Versatility is a watchword for a company that designs and creates solutions for food production lines that run the gamut from processing to packaging. Friesen’s Inc. (www.friesensinc.com) sought versatility and made Ethernet a mainstay in its tool kit because it’s simple to switch and swap peripherals using the popular communications architecture.
The Detroit Lakes, Minn.-based systems integrator is constantly combining controllers and peripherals when it builds conveyors, dumpers and other systems for manufacturing and packaging operations. Some of the equipment requires very high performance, so Friesen’s turned to a real-time version of Ethernet, EtherCat technology provided by Beckhoff Automation (www.beckhoff.us) of Burnsville, Minn.
“Software and the communication terminals available from the EtherCat input/output (I/O) system permit the simple connection of essentially any Ethernet TCP/IP, Serial RS232 and CANopen device simplifying our designs and machine build efforts,” says Kari McAllister, director of product development at Friesen’s. “EtherCat is essentially plug-and-play, so when we add a new terminal, Beckhoff’s TwinCat System Manager can automatically recognize it.”
The ease of adding a wide range of equipment is prompting a growing number of peripheral suppliers to add Ethernet connections to their offerings. Some are eliminating conventional field bus ports, while others are giving customers a choice. Many end users are moving away from fieldbuses to gain ease of both installation and maintenance.
“Ethernet peripheral networking allows plant engineers to forego specialized communications adapters in favor of
off-the-shelf computer ports,” says Henry Loos, controls and application engineer at Applied Robotics (www.appliedrobotics.com), Glenville, N.Y. “This, coupled with the software packages included with most Ethernet peripherals by the manufacturer, makes setup and troubleshooting of these devices much simpler and more efficient.”
As more peripherals connect directly via Ethernet, it’s becoming easier for front office managers to see how production lines are running. A flat architecture with only one communications technology can be used for the entire corporation, reducing maintenance costs and simplifying the job of the information technology (IT) staff.
“Data that was once impossible to reach except via local access and special hardware is now available to all stations on the standard Ethernet network, which is essentially the entire facility’s office network,” says Kurt Wadowick, I/O systems product specialist for Beckhoff.
Now that Ethernet has made its way into large numbers of manufacturing facilities, it is increasingly replacing field buses. Eliminating older buses provides far more communications capability and eliminates extra wiring, which cuts costs and simplifies maintenance.
“Peripherals that historically were limited to RS232, -422, or -485 connections requiring gateways and bridges to participate on Ethernet networks are connecting and communicating right out of the box,” Loos says. He explains that when an EtherNet/IP Tool Changer module can be used to replace a module that formerly offered only DeviceNet, the gateway that linked the field bus to Ethernet could be eliminated. Adding direct EtherNet/IP support reduced costs, removed failure points, and provided enhanced features.
Attention to details
When peripherals are added, users can avoid problems by paying close attention to the small details. Cables and connectors are always important aspects in industrial environments, where vibrations can cause components to shake loose. When speeds rise, aspects like electromagnetic coupling, termination and grounding become even more important. Even factors like the twists in twisted-pair wiring can impact performance when signals move through wiring at very high speeds.
“The majority of problems people face when they’re running networks stem from installation practices,” says Paul Brooks, business development manager for networks at Milwaukee-based Rockwell Automation (www.rockwell.com). “We focus on physical connectivity, getting the right connectors and cables.”
To address this challenge, Rockwell has continued its practice of finding partners to augment its capabilities. For cables and connectors, the company teamed with connector maker Panduit Corp. (www.panduit.com), Tinley Park, Ill. to write a best practices guide. One challenge for global equipment suppliers is that the connectivity solutions may vary from region to region.
“In many applications, unshielded cables are better than shielded,” Brooks says. “The best way to do shielding in North America is not necessarily the best for Europe. There are different grounding practices that can impact the installation of shielding.”
The importance of cabling and connectors becomes even greater when companies move to Gigabit Ethernet (GigE). To date, this version is being used primarily for backbones. But as volumes rise and industrial demands increase over the long term, the role of GigE will likely increase to include high performance peripherals.
“Although using Gigabit requires more care at installation and more diligent maintenance, the payoff is clear. Peripherals can transmit larger amounts of data in less time, and networks can handle traffic from a larger number of connected devices,” Loos says.
Monitoring performance
The growth in the number of peripherals on a network is being matched by increasing complexity for many of these nodes. As the numbers of sophisticated devices rises, users want to know more about their performance. That shifts the focus to Ethernet’s diagnostic capabilities. The network’s offerings are far more extensive than those offered by the field buses that still function in many plants. It’s becoming easier to monitor each peripheral on a network now that these devices integrate improved networking connectivity.
“Adding Ethernet to peripheral devices opens up a broader array of diagnostic and programming functions,” Loos says. The ability to remotely monitor and record critical production data while delivering it simultaneously to plant floor controls provides a big boost to efficiency and resource management, he explains.
This ability to send data to many different locations can be a major benefit for companies as they implement Lean practices and just-in-time delivery. As Ethernet’s data rates rise, it’s becoming easier for equipment to send diagnostics while these machines are also sending and receiving everyday control commands.
“Diagnostic and maintenance functions can be simultaneously executed to increase a machine’s availability,” says Ryan Legg, product marketing manager for Siemens Energy & Automation (www.sea.siemens.com), West Chicago, Ill. When problems arise, users can turn to the Web for analysis, he adds. System faults can be diagnosed quickly by using HTML standard websites, which can service connected devices locally and remotely.
The types of data that can be gathered continue to expand. “EtherCat users have diagnostics functionality such as links of all network devices, slave status, slave state, working counters, CRC errors at all points of the network, lost frames, etc. These can be easily integrated into their overall automation systems,” says Joey Stubbs, North American representative of the EtherCat Technology Group (www.ethercat.org) in Volente, Texas.
Read how a Norway manufacturer is moving towards a flat architecture by moving cameras and other peripherals to a TCP/IP Ethernet network. Visit http://bit.ly/awfeat_034
With all the tools available for the ubiquitous network, users can more easily identify possible system faults, line breaks or other issues during commissioning and throughout the life of machines. This fault reporting can be very precise, giving technicians the exact location of potential issues so they can solve the problem very quickly.
Going forward, peripherals will be able to tell the controller when they are nearing the time for schedule maintenance or when other repairs may be necessary. Prognostic capabilities are expanding rapidly, with some systems even notifying humans directly when it’s time for upkeep. “Peripheral devices are becoming more proactive, pushing diagnostic information out and using tools like e-mail to send alerts,” Brooks says.
Ethernet’s capabilities extend into other areas that are well outside the basic communications provided by LANs. A range of tools developed to help manage these networks can help companies cut expenses and respond to the drive to be green by reducing energy consumption. Certain peripherals can be turned off when they’re not needed.
“Energy efficiency can even be realized through Profienergy, a profile of the Profinet protocol. It can switch off individual loads or even production units at appropriate planned times in order to realize greater energy efficiency,” Legg says.
Meeting complex needs
For many applications, Ethernet already has enough bandwidth to meet all requirements. But for large, complex installations, the network continuously benefits from the upgrades needed for commercial products, which ripple out to industrial products over time. When peripherals move from existing field buses to Ethernet, the increase in bandwidth is stunning.
“When people say Ethernet runs at 100 Mbits, it’s not really running at that rate,” Brooks says. “If you’ve got a switch with eight ports, the eight peripherals are all running at 100 Mbits, making it more like 800 Mbits/second. That’s quite a change from Profibus’ 1.5 Mbits that’s shared among 128 devices.”
Ethernet’s higher performance makes it possible to perform scan rates in the microseconds range instead of milliseconds range. That lets engineers create more complex systems, such as motion control. It can also let integrators employ lower cost drives.
“This impacts not only coordination of the motion for hundreds of servo axes, for instance, but also the closing of control loops, which in the past had to be closed locally at the drive,” Stubbs says. “Now these loops (trajectory control and even tuning control loops) can be closed over the network.”
This enables the drive vendor to remove significant amounts of processing power, RAM and software from the drive, which allows the use of drives that are more like dumb amplifiers, Stubbs explains. The result is lower cost and a considerable improvement in dynamic motion system performance.
As Ethernet-compatible peripherals evolve, they are taking advantage of ongoing increases in microcontroller performance to add more capabilities. The remote nodes of today can easily have more computing power than some of the central controllers of just a few years ago. These intelligent devices are also capable of doing extremely complex tasks at very high rates of speed.
“In the motion control market, peripherals themselves are becoming more intelligent,” Legg says. “Based on Profinet, extremely fast isochronous drive controls can be implemented for high-performance motion control applications using isochronous real-time, which supports applications with cycle times of less than one millisecond.”
The definition of real time varies depending on the application. Some Ethernet variants are making it possible to sample at much higher speeds. For example, EtherCat has also enabled oversampling between the fieldbus cycles. That boosts speeds into the sub-millisecond range.
“If an oversampling rate of 200 samples per scan is accomplished on a fieldbus already scanning at, say 200 µs, it is possible to get a reading every 1 µs. That’s 1,000,000 readings per second,” Beckhoff Automation’s Wadowick says.
Another benefit is that when bandwidth is readily available, various pieces of equipment can access data whenever they need it. That can let system designers and users access peripherals directly, freeing a controller so its computing horsepower can be used for other tasks.
“The bandwidth of Ethernet makes it easy to get data. You no longer need to go to the controller. You can get information from a peripheral using the human machine interface (HMI); there’s no need to go through a controller,” Brooks says.
Though there’s plenty of bandwidth available for most products, sheer speed isn’t the ultimate solution for all problems. In some complex applications like motion control, synchronizing clocks can be as important as ensuring that messages can be delivered quickly.
An IEEE standard, 1588, addresses this problem. The clock synchronization protocol synchronizes distributed clocks with an accuracy of less than 1 microsecond. “An IEEE 1588 EtherCat master clock terminal, the EL6688, permits connection of a very precise master clock by tying 1588’s Precision Time Protocol to a grandmaster clock device,” Wadowick says. “For example, now HMI screens with alarms can be synchronized all around the plant to one precise time clock, and the messages each display generates can be correlated to make more sense. This was a very difficult issue previously in plants with many HMI screens that were all based on the individual time clocks on each computer station.”
Applied Robotics (www.appliedrobotics.com)
Beckhoff Automation (www.beckhoff.us)
EtherCat Technology Group (www.ethercat.org)
Friesen Inc. (www.friesensinc.com)
Panduit Corp. (www.panduit.com)
Rockwell Automation (www.rockwell.com)
Siemens Energy & Automation (www.sea.siemens.com)
Subscribe to Automation World's RSS Feeds for Feature Articles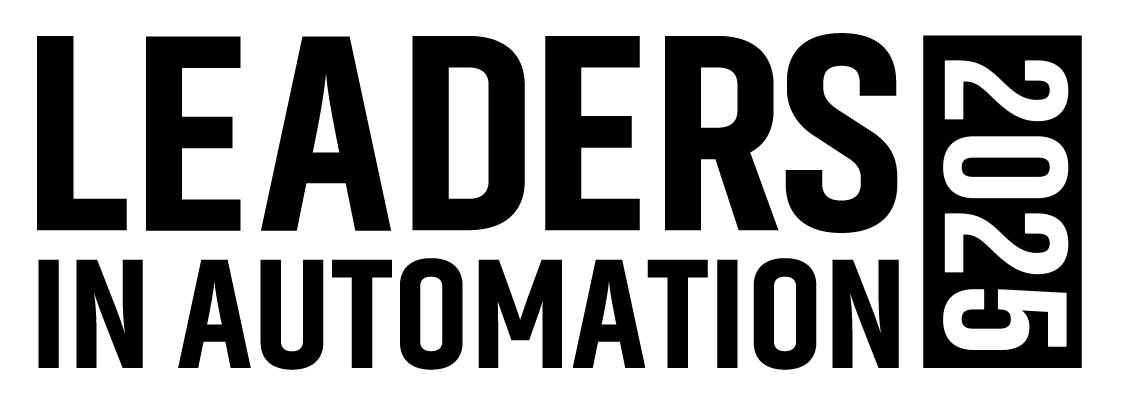
Leaders relevant to this article: