Breaking Through Capacity Constraints
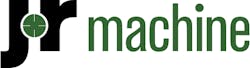
JR Machine is a leading, ISO-certified contract manufacturer for OEM and tier one/two manufacturers. Precision turning with live tooling is a core competency. The shop takes on jobs in the range of 1 to 10 inches in diameter and as much as 28” in length. Customers include some of the biggest and best-known names in the fields of defense, medical, machinery, hydraulics, oil and gas and even auto racing.
A few years ago, JR hit a capacity wall. They couldn’t put any more equipment in the building and couldn’t expand the building. Their backlog of jobs forced them to run 24/7 with two 12-hour shifts. The only way to increase capacity was to improve productivity. The goal was to eliminate 4,000 hours per year of inefficient production time.
Workpiece transfers are often the biggest contributors to unproductive machining time, because the machine has to stop while operators load and unload parts. JR Machine decided to eliminate this inefficient time by automating transfers using a series of spindles.
To facilitate the automation, JR Machine installed DMG MORI NLX 2500 Series sub-spindle multitasking lathes with top-of-the-line Mitsubishi Electric M700 CNC controls. The machines have part-catching and part-conveying capabilities. These capabilities along with the controls give Tim and his team the ability to machine a part in a single setup. They no longer have to manually unload and then flip the part or complete the second side in a separate operation. This has reduced setup time and cycle time.
Integrating these machines into their shop had an immediate impact on high volume jobs. Tim Tumanic, President of JR Machine says these new features give them much better machine performance and varying degrees of higher uptime. On some projects, uptime increased by 30 percent in comparison to older models. The machines also enable long stretches of unattended operation. In one case, a job ran over an entire weekend, only requiring an operator to come in two hours each day to check on the two machines.
Standardizing on one control platform for rock-solid reliability and durability
Several years ago, JR Machine decided to work exclusively with DMG MORI. Tim says, “The Mitsubishi Electric control was a pretty substantial part of that decision. Previously, when we used controls from a different company, we had lots of revisions and technicians coming into the shop. Now we don’t have that. It’s a real positive experience. I don’t have to think about the controls at all.”One of the things Tim likes most about the Mitsubishi Electric M700 CNC controls is their rock-solid reliability and durability.
Tim says the move to standardization brings value on many levels. It’s easier for them to:
- Redeploy people to different machines, because the machines and work centers are the same
- Get newly purchased machines online quickly, because they are tooled just like the others
- Roll out continuous improvement initiatives, because the shop only has to focus on one machine platform
Standardizing on one control platform also makes scheduling easier, because jobs can run on virtually any machine.
Getting more parts out the door more affordably
The machines have delivered huge cost savings for their customers and decreased lead times too. Tim says, “We’re committed to growing with the OEMs and tier one/two manufacturers we serve. We will continue to embrace new technology that improves precision and quality and allows for greater efficiencies in our operations.”This ‘continuous improvement’ mindset has resulted in significant business growth for the company and industry recognition for Tim. In 2018, JR Machine won Wisconsin’s “Manufacturer of the Year” among companies with less than 100 employees.
When asked about the future of machining at JR Machine Tim says, “We see more automation.” Tim is considering adding machine-loading robots between pairs of turning centers. This might make it possible for one machinist to tend four machines.
Companies in this Article
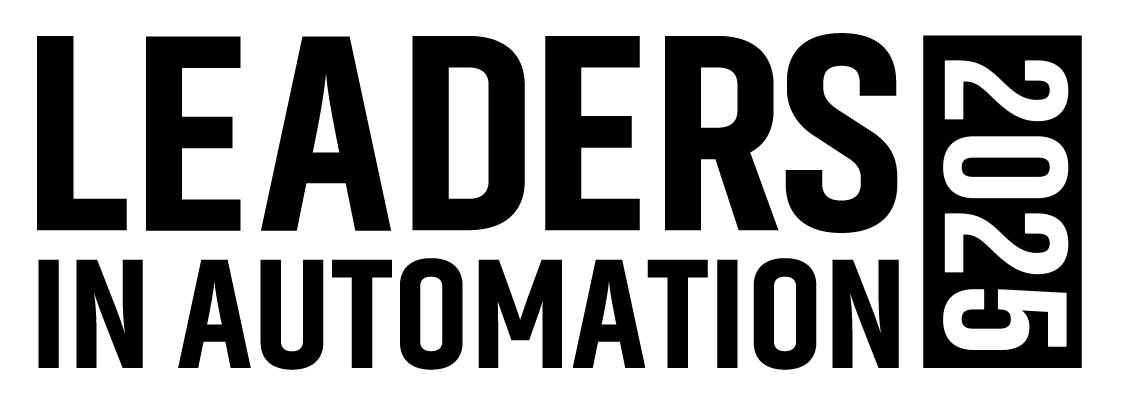
Leaders relevant to this article: