Sustainability today means different things to different people. First, sustainability requires a pro-active approach. The U.S. Department of Commerce (DOC) is committed to help businesses achieve sustainability. After analyzing feedback from a Sustainability and Competitiveness Summit last fall, it found that stakeholders face uncertainty regarding competing sustainability-related product and process information, data, metrics and standards (domestic and international). A Sustainable Manufacturing Initiative team, created to look at metrics for sustainable manufacturing, is developing a “toolkit” to be ready in 2010 to help companies assess and measure the benefits of implementing sustainable practices.
In some companies, sustainability is a philosophy. Others seek durability and quality in their equipment investments to achieve sustainability. In still others, sustainable manufacturing supports company efforts to revitalize a product line or integrate a corporate acquisition. The common thread is developing a sustainable practice that results in bottom-line savings. One of North America’s oldest and largest industrial pasta manufacturers is looking to achieve these savings with a sustainable expansion at its flagship pasta factory in Grand Forks, North Dakota. Philadelphia Macaroni Company (PMC, www.philamacaroni.com), acknowledges that an important component of that effort is the addition of a new pasta production line.
PMC recently expanded its Grand Forks facility to enhance sustainable practices, creating 12 new jobs. Executive vice president Bill Urban managed the multifaceted construction project and commented on efforts to incorporate sustainable systems at the site. Noting that the recent economic climate created a demand for pasta as a “center of the plate” dinner option and a need to increase production, he says, “It’s project design which will make us better corporate citizens in Grand Forks, allowing us to reduce energy and resource consumption while improving efficiencies.”
Sustainability is pro-active
A sustainable or “green” building results from a design which focuses on increasing efficiencies of resource use along with an organized effort to design and build facilities with processes and materials that promote environmental sustainability. Cost savings come through productivity, lower-cost building operations, and resource utilization including:
• Water conservation: a waterless vacuum pump is part of the new pasta line and will conserve more than 2 million gallons of water annually.
• Resource efficiency: locally available building materials, components, and systems were used to save transportation costs.
• Greenhouse gas reduction: an additional rail siding permits greater use of railroad transport of raw ingredients and finished product. (The American Association of Railroads states that railroads are at least three times more efficient than trucks.)
• Energy conservation: energy-efficient T5 lead-free fluorescent lighting provides long life.
Other improvements include 70 percent more plant capacity, 50 percent more warehouse space, pasta production lines with updated programmable logic controllers (PLCs), two new raw ingredient silos, and an integrated Warehouse Management System (WMS).
The family-owned business, headquartered in Philadelphia, has factories in Pennsylvania, North Dakota, and Washington and more than 200 employees. It makes dry, frozen and specialty pasta for industrial, institutional, and contract retail customers across an international customer base.
Philadelphia Macaroni mills durum and hard red spring wheat for internal use and for sale on the open market through its Minot Milling Company division in North Dakota. Pasta and milling facilities, Kosher- and Organic-Certified, operate 24/7 to meet demand.
According to family patriarch Luke Marano, Sr., “My grandfather came from Italy in 1874 and had a grocery business. Today we have the fifth generation here. We’ve been rather successful, especially since the demise of the low-calorie diet; pasta came back.
“When I started working, we came in and opened the valves and adjusted them and opened more valves. Now you put a program into a machine and it works by itself. If anything goes wrong, you call Italy via satellite and it’s fixed.”
A little over a year ago, PMC bought a new dry pasta production line from one of the largest pasta equipment manufacturers in the world, Italy’s Fava S.p.A. (www.fava.it). Marano says, “Our new Fava equipment handles 200,000 pounds a day. We have other Favas that are around ten years old. Laws are strict now and you need high temperature equipment to pasteurize your product. Fava is dependable.”
Executive VP Urban adds, “I bought it. We took a tour a few years ago in Italy and visited pasta companies and equipment manufacturers and formed an assessment based on capabilities and desire. We have built a relationship with all of them over the years. We also looked at auxiliary equipment, buckets and shakers, to complement the line. It was a stretch to buy bigger (we bought more size than we had originally planned). Historically, this industry was always growing. We got a Fava press and dryer in one, one of the largest lines. It’s computer-driven and gives us more capacity.”
Dry pasta is the shelf-stable product bought at the supermarket in small packages. PMC makes it at three production facilities. The complex, yet conceptually simple, piece of machinery is capable of producing 8,800 pounds per hour of dry pasta in shapes called short cuts. These include shapes such as elbows, penne, rigatoni, and noodles, radically different from spaghetti, linguine, and angel hair, the long cuts, and produced with totally different machinery. The production process is all performed within the line.
All phases are automatic, with the PLC monitoring the conditions of phases and making adjustments. Older pasta production lines, built by different manufacturers in different years, were already installed in the Grand Forks plant. But the new Fava line is much bigger (the second largest line in the plant produces 3,500 lbs/h) and represents the latest evolution in terms of pasta-drying technology.
Contrary to other production lines, it features a single drying unit for two main drying phases, with the pre-dryer and final dryer inside the same machine. This approach, first developed by Fava, significantly reduces the required footprint as two drying phases are positioned on top of each other. Heat use is more efficient because less is dispersed into ambient air and the machine is proportionally smaller, requiring less steel and aluminum.
Sustainability is philosophy
Meccanica Nova S.p.A. (www.meccanicanova.com), a manufacturer of CNC grinding systems for the automotive, aerospace and bearing industry, is going greener with a sustainable philosophy.
“We believe that our philosophy to reinvest profits back into our company has helped us maintain our benchmark status in the industry,” says Andrea Catone, director of sales and marketing. “Meccanica Nova has always been sensitive to the environment and the future of generations to come.”
The company’s high-production grinders are used in many industries to produce high-quality components to improve technologies and develop solutions. The machines produce components for fuel-efficient and low-emission engines, as well as for wind-energy turbines.
Meccanica Nova’s latest contribution to the planet is the installation of a self-sustaining clean energy system. The factory and headquarters in Bologna, Italy, were equipped with photovoltaic modules for producing clean energy, going online in the fourth quarter of 2008.
Installation was facilitated by the building’s construction. The roof is a multiple-shed type with a 14-degree angle of inclination to provide an optimized orientation of the panels to the sun, as well as its geographical orientation of 30 degrees S/W.
“The facility’s entire roof has been exploited, the total surface of 50,980 sq ft is covered by 3,425 photovoltaic panels,” says Catone. ”The system is capable of developing 648 kWp of maximum peak output, estimated to produce 738,720kWh/yr of clean energy.”
As of January 2010, the company has produced more than 75,000 kWh of clean energy since going online in 2008, and the system throughout the photovoltaic modules’ estimated life cycle will have contributed to the environment by saving 17,321.85 tons of carbon dioxide, 38,493.00 kg of nitrogen oxide and 43,262.18 barrels of crude oil.
Sustainability is durability
Made in Italy is not just a tagline; it’s a guarantee. North American users of Italian-manufactured equipment agree that durability is one reason they would seek out additional machinery from that country. It is as good as new years down the road.
Silvanus Products, Inc. (www.silvanusproducts.com) provides eco-friendly binders, which the company describes as “not just a binder or a passbook, but the face of a company.” Manufacturing these and similar products since 1929, the company has experienced many innovations and has “built a culture around product quality.”
Claiming dedication to product quality and craftsmanship, Silvanus depends on one machine for creasing and scoring, the Ariemat, manufactured by CMC ITALIA Srl (www.cmc-italia.com) in Italy. The computerized machine features auto-feeding and stacking, scores boards and makes spines for binders.
The device has done a lot of scoring over the last decade and operates constantly. Silvanus general manager Doug Campbell says, “We would certainly consider using additional Italian-made machinery and you can quote me.”
Today Ariemat comes in several versions, including an auto-creaser, a modular machine with high-power precision and adjustable blades; the Aries manual version provides double-register guides on the rear table and front multiple guides as options. Touch-screen controls are standard on all 2006 and later Ariemat models. Creasing programs can be set in seconds, stored and recalled with custom-made software capable of memorizing 100 individual creasing positions.
Sustainability is quality equipment
Crossville, Inc. (www.crossvilleinc.com), the largest domestic manufacturer of porcelain stone, operates the first U.S. tile plant designed to manufacture large-unit porcelain tiles. The Tennessee-based company is a member of the U.S. Green Building Council and is committed to protecting the environment through quality manufacturing processes and offering recycled and environmentally friendly products.
The company’s EcoCycle is the first porcelain tile with a certified recycled content of 40 percent. Scientific Certification Systems, an independent third-party certifier of environmental claims, conducts regular audits of processes and assures that EcoCycle is in compliance. Crossville porcelains do not emit or absorb pollutants.
“It’s always been Italian machinery,” says plant manager Roger Buck. “From the time we began manufacturing in 1986, the technology and manufacturing machines that we use have always been Italian. We have no American equipment. We recently installed a new Sacmi Imola S.C. 7500 (www.sacmi.com), a good press, and we also use equipment from Pedrini S.p.A. (www.pedrini.it), which does a good polishing job, world-renowned SITI B&T GROUP S.p.A. (www.siti-bt.com) and BMR S.p.A. (www.bmr.it) machinery.
“We’re in position to rev up,” says Buck. “We are one of the leading porcelain tile manufacturers and have won awards for our processes.”
The company’s wastewater policies exceed government standards and have earned several citations for effective wastewater practices. Water used in tile manufacturing is returned clean to its natural habitat.
Crossville maximizes use of natural gas, a clean-burning and efficient fuel, which helps alleviate negative impacts such as greenhouse gas emissions, smog, acid rain and water pollution. Its dust collection procedures not only limit air pollution, inside and outside the plants, but also allow reuse of unfired raw scrap materials during manufacturing. While such reuse does not constitute recycling, it does minimize landfill deposits while conserving raw materials.
The company’s Environmental Commitment Task Force comprises representatives from each operational unit to evaluate current practices for efficiency and environmental impact and to recommend future innovations to establish Crossville as the environmental leader in the tile industry.
Sustainability is savings
Albany Chicago Company (www.albanyc.com), founded in 1952 on Albany Street in Chicago, produces highly engineered aluminum die cast parts. The company, now located in Pleasant Prairie, Wisconsin, employs more than 300 people.
Known for machining to tight tolerances for its customers, original equipment manufacturers in industries such as diesel engines, hydraulics, electromechanical devices, computers, health and agricultural equipment, the 190,000-sq-ft facility operates three shifts five to six days a week.
Operations leader Curt Pape praises the Bosello High Technology Srl (www.bosello.it) equipment installed last June. “It works very well,” he says. “We love the equipment and the technology is outstanding. It has auto defect recognition (ADR); we use it for X-ray machines.
“We did a lot of looking before we bought. Bosello could meet delivery and was in our budget framework; this is our first unit. We were invited to visit them, but it’s hard to get away to Italy. However, we saw video demonstrations and we have a local U.S.-based support source.
“Our equipment is used with structural thin-walled aluminum high-pressure die cutting for shock components for BMW. These are called shock towers and they have to be free of porosity. The software looks for certain defects, taking 11 different images per part to see all aspects and makes a decision based on that. Previously we had manual X-ray. This is sustainable and is environmentally friendly in a self-contained cabinet.”
The equipment has a modest footprint about 8 ft wide by 10 ft deep. Only one operator is necessary, and an automated pallet changer saves on labor. With ADR, data can be deciphered to eliminate problems.
Bosello High Technology Srl, founded in 1962, specializes in non-destructive testing and in industrial radioscopy.
Sustainability supports growth
Jones & Vining (www.jonesandvining.com) was incorporated in 1930 to produce wooden shoe lasts. In 1967, it merged with the largest manufacturer of women’s shoe lasts in Canada; in the 1970’s the wooden last was replaced with plastic and J&V introduced the unit sole.
After moving operations to Lewiston, Maine and the addition of factories in Conway, New Hampshire and Iberville, Quebec, growth was sustained through acquisitions and the introduction of polyurethane-based unit soles to the U.S. market.
“We really like the Italian equipment for its simplicity of design, operation and maintenance,” says technical director/production manager Rick House, who oversees material, product development and manufacturing.
“We presently use five Plastak Engineering Srl machines (www.plastak.it), and two component polyurethane casting machines with 40-station rotary turntables. Two of these were retrofitted with GUSBI Officina Meccanica S.p.A. (www.gusbi.com) mixing heads. We also have four single-color Lorenzin extruder injection molding machines and five 2-color Lorenzin extruder injection molding machines from Nuova Simplast di Lorenzin Vincenzo & C. SNC (www.simplast.com), plus two Main Group S.p.A. (www.maingroup.com) 2-color ram injection machines.
“The business sees its share of employee turnover, and training is relatively easy with the Italian equipment. We would buy similar equipment in the future for those reasons.”
Sustainability is immersion
Wigwam Mills, in business since 1905, produces high-quality hosiery products and related accessories for the specialty sporting goods market. Some of its larger customers include REI, Gander Mountain, Cabela’s, Dick’s Sporting Goods, and Marks Work Warehouse in Canada.
“We have always been located in Sheboygan, Wisconsin,” says vice president of operations Jerry Vogel, “and all our socks are produced in the U.S. We moved to our current 200,000-sq-ft location in 1974, and employ 250 full-time people.
“Several of us make trips to Italy on an annual basis to visit manufacturers and look at the latest in machine technology. We continue to work very closely with Italian manufacturers, inviting them to our factory as well.”
Wigwam Mills has machinery from Sangiacomo S.p.A. (www.sangiacomo.com) and Matec S.p.A. (www.matec.it), Lonati S.p.A. (www.lonati.com), Nuova Marctex S.p.A. (www.nuova-marctex.com), Conti Complett S.p.A. (www.complett.it), Cortese S.p.A. (www.cortese.it), and Autotex Italia Srl (www.autotex.it) machinery, all designed and built by Italian manufacturers. The Sangiacomo, Lonati, Matec, and Nuova Marctex are all circular hosiery knitting machines used to knit socks.
The Conti Complett machines are looping (sewing) machines used to close the toe on socks. The Cortese machines are boarding machines used to press and form the socks to remove the wrinkles.
There are several different types of Autotex equipment. One is used for boarding socks like the Cortese. A second is used to store and stack socks after they come off the boarding machine, before they are paired. A third is used for packaging. These packaging machines prepare packaging and attach socks, using various types of packaging and different types of fasteners. The last Autotex machine forms and applies stickers to boxes.
According to Vogel, “We have 29 Matec knitting machines purchased in 2000.The 20 Lonati machines were purchased in the mid-1990s. The 64 Nuova Marctex knitting machines were purchased between 1994 and 2008. We have 200+ Sangiacomo knitting machines that range from 1997 to 2009 models. The Conti Complett looping machines were purchased in 1996-97. The Cortese boarding machines arrived in the mid-1990s. All of the Autotex machinery has been purchased since 2005 -- 6 boarding machines, 6 stackers, 5 sleeve packaging machines, 1 banding machine, 1 rider packaging machine and 1 box erector.
“Most of the machines provide unique or specialized technology; that’s why we purchased them. Productivity and efficiencies are also considerations. As a result, we continue to evaluate new Italian machinery for the latest in machine technology.”
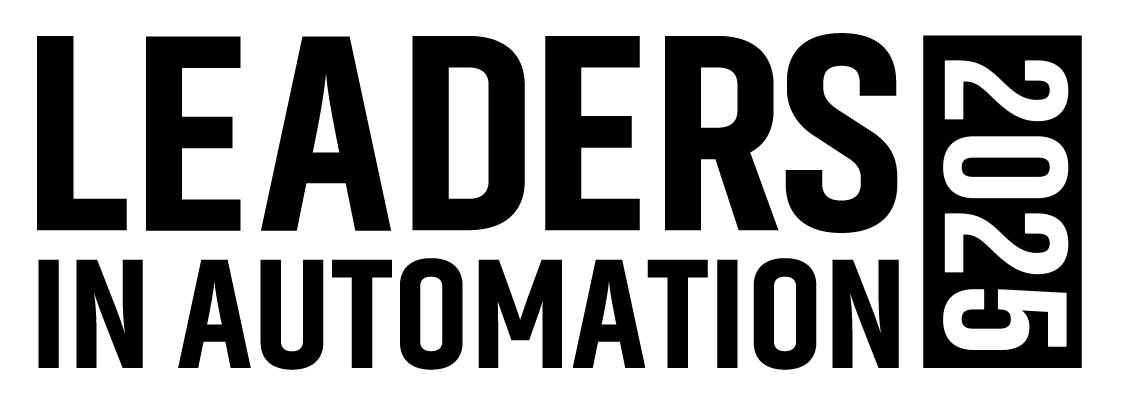
Leaders relevant to this article: