Powerful and flexible, the PAC, or programmable automation controller, is displacing its older brother, the programmable logic controller (PLC), in a growing number of packaging applications. That’s not surprising, considering its capabilities. ARC Advisory Group Inc., Dedham, Mass., began applying the term back in 2002 to describe the evolving class of controllers that went beyond the PLC’s traditional sequential logic capabilities to encompass additional functions such as motion and process control, with a single human-machine interface (HMI) used to access multiple functions.
Benefits of this single-platform, multi-function approach included fewer parts, less wiring, faster programming and maintenance time reductions. Add the enhanced communication capabilities that these newer devices possessed (capabilities more typical of a personal computer, or PC, than a PLC) and a general adherence to industry standards such as the programming languages based on the International Electrotechnical Commission’s IEC 61131-3, and it seemed obvious that the PAC was a winning package indeed.
But not to everyone. Faced with the new, a bit of skepticism is never amiss, and the question, “Why do we need it?” is fundamentally a healthy one. That’s precisely what some people asked about the PAC. Why introduce a new acronym into a field already replete with acronyms? Should it be viewed as a marketing ploy?
To a degree, yes, says Dick Motley, account manager, North American Distribution, for Fanuc Robotics America Inc., in Rochester Hills, Mich. “My understanding is that the term ‘PAC’ is part marketing hype, but it’s based on meaningful enhancements to traditional PLC functionality.” The new term, he says, reflects this expanded functionality.
Graham Harris, president of Beckhoff Automation LLC, a Burnsville, Minn.-based vendor, feels that diligence is needed. “Whether or not the term ‘PAC’ actually means something new is a mixed issue because it all depends on the philosophy and approach of the company using the term.”
He casts a critical eye on some PACs that, he says, “still use the same physical design as PLCs. Those have a CPU card using a proprietary processor and operating system (OS), power supply, backplane, network adapters, and I/O (input/ouput) rack with extra slots for additional processors to handle motion and even an integrated PC for communication. Very basically, you could consider this a PLC with extra hardware to handle the expanded need. Some might call it a ‘PLC Plus.’ ”
Harris, whose firm’s products include the CX line of PACs, contrasts this with what he regards as true automation controllers, built from the ground up “to handle all logic, motion, communications and even HMI.” Still, he feels the term PAC is useful because it indicates at least some measure of expanded functionality.
Signaling the difference
“Machine builders in the packaging industry are increasingly adding more complex motion control,” Harris notes. But he believes that calling a controller a PLC makes many potential users think the device is limited to sequential logic functions. Further, the PAC name indicates the enhanced connectivity via standard Ethernet interfaces that packaging machine builders and users are increasingly demanding.
It also indicates potential cost benefits. “There is an increase in use of PACs for this reason alone.” He cites the “rapidly growing need to obtain data from machinery for feedback on real-time events and activity levels. PACs normally provide these types of data much more easily and less expensively than a traditional PLC.”
“It’s a useful acronym,” agrees Ted Thayer, PLC and HMI product manager for Bosch Rexroth Corp., a Hoffman Estates, Ill., supplier that introduced its first PAC, the MLC 40, earlier this year. “It helps identify the range of functionality that people in packaging and other industries are looking for.”
Along with heightened communication capability, PAC users tend to comment most favorably on the integrated programming environment, or programming suite that, while not limited to PACs, is characteristic of them. And the new MLC 40 is no exception. “It’s one of our big selling points,” says Thayer. “Users don’t have to jump back and forth between different programming environments.” This often results in significant savings in design, programming, and engineering time and thus cost.
“We’re seeing quite a bit of adoption in packaging,” Thayer continues. “Our packaging branch sales are up over previous years with the introduction of the MLC 40.”
The potential maintenance advantages of PAC use are obvious—fewer devices, fewer connections and less wiring mean less to go wrong. But those same characteristics may also pay off in other areas as well.
“Sustainability issues are a growing concern in packaging today,” notes Mike Wagner, global business manager for OEM packaging at Rockwell Automation Inc., the Milwaukee-based automation supplier. “The PAC concept has an impact here. You’ve got a materials reduction in terms of less wiring and fewer devices, as well as the actual packaging of all those products that formerly went into those panels. You also have the waste reduction later when you have to recycle. This is in addition to the more obvious benefits like increased flexibility and reductions in development and commissioning times.”
Flexible filling
It was these obvious benefits that attracted Pac Tec LLC, of Milton, Wis. It builds cup- and tray-filling and sealing machines for the food packaging industry. To control their PT-4S model, the company opted for an Allen-Bradley CompactLogix PAC from Rockwell Automation. According to Pac Tec President and owner Carl Peterson, it’s a decision that has paid off in optimized production, reduced costs and, perhaps most importantly, increased machine flexibility.
Pac Tec can customize its standard machines for particular food packaging applications. This was the case with a PT-4S variant designed specifically for filling applesauce cups. As the machine indexes through its cycle, it places cups onto a carrier platform, fills them with applesauce, covers them with pre-cut foils, and then heat seals the foils in place. The application requires quick acceleration and deceleration as cups move from one section to the next, in order to run as much product through as possible. However, depending on the season and type of apple, some sauces have a thicker consistency, and some are more watery. If a watery applesauce is filled into the cups at too fast a rate, it can splash over the side of the cup and prevent the desired airtight seal.
“The product can change from week to week or even during the course of the day, and this is true for a lot of food manufacturers,” notes Peterson. “There is so much variability that customers really need the ability to make changes on the fly.” The PAC, along with Rockwell’s recipe program accessed through the control’s HMI, gives them that option.
“It allows them to quickly make changes to how a particular station operates and do it while the machine is operating. They can store those changes just for that day, and when they start up the next morning, the machine defaults back to the original parameters.” This, says Peterson, is a particularly popular feature, one facilitated by the system’s intuitive graphics, which also speed troubleshooting. “It makes it a lot easier for their help to operate and adjust the machine—they don’t have to call maintenance all the time.”
Previously, notes Peterson, “we handled all the support calls for our equipment. But now, performance issues are immediately apparent to machine operators through the operator interface, so they can quickly get the line back up and running on their own.”
Switching to the new controllers has also resulted in a number of cost savings. Pac Tec often customizes its standard machines such as the PT-4S for specific applications, and the PAC’s open architecture, together with the array of software tools in its programming environment, has speeded and simplified that process. As Peterson observes, “You don’t have to go back and reinvent the wheel each time.” This has resulted in a 20 percent reduction in design time, and a savings of approximately $5,000 in programming costs for each machine. Plus, integrating discrete, process and motion control in a single device has netted a 30 percent reduction in wiring. Best of all, the PAC-controlled machines have been welcomed by Pac Tec’s customers.
“They’re readily accepted, with open arms,” says Peterson. “The food packaging industry is becoming more and more technologically sophisticated, and our customers are specifying multi-disciplined control systems.”
Bucking the trend
All well and good, but Jack Chopper, senior control engineer for Baltimore-based Filamatic, makers of liquid filling systems, believes that when it comes to automation, one size definitely does not fit all. “The general trend in the industry is to no longer distribute intelligence,” says Chopper. “We’re bucking that trend.”
Filamatic is typically called upon to provide some degree of customization to its standard machines, depending on the target application. “The same model number with the very same arrangement of hardware can behave differently depending on the liquid and the type of bottles you are using,” he continues. “It presents us with many challenges.”
In response, the company has standardized on motion control technology from Pittsburgh-based Trio Motion Technology Inc., a firm which Chopper regards as best in class. “Trio’s controls and software make it very easy to create a generic program and then just attach values to input/output (I/O) points. This has allowed us to establish standard motion program modules for reuse across a wide array of applications, and not have to debug and test the same code over and over. We can confidently launch that code because we know it’s robust and it will work because we’ve used it so many times.” Thus, downloading as much intelligence as possible to the motion system helps Filamatic rapidly optimize its standard machines for specific applications.
He also sees a generational or demographic aspect to the controls question. “I think we are seeing a lot of folks entering the manufacturing field who don’t know how to program PLCs and haven’t been through the maintenance department, but have perhaps gone through a computer science track in college instead. Those folks are going to be more comfortable with a PAC because it resembles what they are used to. After all, you’d be hard pressed to find a ladder logic course in a college.” Filamatic’s target market, he says, is much more comfortable with PLCs, and capable of wringing maximum benefit from that technology.
Still, Chopper admits that PACs have been raising the bar in terms of communication, but believes that the data sharing capabilities of PLC-based systems can and will be improved.
It’s perhaps fitting that we give the last word in this discussion to Siemens, because this automation vendor can be thought of as occupying both sides of the PAC question. A pioneer in PAC-like functionality with its Siemens S7 controllers, company spokesmen have also been critical of the term, viewing it as unnecessary and perhaps confusing.
“When it comes down to it, the name is not all that important,” says Bob Nelson, controller marketing manager for Siemens Energy & Automation Inc., Alpharetta, Ga. “The best controller is the one that most closely enables your automation system to meet the requirements of your manufacturing process, and allows your manufacturing process to integrate seamlessly with other manufacturing and business processes. Regardless of the three-letter acronym used,” he stresses, “it is important to base a controller decision on the requirements of the entire automation system.”
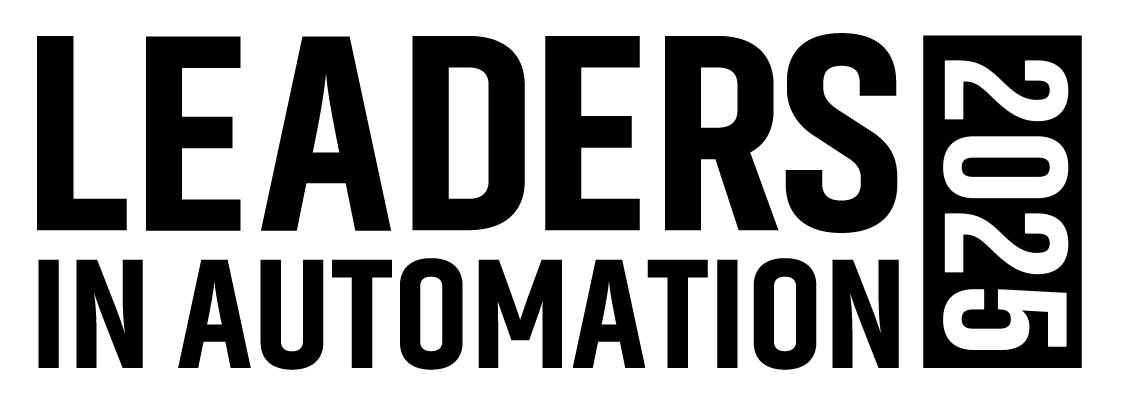
Leaders relevant to this article: