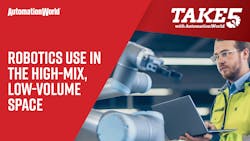
Quick hits:
- In addition to assembly and machine tending, high-mix, low-volume (HMLV) manufacturing boosts efficiency in applications such as e-commerce fulfillment and medical device production and packaging.
- An estimated labor shortage of 600,000 machine operators is forcing small manufacturers to find creative solutions to enhance productivity.
- Shorter product runs coupled with pressure to reduce lead times has mandated companies be capable of more rapid changeover.
- Automation technologies such as cobots and flexible feeding systems have helped manufacturers to keep up.
Related to this episode:
- Automation World Feature: Robotics Adoption Survey Finds Ups, Downs, and a Few Surprises
- Flexible Robotics Boost Business for Contract Manufacturers
- Take Five Video: Part Feeding Systems Get Automated
- Gain an in-depth look at PMMI's research on automation and hear from experts on industry topics by visiting PMMI's Business Intelligence video library.
Hello and welcome to Take Five with Automation World. I’m David Miller, Senior Technical Writer for Automation World.
Today, I’m going to be talking about the adoption of robotics and other forms of automation among High-Mix, Low Volume manufacturers. And when I say high-mix, low volume manufacturers, what I’m really talking about is small job shops, probably contract manufacturers, who staff between 10-15 people, and which produce highly variable make-to-order products in small quantities. A lot of these types of companies spring up around bigger manufacturers in order to provide them with component parts for larger assembly operations.
Typically, when we think of industrial automation, we have the bigger players, such as automotive, in mind—but big automotive plants and others like them are often supported by these smaller job shops, which often don’t join trade associations, don’t do much networking, and as a result remain essentially invisible unless you’re actively looking for them. These companies also aren’t as capable of straddling the high CAPEX costs that have come with investing in automation in the past.
Still, we’re seeing a lot of that start to change. For one, these companies are currently faced with a tidal wave of different challenges. They’re confronting unprecedented labor shortages, with an estimated 600,000 machine operator jobs going unfilled in the next ten years. In addition, that tight labor market has raised labor costs, which places strain on them given that they are already suffering from shrinking profit margins. Not only that, but trends like mass customization and a consumer culture increasingly fixated on novelty means that shorter product runs are becoming more common. What that means is that these companies need to be more flexible in what they can produce, and more capable of conducting rapid changeover as they race to meet more and more competitive lead times on these more and more varied product runs.
So, as I’ve said robots—and especially cobots—are increasingly helping these smaller companies to navigate these challenges. For one, as robotics have become more mature, lower cost options have become available, allowing these companies to start trying them out. Not only that, but with the rise of cobots, programming and working with robotics has become safer and more intuitive, allowing those with less pre-existing robotics experience to easily integrate them into their operations.
The uses these robots are put to vary, but they’re particularly useful for simple tasks like machine tending, injection molding, pad printing, heat stamping, and pick and place operations. With machine tending, for example, a cobot that can work in close conjunction with a human worker might work alongside a CNC machine, taking out materials, putting materials in, and so on. The human worker would still need to perform the core operational procedures on the CNC machine, but they wouldn’t have to stand by for machine tending. In other words, they could go put their hands to some more useful work. And so as you can imagine, if each employee’s time is being used more productively, less workers are needed, and labor shortages become easier to navigate.
The other thing we’re seeing is growth in automated, flexible feeding technologies, some of which involve robots working in conjunction with parts feeding machines. Typically, standard feeding systems are used to sort parts for handling by other machines and systems by using vibration and gravity to move components, but they need to be configured very precisely for each type of part they move. Because of that, if changeover needs to occur, as we discussed earlier, extensive reconfiguration and therefore loss of throughput can occur. Now, by pairing robotics and visions systems with typical feeders, a single feeding system can be used to sort and direct numerous different types of parts with little or no changeover time.
So, this is obviously a very in depth topic that we could go on a lot more about, but for now, that’s all I have. If you’re interested in hearing more about this, check out the links in the description below this video. Remember to keep your eye on this space for more videos like this come in the days ahead.
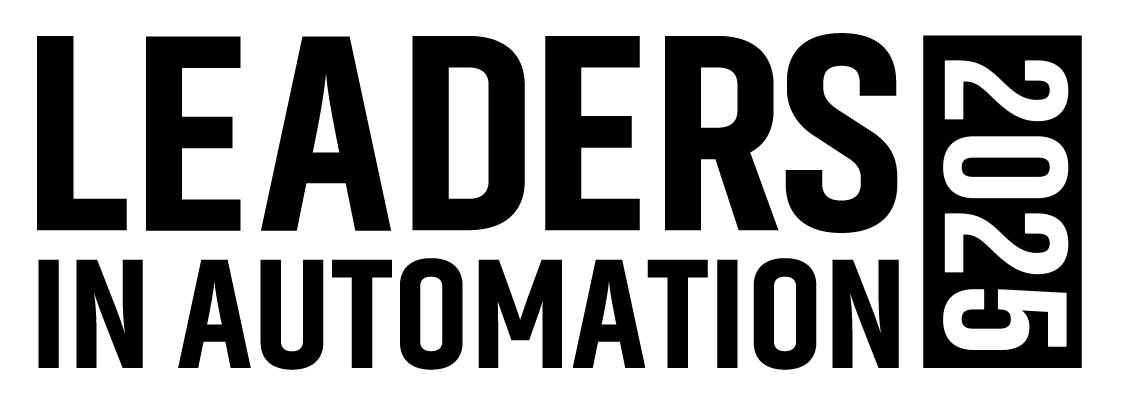
Leaders relevant to this content: