The full color printing presses that print the high precision photos and text to create hundreds of thousands of magazines and newspapers in short timeframes are extremely complex devices. For the printer that produces some of Italy’s leading publications, a key aspect of keeping them running efficiently was to build a network to manage all the sensors, actuators and controllers of its huge presses.
Officine Meccaniche Cerutti (Cerutti’s Mechanical Workshops) handles prominent Italian weekly magazines “L’Espresso” and “Panorama,” a version of “National Geographic,” and Italian daily newspapers “La Repubblica” and “Famiglia Cristiana.”
The local area network at Cerutti’s facility in Casale Monferrato has nearly 500 nodes and 13,000 input/output (I/O) points. That requires a complex scheme that includes a set of sub-networks. The flexographic machines used to print daily papers require a combination of very different devices featuring heterogeneous communication protocols. A single machine can incorporate no fewer than seven types of networks.
Writing software and making sure these networks communicate efficiently is an ongoing challenge. “Cerutti is doing an important job concerning the product engineering of software applications and the optimization of data exchanges among devices and interconnected systems,” says Paolo Di Santo, director of packaging machine software at Cerutti.
While Ethernet is increasingly being used for all of these networks, many systems rely on time-tested fieldbuses to handle I/O, sensors and some real-time tasks. Though they’re often viewed as fading technologies, these fieldbuses remain viable in many applications, operating as sub-networks that usually feed into Ethernet backbones.
Beyond their obvious value in legacy applications, the array of fieldbuses offers low costs, simple installation and versatility. Another benefit of mature fieldbuses is that compatible components of all types are readily available. For example, some companies that build complex machining equipment aren’t even thinking about a move to Ethernet for many facets of their designs.
“At this point, many of the products we communicate with do not support EtherNet/IP. DeviceNet remains our choice for these systems,” says David Walton, integration engineering manager at Makino Production Machinery, in Mason, Ohio.
This lack of compatible equipment extends across most industries. At Cerutti, that was also a reason for using a range of networks. “The choice of using other fieldbuses has been compulsory because of the lack of Ethernet-interfaceable devices, such as sensors, encoders, electro valves and so on,” Di Santo says.
Exploring tradeoffs
Even when Ethernet-compatible components are available, there are solid reasons for using fieldbuses at certain points in the factory. A couple are common throughout the electronics industry. “Studies show that it comes down to two things, the price of the solution and the performance,” says Scott Rohlfs, director of product marketing at vendor Mitsubishi Electric Automation Inc., in Vernon Hills, Ill. “Companies are concerned about determinism.”
Though real-time versions of Ethernet are available, fieldbuses provide speed without forcing system designers to pick one of these Ethernet alternatives. “The biggest disadvantage of standard Ethernet is that it can’t provide high-speed, real-time capability, and therefore, it is not a suitable solution for most machine applications,” says Stephan Stricker, product manager, B&R Industrial Automation Corp., an automation supplier in Roswell, Ga.
Even those who don’t need real-time performance may find that fieldbuses can help when they start bumping up against bandwidth limitations. Although many people think that Ethernet has almost unlimited bandwidth, that’s not really the case. Industrial Ethernet solutions still use transmission control protocol (TCP) and/or user datagram protocol (UDP), and are therefore not totally immune to data collisions on the network.
“Ethernet solutions work well as long as the network loading is under 30 percent, and under 10 percent if at all possible. Using switches (instead of hubs) limits the size of the collision domain. But even in these situations, collisions on the secondary side of the involved switches cannot be excluded,” says Helge Hornis, manager, Intelligent Systems, at vendor Pepperl+Fuchs Inc., in Twinsburg, Ohio.
One way to avoid potential bottlenecks is to use fieldbuses that are optimized to work with small, packetized chunks of data. These small packets are often passed to the Ethernet backbone on a fairly regular basis. “Fieldbuses usually handled scheduled tasks. You can schedule the timing so you can manage traffic that’s dropped onto the backbone,” says Shannon Foos, segment manager for process networks at Milwaukee-based automation supplier Rockwell Automation Inc.
Often, the bus couplers within these fieldbuses do not send data automatically. They are typically polled by a master device, responding only to requests. That can also help control the volume of data sent over the networks. “The traffic on the bus depends on the polling frequency of the master. The user can decide how often he needs a value from a device and can control the traffic through the polling frequency,” Stricker says.
Using architectures with small packet sizes and minimal header size is often an efficient route. Much factory equipment operates independently, only needing occasional instructions from external controllers. Similarly, these machines don’t send much data out to the network.
In these instances, much of the information needed to route signals through the large corporate networks Ethernet was designed for are extraneous. “Ethernet is flexible and open, but it carries a lot of overhead. Dropping a small sub-network is a lot simpler than using industrial Ethernet,” says Greg Dixson, automation systems marketing manager at vendor Phoenix Contact Inc., in Middletown, Pa.
Then there’s the other aspect that often comes with simple systems: their cost. Like Ethernet, fieldbuses are built into much equipment, so there’s little price burden. But there are other costs that come into play. One is in the overall infrastructure.
Adding in overhead that’s necessary when Ethernet’s bandwidth is being tested can bring the added expense of additional servers. When the efficiency of fieldbuses is added to their low price points, the advantage is often clear.
“Depending on the fieldbus and the application, there can be a cost advantage in using a fieldbus,” Dixson says. “For example, Interbus has a very low cost point, yet it’s incredibly efficient on data throughput.”
Adding new equipment to the Ethernet backbone can often be handled quite simply by using fieldbuses. That’s particularly true when there are many architectures feeding into the Ethernet architecture. It’s not expensive to add controllers that communicate with many different networks. For more on fieldbus networking, see "Fieldbuses Adapt to the Wireless World".
“We have a $70 device that runs multiple drives,” Dixson says. “It can run an Ethernet client, serve as a Modbus server and an Interbus master. It looks like a node on a network.”
Building networks
One of the keys to successful fieldbus implementations, as with any network, is to use gateways and couplers efficiently. Often, that can be accomplished by working closely with suppliers. Close cooperation with Rockwell helped Cerutti manage its presses. That network includes more than 100 managed switches.
“The use of a natural gateway component, such as ControlLogix, has been fundamental. It handles the simultaneous management of several networks of different types on just one platform. This ensures added value and easy deployment,” Di Santo says.
The ongoing integration of electronics is making it simpler to add the couplers and gateways that tie various networks together. As chips get smaller and more powerful, it’s becoming possible to extend networks by adding cards instead of finding a place for another networking module.
“Control can be distributed now. You can run the fieldbus directly into a card in the controller chassis instead of putting in a fieldbus adapter or protocol converter,” says Cliff Whitehead, strategic applications manager at Rockwell Automation, in Mayfield Heights, Ohio.
He explains that many users don’t want a number of intermediate boxes, so they eliminate them by bringing wiring into the chassis. Though that solution works in many instances, this architecture isn’t always best. “It’s not really that one way is better than another. They’re just different paths,” Whitehead says.
Programmable automation controllers (PACs) and programmable logic controllers (PLCs) have more networking capability built in, sometimes eliminating the need for network control units. These controllers often include the protocols for a number of popular networking architectures, making it simple for engineers to link together a number of different networking architectures.
“With our PLCs, you set the names in a function block and you can talk to any network. It’s relatively transparent to the user which network they’re using. That’s a lot simpler than setting up a switched network, which is a lot of work,” says Ted Thayer, PLC product manager at Bosch Rexroth Corp., a Hoffman Estates, Ill.-based automation vendor.
Another benefit of more powerful chips is the ability to handle multiple technologies using a single controller. Today’s powerful microcontrollers have the computing horsepower to handle the difficult task of motion control along with other tasks.
That makes it possible to add other tasks to an existing network motion control network. Simple devices can handle the communications needed to add functionality to an installed network.
“For motion control, a bus coupler lets you hang an I/O network onto the motion network,” Dixson says. “In the past, you may have had a motion network and separate Profibus and/or DeviceNet networks. Now you can just add a few I/O points and save costs.”
These couplers can also handle more than one task, helping keep costs down. “A bus coupler can function as a device on industrial Ethernet while serving as a master for a sub-network,” Dixson continues. “In the past, that was expensive.”
Versatility also brings other benefits and challenges. Equipment makers are attempting to keep costs down by using one architecture for all products. That can be difficult when equipment is shipped to various continents.
Regions often use different standards and the dominant vendors are often different as well. Some equipment suppliers use fieldbus architectures to address these changes so systems require only minor changes.
“When shipping machines to Europe, the required PLC may come from Siemens, while systems built for North American customers may have Allen-Bradley controllers,” Hornis says. “A lower-level network like AS-interface allows the complete I/O and safety structure to be designed once. The only component that will have to be modified for the various markets is a gateway.”
Managed or unmanaged?
There are also different paths when engineers want to link these fieldbuses up to the Ethernet backbones that are becoming common throughout the manufacturing world. Determining whether to use managed or unmanaged switches is another choice for developers.
“One of the big things to watch if you expect data to flow between industrial Ethernet and fieldbuses is to follow good recommended practices for Ethernet,” Dixson says. “You need to use a managed switch to manage bandwidth.” Using an unmanaged switch may be cheaper, but features like diagnostics may be lost. For example, it’s difficult to do port mirroring to examine networking issues, he explains.
Yet another concern for network developers is to make sure that the data they’re moving around is useful. It’s increasingly easy to get all kinds of data from every machine in a plant. But simply having reams of facts and figures about all these operations can be a hindrance as much as a help. A major push throughout the industrial world is to make sure that this information can be understood in ways that benefit the enterprise.
“Customers need to consider the type of information that’s available on their network and the level of information available on DeviceNet,” says Mitsubishi’s Rohlfs. “They may need to contextualize this data so it can be used on their Ethernet network. Data alone is not useful. You need information that can be acted upon.”
A related aspect is the human-machine interface (HMI). Liquid crystal displays (LCDs) continue to drop in price while their reliability improves, making them more suitable for industrial environments. Flat panel displays are increasingly being used to provide HMIs that are far more useful than those of the past.
“Enhancements come from Pepperl+Fuchs user-friendly large graphical LCDs with easily readable and understandable status information instead of cryptic LEDs blinking at various frequencies and colors that no one ever remembers,” Hornis says.
Companies in this Article
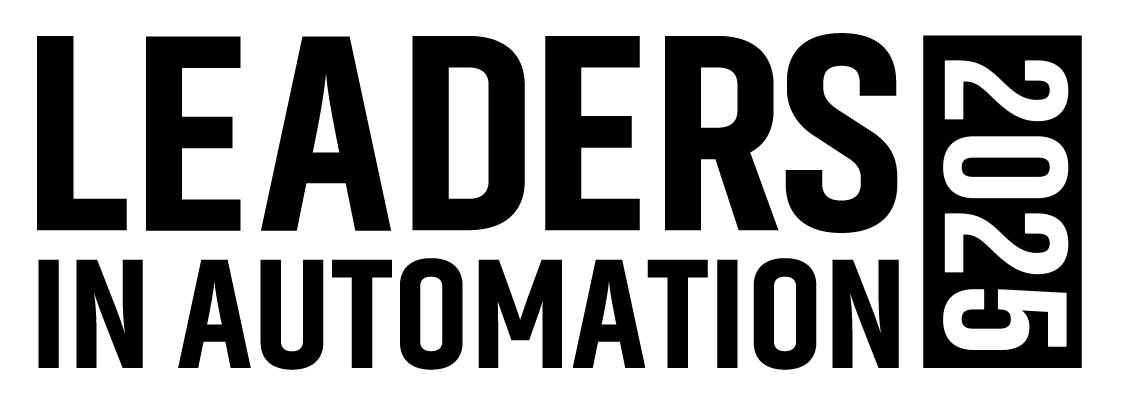
Leaders relevant to this article: