At the dawn of this century, vision-guided robots were a rarity in packaging operations. Small wonder—each of the component technologies had their own degree of complexity and cost, and getting them to work together presented an additional level of difficulty and expense. Despite the benefits in terms of speed, flexibility and precision that vision-guided robotic applications offered, relatively few end-users felt they could be justified, so while the number of applications grew from year to year, that growth was modest.
Times change. The trickle of vision-guided robot applications that characterized the packaging industry earlier in this decade has now become a strong and rising stream. Whether as traditional stand-alone robots, purpose-built robotic work cells engineered for specific tasks or as robotic packaging machines, robots have now become a common sight on packaging lines, and increasingly, those robotic systems have a vision component.
“In 1988 at the Pack Expo show, there was one robot,” recalls John Dulchinos, president and chief executive officer of Adept Technology Inc., Pleasanton, Calif. “It was a vision-guided Adept robot and it was handling chocolate. At the last PackExpo, there were well over 50 robots, a great many of them with vision. It underscores the fact that the market has come a long way, and I think we’ve still only scratched the surface.”
So the obvious question is, why the change? For starters, there are the robots themselves. “Our ongoing goal has been higher speed, lower cost and greater performance,” says Laxmi Musunur. As manager, picking/packing/palletizing, for Fanuc Robotics America Inc., Rochester Hills, Mich., Musunur speaks for Fanuc, but it is a sentiment with which the rest of the robot industry would concur. It’s also a goal that has, with very few exceptions, been met. Faster, cheaper, better…which means that many applications that couldn’t be justified 10 or even five years ago can be justified today. Add Delta robots to the mix, and the number of cost-justifiable applications expands even further.
Delta-style robots employ a base that contains the actuators and which is mounted above the workspace. Three arms, typically made of lightweight composite material, extend from the base and provide movement in the X, Y and Z axes. Because the arms are so light, they can move faster than what by now could be called traditional robots. While no threat to the large and heavy robot arms that move and weld auto parts, they have proven remarkably successful in handling consumer packaged goods. Use of this design had been constrained by patents and by licensing agreements, but the agreements have expired, and now a number of companies sell Delta-style robotic systems to the packaging industry. Notable offerings come from ABB Robotics, Auburn Hills, Mich., one of the original license holders for the technology, as well as Adept (which offers a four-armed version), Fanuc and Fallas Automation, Waco, Texas, to name but a few.
Delta explosion
“The Delta technology has taken the market by storm recently because original equipment manufacturers (OEMs) can much more effectively embed these small arms into their packaging processes compared to bulky automotive robots,” says John Kowal, global marketing manager for Elau Packaging Solutions, Schneider Electric, Schaumburg, Ill. He notes that the vogue for Delta robots occurred first in Europe, where builders have increasingly been incorporating these lightweight arms into purpose-built systems and robotic picking and case packing machines. “North American packaging OEMs have rapidly embraced the technology, especially for case packing. This growth is displacing traditional six-axis articulated robots adapted from automotive and material handling applications, as well as conventional case packers.”
Vision systems, too, have undergone their own rapid evolution toward more cost-effective, easier-to-deploy formats. In the 1980s and ’90s, lighting for a vision system was as much a work of art as it was engineering. Today, increases in computing power have allowed vision system providers to employ software algorithms that are better able to handle the variations in lighting that can occur in plants. Increased standardization of vision system components has also helped to rein in engineering and installation costs, and the proliferation of low-cost vision sensors capable of handling many basic vision tasks has further lowered cost and complexity, making many more applications justifiable.
“We are seeing a trend toward smaller cameras designed to do a specific task,” says James Anderson, machine vision product manager, Sick Inc., Minneapolis. “This is a concept that camera manufacturers have been trying for years, calling them ‘vision sensors.’ This term used to mean simple, but low performance. This concept is changing quickly as these sensors become more sophisticated in their tools and communication capability.”
One of the chief enablers of this expanded communication capability is Ethernet, according to Anderson. “Ethernet is becoming more common on these sensors, and the amount of data they can share is increasing quickly.” This additional data is making applications possible that would typically have required a complete vision system in the past, Anderson says.
It would also have required considerable time for a person to program that application into the vision system, he adds. Newer vision sensors, with their increased processing power and communications capabilities, obviate that need. “The adoption of the technology seems to be growing very quickly. Areas like palletizing and de-palletizing seem to be leading the way, highlighted by the use of 3D data to optimize the pick pattern.”
These increasingly powerful, yet affordable, vision devices are also helping packagers to comply with growing regulatory and commercial demands for greater traceability. “The integration of vision technology into robotic-enabled packaging lines has traditionally only been viewed from the perspective of product location and orientation,” observes Ed Housler, business manager, factory sensors, for vendor Siemens Energy & Automation Inc., Alpharetta, Ga. “Today, and in the future, vision-based track-and-trace solutions are being implemented in packaging lines to provide real-time visibility of the process.”
As an example, Housler cites the growing popularity of Data Matrix Code (DMC), a two-dimensional barcoding technology that allows for a greater amount of data to be encoded than is possible with one-dimensional barcodes and also permits a high level of data redundancy. “DMCs are read, and decoded, on the packaging line using vision-based hardware platforms that can be easily integrated into the overall system architecture.”
Synergy
These converging streams of robot and vision improvements coupled with advances in computing and software were much in evidence at last November’s Pack Expo show in Chicago, and perhaps nowhere more so than at the Rovema booth, where the new ELR-100 robotic case packer was on display. Employing a Delta-style robot, the new high-speed case packer incorporates product and case conveyors and a Cognex vision system, all controlled by a Rockwell ControlLogix programmable automation controller (PAC).
The point here is not that this particular case packer is an innovative product; it is, but it’s also an illustrative product, shedding light on the new generation of robot and vision-enabled packaging equipment. Jeff Sandrock, controls engineer for Rovema Packaging Machines, Lawrenceville, Ga., stresses the importance of control technology for this new generation.
Related Article: "Vision-assisted Robotics Ensure Fast, Accurate Tube Filling"
“Of prime importance is the ease of integration between the camera and the programming software, which is a function of the Rockwell PAC and its integrated software and control environment,” says Sandrock.
Tim Warren, Rovema product manager, makes the point that the Rockwell PAC helps reduce the case packer’s overall cost of operation. “The people that are building with the proprietary, black-box type controllers also have to have a PLC on top of that for safety and conveyors and that type of thing. With the ELR-100, all of that is done within the PAC.”
The black box that Warren speaks of is an image that comes up frequently when automation professionals discuss the future of robotics in packaging. “The days of black boxes talking to black boxes are over,” says Mike Wagner, OEM packaging global business manager for Rockwell Automation Inc., Milwaukee. “Kinematic solutions in a multi-axis environment have always been the domain of the special processor, the dedicated control system. But today, with a standard PAC controller, you have the ability to handle the most complex math functions and multiple axes all in a single architecture and on a single network connection without having to create a complex communication strategy between controllers.” This not only impacts system performance, but also speeds and simplifies development and installation, reducing associated costs.
But projects have to be sold before they can be implemented, and Warren notes that today’s vision-assisted robotic automation, with its emphasis on simplification and standardization, has some advantages there as well. “Our customers appreciate this standardization because it lowers their training and spare parts inventory costs and provides dependable support. There’s a certain comfort factor in that, which makes it easier for people to consider new approaches.”
And there’s also a certain discomfort, and cost, associated with the older approach to vision-assisted robotic automation. John Cochrane, business development manager, Electric Drives & Controls Division for the packaging industry for vendor Bosch Rexroth Corp., Hoffman Estates, Ill, points out one of these areas when he notes that, “In the past, you've seen a lot of manufacturers shy away from robots because they didn’t want to have to support a separate controller and its native language. In many cases, it required someone in the plant who was dedicated to programming the robot. Then you typically needed another person who was responsible for programming the PLCs. Then there was another specialist who was responsible for programming motion control, so you might need three engineers to support robotic automation.”
The ability to integrate different control functions and tasks into a multidiscipline controller such as today’s PAC, employing the common programming languages of the International Electrotechnical Commission’s IEC 61131 standard, makes these considerations look suddenly archaic. The growing support by automation providers for the International Society of Automation’s ISA88 standard, laying out a flexible state model for machine operation and communication, reinforces this picture.
Then Warren switches to a topic that at first glance might seem out of place in a discussion of packaging technology, namely, the recession. Because of it, he notes, “packagers are looking to reduce head count. Case packing manually is labor intensive. It’s typically not done by one person but by a group of people, so robotic case packing makes economic sense. In addition, when products change, traditional case packers sometimes need to be scrapped, whereas with a robot, it’s generally a matter of a simple change of programming and a change of end-of-arm tooling.”
Rockwell’s Wagner believes that companies facing today’s economic downturn will now need to show a better return on investment in order to justify expenditures on new equipment. “Formerly, incremental improvements were acceptable. Today, with capital being scarce, what we’re seeing is people going for higher rates of return on investments. With the flexibility and productivity of the robot, it’s not too hard to build a fairly significant business case for change, as opposed to, say, just buying a machine that takes you from 180 to 200 products per minute.”
Predicting the depth, or effects, of the current recession is risky business, but food and basic consumer packaged goods—the sorts of things that keep most packaging lines humming—are among the last items that even cash-strapped consumers will cut back on. With that in mind, it is logical to conclude that the future of vision-assisted robotic packaging may be nearly as bright as automation vendors claim.
Companies in this Article
Sponsored Recommendations
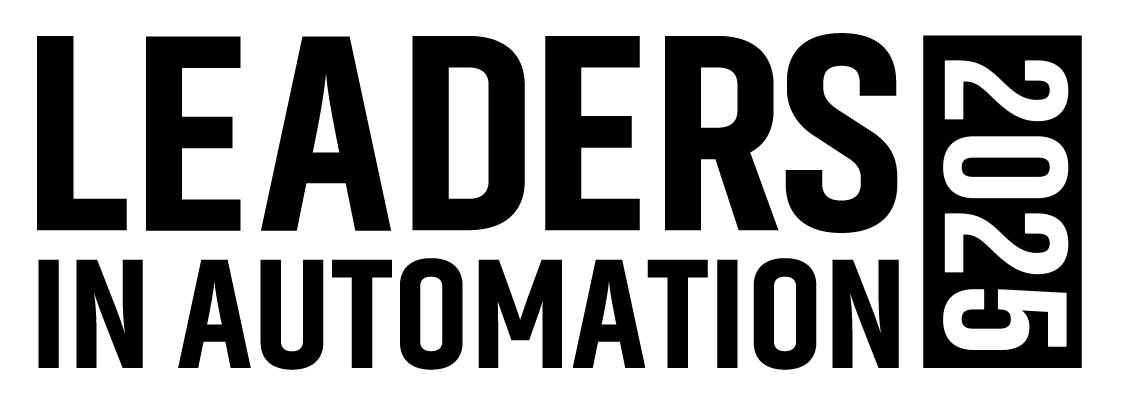
Leaders relevant to this article: