He was married, had a very upbeat personality, a good position at the company, and
was pleasant to be around. One day, Henry was trying to track down a low
voltage problem and was conducting voltage measurements on a 4,160V to 480V dry
type transformer on an upper level mezzanine. He took off the transformer
cover, knelt down in front of it with a meter to test the 480V side and got the
4,160V side by mistake. The resulting arc flash explosion sent a fireball
blasting out of the cabinet catching him in the torso and groin before rolling
up his face.
With his clothes burning, Henry managed to make it down the ladder. Coworkers put
out the fire and rushed him to hospital where he was diagnosed with third
degree burns over a large portion of his body. He lingered in the hospital for
an agonizing seven days and then died.
“From that moment, the way I viewed electrical power changed forever,” says Jim Phillips, who was called in to conduct the forensic investigation the next day.
Today, Jim is one of America’s foremost experts on Arc Flash and teaches
numerous seminars on electrical safety through his company T2G Technical Training Group and has written a book on the subject that will be published in the fall. “If you work in this business long enough, you either know an arc flash victim or you know someone that knows a victim.”
As defined by IEEE and the National Fire Prevention Association (NFPA), an Arc Flash is a strong electric current – and often a full-blown explosion – that passes through air when
insulation between electrified conductors is no longer sufficient to contain the voltage within them. This creates a "short cut" that allows electricity to race from conductor-to-conductor… to the extreme detriment of any worker standing nearby.
Arc Flash resembles a lightning bolt-like charge, emitting extreme heat – up to 35,000 degrees Fahrenheit or four times the surface temperature of the sun. Anyone exposed to
the blast or heat without sufficient personal protective equipment (PPE) would
be severely -- and often fatally -- injured.
Arc Flash incidents cause several types of injury. Like Henry, victims may be
burned. They may also be thrown by the force of the explosion sustaining impact
injuries such as concussions and fractures, and/or deafened by the bang, which
can reach 160 decibels – louder than a jet engine. The extreme heat of the
explosion may also melt and shatter metal wiring and equipment and spray it
across the room as projectiles, causing shrapnel wounds, burns and igniting
clothing.
According to most studies, the most common cause of these accidents is human error.
Henry’s tragic mistake in measuring the wrong side of the cabinet is a case in point. But many other factors may trigger an incident. In some cases just coming too close to a high-current source with a conductive object can cause the electricity to flash over. Other causal factors include equipment failure due to use of substandard parts, improper installation, or even normal wear and tear, breaks or gaps in insulation or dust, corrosion or other impurities on the surface of the conductor.
"It’s practically impossible to completely eliminate arc flash incidents," says Greg Richards, an automation consultant with Siemens Energy & Automation. “The best way to avoid an Arc Flash incident is to avoid working on energized equipment, but that’s not always realistic,” adds Richards. “If you are in a continuous process
environment or a facility like an Air Traffic Control tower then you may just
have to deal with it.”
“However, there are a number of ways you can significantly reduce the risk, starting with understanding how dangerous these incidents can be, performing all the proper
groundwork as outlined by IEEE and NFPA regulations (see NFPA 70E “Standard for
Electrical Safety in the Workplace” and IEEE 1584 "IEEE Guide for Performing Arc Flash Calculations") and making sure that when you do work on live equipment you have the appropriate PPE on at all times.”
Richards has his own Arc Flash horror story. Prior to joining Siemens he worked in a plant where a worker got seriously hurt checking the voltage on a circuit to make sure it had enough power to drive another piece of equipment. “He had second and third
degree burns from the waist up. He was in the hospital for nearly a year and
needed multiple skin grafts.”
This incident led to the creation of an Arc Flash task force for the company’s five North American plants. “We started with making sure we had the right PPE, but then we went
looking for ways to eliminate Arc Flashes altogether.”
Eventually Richards realized that reducing the need to open the cabinet in the first place was one of the best ways to accomplish that goal. "People open the cabinet for many reasons, but chief amongst them is that, typically, they don’t know what’s
going on inside," he says. "They know there’s a problem; they are getting an
alarm or a circuit has tripped or something. But they don’t know exactly what.
What if we can get that information without opening the cabinet?"
By integrating all the relevant equipment, such as the motors, drives and switchgear, with the communications network in what Siemens calls a Totally Integrated Automation
(TIA) architecture, operators are able to monitor and pull diagnostic information, perform trend and root cause analysis and generally better see what the problems are before sending an electrician into the plant to deal with a problem. Over time Richards found that workers were going into the electrical cabinet less and less often.
“As we used it more, the guys learned to trust the information they were getting,” Richards said. “If a breaker tripped, they knew it. But, before the TIA system, there was nothing to do but reset the breaker. The TIA diagnostics allowed engineers to go back and
trend the data—to perform and process the diagnostics externally. For example, if I wanted to know what the drive current was, I could just look that up. As a result, we found that, over time, people were going into the cabinet less and less.”
Phillips agrees that the TIA approach is solid. “If there are ways to monitor and control things that keep people from opening the cabinet then that’s a much better way. The best option is always to avoid the hazard. Doing this through automation and control
is a great approach.”
Many free articles and downloads - www.brainfiller.com
A global community about arc flash and electrical safety - www.ArcFlashForum.com
Siemens Arc Flash brochure
Siemens Arc Flash studies
Video of Arc Flash accident
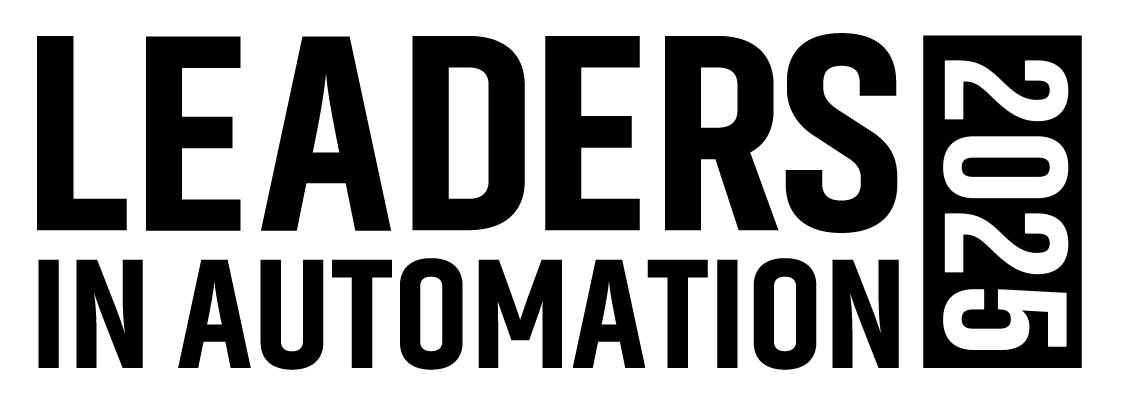
Leaders relevant to this article: