Supply Chain Headaches Reveal Golden Opportunities in the Industrial and Utility Worlds
There’s not an industry in the world right now unaffected in some manner by supply chain headaches, and the constant logistics needed to keep up can be maddening. Turbulence in the supply chain, shortages of skilled labor, economic uncertainties and increased demand specifically for manufactured household items (everything from toilet paper to lumber to computers and the chips that make them) are playing a significant part in outlining what 2022 will look like. And it doesn’t look like it’s easing up any time soon.
So what does that mean for industrial manufacturing looking to automate their plants and ease some of the missing worker tensions while still keeping up with production? How will it impact utilities charged with keeping the grid going and the water flowing to protect and provide for their communities?
As with any obstacle there are multiple ways to tackle it. You could literally roll back time and revert back to decades-old technology like relay or pneumatic-based controls, but honestly you really don’t want to do that. A decision to follow that path risks losing efficiency along with any competitive business advantage that comes with new technology.
Alternatively, you could push a project aside until the supply chain catches up. But, with no end in sight, fierce competition still waging battles across industries, and legislative bills poised to inject investments into automation and upgrading systems, that might not be the wisest decision. In fact, the additional cash flow about to be infused into utilities and industries might be just the right motivation to find a way through the maze of supply chain logistics. But what’s the key to making that a success?
Navigating Supply Chain – Strong Communication
Let’s start with the basics. Communicate well and often. Good communication with your internal team and the customers you serve will go a long way to helping you understand where supply chain hiccups will affect you the most.
Internally examine both your personnel situation and your existing systems. Are you having a hard time finding skilled workers to take once fillable positions and is your HR team spinning their wheels trying to find skilled labor at rates that won’t put you out of business? Is this an opportunity to introduce some form of automation or a collaborative robot to take on the monotonous jobs and ease the burden of finding good skilled labor?
Communicate with your existing team the challenges you’re facing and talk creatively about how you could free up some of those positions and divert important human personnel to focus on more strategic, intuitive processes. Good communication could effectively help you strategize for the long term and alleviate concerns your team may have about being “replaced” by a robot. It should, if communicated well, show them a new future at their position where their time could be devoted to additional career development.
Do outdated systems require inefficiencies and time-consuming battles you can’t afford now while still achieving your production goals? Now is the time to have some strategic discussions about the future of your company and its longevity in a highly-competitive environment. Allowing supply chain issues to impact your long-term strategy may prove detrimental in the end. Seek out opportunities to gain access to federal monies devoted to upgrading and automating processes and secure your team's place with growing and thriving companies.
Solid communication with your purchasing department and those on the front lines is imperative. Talk about which component parts are experiencing the most setbacks and share any knowledge gained of alternative solutions that could work for a given project. Information shared within the company can allow better communication outside of your walls.
Consistent and accurate information passed onto your customers can be your biggest weapon in the fight we’re all in regarding supply chain issues. Being forthcoming on any possible supply chain setbacks you may be able to predict allows your customers the flexibility to go back to their own team and talk through their options.
Once open communication has begun and some decisions have been made about the future of a project, then the real creativity comes in.
Partner with a Trusted System Integrator
For industrial automation projects and various utilities, collaboration with a trusted system integrator and their vendor partners allows the right people to be in the room to think through a viable solution.
Control System Integrators Association (CSIA) has already vetted business partners and system integrators for their professional business practices, ensuring a CSIA certified company can be trusted. In parallel, many hardware and software vendors have their own certification programs highlighting system integrators with experience in their systems. These can be great launching points to find a system integrator that will work well for you.
Identifying a system integrator who is technically sound in multiple software and hardware applications will allow you to draw on their expertise and contemplate multiple solutions. Working with that integrator to brainstorm ideas for alternative and more easily accessible products is an exercise in creativity. A solid system integrator will be well-versed in similar solutions that can either be used in the interim or on a more permanent basis. Experience and knowledge in automation processes and multiple systems allows them flexibility to be creative with confidence that an outside of the box solution will work.
Be willing to consider an interim part that may be more easily accessible to meet ongoing production goals. Open your mind to an entirely new way of thinking that may work as well or even better.
Though there are likely hundreds, two common scenarios come to mind.
A production facility realizes unexpectedly that a component part has been corrupted and halts production. In this urgent scenario, if you cannot find readily accessible replacement parts, the cost to your company could be tremendous in this unplanned situation. Leaning on the expertise of a qualified system integrator will save hours if not weeks, not to mention real-time dollar costs, in getting that system up and running again.
Now, let’s contemplate an entire plant built with one vendor’s hardware for ease of use. In an ideal state, that makes total sense. In a time of short supply though, considering an alternative item that is more easily accessible, even in the interim, could be a distinct advantage to keeping the entire plant running at peak efficiency and meeting production goals. When system-wide production processes are at risk due to scarce components parts, the leap of faith required to add an operational part from another vendor seems less risky than the possibility of shutting down production for an extended period of time.
This is where the trust developed between a customer and an integrator can shine. Communication from an integrator striving for what’s truly best for the customer without taking shortcuts is priceless. The last thing either party would want is to partner with someone who is a here today gone tomorrow vendor partner so that when things get tough they are nowhere to be found.
Find an Outside of the Box Solution
As we alluded to, if you have a project that could help ease some of the current economic climate stresses (like an automation upgrade) and you’ve been putting it off for some time, you realistically have two possible viable paths forward. Push pause on the project and wait for supply chain issue to resolve on their own or get creative and start thinking outside of the box. A qualified system integrator will be ready to brainstorm alongside you. Taking advantage of their breadth of knowledge of software and hardware, there may be alternative ways to engage a process with slightly disparate systems and still execute on critical production processes.
Here’s an example. Think about traditional I/O modules that reside in the PLC rack, like analog input modules. In the world of manufacturing, replacements for these are very hard to come by these days, (at least in any expedited timeframe) although they are certainly common in many manufacturing applications. Now might be the perfect time to consider a new technology that could yield the same, if not better, results.
IO-Link may be an alternative technology module beyond what you were preparing your plant for at this time. In fact, this may be the perfect solution to keeping your plant afloat and set up for future success rather than stalling production based on some hard-to-find parts.
Similarly, Profinet or Ethernet/IP devices may offer a solution that could replace the hard to find traditional hardwired I/O modules. In this case, what started as an obstacle can now become an opportunity to find a solution that will work equally well.
In most cases theses alternative solutions will also provide access to additional diagnostic information from smart devices. This access to data analytics can make you more efficient, allowing you to use predictive analytics to make better business decisions.
A well-trained and certified system integrator will have that solution option at their fingertips, saving costly time in researching various options. Using a subject matter expert gains you access to options to bypass the supply chain obstacle standing in your way.
At the end of the day, recognizing we’re all facing some of these same challenges and facing them with a little patience, understanding, and creative partnership will serve us all well. And to those of you who have done just that with open communication and a little bit of humor along the way, we say thank you. To those still lost in frustration we say, give us a call and let’s work through it together.
Companies in this Article
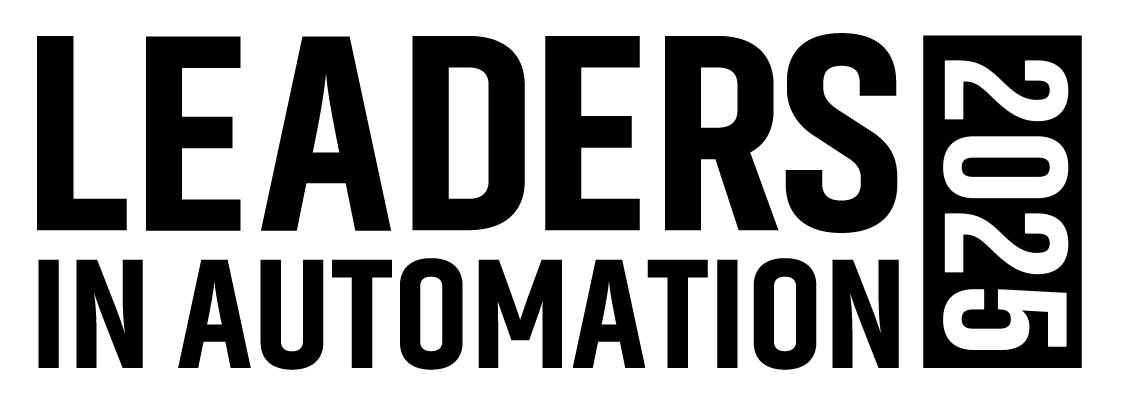
Leaders relevant to this article: