes even developing it themselves.”
Henderson of Siemens says, “It is hard to estimate the degree of acceptance of mechatronics; however I would say that the acceptance level is not high enough.” He includes both user and vendor communities in that statement, and believes the situation will change for a couple of reasons.
“I believe that the near future will see more graduates with mechatronics degrees,” says Henderson. In addition, there is the contagious effect of successful examples as “industry will see more machines optimized using mechatronics techniques, and the machine builders that adopt mechatronic techniques will find their machines produce more for less.”
A brain gap?
For Keith Campbell the lack of graduates with mechatronics degrees is problematic, even troubling. Campbell, an engineer and automation industry blogger, has been an active campaigner for mechatronics education and has been involved in the creation of mechatronics curricula. Today, he says, there is an “extreme shortage of engineers skilled in mechatronic design, especially in the United States. Canada, Europe and the Orient are way ahead of us on this.
“Advanced manufacturing in the U.S., he continues, is being dramatically impeded by lack of technical skills. This is much bigger than a packaging or mechatronics problem. This lack of skills impedes development, pull-through, adoption and successful implementation.
Campbell sees corporate culture as another stumbling block, with packaging OEMs often reluctant to redesign existing equipment that they have already invested heavily in. For this reason he feels that systems integrators will often be among the leaders in terms of applying the mechatronics approach to packaging equipment design. “They have the skills,” says Campbell, “have no legacy machines holding them back, and they want to switch from high risk one-offs to standardized products.”
One such company is JLS Automation (www.jlsautomation.com), York, Pa. Starting as an integrator, the company switched in 2002 to designing and building its own robotic packaging systems. “We weren’t initially in packaging machine building,” says JLS president Craig Souser. “We came to it with a clean sheet of paper. We’ve focused on design for agility where we leverage today’s robotic technology with the tools we develop in order to meet the need for greater flexibility.”
Toward that end they adopted a mechatronics approach to design. The move to mechatronics was the result not of lengthy engineering studies or reports from consultants, but because it made sense—it helped them build the sorts of agile systems they wanted to build. After all, stresses Souser, “this isn’t rocket science.”
>> Motion Control Alternative: Read how automated soup packaging challenges machine makers, who turn to electric cylinders that mimic pneumatics. Visit http://bit.ly/caseapp061
It’s not rocket science, and it’s getting easier says Matt Lecheler, motion specialist with Beckhoff Automation LLC (www.beckhoff.com/packaging), Burnsville, Minn. “Innovative mechatronic solutions which abstract extremely complex control theories and provide the development engineer with a rugged, yet easy to use toolset will continue to aid creative professionals in the development of industry altering solutions.”
Lecheler cites the consolidation of discrete components into more integrated systems like his own company’s industrial I/O, integrating many traditional sensor functionalities, as an example of that trend. It is a trend, he says, that will blur the line between where “the mechanical ends and the electronic begins.”
There is another reason to think that mechatronics practices will become more widespread in the future—one pointed out by Rachel Jacobs, mechatronics product specialist for Rockwell Automation: the reduction in the cost of computing power.
The software tools used in the mechatronic design process, tools that allow users to quickly model and simulate a variety of options, will continue to grow faster and more powerful to take advantage of computers that are doing the same. “As computers have become faster and faster,” says Jacobs, “the power of virtual prototyping has been put in the hands of the everyday user.”
With such power in their hands, we can expect those everyday users, increasingly, to employ it.
Companies in this Article
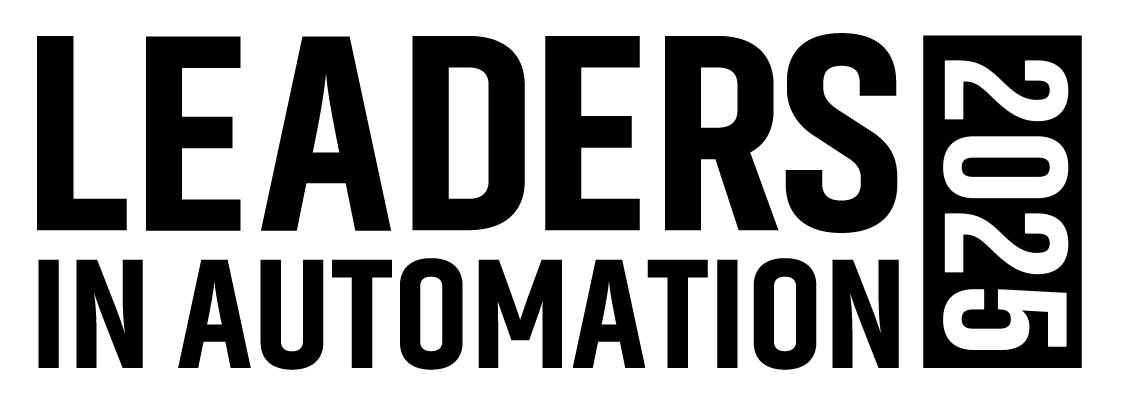
Leaders relevant to this article: