Manufacturing execution system (MES) and manufacturing operations management (MOM) applications automate manufacturing workflow. Such workflow software captures the knowledge of individuals and the data from sensors and shares it so processes are smoothed, quality is improved and knowledge is transferred—shift to shift, batch to batch or step by step.
“Broadly based, [workflow software] is an MES offering based on database, execution, product management. The idea is to turn data into profit,” says Jon Kadane, director of product marketing for AspenTech (www.aspentech.com), a Burlington, Mass. supplier of advanced process control software. He says workflow product evolution follows the requirement of what customers require: “Pharma is compliance-oriented, while chemicals customers have fewer regulations on product and compliance, but need safety and health reporting.”
>> Click here for the Top 10 Question to Ask Your Workflow Vendor
To show the range of workflow software applications and benefits, here are three stories: from a medical products manufacturer, a semiconductor manufacturer and a pharmaceutical manufacturer.
In search of ideal parameters
A leading medical products manufacturer serving a growing demographic of aging baby boomers needed to rapidly expand production capacity to keep up with growing demand. With limited space in its facility to add new lines, the company needed to focus on improving cycle time and yield by gathering more data and establishing ideal operating parameters.
“Our customer had some challenges for control on the factory floor,” says Chris Monchinski, director, manufacturing IT at Automated Control Concepts (ACC, www.automated-control.com), a Neptune, N.J.-based systems integrator. (Monchinski also volunteers as a co-chair of the ISA 95 committee.) “They had been acquired and in the acquisition there was new capital available. They wanted to advance their technology. It’s a high quality GMP [good manufacturing practices] company in an organic growth period. Many of their operations grew out of best practices developed internally. But the paper trail was not always accurate. The challenge was how to maintain quality and grow 200 percent.”
To address yield while operating under tight regulations and reporting requirements, the company needed to reduce or eliminate losses and shipment delays caused by reporting or quality issues.
ACC designed and implemented an information system based on the FactoryTalk software suite from Rockwell Automation (www.rockwellautomation.com) and ACC’s own software, processRecords. Since its implementation, the new information system has helped operators attain a 5 percent increase in equipment efficiency through better equipment utilization. In addition, the manufacturer saw an increased productivity of 20 percent over the previous system, while plant floor staffing has remained the same.
Monchinski continues, “Control over the records was essential. Trying to find a piece of paper was becoming more and more difficult. Then we needed to streamline inter-department communication. Their products are pretty custom, so that added complexity to the problem. Streamlining information flow was essential.”
The customer’s requirements were to get control of data from departments, machines and devices on the factory floor, as well as data from the quality and order management areas. The source would be either manually or automatically generated data. Another challenge was that production was a combination of discrete and process manufacturing.
Rockwell’s FactoryTalk Historian and FactoryTalk View SE gathered the data and gave visibility. Because ACC’s processRecords product is workflow-driven, it helped determine what data needed to be collected and provideed the status of a part through production.
In addition to the basic IT functionality, ACC also provided security, disaster recovery plans, fault tolerance, back up, operator acceptance and training. “processRecords basically presents forms for the operator or tester to fill out either automatically, via keyboard or by scanning a bar code,” explains Michael Blechman, ACC president.
Since installing the system, the medical products maker has seen the benefits. “They now have no paper on the factory floor. Now they have all this historical data and can make decisions about tolerances and process improvement,” says Blechman. “They had so much manual data entered into massive Microsoft Excel spreadsheets. Now it’s all in one place. Not to mention there is also a predictive maintenance tool.”
Making better semiconductors
A U.S-based semiconductor manufacturer, operating a 200,000 square-foot facility that includes 62,000 square feet of cleanroom space for wafer fabrication, was in pursuit of better control of its processes. To that end, it worked with Minnetonka, Minn. based Savigent Software (www.savigent.com), using Savigent’s Catalyst Workflow (workflow automation software) to take run-to-run control to new levels of efficiency.
The semiconductor maker’s manufacturing facilities include a six-inch (150mm) and an eight-inch (200mm) wafer fab. With these fabs, this semiconductor manufacturer has the ability to process more than 4,000 wafers a week.
Semiconductor fabs put a pattern on a wafer using a photolithography process. On subsequent layers, they put down another pattern. The layers need to overlay nicely to ensure high yield and device performance. That’s the principal technical challenge addressed by overlay control. “About three years ago, when overlay control was initially becoming an issue here, we found a ‘poor man’s solution,’ ” says a photolithography process engineer at the company.
For a given lot of wafers, the company set up what it called a restricted aligner. Out of maybe 22 photolithography layers, maybe three were designated critical to have good overlay to each other; the rest were considered non critical. The manufacturer recorded wherever that first critical layer went down on a particular step or lithography tool number. Later, when the wafers came back for the second of the critical layers, engineers made sure that the automation system forced the wafer back to the same lithography tool that had been used previously (hence the term “run-to-run control”).
This process achieved what is called “single tool overlay performance.” It was a move in the direction the manufacturer wanted to go, but not quite enough. So the company began working with Savigent to improve the process.
“In our lithography program, we were looking to make adjustments from lot-to-lot, and to gain feedback information based on output,” says the engineer. In this case, feedback is based on metrology performance metrics that company has for materials. Then, based on that metrology information, adjustments are made to the lithography tool recipe for the next lot to be processed. Integrating the feedback information from the metrology tool to the process tool was critical to making these run-to-run adjustments.”
A station controller cues up the stepper job so that an operator can run a lot of wafers through a lithography tool. The run-to-run controller is integrated to the manufacturer’s MES system, the lithography tool (through the station controller) and metrology equipment, providing the means for real-time communication of critical data such as lot numbers, routes, metrology data and more. “Now when a lot is coming to a particular lithography tool that’s about to do an align layer, information is shared by all the tools involved,” says the engineer. “Once that information is handed off, a decision is made.”
The manufacturer is now able to take what were baseline numbers with no corrections applied and look at key output metrics from the overlay tool: registration maximum, registration minimum, and mean values for both the X and Y dimensions. “With the Savigent technology, we’re able to drive those metrics to lower and lower numbers,” says the engineer. “Zero would be our ultimate goal for the mean. Max and min won’t ever go to zero, but we’re always trying to make them smaller. That shows we’ve achieved a better overlay than without the run-to-run controller.”
Since implementing the new system, the company has reduced a typical max/min value in the range of 100 nanometers into the range of 60 nanometers, an improvement of 40 percent.
Mistake proofing pharmaceuticals
Jim Cahill, writing in his popular blog, Emerson Process Experts (www.emersonprocessexperts.com), relates a story from the pharmaceutical industry. Emerson’s Michalle Adkins shared a story of one pharmaceutical manufacturer’s journey to justify workflow technology to reduce deviations, eliminate redundant work, and improve production efficiency.
The existing method of operations included paper batch records and manual data transcriptions throughout the work process. As a result, batch release times were not optimal due to the time involved with paper record reviews by the Quality and Production departments.
In addition, the effort involved in releasing a batch included many non-value-added steps. Over 20 percent of the atypical events found were due to manual recording errors. Mistake proofing the process would deliver economic benefits with faster batch release times, less required labor, and fewer quarantined or discarded batches.
The manufacturer had an existing manufacturing execution system (MES) at its various facilities, but it was centered on the historization of simple automated processes. Some examples included data trending and recording as well as comments and e-signatures. The system was minimally connected with the control system via OPC. The other major issue was the MES was customized for each site, and the manufacturer’s approach is “configure, not customize” for site validation.
Achieving the desired level of mistake proofing would require close integration between the MES and control system. This mistake proofing approach required the inclusion of complex automated and manual processes with long residence times to be incorporated automatically into the batch records. The project team was comprised of representatives from key departments with overall site leadership sponsorship. Team members represented Operations, Quality, IT, Engineering, Automation, Plant Management, Corporate Management, and Validation departments.
A key part of the process was the delivery of a prototype to visually show how mistake proofing could be accomplished and how the requirements could be realized. The team followed the Operational Excellence process and involved members from the corporate automation and information technology (IT) teams.
The prototype timeframe was three months and included the MES recipe integrated with their DeltaV control system. The team included members of Emerson’s Life Sciences consulting team to provide system setup, proof of concept criteria development, implementation & testing, presentation assistance, and proposal development for project implementation.
The Syncade MES applications in the prototype included Recipe Authoring, Electronic Batch Records, Equipment Tracking, Materials Management, Weigh and Dispense, Document Control and Archiving, and the Security and Audit application modules.
The process to develop functional requirements grew out of an initial draft developed by the manufacturer. Paper records were deconstructed with mapping all of the data entry and parameter fields in the MES and DCS. Definitions were developed for ISA88 unit operations, parameters, recipe-specific values, operator text displays, sequencing logic including manual steps, and signature requirements. These functional requirements were reviewed and revised with stakeholders representing each of the functional departments.
Based on this iterative process, the prototype was designed, built and tested. Prototype presentations were given to smaller groups by department to allow focused questions and feedback based on the perspective of the department. A justification based on the Operational Excellence process was developed and tangible benefits identified through value stream improvements in reduced document handling time, document review time, data entry time, calculations and document rework.
Other tangible benefits included reduced inventory, storage, material losses, and deviations/event comments. Intangible benefits included greater focus on true product quality, greater availability of information and the empowerment it provided staff members at all levels. This approach better organized the information to spot improvement opportunities including the identification of situations to apply Process Analytical Technology (PAT) methods. The benefits were quantified and return on investment (ROI) calculations were performed for overall project justification.
>> More MES Applications! Find more case studies, news, columns and primers on MES and MOM. Visit http://bit.ly/findmes
So, is all this workflow software? If it improves the process and the transfer of knowledge, yes.
Dan O’Brien, Honeywell’s (www.honeywell.com) director for collaborative software solutions in Phoenix, explains it this way: “Workflow is a layered-up IT word. We’re making investments that use workflow as a pillar—as, say, part of the approval process or automatic notices. Lots of applications have work sequencing or workflow built in. It also encompasses knowledge capture. This has people working to the process that’s documented, instead of by memory—knowing they’re doing the right thing at the right time.”
Companies in this Article
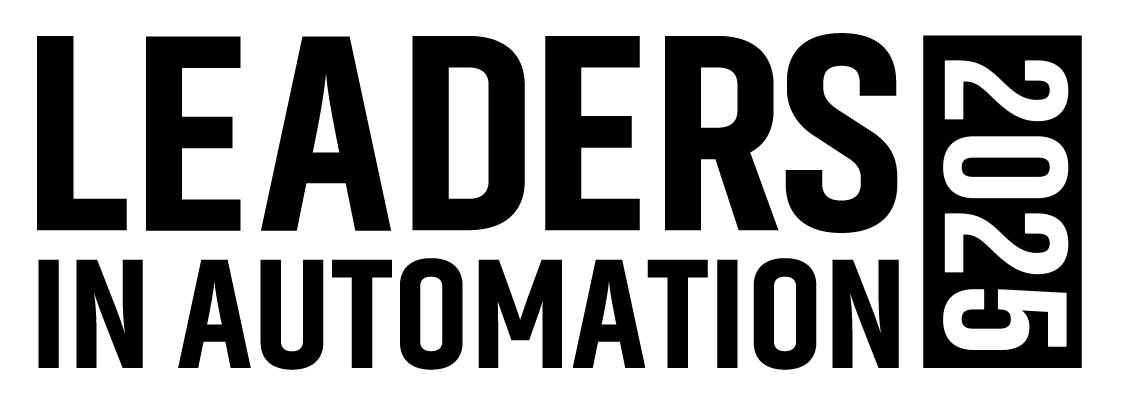
Leaders relevant to this article: