Recent global consumer economic numbers show limited demand for some textile materials in certain markets, but acrylic fibers isn’t one of them. These flexible, synthetic fibers appear in sweaters, tracksuits, glove liners and carpet components. And global demographic trends are helping this flexible fabric as consumers in the U.S. and China begin to reach retirement age and gravitate toward “relaxed” clothing, according to a recent Textile World article.
With this consistent demand, legacy acrylic fiber process plants are focusing on optimization as they extend brownfield plants well into the 21st century. Turkey-based Aksa has a legacy processing plant that it says is the largest acrylic producer in the world under one roof, and the company has been working for several years to optimize operations.
The manufacturer’s plant in Yalova, Turkey, began production in 1971 with a capacity of 5,000 tons per year and now produces just under 1,000 tons in a day. Aksa turned to Honeywell Process Solutions and its advanced process control (APC) software, Profit Suite, to achieve better plant efficiencies in 2011. Also known as multivariable predictive control (MPC), the APC software executes simultaneous control of multiple inputs and outputs for a particular process application.
“Aksa used our APC software for its solvent recovery units and those results led management to examine more optimization projects within the plant,” says Jan Jech, solution consultant for Honeywell Process Solutions.
With previous plant optimization success, Aksa developed a company benefit study in July 2013 and identified potential improvement for its industrial power plant applications. The APC project began in 2014 with a focus on three phases: selective catalytic reduction, steam temperature optimization and boiler optimization. For this power plant optimization project, the global acrylics company projected a performance guarantee of $640,000 a year, but eventually reached $2 million.
Honeywell describes its APC software as layered optimization that offers embedded regulatory control, advanced energy solutions, soft sensing, multivariate statistical analysis, real-time optimization and benefit sustainment.
The first level of optimization is the product value optimization (PVO) built into the multivariable controller (Profit Controller) and its predictive capabilities. The PVO component provides economic optimization for a process or sub-unit, based on the user’s specific product values and associated production costs. The predictive controller uses a range control algorithm (RCA) that minimizes the effects of model uncertainty while determining the smallest process moves required to simultaneously meet control and optimization objectives.
Besides evaluating process optimization savings, Aksa also identified cost savings by moving away from natural gas for its boiler combustion control. “Improved boiler responsiveness with coal reduces natural gas consumption and is only used to secure a boiler in case of process incidents,” Jech says.
For the boiler combustion optimization, APC software identified minimum variance control between the coal feeder equipment and primary air variables. The boiler load is controlled by primary air to improve flexibility while the slower coal feeders keep pulverized fuel (PF) concentration stable during transients.
“Concentration of pulverized fuel is indicated by differential pressure (dP) and dynamically coordinated by the primary air and coal feeder ratio for minimum variance control,” Jech says. The APC controller also optimized the selective catalytic reduction installed on two boilers, the steam network and boiler outlet temperature optimization.
Other optimization included a drum-type boiler with natural circulation, two steam superheating lines, and a backpressure steam turbine with nominal power of 25 MW. The steam network optimization included the entire turbine system, back-pressure turbines with extractions and pressure valves. APC software’s controller reduced the steam outlet temperature variability and increased it by 12 °C.
The software controls and coordinates process steam pressure at 20 and 6 bar across the Aksa plant. The objective is to increase cogeneration efficiency with the upgrade. “The controller runs mostly against extraction valve constraints over three installed turbines to meet optimization requirements,” Jech says.
However, acrylic fiber production at the Aksa plant is sensitive to pressure upsets, with the quality of the final product depending on steam and heat stream stability. Optimization was a challenge because of the steam power plant keeping pressure and temperatures on different steam levels, with energy efficiency being a second priority.
For these projects, Honeywell hooked into Aksa’s distributed control system (DCS) and programmable logic controller (PLC) architecture via base layer control blocks to simplify system integration. The control blocks are based on templates for certain DCS/PLC platforms and reduce customization and commissioning time.
These successful projects at Aksa clearly point to some obvious takeaways for the process industry with brownfield plants. With this discipline being democratized via software vs. APC plant experts of years past, business justifications are much easier for plant management in a demanding global economy.
Companies in this Article
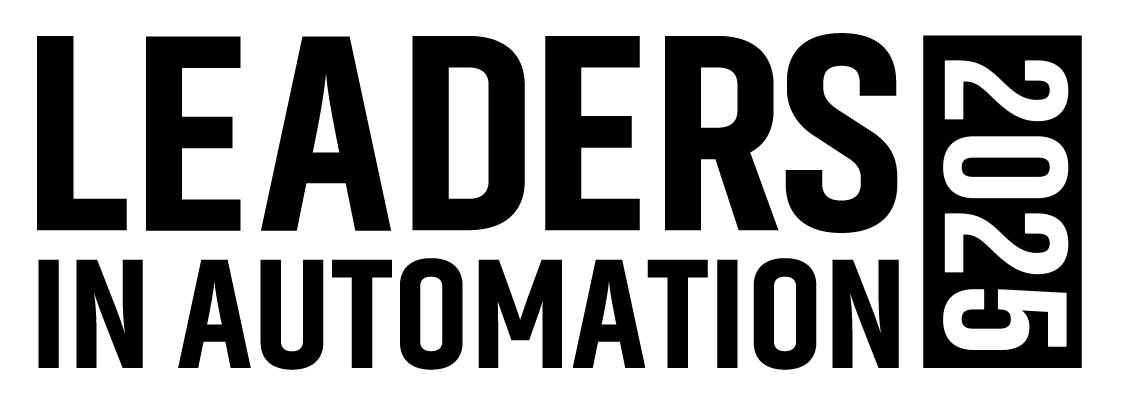
Leaders relevant to this article: