When engineers at Automated Interface Solutions go into sheet goods production facilities to install gauge systems, communicating with some of the commonly used hardware often poses a big problem. Installed equipment uses a range of systems, forcing engineers to employ gateways that don’t help achieve the goal of increasing productivity and precision.
In a recent installation that mirrors many others, the gateways were already a source of headaches, causing many shutdowns. The AIS customer that produces an array of polypropylene-based products wanted both improved quality control and enhanced reliability. That meant AIS had to fix the networking problem.
“In the old system, the networking schemes were mostly serial links, with data that had to go through custom-built gateways. There were a lot of issues with reliability that resulted in many thousands of dollars in lost productivity,” says Glenn Wrightsman II, senior software engineer at AIS.
The Terre Haute, Ind., system house had to resolve that while adding its sophisticated systems, which constantly measure the weight, moisture and thickness of sheet goods. They turned to Ethernet, extending it down to the input/output (I/O) of its measurement system. Reliability issues disappeared and AIS realized benefits such as simplified installation. “We use an Opto 22 package that’s very dependable and has a low cost per I/O point,” Wrightsman says. “It’s very easy to use and you can put a rack of I/O anywhere in the plant.” Opto 22 is an automation supplier located in Temecula, Calif.
These simplified installations and improvements in reliability are key reasons that a growing number of system integrators and plant managers are extending Ethernet down to the I/O level. Leveraging the popular network also drives down costs, both during installation and over the lifetime of a system.
The long-term savings come in part from simplified diagnostics that help AIS customers and many others reduce downtime. Ethernet gives users more insight into the health and usage of their equipment, reducing failures and improving productivity. These diagnostic tools, like the network itself, leverage the huge consumer and business base, which drives costs down while bringing benefits such as ease of use.
Searching for simplicity
When companies replace fieldbuses with Ethernet, the payoffs continue well beyond the initial installation. Ethernet comes with a wealth of diagnostic tools that help keep equipment running efficiently. The vast array of troubleshooting tools gives technicians more options than they have with fieldbuses. At the same time, technicians know that upgrades will continue. Everything connected with the network is within the mainstream.
“When you’ve got real-time communications based on Internet protocols or Ethernet protocols, you can use a normal laptop and its tools,” says Stephan Stricker, product manager at B&R Industrial Automation Corp., an Austrian automation supplier with U.S. headquarters in Roswell, Ga. “When you go with something like CANopen, you need an analyzer or a third-party device.”
Many product developers are taking advantage of the processing power and memory space of today’s systems to add monitoring software into their hardware. When machines have this sort of self-checking capability, technicians don’t need any specialized equipment to peer beneath the covers to see how their equipment is performing. “With Ethernet, you can build diagnostics right into the controller,” says Jason Haldeman, automation marketing specialist for vendor Phoenix Contact Inc.’s Automation Systems Group, in Harrisburg, Pa. “Building diagnostics into the device lets you use diagnostic tools like Internet Explorer that let you go to an address and see what’s going on at that point.”
It’s not only the array of monitoring tools that make it simpler to pinpoint problems in Ethernet networks. Many of the human-machine interfaces (HMIs) include software that warns operators when problems arise. “There are a number of Simple Network Management Protocol tools, like SNMP OPC servers that help you bring information into the HMI so operators can act on alerts,” says Carl Henning, deputy director at the Profibus Trade Organization, based in Scottsdale, Ariz. That’s possible because information is in both the controller and the HMI, he explains.
Sending alerts to equipment operators facilitates the quick responses that are necessary on production lines that run at high speeds. “Alarms at the I/O level send messages to a technician or engineer, alerting them of an issue. This facilitates quick decision making and gets the job done faster,” says Karie Daudt, senior product manager with automation component vendor Turck Inc.’s network and interface division, based in Minneapolis.
Updating these alerts constantly makes it more likely that operators will be able to respond in time to prevent many potential problems before they wreak havoc on production. Often, these tools have already been in use in front-office networks. That usually gives software enough field testing to satisfy managers in the harsh industrial environment.
For example, many information technology tools that monitor network traffic levels can be used on the factory floor. When traffic exceeds desirable levels, the system can send alerts. “You can divert traffic or make other adjustments before traffic hits 100 percent and you have problems,” says Brian Oulton, networks business director at supplier Rockwell Automation Inc., in Mayfield Heights, Ohio.
Though an array of diagnostic tools is readily available, some engineers note that these tools aren’t a huge factor in their decision to deploy Ethernet. For example, AIS finds so few problems that staffers rarely use software tools that were downloaded from the Web.
“There are shareware programs that let you view data packets that move over Ethernet. We rarely use them,” Wrightsman says. “Once we’ve verified that the cables are properly installed, we have no other problems.”
Using Ethernet also makes it simpler to simply do away with cables by employing wireless communications. Wi-Fi is already being used in some facilities to connect actuators or sensors that would be difficult to wire. Though wireless remains a small percentage of usage, it’s growing steadily as reliability questions are answered.
Whether managers move to wireless or stick with cables, simplified installation is a central reason that many companies turn to Ethernet. Many integrators and equipment developers note that eliminating gateways saves both time and money. Using a single networking scheme makes it simpler to find installers who are familiar with the nuances of installing an industrial network, helping reduce installation times. “Having a single network can improve set-up and commissioning, as the user is not required to be an expert in multiple network protocols,” says Turck’s Daudt.
One, Not Many
Wrightsman echoes that sentiment, explaining that even very complex systems can be linked together quickly with widely available category 5 cabling. Using Ethernet lets AIS run a single cable instead of worrying about how to connect elements that must be linked using complex cable harnesses. The bandwidth also makes it possible to install equipment anywhere, because Ethernet can carry large amounts of data from a station that’s installed far from its controller. “We have actuators that control the weight and moisture for each slice across the sheet. We put a remote rack out there and control the actuators with this remote I/O. It’s nice to run one cable out there instead of a whole bundle of I/O cables,” he says. Wrightsman also notes that shielding a single cable is also far simpler.
Cabling is not the only change. One of the key architectural differences between Ethernet and conventional industrial networks is that switches come into play. Adding switches improves troubleshooting and gives engineers more freedom in the way that they set up their networks.
“Switches add a diagnostic level to the network that you don’t have with traditional fieldbuses,” says Dave VanGompel, an ODVA Technical Review Board member and principal engineer at Rockwell Automation. “But switches cost more per port and they also need a power source, which adds cost.” (ODVA Inc. was formerly known as the Open DeviceNet Vendors Association.)
However, networking specialists note that plant managers need to look beyond the basic hardware cost. The huge base of Ethernet users brings an array of tools, many of them priced at commodity levels, given the high volumes gained in commercial markets.
“There are a lot of traffic analyzers that let you decode SNMP and other protocols,” VanGompel says. “Technicians who want to go down to the packet level can use a range of tools that were developed for industrial applications.”
Though those tools provide a pathway into the depths of Ethernet communications, they may not be enough for many technicians. In some instances, problems may be in legacy protocols that are still running on older products.
“When everything is linked with Ethernet, one network can run multiple protocols. Modbus TCP, Profinet and others can all run on the same wire,” says Phoenix Contact’s Haldeman. However, observers note that networking problems associated with these legacy protocols are rare.
The range of tools gives technicians and operators the ability to examine all sorts of parameters. But often, operators don’t want any more data than a straightforward go or no signal. These “idiot lights” can be especially effective in point-to-point links. They tell operators whether both ends of the connection are ready to run, or highlight which one has failed.
“One of the things Ethernet brings is point-to-point technology. It’s evolved to a switched infrastructure so everything is connected point-to-point,” VanGompel says. “With point-to-point, simple LEDs (light emitting diodes) on a device can make it easier to troubleshoot.”
Compromised cables?
Product developers have invested a lot of time and research effort into one of the more vexing problems on the plant floor—broken or disconnected cables. Pinpointing the point where wires are broken can be a very time-consuming task. The switches that commonly connect Ethernet network segments are critical elements for this capability. Unlike conventional unswitched field buses, switched Ethernet networks can monitor what’s going on with cables. Data and system monitoring software is typically designed into this hardware.
“One nice things about managed switches is that you have diagnostics in the infrastructure,” says Henning. “The switches keep a lot of statistics, so you know if you’re having a lot of retries or where something on the cable went if it’s disappeared.”
Managed switches provide far more diagnostics than unmanaged switches. Unmanaged switches only provide some LED alerts on the front panel, providing far less information, Henning notes.
Some industrial versions of Ethernet have more capability to recover from cable breaks than others. Joey Stubbs, North American Representative for the EtherCat Technology Group, in Volente, Texas, notes that EtherCat handles telegrams differently than other real-time versions of the standard, providing more support. A link detection notes faults and closes problem ports. Telegrams are then sent back to the controllers.“Each slave device has its own support structure, so frames are returned even if you have a sheared cable,” Stubbs says. “We can get localized diagnostics even when a slave loses power or its onboard processor dies.”
Subscribe to Automation World's RSS Feeds for Feature Articles
Companies in this Article
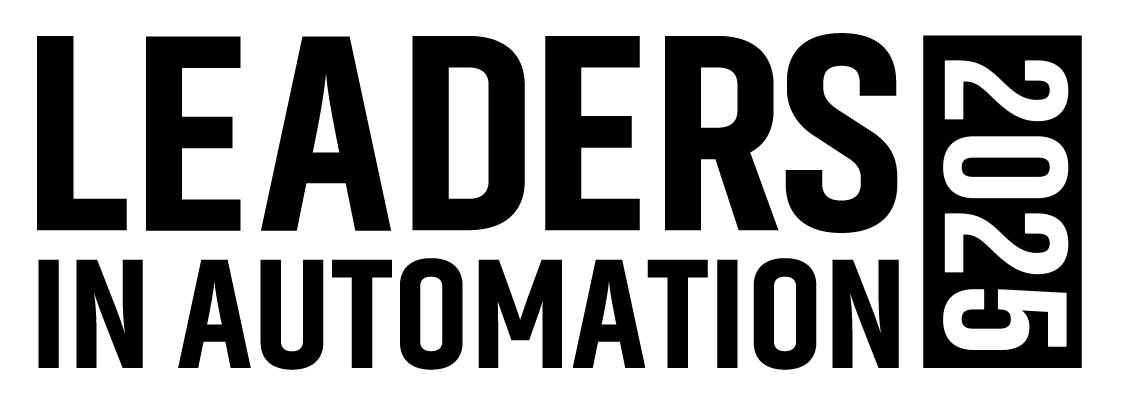
Leaders relevant to this article: