LINKS FOR FURTHER READING ON INDUSTRIAL SAFETY TECHNOLOGIES
- Assessing Cobot Safety
- Ensuring Safety in Industrial Control Panels
- Chooing the Right Safety Devices
- Robot Safety Awareness
TRANSCRIPT
Welcome to the Automation World Gets Your Questions Answered podcast. I’m David Greenfield, editor in chief at Automation World and in this episode, I’ll be looking at the basic safety device types used in industrial automation across the discrete and batch manufacturing industries as well as sharing some industry expert advice for choosing the right safety device for your application.
So to start, let’s look at the most common machine safety devices:
The first type we’ll look at are Machine guards, which are also referred to as hard guarding. These involve placing a physical barrier on or around a machine to prevent workers from coming too close to the machine and/or touching potentially dangerous parts of it.
Then, of course, there are safety light curtains, which create a sensing beam or screen of light across a machine’s access points. If a person or object interrupts the beam, it triggers an alert to cease the machine’s operation.
Safety laser scanners are functionally similar to light curtains in that they use infrared laser beams to scan a machine’s surrounding area two-dimensionally. The invisible beams act as a protective field so that if a person or object enters the field, the scanner detects the event and generates a change in its signal output to stop equipment operation.
Now, safety controllers are a type of stand-alone safety device that were part of the discussion some years ago among engineers who believed that regular operations control and safety control networks should remain separate. But with the advance of multi-core processing capabilities, more controllers are now available that include both regular machine control and safety control capabilities. Despite this, there is still wide use of safety controllers which are designed to meet specific safety standards to monitor other safety devices and shut off power when needed.
Two-hand controllers are a type of safety device used to ensure workers’ hands are clear of dangerous mechanisms. These devices require personnel to use both hands to initiate and maintain machine functions. They’re mostly used on machinery with high-force closing movements such as hydraulic presses, stamping machines and cutters.
Interlock switches prevent machine operation or startup in an unsafe situation such as when a door or guard is open. These switches can also prevent doors or guards from opening while the machine is in operation. Often included in this family of safety devices are trapped key interlock switches, which rely on mechanical locks and keys to control access to gates, guides or doors on active machines.
Enabling devices are used to initiate a particular safety function when a user squeezes or releases a switch in a handle grip, which is typically similar to a joystick. Unlike e-stops which are button switches that allow workers to stop a machine by pushing the button—and which are probably the most well-recognized safety device—enabling devices can be used to activate a variety of safety functions, whereas e-stops initiate only one, such as stopping the machine.
And finally in this list of the most commonly used industrial safety devices, there are indicator lights which are available in single-and multi-color options to provide visible indication of a machine’s operating functions as well as its safety status. As I mentioned earlier, this list is not a complete list of industrial safety devices, but rather a listing of the most commonly used devices. Other common safety components include enclosures, circuit breakers, intrinsically safe isolators, relay modules, surge protectors, and safety mats.
Armed with information about the many safety devices available, the next task is to think about your application in depth to help determine which type of safety device or system is your best choice.
Robert Mosher, business manager of safety at Rockwell Automation says one thing batch manufacturers in particular need to take into account is how often change-overs are required and the need to access the machine during those changeovers. He says the more often a particular part of a machine or process needs to be accessed, the more likely that hard guarding will not be the best option and either safety interlocks or presence sensing devices may be required. Also, special consideration needs to be made to ensure that the machine cannot be inadvertently started while a person is in the machine conducting the change-over. For example, a trapped key interlock switch can be configured to ensure that a predetermined sequence of events takes place or that hazards have been reduced before an operator becomes exposed to them.
Noting that light curtains are often used where frequent access, such as during changeovers, is needed, Mosher notes that it’s “critical that a light curtain of the appropriate length and resolution be selected and that the light curtain is located at the appropriate distance to ensure that a person falling through the light curtain can’t reach the hazard before the hazard has time to fully stop.”
He adds that, if a person is on the inside of a light curtain area, care should be taken to make sure that the machine cannot then be started. In some cases, he says this requires placing a second set of light curtains perpendicular to and between the machine and the first set of light curtains.
Travis Holley, machine safety services manager at system integrator Polytron, recommends that “safety devices must be able to withstand environmental factors such as dust, washdown and extreme temperatures. He says Many machines in process manufacturing, for example, have an inherently high run-down time. So, the use of non-locking safety switches on guard doors could allow access to these hazards. Guard-locking safety switches can be used to keep workers out of the hazard zone until the machine has achieved a safe state. So, when selecting a guard-locking safety switch, it’s important to follow industry standards that require the device to be a power-to-unlock type, unless specified otherwise by the machine’s risk assessment.”
Bryant Eismeier, a senior automation engineer at system integrator Flexware Innovations, says that in batch processing applications—such as chemical mixing, water/wastewater or food processing—handling of materials that are explosive, caustic or biologically harmful often requires safety measures such as specialty fire monitoring systems and gaseous or liquid chemical detectors. These types of technologies are more common in industries typified by process hazards rather than discrete hazards that tend to be more mechanical in nature.
Joshua Vernon, director of engineering for the South Atlantic region at system integrator Automated Control Concepts stresses that another variable to consider is that stopping all the equipment may not be possible because the process to do so could be lengthy and a full stop could present more danger than continuing. He says this reality highlights why a hazard analysis is so important before choosing safety devices.
If you’re interested in learning more about industrial safety devices and systems, be sure to visit this podcast on the Automation World site. There, just above the transcript, I’ve included links to several recent articles on these topics.
If you’re listening to this podcast via one of the various podcast platforms, you can access those links by going to: automationworld.com/safetypodcast
So thanks for checking out this episode of the Automation World Gets Your Questions Answered podcast series. And remember to keep watching this space to stay on top of the latest news, trends and insights on the world of industrial automation.
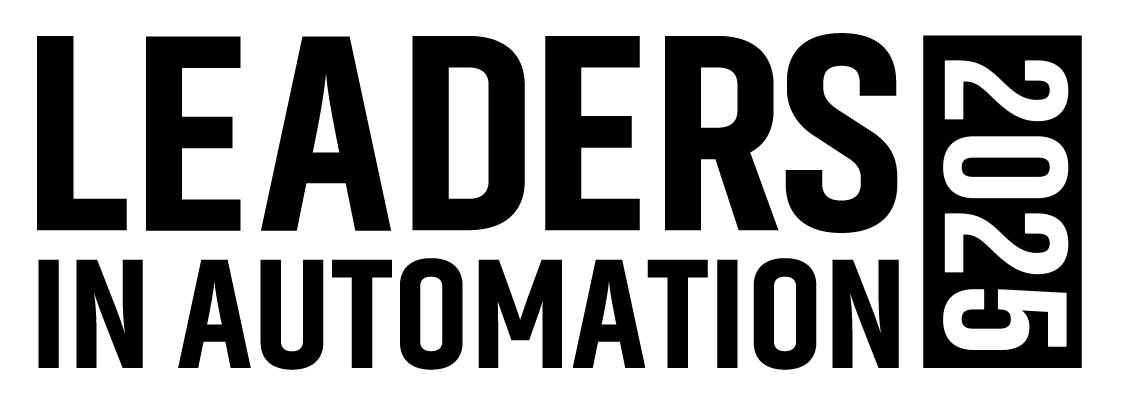
Leaders relevant to this content: