The many networking schemes that once connected equipment on the factory floor are being replaced by a single well-known technology. Ethernet is rapidly becoming the standard for industrial networking, simplifying communication throughout an entire facility while easing installation and maintenance. Today, there are few reasons not to extend Ethernet to the factory floor. Ruggedized equipment ranging from connectors and cables up to networking infrastructure equipment like switches can stand up to the harshest environments. Real time capability has been added for applications that require high-speed determinism. Plus, a multitude of engineers and technicians are already familiar with the basics of Ethernet, so installation, diagnostics and upkeep are comparatively easy for the plant network as well. Ethernet works because it can now reach down to the machine level. Ethernet was first used on the factory floor as a backbone for linking various industrial networks together. Typically, it was only used to connect a manufacturing process to the business environment to gather quality data and manage recipes. But that has changed dramatically in recent years. Ethernet now reaches down to the machine level, where it handles I/O and other jobs that only use to be possible with a range of deterministic field bus protocols. Ethernet is also displacing field buses at the system level, linking automation equipment together in a single homogenous network, even when the equipment is from a variety of vendors. Instead of spending unnecessary hours figuring out how two pieces of equipment can coexist on one network, Ethernet makes it simple to plug them into a common switch. These benefits come without impacting the existing links between manufacturing processes and the Manufacturing Execution System (MES) tools used to manage the complete plant. As a result, it is possible to have one network infrastructure from the I/O level all the way to the MES.Why use Ethernet?There are many reasons to choose Ethernet throughout the networking hierarchy. One of the key driving factors in many organizations is the desire to create compatible networks throughout the entire facility. Automating operations is a critical factor for success in lean manufacturing environments. Linking the management systems that bring in orders to the manufacturing equipment that fulfills those orders makes it simpler to streamline operations. Instead of passing and translating information from one level to the next over several different types of networks and field buses, Ethernet makes it possible for the management system to send information directly to individual pieces of the manufacturing equipment over a single network. This is possible because Ethernet supports multiple protocols such as TCP/IP, HTTP, SNMP, OPC and real time I/O at the same time on the same wire, which is far more efficient than dedicating a field bus for each protocol. Ethernet opens communication possibilities. Using a single networking scheme also pays off when problems on the plant floor are diagnosed. For instance, it was traditionally difficult to notify the maintenance staff if a wire broke on an I/O device’s sensor. First, the automation controller would have to recognize that there was an issue on one of its I/O devices on the dedicated field bus. Then it would send an alarm to an HMI over another network to notify the machine operator. Next, the machine operator had to alert the maintenance staff. They would then have to plug their programming device directly into the automation controller and its field bus to investigate the problem. Here’s how Ethernet can simplify your life.Using an Ethernet network greatly simplifies this broken wire situation. When the I/O device recognizes a wire break, the information can be pushed directly onto the Ethernet network by the device itself. The diagnostic then can be read in multiple locations by a variety of devices. For example, the HMI can let the machine operator know that there is a broken wire, the MES can read the message and record the issue into its quality database, and the maintenance staff can be informed via an SMS message sent directly over the plant’s Voice over IP system that it uses on the same Ethernet infrastructure. The maintenance staff can even collect further diagnostics directly from the I/O device regardless of where the programmer is located in the plant. This sort of Ethernet connectivity extends plant network visibility, bringing many new possibilities for delivering real time information and keeping equipment running at peak performance. Ethernet can lower your costs.Cost is another benefit of Ethernet because compatible network throughout the enterprise helps keep expenses down. First, it eliminates the need for field bus gateways, devices or software that perform media translation. Beyond the obvious hardware cost of these gateways, there is also a cost for installation, commissioning, and maintenance. Additionally, supporting multiple networks in a plant means that the engineering and maintenance staff must be trained on multiple networks and a number of specialists are needed to support each type of network. This means additional expenses. With Ethernet throughout the plant, these costs are greatly reduced and in the case of additional gateways, completely eliminated.Ethernet opens up a whole new toolbox for you.Once a plant decides to standardize on Ethernet, a whole new world of technologies are available. New innovations in the Ethernet community provide constant improvements in automation technology. These advances save time and money during design, engineering, and commissioning. Many of these new technologies have been enabled by the addition of real-time protocols to Ethernet. Because protocols such as TCP/IP and OPC by themselves do not support real-time capabilities, there has been considerable innovation that has provided automation-based protocols for Ethernet. Several protocols from different field bus organizations now provide real-time, automation-based solutions. These field bus organizations have transformed their real time device level network strategies of the past into protocols that runs on today’s Ethernet networks. As a result, it is possible to do much more on Ethernet today than in the past. Give your devices the new party line.Adopting the versatile Ethernet network makes it possible to streamline communications by letting devices talk directly to each other. These devices can be as simple as an I/O module or as complex as a complete automation cell. Device-to-device communications are becoming increasingly common as engineers figure out how to use data without taking time for humans to review it. With Ethernet, it is much simpler to communicate because Ethernet enables more comprehensive protocols. In the past, adding a camera to an automation controller was a difficult task because of the type of data that a camera transmits. With Ethernet based protocols, data easily passes between the camera and the controller. Ethernet setup is easy. Really!Equally important, it is simpler to set up the communications between these devices. With existing field buses, systems must be hardwired to communicate, or programmers must figure out the various commands for each device, writing complex programs to tie them together. Using Ethernet opens the door to device-to-device communication protocols, which let users link pieces of equipment with graphical engineering tools by simply drawing communication lines. Devices such as independent machines can be identified on the user’s screen as component icons that identify the information points going in and out of the machine. Users do not have to know the application program or even how to program at all. They can simply link the machines by drawing lines between these components. That makes it very easy to tie them together and to alter these machine-to-machine communications as needs change.Ethernet lets you unplug and go wireless.The benefits of Ethernet’s seamless networking environment extend to wireless communications as well. For many companies, one of the biggest potential benefits of Ethernet is the ease of adding wireless communications. This was not possible with past field network protocols. Wireless can be a real advantage for industrial applications. Equipment can be moved without worrying about wiring. A distributed I/O connected to field devices such as sensors and motors can be installed in hard-to-reach spots. Temporary monitoring stations can be installed without the cost or danger of stringing wires around equipment. Expanding into wireless technology for automation is easily accomplished by implementing the Wi-Fi technology that is an extension of the wide-ranging 802.x Ethernet specifications and the automation protocols designed for them. A number of companies have been using Wi-Fi in harsh factory environments for years.Wi-Fi simplifies the transition to wireless, maintaining all the commands and protocols of conventional wired Ethernet networks. Employing Wi-Fi extends the compatibility that comes with using Ethernet throughout the enterprises, bringing ease of maintenance along with compatibility. This trend to wireless communications is expanding rapidly because it brings a high level of freedom. Operators who have to move equipment used to have to deal with wiring trays that were difficult to set up and manage. Wireless links eliminate that complexity. Similarly, engineers can add sensors to monitor equipment in a matter of minutes.Imagine the possibilities if you didn’t need to hard wire.Eliminating wires also facilitates the use of autonomous vehicles that can deliver materials or components. Traditionally, these automatic guided vehicles (AGVs) communicated back to a central controller over a hardwired network using slip-ring technology. This technology, because of its mechanical nature, had many possibilities for failures, so maintenance costs were frequently very high. When these robotic vehicles can communicate over a wireless network, they can move freely and alter their routes to maximize efficiency since they are not physically tethered to a network cable.Gimme bandwidth! Dedicated circuits and expansion headaches are history.Ethernet also has the bandwidth to support protocols for safety signals and communications. Eliminating dedicated safety circuits and wiring provides a significant benefit in plants where expansion and equipment upgrades are common. When safety signals are sent over Ethernet, safety circuits can be handled in ladder logic that runs on automation controllers. Safety equipment such as a light curtain is typically linked to a failsafe input card that sends alerts to automation controllers over Ethernet.Using Ethernet to carry these safety signals also makes it simpler to keep a plant up and running. Conventional safety relays shut down power to broad areas, regardless of the type of problem. With Ethernet connectivity to all equipment, it is a straightforward process to program systems to only shut down the equipment that is related to the safety alert. The system can analyze the reason for a safety alert, and then determine whether all equipment in the area of the alert should be shut down or whether sections of the system can continue running without danger. Since Ethernet and Wi-Fi are tightly integrated, these benefits extend to all equipment linked to the safety system even with a wireless connection.Toss out the limitations of field bus technology.Using Ethernet allows for many more possibilities in the types and number of devices that can be communicated across a network. Traditionally, distributed devices at the controller level were limited by the field bus technology. These field buses were limited and dedicated, so only a set number of devices could be connected to the network. The amount of data sent back to the controller was limited to relatively small packet sizes. This was fine for normal I/O and drives, but became challenging for peer communications or very large installations. Be flexible and sophisticated while you’re lowering costs.With Ethernet, another level of freedom comes from the ease of communicating with sophisticated devices like motion controllers and automated vision systems. Ethernet has the bandwidth to support them, and its I/O structure makes it simple to add, upgrade or move these devices as needed. Ethernet can support several thousand addresses, making it possible to add large numbers of devices. Removing the restrictions posed by traditional field buses makes it easier to design a complete machine communication infrastructure. Bandwidth expansions will increase to give you more capabilities.This bandwidth will continue to increase further in the future. Industrial versions of Ethernet now use the standard 1 Gbit/second, with the promise of 10 Gbits/second coming as this version expands into the mainstream of the commercial world. The IEEE standards body is already working on a 100 Gbits/second version, offering a road map that simply does not exist for many existing field buses, which are limited to existing speeds. Enter the web server…. now you’re global fast!Another interesting technology that is made possible by Ethernet is the use of Web servers for displaying data about a device or machine system. Embedding a Web server inside a device on an Ethernet network makes it possible to link into it with a standard Web browser from a remote location to display current status or diagnostic information. Since the Web server is part of the device itself, no programming is needed to display a wealth of information.Yes, the factory is not your home.Though installing Ethernet in a manufacturing environment is fairly straightforward, adopters must realize that there are differences over the plug and play aspects of home networks. First is the physical network itself. Ruggedization and shielding must be added in industrial applications. Often, network wires must be heavy duty, shielded cables to block out noise interference produced by the equipment inside the plant. Additionally, industrial switches exist which are designed for the automation environment. These switches perform the same function as a non-industrial rated switch, but are designed to run in industrial applications where the environments are harsher than in the typical back office. While these switches can coexist with the IT network, they are configured in the automation engineering environment and are able to be diagnosed by the automation controller and HMI. One of the keys for many industrial operations is the need for determinism. In factories, messages that start or stop operations have to arrive on time. Delays of just a few milliseconds can destroy entire production runs or injure workers. This is an aspect of the industrial environment that does not exist in offices where there is rarely an impact if an e-mail arrives a few seconds late. Gain the benefit of real-time communications.Over the past few years, many different Ethernet protocols have emerged to address the factory’s need for precise timing. These protocols provide determinism without impacting compatibility with existing data transfer. This means that real-time communications can connect a controller and a servo drive on the same Ethernet network that sends database records to the MES. The real-time protocol guarantees that the drive data is delivered from the controller on time with higher priority than transferring the record to the database. Since this is a property of the protocol itself, the user does not have to worry about special programming for deterministic data. Gaining all these benefits does not require a lot of effort. Ethernet is well proven in the industrial field. The ARC Advisory Group pegged the market at 1 million nodes in 2007, forecasting an increase to over 3 million nodes by 2012. The size of the market underscores the availability of components, systems and installation expertise.Adding all these factors together has led many management teams to the same conclusion: Ethernet offers a low cost, high bandwidth, standard network infrastructure that greatly simplifies connectivity, ease of installation, and maintenance while still meeting the performance needs of the automation environment. Integrating this network infrastructure into factory floor automation offers solutions that can greatly increase productivity in ways that were not possible before.Written by Eric Kaczor, Product Marketing Manager, Siemens Energy & Automation, Inc.
Sponsored Recommendations
Sponsored Recommendations
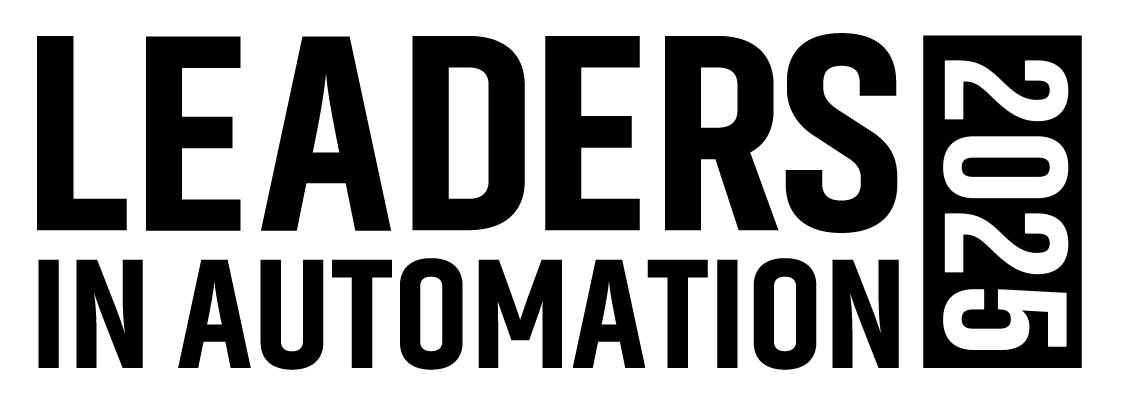
Leaders relevant to this article: