Search for articles on wireless technology in packaging and you’ll find a number of them. Chances are, though, that most of them will have been published in the last year. That’s because wireless technology, apart from some radio frequency identification (RFID) applications, has been slow in coming to packaging. Chris Kozup, senior manager, mobility solutions, for network component supplier Cisco Systems Inc., San Jose, Calif., gives some insight into this chronological oddity.
“It’s easier from a cost perspective to integrate Wi-Fi or wireless into equipment for broad market segments. When you’re dealing with more specialized or highly verticalized equipment like packaging machinery, there is sometimes a bit of a delay. That’s why the level of adoption in packaging has yet to reach the level of some of the other industries.”
That’s changing quickly, as the sudden spate of articles mentioned above indicates. Why? Vendors would no doubt cite the rapidly growing number of wireless-enabled products relevant to packaging applications. There is certainly some truth to that. But more significant—and a major reason why vendors have been more eager to jump into this field—has been the rapid development of wireless standards, providing equipment users with higher levels of device suitability and interoperability.
Of the many standards that impact wireless technology, three are most relevant to industrial applications. These are WirelessHart, ISA100, and IEEE 802.11n.
The WirelessHart standard, published in September 2007 by the Hart Communication Foundation, was accepted by the International Electrotechnical Commission (IEC) as publicly available specification IEC/PAS 62591Ed. 1 in September 2008. In April of this year, the International Society of Automation’s ISA100 Standards Committee on Wireless Systems for Automation voted to approve the ISA100.11a, the “Wireless Systems for Industrial Automation: Process Control and Related Applications” standard. Though currently in draft stage, ISA100.11a is expected to become a full-fledged standard soon. In addition, work is underway to bring WirelessHart and ISA100.11a into convergence as a new standard, ISA100.12.
Arguably of even greater significance has been the growth of IEEE 802.11 and its various iterations (802.11a, b, and others), the Institute of Electrical and Electronics Engineers standard for wireless local area networks (LANs). This is Wi-Fi, short for Wireless Fidelity, the wireless technology in our laptops and Internet-enabled phones. Because the technology is so widely employed, Wi-Fi chips and circuits have become very inexpensive, which, of course, helps push down equipment prices. Perhaps its most widespread use in industry today, including packaging, is in remote bar code scanning (and often, concurrently, bar code printing) with handheld devices.
This is one of those “What’s not to like?” applications, providing real-time snapshots of the inventory that is actually on the plant or warehouse floor, as opposed to what is merely supposed to be there. But while it illustrates some of
the strengths of today’s industrial wireless technology—mobility, ease of deployment, real-time data from uninstrumented assets—it also points up some of its weaknesses. This is an application that doesn’t require the exceptional speed and accuracy needed for control and real-time quality monitoring. Similarly, robustness is not a major issue in handheld bar code reading—a brief, unexpected delay due to interference, say, is no big deal. That’s not the case in mission critical applications. And security isn’t an issue. Again, that’s not always the case.
The wireless community is aware of these roadblocks and is striving to address them with a new version of 802.11—IEEE 802.11n. This new version will provide for greater bandwidth, speed, reliability and security, along with more protection against interference.
“802.11n is the next wave of wireless technology,” declares Cisco’s Kozup. “It is where customers should be placing their money when they make investments in wireless, because it’s going to have the longest lifetime of any technology that’s out there in the market today.”
Highlighting only two of the many advantages in the new standard, Kozup stresses that 11n will provide for six to seven times more bandwidth than previous versions, and perform much more reliably and predictably in industrial environments. “I’m talking about environments that have large ceilings, a lot of metal machinery, shelving units, motors—11n is very well suited for those environments.”
Knowledgeable observers have predicted that 11n will be finalized by November. Kozup confidently predicts otherwise. “We expect that on Sept. 9, the IEEE will finally ratify the 11n standard. This should remove the last hurdles to customer investment in the new technology.”
He goes on to note that already, some 600 products have been certified as 11n compliant by the Wi-Fi Alliance. Only a small number of these, though, are handheld devices. “A lot of the handheld devices like scanners or printers still tend to use the older technology, but over the next 12 to 18 months, we expect to see the 11n silicon come down in price and footprint to the point where it can be supported by most of these mobile devices.” Because IEEE 800.11n is backward compatible, these new devices will work with existing applications, In fact, they can be expected to bring some performance and reliability improvements to many of those existing applications.
As mentioned above, 11n also enhances Wi-Fi security. Wireless security in general has been a major concern for many potential users. Earlier this year, research firm Frost & Sullivan looked at key Western European economies in a report titled “Wireless Devices Market in Factory Automation,” and found that the market, while growing, is being held back by user concerns over security, as well as interoperability and reliability. Packaging was not specifically targeted, but the food-and-beverage sector as a whole was studied.
IEEE 800.11n should help to reassure such users, but Ben Orchard, systems engineer for automation and control vendor Opto 22, Temecula, Calif., argues that what’s needed in this respect is not just standards, but education.
In reality, he says, industrial wireless security standards are already high, even apart from 800.11n. “The earlier WEP (Wired Equivalent Privacy) security algorithm, which was found to have serious flaws, has been superseded by much stronger and more secure transmission algorithms. Wi-Fi Protected Access (WPA), including the Temporal Key Integrity Protocol (TKIP), replaced the older WEP algorithm in 2003. The more recent WPA2, introduced in 2004, uses the even more secure Advanced Encryption Standard (AES) 802.11i algorithm.”
Orchard says that WPA2’s AES algorithm is compliant with the National Institute of Standards and Technology’s (NIST) FIPS 140-2, which is required by some government agencies. “These standards can protect a robust communication system. Hopefully,” he adds, “in the near future, wrong-headed assumptions about a lack of security with wireless will begin to wane.”Not more, but different
Still, just because major hurdles to investment in wireless technology are falling doesn’t necessarily mean that manufacturers in general, and packagers in particular, should invest in wireless. Wireless technology brings with it the promise of greater communication, but if you have implemented, or are implementing, wired Ethernet communication throughout your facility, you could be excused for asking the obvious question: How much communication do I need?
The proponents of the technology, who increasingly include major automation vendors, provide a variety of answers to that question, but they can collectively be boiled down to the following: Not just more, but different.
Cisco’s Kozup again: “Wireless allows for the simplification of processes.” He is speaking here primarily of the ability to check on equipment without being tethered to a wired connection. Even in a highly wired situation such as an automated packaging line, not all desired information is automatically captured, and many peripheral systems are not as completely integrated as the machines on the line. But mobile workers equipped with a laptop or handheld device can simply walk over to a machine or panel, enter the desired information, and instantly relay that information to the control system, maintenance database, enterprise resource planning (ERP) system or wherever it needs to go. Not only is it quick and simple, it is also much cheaper than running new connections to outlying pieces of equipment.
Similarly, alarming, or notification of existing or impending malfunction, is a vital function, one not uniformly covered throughout the plant. Here again, wireless technology can provide a simple and cost-effective alternative. Companies are rapidly moving into this space with quickly deployed systems employing small, phone-like devices that reside within a machine or panel and communicate to a designated recipient when something is amiss. Think of it as a cell phone call from an outlying machine telling you all is not well.
Regulatory compliance, particularly in the area of temperature monitoring employing so-called “lick-and-stick” temperature sensors with wireless communication capabilities, is another current wireless application that is expected to see significant growth.Capturing the unseen
As significant as these applications may prove to be, for Charles Mohrmann, vice president at vendor Wonderware Mobile Solutions, Houston, the real promise of wireless lies less in expanding the present applications than in exploring what he calls “the art of the possible.”
To begin that exploration, says Mohrmann, we must consider not just the equipment, but also the people who operate and interact with that equipment. “Don’t just think of how to improve the equipment’s performance, but how improve the performance of the people and the equipment, because no matter how much we automate, human decision-making still factors in significantly into all of the production processes.”
He notes that field workers are the ones who are closest to the equipment and the processes. “They are the folks who feel the heat, hear the noises and see the changes that can be the first indicators of trouble. These people frequently do their jobs based on individual experiential knowledge acquired over many years.” Years of massive investments in automation have yielded obvious benefits, but, he says, they have also made it more difficult for management to access this hard-won shop-floor knowledge, or in some cases, even realize that it exists.
Wireless technology can help management and workers capture, share and employ this knowledge. How? Mohrmann cites a plant with three shifts, one of which consistently outperforms the others. “Why is that? It may be a case of more experienced workers on that shift who are doing visual inspections, or who recognize certain sounds that other workers don’t, or are performing simple informal diagnostics while the line is running. Once you understand the differences, you can begin to capture and replicate those best practices.”
A wireless-enabled handheld computer is the best way to make those best practices available to those who can use them, says Mohrmann. “In addition, these devices can help bring field workers into the automation loop by providing a bidirectional flow of data between them and data historians, enterprise asset management systems, ERP systems, visualization tools and the like. And of course, their experience can also enrich the quality of the information in that loop.”
Leo Petrokonis, business development manager, packaging industry for automaton vendor Rockwell Automation Inc., Milwaukee, has a similar vision. “As individuals today, we communicate in a wireless fashion, but that hasn’t yet made it to the plant floor.” It should, he says, as it could empower workers and, ultimately, management.
Petrokonis cites eight ounce bags of potato chips. Often, when these hypothetical chips are run, certain anomalies occur that result in less than optimal performance. Management sees only the results and not the look, sound and feel of the equipment and product when these events occur. Experienced workers equipped with handheld computers could capture and share that information, initiating potentially far-reaching process improvements, and, equally as important, a transformation in their own relationship with the process.Related Sidebar - Solving Slip Ring HasslesTo read the article accompanying this story, go towww.automationworld.com/feature-5966.
Subscribe to Automation World's RSS Feeds for Feature Articles
Companies in this Article
Companies in this Article
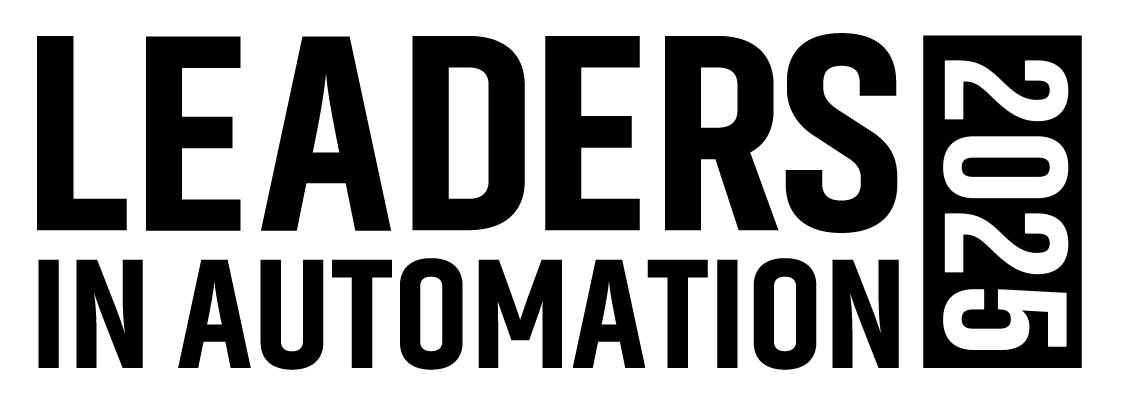
Leaders relevant to this article: