Events at a production station are usually recorded in a shift log. Most of these events, however, relate to major problems requiring maintenance work. Many minor, often homemade, issues are not logged for time reasons. And yet these are the issues that actually cause the majority of production losses and would provide important information for developing a good maintenance strategy. This document details the integration of production information in SAP R/3 via a Siemens S7 OPC Server to enable automated fault logging with precise time information.
An ERP system like SAP contains vital information, such as plant structures, maintenance messages (SAP-PM), production orders, and production progress (SAP-PP). However, large ERP systems often lack functions for recording production events. This shortcoming of SAP can be overcome with add-on programs, such as bi-tuned-ESP from Saager Management-Consultants, which keeps an electronic shift log. Every change of a station's production state is automatically entered in the shift log. The production staff needs to categorize and give reasons for the state changes. This ensures that not even the smallest events will get lost. Operators can initiate maintenance requests at the push of a button and monitor the progress of the work. The add-on program is seamlessly integrated with the SAP software and allows conclusive analysis and evaluations covering practically every aspect from setup and production times to organizational and technical problems, through the representation of plant Overall Equipment Effectiveness (OEE).
Automated Event Logging via OPC
The ERP system needs to be coupled directly to the production facilities to automatically enter the production events in the shift log. A major roadblock to this direct coupling is that the facilities usually feature a vast variety of multi-vendor machinery and equipment with widely disparate interfaces. OPC technology, as a well-established interface standard, neatly bridges the divide. OPC Client and Server interfaces provide an easy-to-use communication link between multi-vendor applications. Take the production of frozen pizzas, for example: Using OPC technology to tightly link SAP with Siemens S7 controllers, the SAP system receives the information from Softing’s S7/S5 OPC Server. The S7/S5 OPC Server is connected to the Siemens controllers via the Ethernet interface of Softing’s NETLinkPRO S7 Adapter. The data supplied by the OPC Server is read by a Softing OPC Client and saved to an IDoc file. This Intermediate Document (IDoc) acts as a container for exchanging data between SAP-R/3 systems and OPC Clients. OPC thus allows transmitting information on the facilities' states and diagnostics, production rate, quality, malfunction messages, and changeover or cleaning times to the ERP system automatically, in real-time, and error-free.
In addition to its great flexibility, the S7/S5 OPC Server from Softing provides quick and easy data access to the following range of Siemens controllers: S7-200, S7-300, S7-400, and S5. Changes to the PLC programs do not pose a big challenge to the S7/S5 OPC Server since it effortlessly integrates with the SIEMENS Step7 programming software by offering a direct import of the tag names (S7 symbols) from the S7 project. These tag names represent input/output data, data blocks, flags, timers, and counters that can be read and written in the S7 controllers. This ensures that the tight link between the production operation and SAP is easily maintained.
Increased Efficiency in the Pizza Factory
Pizza was one of the first convenience products and is still as popular as ever. The choice is huge. Pizza comes in all shapes and styles from classic stone baked pizza to light and fluffy American style pizza. Over 200,000 frozen pizzas roll off a major German pizza manufacturer's production lines every day. The manufacturer continually develops new high-quality recipes in dialogue with their customers to meet consumer needs. Each time the product changes, the machines need to be cleaned and the facilities have to be retooled to accommodate the next style of pizza.
The cleaning process can take up to four hours depending on the type of pizza. To clean the facilities, the current shift staff stops the production line. In the past, for an assessment of overall equipment effectiveness, the production personnel had to document downtime. This was done manually by entering the start and end of the downtime into the production module of the SAP system. “Logging the production-stops automatically was not possible until the introduction of the SAP-Simatic coupling from Softing,” explains Gunter Nisseleit, Technical Director at the pizza factory. “With our traditional process setup, SAP controlled the gross production just by evaluating the costs per product in Euros.” In the past, while entering the downtime manually the production teams had to distinguish between downtime due to retooling or other organizational reasons and downtime due to unplanned machine failures.
Unfortunately, the hectic rush of the day-to-day business of retooling or repairing the production machines led to inaccuracies in entering the downtimes manually. Typically, the times entered were only estimates. Production stops lasting less than 15 minutes were not recorded at all. However, the sum of all of those failures adds up to a significant downtime at the end of the day, with a considerable negative impact on the result.
“Because of these habits, we were not able to record and analyze all downtimes and precisely assess the overall equipment effectiveness,” says Gunter Nisseleit. “However today, with increasing order volumes and our growing range of products, it has becomes very important for our company to close these gaps. The fact that Softing helped us to tightly couple SAP to Simatic controllers enabled us to analyze our processes more accurately, identify weak points, and optimize the processes. The SAP integration based on OPC technology from Softing provides our management with a complete and up-to-date overview of the production progress and performance at all times. Thanks to the resulting process optimizations, our investment in the OPC software and NETLink PRO actually paid for itself within just a few months.”
For more information, visit http://www.softing.com/opc.
For those who have acquired a taste not only for the technology, but also for a delicious slice of pizza, there is a huge collection of pizza recipes from classic to exotic at the following website.
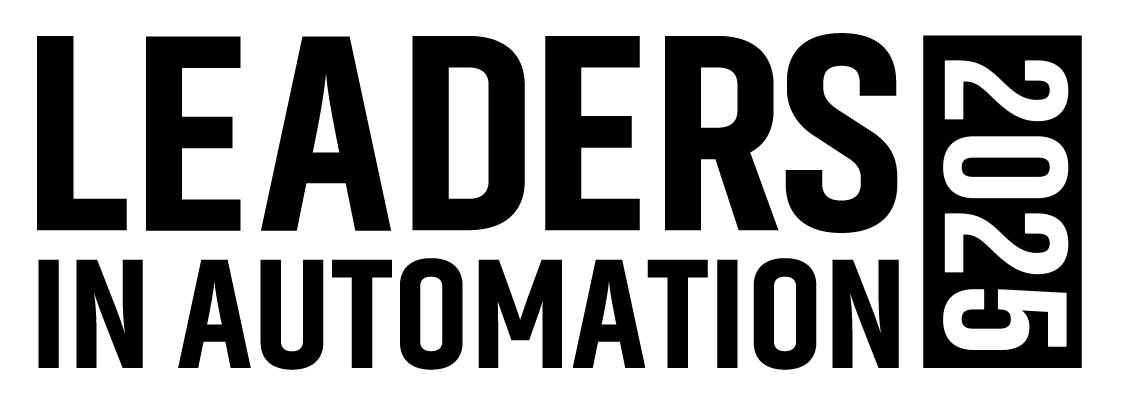
Leaders relevant to this article: