Connectivity is like motherhood: Everybody praises it in the abstract; it’s the concrete examples that can spark disagreements. One thing that there is little disagreement about, though, is the central role of Ethernet.
“Ethernet is the foundation for establishing heightened communications,” says Robert Muehlfellner, director automation technology, at vendor B&R Industrial Automation Corp., Roswell, Ga.
Mike Hannah, business manager for NetLinx at Milwaukee-based supplier Rockwell Automation Inc., concurs, seeing the technology as a natural fit for the packaging industry. “It’s the network that best fits packaging,” he maintains.
Why? “It satisfies not only the end-user requirements but the original equipment manufacturer (OEM) requirements as well. The packaging OEMs have been using networks for many years—they have a motion network, they have a drive network, they’ve had to use some safety networks, and because of that, they’ve had to work with different media, different protocols, and they all require different programming and configuration tools, even multiple communication cards in the programmable logic controller (PLC). By going with Ethernet, you collapse all that into one network, and that simplifies their machine design.”
From an end-user perspective, says Hannah, Ethernet helps users more easily integrate equipment into their facilities and “helps them to realize the full efficiency potential of their machines.”
Rick Rey, business development, electric drives & controls, for Bosch Rexroth Corp., a Hoffman Estates, Ill,, vendor, summarizes the benefits of that efficiency. The prime advantage, he says, is “being able to connect your primary with your secondary and tertiary packaging machinery so that when a new product, or a different size or package for the same product, is coming through, the necessary axis movement changes and other modifications are all made seamlessly. This helps you operate with maximum efficiency.”
Of course, there are different approaches to Ethernet, as Jeremy Bryant, networking business manager for Siemens Energy & Automation Inc., another major automation vendor in Alpharetta, Ga., makes clear. “As far as the connectivity goes, Ethernet is really the key. When you start looking at your control network, though, it needs to be able to handle all the possibilities of your application while still allowing the openness of Ethernet. Some networking options may be Ethernet-based, but if all they allow on that cable is the protocol for that particular application, be it motion or whatever, then you’re losing the whole point of Ethernet.”
That’s why, he says, Siemens opts for Profinet, the Ethernet protocol controlled by the organization that oversees the Profibus standard. Importantly, Profinet permits a degree of determinism, facilitating real-time operation.
Safety first
Safety, in the face of disruptive network issues and the sorts of intrusions that bedevil personal computers, is another point of divergence. Proponents of Profinet such as Bryant point to various safety features built into the protocol. Sometimes, though, vendors seem to shrug off network safety concerns, saying that information technology (IT) departments are quite capable of handling any issues that arise—after all, that’s their job. To a skeptic, this approach may seem uncomfortably similar to assurances that the big banks won’t make risky investments; after all, managing money wisely is their job.
B&R’s Muehlfellner is a skeptic. “I’m not a believer in having everything on a single Ethernet network,” he says. “I’m talking about a situation where you have your corporate systems, your PLCs or your PACs (programmable automation controllers), your drives and your I/O (input/output) all on the same Ethernet network. Technology now makes that possible, but I don’t think it’s the direction to go, first, because it requires tremendous configuration effort, and secondly, because I believe it’s a somewhat volatile solution. There should rightfully be some concern from end-users about having everything on a single network.”
Instead, Muehlfellner favors having corporate computers on some form of standard Ethernet, with plant floor equipment linked via a real-time network. For this, Muehlfellner and B&R favor Ethernet PowerLink, which adds time slicing and polling features to standard Ethernet in an effort to make it more suitable for plant floor operations.
“Ethernet PowerLink allows for very precise, deterministic data exchange between a PLC and I/O and other intelligent devices,” he maintains. With the controller acting as a gateway, plant and enterprise, in Muehlfellner’s estimation, can then conduct all necessary interchanges in relative safety, aided by communications technology such as OPC, an open connectivity standard.
The diagnostic advantage
Ironically, Muehlfellner feels that unnecessary security concerns may be hampering one of connectivity’s key benefits: remote diagnostics. “Increased machine-to-machine communication helps in many ways, but one of the areas I see as being most productive is in predictive vs. preventive maintenance.” For instance, he says, you can get a readout on the actual current drawn by a motor, and if you average this over a machine cycle, you can now monitor trends. If it’s higher than it should be, you can send maintenance out to correct the problem before it shuts down the line.
“In addition,” says Muehlfellner, “with preventive maintenance, you get more efficient operation, because you are catching decreases in performance sooner. Couple this with reduced maintenance costs and you are decreasing the total life cycle cost of the machine.” Also, remote diagnostics can allow an OEM to address a problem without the time and expense of flying a service technician out to the end-user’s plant. “But today, we see a lot of reluctance on the part of end-users to allow remote access, despite the fact that there are means to ensure its safety.” Network security wasn’t studied when most of today’s control engineers were in school. Younger engineers, he says, are more familiar with the issue, so remote diagnostics should become more prevalent in the future.
Of course, Ethernet isn’t a magic bullet; it is an enabler rather than an actor, a point succinctly made by Siemens’ Bryant. “The two big challenges, I think, are connectivity and communications—not just being connected, but having the machines talking to each other.” Companies are finding ways to benefit from greater plant floor communication, while, in many cases, feeling their way toward greater exploitation of the connectivity potential of Ethernet. Case in point: Hartness International Inc., a maker of packaging equipment and conveyors for bottling and material handling based in Greenville, S.C.
Rapid change
According to Robert Beesley, engineering manager at Hartness, “Perhaps no industry is experiencing change as fast as packaging.” Packaging, he notes, is being redesigned more frequently to attract consumer attention, and in a growing number of cases, to make the packages more ecologically friendly. Packagers want their equipment “to perform with greater reliability, be easy to monitor and to diagnose line performance, and to quickly change to accommodate different products and packaging requirements. They also want to use fewer operators on their packaging lines.”
Hartness’ latest attempt to address these needs is GlobalShrink, a family of film-only multipackers and tray former shrink wrappers. “The GlobalShrink platform demonstrates how we design packaging machines to achieve the extreme flexibility that customers demand,” maintains Beesley. Able to pack bottles on four-wall trays, on wall-less pads or with two-wall U-boards, or with film only—either printed or plain—the machines can be built to perform at 60, 80 or 100 cycles a minute. An 80-cycle machine running two lanes of bottles, for example, can pack 160 six-bottle packages every minute.
Importantly, changeovers are handled through a machine’s human-machine interface (HMI) system, speeding the process and saving labor costs. Thus, says Beesley, “We make it easier for customers to handle different products and package sizes on the same production line.”
In the future, Hartness plans to move to distributed control systems with Ethernet-based I/O to further reduce wiring and assembly time. “In a centralized control system, every sensor and actuator has to be wired back to the control panel. By distributing control, machine functions can be governed by the drives, I/O blocks are located on the machine, and wiring is reduced to a 24-volt power cable and an Ethernet cable, which eliminates hours and hours of work and wires.”
Beesely adds, “Since a typical packaging line is 80 feet long, a finished machine must be divided into separate sections for shipping. A distributed control system simplifies reassembly and reduces wiring errors in the field.”
Growth of a standard
A key aspect of communication today is OPC. This open connectivity standard allows devices and software from disparate vendors to communicate with each other, as well as with higher level systems such as manufacturing execution systems (MES) and enterprise resource planning (ERP). While not suitable for the transmission of critical deterministic data (it is more effective communicating between HMIs than between devices), the fact that it has become nearly ubiquitous boosts its usefulness and helps keep users from being locked into a single vendor.
Not everyone, though, is ready to sing OPC’s praises. It has its shortcomings, and these can be gleaned from its name. When it was launched a decade ago, OPC stood for OLE for Process Control, OLE being Microsoft’s object linking and enabling scheme. OLE has passed out of use, but the Microsoft connection still haunts OPC. Some users complain that there are too many transmission failures. Defenders of OPC blame the peculiarities of Microsoft’s authentication requirements for many of these failures. One solution is tunneling, or creating software tunnels through firewalls in order to bypass Microsoft authentication.
Some choose to bypass OPC for specific applications. One example is Acsis Inc., a Marlton, N.J., company that develops product-tracking software. It employs communications libraries from CimQuest InGear, Phoenixville, Pa., to forge connections with Allen-Bradley PLCs from Rockwell Automation.
“The InGear library has allowed us to talk to PLCs directly rather than having to use OPC,” says Ross Levin, director of product development for Acsis. The result, he says, has been “a real-time performance advantage.”
Transitions Optical Inc., Pinellas Park, Fla., a leading lens manufacturer, is another company that chose to bypass OPC. Along with performance advantages that the company believed it could gain through InGear, it was also influenced by the fact that it has many customized systems deployed over five plants.
“OPC is an open source standard, while our company is privately held and uses no open source, so if we used OPC, we would have to change the methodology that we use to interact with our machines on a global basis,” says Patrick LaFerriere, project leader at Transitions Optical.
“When we first get the lenses as raw substrate, we use a laser to put a tiny matrix on the back. That matrix contains the crucial information that will be required as the lens is processed. We use the InGear communication tools to interface with our PLCs, the laser and the production machines.
“When the lens gets to packaging,” he continues, “we use a vision system to read the data matrix and determine what box and what label to use, as well as any special instructions.” LaFerriere notes that the same communication tools interface with customized HMIs that scan every 100 milliseconds to gather data on machine status. The HMIs, in turn, are interfaced with the plant’s MES.
The OPC Foundation, Scottsdale, Ariz., has responded to problems such as these by kicking things up a notch through the launch of OPC Unified Architecture, or UA.
Unlike its predecessor, OPC UA is not bound to proprietary Microsoft technology. It employs Web Services as well as Microsoft .Net in preference to the fast-fading Microsoft common object model (COM) and distributed COM (DCOM). It is capable of handling more complex data and expands the range of OPC, reaching farther down into the control level and farther up into the enterprise systems level. Importantly, its “wrapper” software allows it to work with existing OPC interfaces.
Referring to OPC and other standards, B&R’s Muehlfellner notes, “The needed standards exist. Now it’s up to people to implement those standards. As that implementation progresses, I think it is going to be beneficial for the packaging industry as a whole.”
Sidebar - Profiting from Speed and Control
To read the accompanying sidebar to this article, go to www.automationworld.com/feature-4913
Companies in this Article
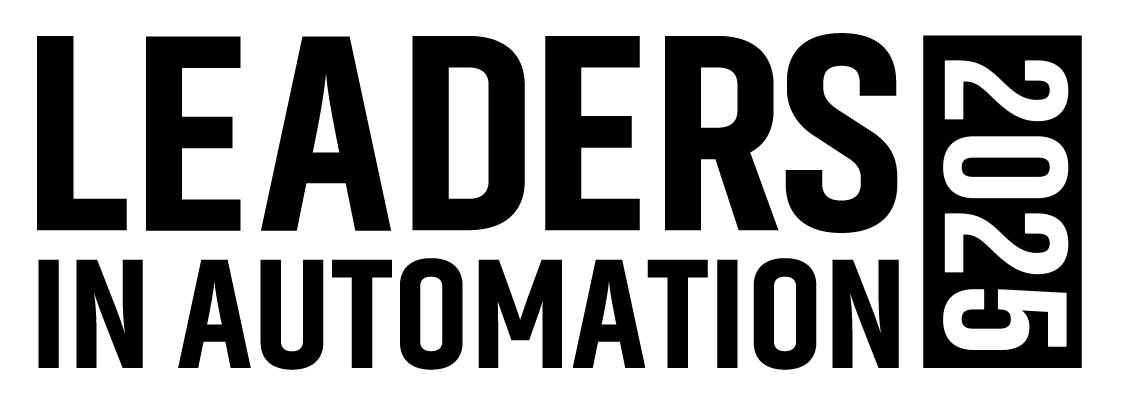
Leaders relevant to this article: