Blue Bell Creamery of Brenham, Texas, is busy installing its thirteenth robot, packaging ice cream in one of its three plants across the Southern United States. But Blue Bell was not always so automation-savvy, as company Vice President of Operations and Associate Director Gene Supak relates: “With the earlier models, speed was an issue, and cost was an issue. Over the years, the robots have gotten faster, and the prices have come down. We have looked at automation for years, and the pricing was just out of reach. In the last 10 years, the pricing has gotten to a point where it’s economically feasible.”
Supak’s experiences mirror many packagers’ who, once intimidated by the high price tags and complex electronics of automation, are now successfully employing robotics that offer enhanced flexibility with great success. Wolfgang Candy is a good example.Candy pick & pack
Increased volume was the catalyst for a new packaging line with robotic pick-and-place at Wolfgang Candy Co., one of the oldest family-owned and managed confectionery manufacturers in the United States. From the time it was incorporated in 1921 until six years ago, the York, Pa.-based company primarily operated in the fundraising sphere. With the takeover of the business in 2003 by the family’s fourth generation, Wolfgang expanded into new areas, including contract and private-label packaging, and production and packaging of its own brand of chocolate and non-chocolate confections for retail sale.
Wolfgang’s 100,000-sq-ft operation, consisting of three buildings in a one-block radius, now produces close to 120 different stock keeping units on 14 lines. Given the flexibility required to meet its range of customer needs, packaging for Wolfgang’s products has remained almost exclusively manual. “Without any automated systems, it’s as flexible as a human being,” relates Robert L. Wolfgang III, managing partner responsible for Food Safety and Quality.
Until recently, Wolfgang hesitated to add automation to its packaging lines because of the poor return on investment (ROI), once space requirements and production volumes were considered. “In the past, when we ran through the real numbers, the return on investment wasn’t there,” says Wolfgang. “As we pursued different markets, we realized increased volumes and larger production runs. Then all of a sudden, automation made sense.”
In June, Wolfgang installed a new tray-packing line, specified and integrated by JLS Automation, York, Pa. New equipment includes a tray denester/placer from FEMC, Bedford Heights, Ohio, a Carrera horizontal wrapper from Ilapak, Newtown, Pa., and the JLS Talon Series dual-robot packaging system. The Talon features two IRB 340 FlexPicker robots from ABB Robotics, Auburn Hills, Mich. The top-mounted robots, nicknamed “Lucy” and “Ethel” by Wolfgang operators, inspect product and then pick and place it into thermoform trays accurately and reliably.
Explains Wolfgang Managing Partner and Chief Marketing Officer Mike Schmid, one of Wolfgang’s chief requirements for the new line, and for the robot in particular, was the ability to gently handle a range of product types—from well-defined, molded candy pieces to candy bars, both with inclusions and plain chocolate bars, to molded plaques, such as Easter bunnies and Santa figures.
Says Wolfgang, “What JLS has given us is flexibility, because it is a pick-and-place system and not a dedicated, hard-
engineered system. We can pick and place nearly anything.”
Another expectation for the robot, says Wolfgang, was speed. The company was looking for a system that could meet or exceed 200 pieces/minute. Lastly, it needed a solution that could fit in a defined footprint.
The new line is currently running two types of cookie products containing a molded piece of chocolate in the center. After the cookies are produced, they are delivered by conveyor to the JLS system. Product is conveyed at a constant speed through an existing metal detector and then onto the robotic-picking belt.
On the picking conveyor, product location is identified with a camera, and each cookie is analyzed to check that most of the top surface is covered with chocolate. Product that passes inspection continues on the picking line. Operating on-demand, the tray denester provides a tray to each wrapper flight. Tray presence is verified with a sensor. The robots then pick each cookie, with vacuum technology developed by JLS, and place them individually into a tray on the flow-wrapper infeed conveyor. The flow wrapper operates intermittently and ensures that all trays are completely filled via communication with the robot software before trays leave the robotic work cell.
Since it was installed, the line has met Wolfgang’s productivity expectations, from both a speed and a flexibility standpoint. Automation certainly provides some other benefits over manual operations as well, says Wolfgang. “The robot doesn’t take any breaks, and it doesn’t call in sick,” he says. “So far, it has been very reliable. It doesn’t stop.”
As for ROI, “the cost is worth it,” says Wolfgang Chief Executive Officer Benjamin A. McGlaughlin. “We will realize a return in a relatively short time period. So the results are well worth the investment.”Robotic shot in the arm
In Rosia, a small town near Siena, in Italy’s Tuscany region, vaccines for threatening illnesses—among them influenza, polio, diphtheria, tetanus, rabies, meningitis, and others—are produced and packaged by Novartis Vaccines & Diagnostics, a division of Swiss-based Novartis AG. Novartis is the fifth-largest vaccine manufacturer in the world and is the second-largest supplier of flu vaccines in the United States.
To preserve a safe and sterile environment, everyone at the Novartis plant in Rosia has to respect Good Manufacturing Practices (GMPs). Here, up to 35 different vaccines are prepared and packaged for shipment to 70 countries around the world. The only workers who don’t have to follow the GMP-mandated dress code are three hard-working robots from ABB Robotics.
The first robot to be installed at the plant was an IRB 660 FlexPalletizer palletizing robot in 2005. The IRB 660 is equipped with two scanners and sorts cases arriving on a conveyor belt by reading their bar codes. Depending on their contents and destination, it places them on one of three pallets for shipping. “The shapes of the boxes change significantly for different markets worldwide,” says Carlo Romani, process engineering manager for secondary technical operations.
The robot is designed to do the placement in a way that ensures maximum stability in the loading of the pallets. The palletizer has proved so fast and reliable—replacing the work of up to three employees—that it will soon be moved to a larger area where it will load six pallets at a time.
The second robot, the IRB 340 FlexPicker pick-and-place robot, arrived at the plant in 2006 and is used primarily in packaging oral vaccines for polio. The IRB 340’s advanced vision system is an essential component of the production process because it has to pick up each polio cartridge individually from a conveyor belt and position it correctly in a box of 20 cartridges. Here, as with the palletizer, several checks for accuracy and precision are built into the process.
The most recent and most innovative robot application, according to Romani, is the IRB 260 robot denester, which became operative in March 2008. “This is a very innovative and sophisticated application, and we are the first pharmaceutical company to implement it,” he says. The IRB 260 anchors a new, 131-foot-long packaging line for flu and meningitis vaccines that handles up to 500 syringes/minute and involves three separate operations, formerly done manually, which risked human error.
During operation of the packaging line, flu syringes in lidded plastic tubs arrive from the aseptic department after an inspection phase. Each tub contains a nest of 100 syringes. In the first automated operation, the robot removes the lid of each tub by vacuum. It then lifts the nest and places it on a conveyor belt. “This is a delicate step because a tub’s contents may be worth thousands of euros,” says Romani.
During this process, a telecamera on the robot’s head matches the contents of the tub with the tub and lid by way of datamatrix codes. This is done to ensure that there has been no cross contamination of vaccines. Three verifications are performed, and if something is amiss, the operator is alerted.
In the final step, the empty lids and tubs are then positioned separately on a pallet for reuse. The positioning has to be precise because, in the course of a year, several million lids and tubs will be handled, and GMP for the pharmaceutical industry requires strict separation of packaging materials and products.
“This ABB robot is oversized and can handle much heavier weights than are used here, but it is perfect because of its speed and precision,” says Claudio Boncompagni, in charge of validation for Fill-Finish (packaging) Operations.
As for the syringes, after being placed on the conveyor, they advance to the next station on the line for final packaging before distribution.
Use of the IRB 260 robot denester allows for complete control of tubs coming from the filling department, the same level of accuracy in handling for each nest of vaccines, and a reduction in safety issues close to the packaging machine, notes Romani.
He adds that Novartis’ use of robotics has enabled the company to achieve better pallet management, additional control of materials, a drastically reduced risk of cross contamination, and a reduction in manual activities having a heavy ergonomic impact.Ice cream automatons
Eliminating a repetitive and chilly job from its packaging process was the goal of Blue Bell Creamery’s Sylacuaga, Ala., plant when it installed four robotic systems to replace manual palletizing for a number of its ice cream packaging lines. Blue Bell, headquartered in Brenham, Texas, offers the third best-selling ice cream in the United States. To guarantee the quality of its product, Blue Bell retains control over all aspects of its business, including production, packaging, and even shelf stocking—drivers of Blue Bell’s delivery vehicles personally stock store shelves in the 18 southeastern states where the product is sold to ensure proper product handing.
In the past two years, Blue Bell has equipped three of its existing palletizing stations at Sylacuaga with Fanuc M-410iB four-axis, electric servo-driven robots from Fanuc Robotics, Rochester Hills, Mich., specified and integrated by Flexicell, Ashland, Va. A fourth M-410iB robot has been installed to accommodate product from new production lines at the facility that, as of press time, were nearing completion.
“The work is being done in a refrigerated area that can be anywhere from 35 to 40 degrees Fahrenheit,” explains Blue Bell’s Gene Supak. “The work is very labor-intensive, very repetitive. All the operators were doing is stacking ice cream all day long, so it was difficult to keep staff in that area.”
Product being palletized on the lines consists of individual three-gallon containers, one-pint ice cream containers packed 10 to a corrugated case, three-ounce cups of ice cream packed 48 to a case, and half-gallon containers wrapped four to a corrugated sleeve. Each palletizing station is fed by a minimum of two packaging lines, each of which first feeds into a common hardening system that freezes the ice cream product. During the process, multiple product types become intermixed and require sorting before palletizing.
“When we were manually stacking product, we had a long line of people visually picking out the product they needed to stack,” says Supak.
To automate the palletizing process, Blue Bell approached several integrators, but they “just didn’t have an answer” for the company, says Supak.
One challenge was the fact that Blue Bell reuses its shipping cases and sleeves anywhere from six to 10 times, causing wear and tear on the corrugated cases, explains Blue Bell engineer Russell Halfmann, project engineer for the robot installations. “They get rips in them, they get holes in them, they get soft from coming in and out of the cold,” he explains. “This can make them harder to handle.”
Another obstacle, he adds, was keeping product stable in the open-ended sleeve during palletizing. “There is a certain amount of inertia at that speed that wants to fling that product out,” he says.
Space was another challenge—installing equipment on existing lines meant very tight areas in which to work.
For all of these concerns, Flexicell was able to meet Blue Bell’s requirements. “The robots we are using are common to the industry,” says Halfmann, “but we liked Flexicell’s method of integration and material handling. They were willing to adapt to our existing conveyors and components, and had a knack for tailoring the solution to our specific needs and space requirements.”
Custom-engineered end-of-arm tooling consists of a series of vacuum cups that can lift three to four cases or multiple three-gallon containers at once. For sleeve applications, the robots also use mechanical grippers that clamp down on the ends of the load to keep product from flying out. The robots were programmed by Flexicell and “tweaked” to Blue Bell’s specifications during start-up. Programming is performed using Fanuc’s PalletTool handling software, with robot control handled by an Allen-Bradley CompactLogix PLC from Rockwell Automation Inc., Milwaukee.
Supak estimates that replacing manual palletizing with automation has allowed Blue Bell to eliminate four to five operators per line. “In the past, we would have had five people sorting and stacking ice cream,” he says. “Now we are doing the same thing with one person and two robots.” In the future, Blue Bell plans to automate product sortation as well—a process that is already incorporated on some other lines (Blue Bell has a total of 13 robots operating within its three production facilities) using a system of sensors, supplied by Flexicell.
Supak notes that the robots have also allowed for greater precision in product placement during palletizing. “The repeatability is phenomenal,” he says.
As a final comment on the project, Supak applauds Flexicell’s skill at installing the robots while Blue Bell continued production, working on one section at a time to minimize downtime. “They had the systems pretty well designed and tested in their shop before they shipped them out,” he says. “So the robots were proven out with very little time required for debugging once they were installed.”Related Sidebar - Contract Packager Crafts Portable, Flexible SolutionTo read the article accompanying this story, go towww.automationworld.com/feature-5968.
Subscribe to Automation World's RSS Feeds for Feature Articles
Companies in this Article
Companies in this Article
Sponsored Recommendations
Sponsored Recommendations
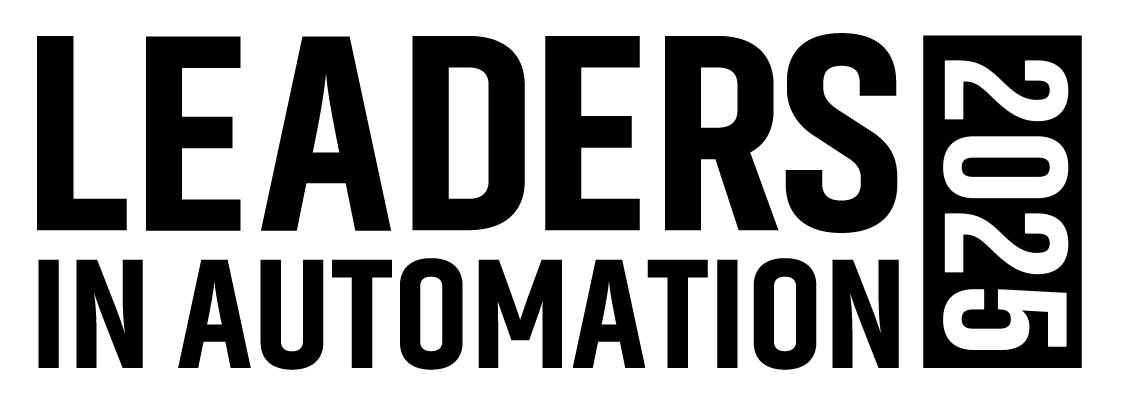
Leaders relevant to this article: