Utilizing simulation environments for control systems in manufacturing facilities can reduce risk and prevent plant downtime. Setting up a simulation environment means using programmable logic controllers (PLCs), human-machine interfaces (HMIs), and other devices to emulate real-life production and equipment situations to train and troubleshoot without risk. More clients are asking us to set up simulation environments at their facilities for training operations, but how much value it provides depends on your specific production environment.
Beyond testing
Many companies and facilities use simulation environments to test upgrades and new products before installing them on the production floor, but plants can also use them beyond testing. These test environments are equally useful for training operators on using the system and troubleshooting specific scenarios. The simulation environment looks very similar to the HMI on the plant floor, helping operators get comfortable with the system and preparing them to fix any problems that arise in real life. Troubleshooting scenarios can differ from facility to facility, but general examples include a low-level signal on a bin or an alarm on a conveyor. Seeing how the system will react to these problems helps operators learn how to fix them. When operators understand how to troubleshoot as a result of using these simulation environments, we see less downtime. Additionally, we receive fewer service calls, and even the maintenance staff is called less often.
Pros and cons
The pros of using simulation environments are two-fold: These environments allow facilities to test a system before it is on the plant floor, and can decrease downtime. If operators can troubleshoot potential problems and train on the control systems before issues ever happen, it will result in less downtime, which means more cost savings. Thorough training on updates and upgrades helps every operator, especially in plants where turnover or multiple shifts aren’t uncommon. If you have ten or more people using the system, a test environment will be more advantageous than for a facility where only one or two people run the show.
There is really one primary con: Simulation environments can be expensive. You must have the computer, the PLC hardware or RS 5000 Logix Emulate software, and all the necessary licensing. Whatever control system components you have in your production environment should also be in your simulation.
Tips for best outcomes
For a significant investment, it’s important to get the most value out of a control systems simulation environment. Consider these five suggestions to maximize your investment:
1. Combine upgrades for a lower overall quote. If you’re planning plant upgrades and want to break them into multiple pieces for cost reasons, it’s cheaper to do it all at once. Testing and debugging can be resolved as a part of one package instead of requiring several different visits, tests, and installations.
2. Address risk as it happens. Mistakes can occur at busy plants when lots of activities are happening. Don’t let problems linger—utilize the training from the simulation environment to troubleshoot the problem as soon as possible.
3. Perform full testing on all equipment. Testing all the equipment in the simulation before it goes live ensures that problems are caught early, before there are any detrimental effects.
4. Make sure the right people are involved. Ideally, the people helping set up the simulation environment will have a good, solid knowledge of the system. They will know common issues that occur in the production environment.
5. Choose a vendor with combined services. Find a company that can set up the whole environment—from hardware to controls to databases. You need all these components to work together seamlessly, so, on top of being more cost-effective, choosing a turnkey provider will provide a seamless experience.
Whether you’re debugging before installing an update or training multiple shifts of operators on how best to run your specific control systems, a simulation environment is a low-risk, high-benefit option. Choosing the right vendor to set up your simulation is essential, and the avoided downtime will be proof that the extra training is working for your plant.
Heather Johnson is an automation manager at Interstates, a certified member of the Control System Integrators Association (CSIA). For more information about Interstates Control Systems, visit its profile on the Industrial Automation Exchange.
Companies in this Article
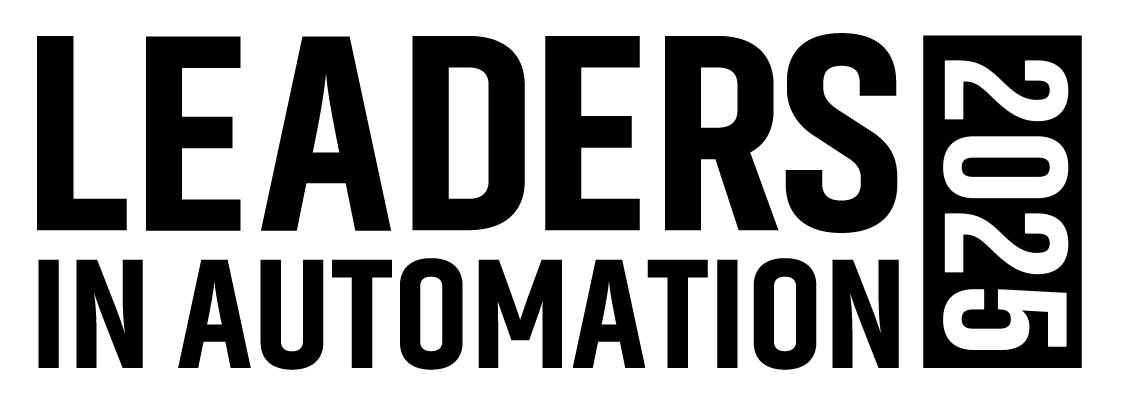
Leaders relevant to this article: