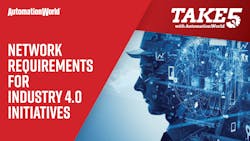
Quick hits:
- Industrial Ethernet is quickly becoming the preferred network in discrete manufacturing.
- Interoperability, higher bandwidths, and deterministic communication are the qualities an effective industrial ethernet network can bring to operations.
- In the process industries, Single Pair Ethernet (SPE) and Ethernet Advanced Physical Layer (APL) may help to usher in a shift similar to that which has been seen by discrete manufacturing.
Related to this episode:
- The 4 Aspects of Industrial Networking Required for Digital Transformation
- Fieldbus in the Industrial Ethernet Age
- Automation World Feature: Industrial Ethernet Advances Broaden the Network’s Value Across Industries
- Visit PMMI's Business Intelligence Library and download their executive summaries of their latest reports for free
So, as our viewers certainly know, industry 4.0 is not driven by any single technology, but is all about finding new ways for previously siloed people, pieces of equipment, and software products to communicate in order to better coordinate their activities and unlock new efficiencies.
And we see this shift to a system-oriented way of thinking everywhere in today’s industry. In supply chains, we see companies looking to acquire real-time visibility into numerous production facilities so that if a disruption such as a natural disaster that closes ports or a labor shortage that reduces capacity occurs at a particular location, they can more easily re-route through other facilities or suppliers.
In the four walls of plants themselves, we might see something like a machine learning algorithm that groups different types of production units together based on material commonalities and then routes them through the same CNC machines or other equipment in order to reduce scrap.
Of course, none of this would be possible without a network infrastructure that allows data to be collected, communicated, and analyzed quickly and reliably. So what are the qualities a network needs facilitate this? That’s what I want to talk about next.
First of all, the network has to provide seamless, top to bottom communication from the field all the way to the enterprise level – otherwise, the process of getting data from field devices, sensors, and real-world equipment up into a unified, cloud-type environment where it can be viewed globally across many different facilities is just too complicated. Someone I spoke to once described it as being like having to build a kind of Rue Goldberg machine that was using network gateways to engage in protocol conversion multiple times as the network moved from plant-level fieldbus to back-office ethernet and back again.
Luckily though, more unified networks have been made possible in recent years by open industrial ethernet protocols, which make plant-level ethernet protocol agnostic, meaning that they are able to interface with any higher level ethernet protocols without the need for any type of protocol conversion.
So our second requirement is high bandwidth to accommodate the growing quantities of complex, granular data being produced by IIOT connected sensors and devices. It’s this data and the fact that it’s richer and more detailed that enables us to develop the level of insight necessary to build a digital twin or train a machine learning algorithm. And that’s another reason we see industrial ethernet taking over—If you look at fieldbus, it has a communication speed of 31.25 kilobits per second. Something like Hart, literally only 1,200 bits per second. But if you look at ethernet, you’re looking at anywhere from 100 megabits per second to 10 gigabits per second. That’s a very, very significant increase.
Now there’s one final ingredient you need for a really effective Industry 4.0 network infrastructure —and that’s determinism. When you have all of this complex information being sent back and forth across a network, latency can become an issue. As those in industry know, a millisecond delay on a command for a very rapid motion control application can be a botched process. So, what deterministic protocols really allow for is the identification and prioritization of time-critical, time-sensitive data on a network, so that its delivery without any latency can be guaranteed. Then other data that is going up to higher-level systems—historical data, things like that—can take its sweet time. We’ve seen that become a reality in recent years with deterministic ethernet, and we’re seeing it become even more common with time-sensitive networking technologies.
Of course, much of this has already become increasingly common in the discrete manufacturing industries—however, the transition has been a bit more difficult in the process industries where restraints exist such as needing to run cables significantly longer distances, and often in hazardous environments where power on a wire needs to be kept very low to avoid igniting a flame.
But keen viewers probably know that many of those problems are beginning to be solved by technologies such as single pair ethernet and ethernet advanced physical layer, so that it may be the case that even the process industries soon begin to see top-to-bottom ethernet taking over their operations. If you’re interested in learning more about SPE and APL, you can read about it our July print issue. In any case, that’s all I have for you today.