When the welding robots first arrived at DeAngelo Marine Exhaust, the fabricators in the shop weren’t quite as enthusiastic as Justin Montes, CEO of the Fort Lauderdale-based company. These highly skilled craftsmen were skeptical about robots relieving them of producing aircraft-quality welds on the exhaust parts that they make for marine engines. So, as is often the case when workers encounter new forms of industrial automation, DeAngelo’s fabricators gave the robots a cool reception.
Despite generating anxiety and suspicion among some in the workforce, advanced automation technologies, such as robots and artificial intelligence (AI)—have great potential not only to increase productivity, but also to relieve workers of burdensome tasks, create opportunities and even enhance job satisfaction.
The fabricators at DeAngelo learned this lesson, once Montes had coaxed them into running a few parts on a cobot welder from Hirebotics, a robotics-as-a-service company that uses collaborative robots from Universal Robots. When the fabricators saw that the robots were indeed capable of producing the required-quality welds quickly, they were impressed.
Now, the robots weld high-volume subassemblies in a newly created pre-fabrication department before the subassemblies go the fabricators for further processing. The fabricators, who are the highest paid employees in the shop, now focus on more challenging work and leave the mundane, repetitive work to the robots and the operators who tend them.
In addition to resolving DeAngelo Marine Exhaust’s growing backlog of work caused by the shortage of skilled fabricators, the robots have contributed to job satisfaction by relieving the fabricators of burdensome work and creating opportunities for the operators.
“These same people who were afraid of the cobot are now calling me on weekends, suggesting new parts to run on the cobot,” reports Montes. “It’s been a morale booster for our work culture.”
This boost in morale came in part from integrating the robots into the workflow in a way that assists the workers, rather than adding a burden, even a tiny one. This is an important tactic for preserving and enhancing job satisfaction, according to Bob Rice, Ph.D., vice president of engineering at Control Station, a developer of process analytics and optimization software.
“The last thing that workers want is another gadget that they need to babysit, another web portal to monitor, or one more source of alerts and alarms,” he noted. And that’s especially true when the underlying technology is perceived to represent a threat to someone’s livelihood.
So, Control Station facilitates the integration of its plant and enterprise analytical tools with other, existing platforms. “Rather than requiring plant staff to use yet another dashboard, we’ve found that using a REST API (application programming interface) to synthesize the most important KPIs (key performance indicators) within a control room’s primary console is a source of relief,” said Rice. If the selected KPIs indicate that something is amiss, the staff can then launch Control Station’s tools for root-cause analysis and developing a plan for corrective action.
Address employees’ fears
Another set of tactics for preserving and enhancing job satisfaction is to address the two chief sources of anxiety and fear caused by the installation of new advanced automation: displacement and upskilling. Being displaced by automation is a possibility in the more rote, less-skilled jobs because a great deal of automation is actually designed to replace these jobs, points out Misha Schurman, Ph.D., director of enablement and user adoption at Seeq, a developer of analytics software for the process industries.
“The fear associated with up-skilling usually has to do with not wanting to do a different or harder job,” she continues. “In this latter case, this fear can be driven by upcoming retirement, or personnel may be afraid of an inability to handle more advanced training or tasks.”
Schurman advises tackling these fears up front, first by naming them. For example, if you’ve heard about fears that folks will be replaced or let go, “address it by describing exactly what employees will be expected to do and what opportunities this transition might offer,” she said. Be sure to clarify if it will offer them work that is more interesting, has better pay, or provide a growth path.
To provide growth paths, Schurman urges employers to set aside the necessary resources to support a continuing upskilling program. “This includes monetary and time investments for hands-on, relevant training,” she said. “Employers should provide paid time for training without distractions from the workplace.” They should also have someone with the responsibility for establishing and executing the training plan.
Such plans should go beyond teaching workers the mechanics of how to accomplish particular tasks. “When tasks involve judgment, that’s where human workers add unique value and justify higher compensation,” added Rice. “There’s a growing demand for individuals who are comfortable working in ambiguous situations, who can see the bigger picture and understand how to apply the correct tools.”
This means that workers increasingly need to understand processes from first principles and have the ability to use data analytics and causal reasoning to determine why something is occurring in the process and to predict what will happen.
“Spending great deals of time learning the intricacies of coding is on the way out,” observed Schurman. “It is being replaced by higher-level critical thinking and a focus on understanding systems.”
Exploit available training
One way that employers can help employees hone these skills is to keep training in mind when selecting new automation. “Some vendors provide extensive free training,” explained Corey Adams, education program manager at Universal Robots. He points to his company’s UR Academy, which offers nine free, interactive modules that cover the basics of robot programming and setup.
This resource played a central role in generating enthusiasm among workers for new robots going into production lines at Darex, a manufacturer of drill and knife sharpeners in Ashland, Ore. Because the family-owned company is tucked away in a rural valley, labor is hard to come by. So, when John Griffin needed more production capacity, the director of operations decided to install collaborative robots from Universal Robots to automate some screw-driving and box-erecting operations, both of which were troublesome and undesirable tasks.
Not only did Griffin want the robots to work alongside workers, he also needed one of those workers to become the robot technician. So, he organized a competition that had the robot technician job as the prize. He gave the production line operators the web address of the UR Academy and told them to study up on programming. Three weeks later, Darex held several rounds of contests in which employees programmed the robots to perform simple pick-and-place tasks.
An operator named Brittany Mohrman won and was promoted to robot technician. Now, besides performing day-to-day maintenance, she troubleshoots robot problems and handles changeovers. According to Mohrman, her new job is much more interesting than the old one.
Besides reaching out to suppliers for training, Adams also recommends collaborating with your local manufacturing extension partnership (MEP) to explore avenues that might exist for supporting an upskilling initiative. Online resources, like roboticscareer.org, might help with finding training available in specific regions.
Tips for improving reponse
A technique that Schurman has found to be useful for changing negative attitudes is to create teams that mix workers who have a negative perception with those who have a positive perception. She had success with this technique during a data analytics course that she recently taught at a plant with a mix of older engineers nearing retirement and younger, more tech savvy colleagues.
“Initially, the older engineers were very resistant to the course,” she said. “Their approach had worked fine for decades, and they didn’t understand the computer programs.” Besides not being convinced of the need for analytics, there was also a fear that automation would replace them only a few years out from retirement.
The younger engineers, on the other hand, picked up the software procedures quickly. They, however, had difficulty clearly identifying what problems to optimize first and what you need to understand about how your process is running.
“We paired the more senior engineers—who could articulate exactly what they wanted to know—with the younger engineers, who, once given the right questions, could easily answer them using the software,” reported Schurman. “The team bridged a long-running divide and frustration between the two groups, facilitated knowledge transfer from the older generation to the younger, and increased respect the two demographics had for one another.”
Advanced technology can also facilitate collaboration on its own. A.G. Stacker in Weyers Cave, Va., for example, is using digital twin technology from Siemens to train the equipment operators and streamline its design and manufacturing processes. Electrical and mechanical engineers there build electronic prototypes using software like Siemens NX Mechatronic Concept Designer.
“With built-in visualization tools, a mechanical engineer can define a basic simulation to show end users how the physical machine will work,” explained John D’Silva, automation technology manager at Siemens Digital Industries, Factory Automation.
This simulation is then used with virtual reality at A.G. Stacker’s headquarters in a Digital Innovations Lab that doubles as a training facility for users of their corrugated material stacking machines. This lab also serves as a center for research and development. “Not only do end users test drive and learn A.G. Stacker’s machines here—producing valuable user insight and feedback—but A.G. Stacker’s employees also collaborate on designs cross-departmentally,” said D’Silva.
Digital twins also promote safety by designing out unforeseen problems. This means that users no longer need to wait for machinery to be built and delivered to begin training.
“Inadequate operator training resulting in workplace injuries, loss of morale, lost production and downtime decreases employee satisfactory tremendously,” added D’Silva.
Another way of fostering a sense of belonging to a team is demonstrating a commitment to the employees.
“Job satisfaction also comes from working at a company that invests in its employees, promotes from within and fosters entrepreneurial thinking,” said Tom Doring, president of the Americas at the Ammega Group, a manufacturer of smart conveyor belts.
Instilling job satisfaction requires a clear strategy. In fact, Doring said introducing automation to workers too early—before an action plan is in place—is a common pitfall.
“Job security and confidence impact employee satisfaction, which is why companies need a plan to communicate the benefits of automation to their employees and offer them opportunities and rewards for advancing their knowledge and skills,” he said. “When employees feel they can participate in continuous improvement workshops, showcase their knowledge and improve a process, there is a sense of ownership and pride.”
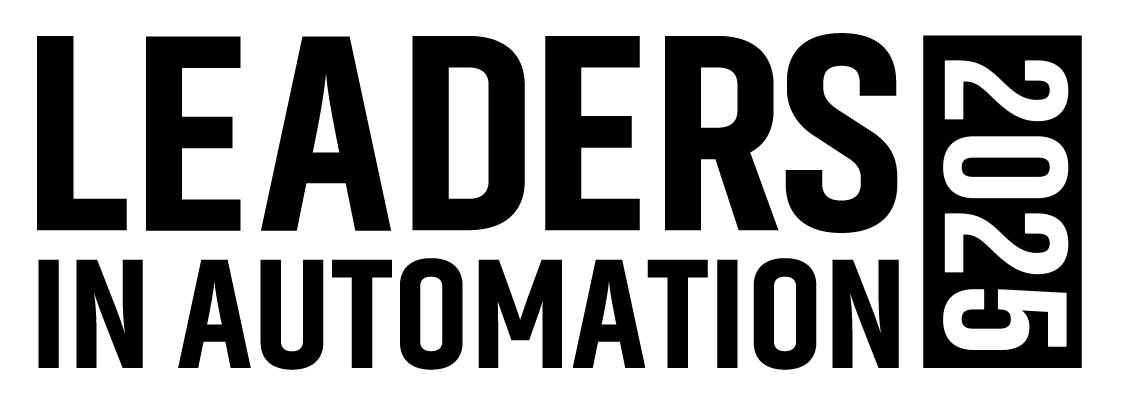
Leaders relevant to this article: