Over the past several years, Ethernet has made an impressive footprint on the plant floor, becoming the de facto standard for most new installations and expansions. But fieldbuses like PROFIBUS show no signs of fading away soon, making it important to understand how they work together.
Ethernet has been beefed up by many companies and trade groups so it can work in harsh industrial environments without sacrificing the compatibility that makes the standard valuable. One of the most popular of these ruggedized versions is PROFINET, which carries many of the traits that made PROFIBUS a dominant technology during the first phase of industrial networking.
Sales of PROFIBUS products are continuing to grow even though many observers have predicted that older fieldbuses would see declining sales. Though the low cost and proven reliability of this well-tested technology provide a big lure in some product categories at the low end of the technology spectrum, there’s a clear trend for higher-level connectivity.
“When you’re building something new, PROFINET makes sense,” says Carl Henning, deputy director of the PTO (formerly the PROFIBUS Trade Organization) in Scottsdale, Ariz. It can connect to front office systems without gateways, and it offers more address space than PROFIBUS. It can also handle up to 150 axes of motion, far beyond the 30 that PROFIBUS can provide.
Then there’s the newer network’s overwhelming speed advantage. PROFINET moves a lot of data, running at 100 Mbits/second, carrying telegram packages that hold 1,440 bytes. PROFIBUS is much slower, though it still offers more than enough speed for many industrial products. The fieldbus runs at 12 Mbits/second, carrying 244 byte telegrams.
However, PROFIBUS isn’t fading away. There are already more than 30 million nodes in the field, and the market has to date defied the predictions that sales would start declining. That success means all sorts of industrial products offer PROFIBUS connectivity. “PROFIBUS has been around a long time so it’s easy to find products with PROFIBUS,” Henning says.
The time-tested fieldbus has also been upgraded to meet needs that other networks can’t address. For example, it’s one of the few connectivity schemes that can be used in intrinsic safety applications like oil refineries where a spark can cause an explosion.
For these and other reasons, linking to existing fieldbuses is one of the critical items for all the variations of Ethernet that target industrial applications. PROFINET makes this critical link much simpler than with some other networks. Unlike alternatives, it uses proxies, which are similar to gateways, to handle the mapping that converts data streams from one protocol to another.
The proxy approach offers more standardization than gateways, which are more closely tied to a single company. PROFINET proxies are part of the PROFINET specification and have also been adopted by Interbus, so any of the devices that use that fieldbus scheme can be linked to PROFINET with minimal effort just as PROFIBUS can. The proxy concept works so well that it has been used for connecting many other networks.
Another important factor for success is the time it takes to become comfortable with the technology. When engineers who haven’t worked with PROFINET move up, their learning curve will be fairly short. “The similarities between PROFIBUS and PROFINET are striking," Henning says.
Though PROFINET uses the important facets of Ethernet to provide compatibility, it also brings many expanded capabilities. “It’s really a different protocol that leverages the concepts of Ethernet versus other approaches," Henning says.
“We’ve found some clever ways to use Ethernet so we can do motion control with 1 millisecond update times," Henning says.
PROFINET also lets controllers talk directly to each other. Peer to peer communications helps to integrate different machines into a production line. PROFINET calls this component-based automation (CBA). For example, when machines need to share complex information like tracking or sending serial numbers between machines, CBA lets users configure the necessary communications using graphic interfaces rather than using more complex PLC programming.
The networks also shine when it comes to another critical requirement in today’s factories, functional safety. PROFIsafe sits on top of the basic networks – both PROFIBUS and PROFINET - making it very simple to create functions that can protect operators from injury or prevent machines from causing damage to themselves or things that are nearby.
PROFINET also provides determinism, even though Ethernet does not provide assured delivery for messages. Like most other Ethernet-compatible solutions, PROFINET uses the TCP/IP layer, which resides on layers three and four of the conventional ISO reference model for networks.
Since TCP/IP doesn’t guarantee delivery of time critical data, PROFINET skips the TCP/IP layers to reduce variability and improve determinism. For even greater improvements, PROFINET uses a technique called bandwidth reservation. Reserving time on the network for critical message guarantees that they won’t be delayed by collisions or other traffic. PROFINET also provides scheduling, which is important for motion control. The controller knows the topology of the network, and it uses this information when it’s broadcasting instructions to many nodes.
Messages going to the most distant nodes are sent before those going to nodes closer to the transmitter. This approach helps to ensure that messages arrive at the desired time.
While PROFINET brings a number of benefits to the plant floor, it also shines in one of the areas that initiated the drive to extend Ethernet into factories. It makes it easy for industrial equipment to communicate with business systems, giving front office managers greater insight into production.
It’s not enough that the plant and office systems both use Ethernet which only defines the cabling and signaling aspects. The messages also must be in a format that both systems can understand.
The ISA 95 standard was developed to reduce the cost, risk and errors associated with implementing interfaces between enterprise resource planning (ERP) and manufacturing execution systems (MES). PROFINET parallels ISA 95 communications, but from the plant level up to the MES level.
The standard specifies a generic activity model that applies for different types of manufacturing information such as production, maintenance, inventory, and quality. The PTO has completed a maintenance profile and is moving ahead with the other three.
This type of continuing evolution adds value to PROFINET and PROFIBUS, making them effective technologies in any sort of industrial applications.
For more information on PROFINET, please click here.
For more information on PROFIBUS, please click here.
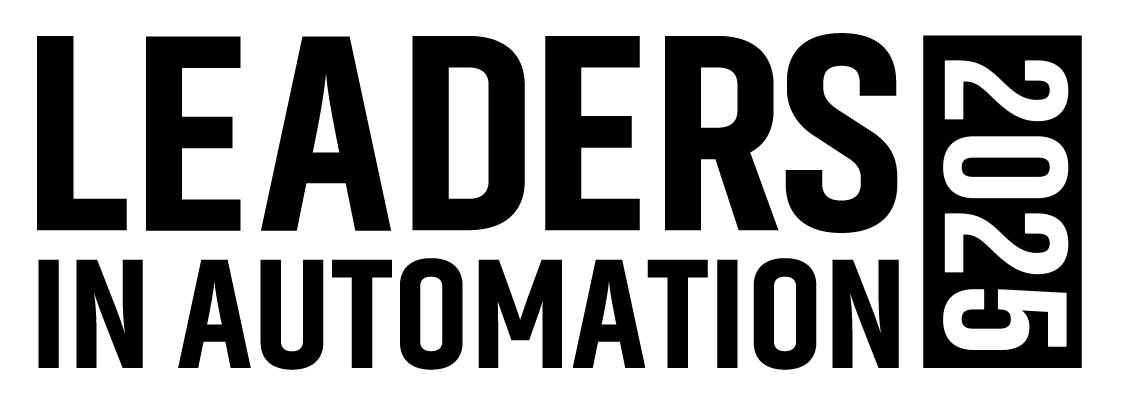
Leaders relevant to this article: