Linking disparate automation equipment remains a big challenge for engineers charged with networking the factory floor to the front office—in fields as diverse as manufacturing facilities and power distribution plants. Regardless of the industry, Ethernet is now the technology of choice.
In Oregon, electrical provider Portland General Electric is using the network to tie together a number of generators it taps to add capability during peak load times. Rather than buying a large turbine generator, PGE is tapping unused back-up generators at hospitals, businesses and other sites within its service area.
“Instead of turning on one big turbine generator, we’re turning on 35 to 50 diesel generators that have the same effect,” says Mark Osborn, distributed resources manager at PGE. “We’re getting peak performance from diesels in about 10 seconds, instead of waiting from five to 15 minutes to get turbines up to speed.”
On the factory floor, Canadian-based Konal Engineering & Equipment Inc. uses Ethernet to boost efficiency and reduces cost as it manufactures headliner systems for the automobile industry. Those headliners are created by thermally forming multiple layers, which all bond at different temperatures.
To set up and monitor key process variables during the manufacturing process, the manufacturer from Blenheim, Ontario, uses controllers from Watlow Inc., of St. Louis. Ethernet capability in the controllers means Konal no longer needs to buy a full thermocouple or input module, eliminating the cost of buying modules with several input/output (I/O) points that went unused.
“We wind up saving about $400 on each project, and that really adds up over a year,” says Mike Schoger, Konal’s manager of electrical controls. Data logging features also save additional time and resources, storing information for later analysis, he adds.
All you need
Ethernet is being increasingly accepted as the only network needed in many industrial sites. It forges a link between information technology (IT) departments and the factory floor, letting all operations share data without complex, error-prone translations required when multiple networks are used. This streamlining typically provides big improvements in productivity.
The use of Ethernet is so well entrenched in many companies that it’s bringing down more of the walls that have long existed between factories and offices. Managers in IT and on the plant floor are no longer considered adversarial “other guys.” In many plants, the groups now fall under one management structure.
Sidebar Story - Keep it Simple, Somehow
To read the accompanying sidebar to this article, go to www.automationworld.com/feature-4463.
“We’re seeing a lot of organizational structures merging, so manufacturing and IT personnel report to the same people. That increases awareness and interest on both sides,” says Dan Knight, industry solutions manager, manufacturing, at Cisco Systems Inc., the San Jose, Calif.-based network products provider.
Though there’s a merger of these groups, a common approach is to let the IT personnel familiar with corporate Ethernet extend the network onto the factory floor. “More and more, IT is moving onto the plant floor. System footprints keep increasing as companies want to know more about manufacturing,” says Claus Abildgren, marketing program manager at Wonderware, an automation software supplier based in Lake Forest, Calif. “Many customers have gone through some level of reorganization for this bridging.”
Abildgren notes that even when IT becomes the dominant force in an enterprise, IT personnel are taking more time to understand what plant managers need. “The IT guys have learned a lot through them, things like the need to run 24/7 and that you can’t shut systems down for patches or updates,” Abildgren says.
Though there’s been progress, getting humans to communicate efficiently isn’t as easy as networking machines together with the common structures provided by Ethernet. At many operations, the two groups still struggle to understand the intricacies of the other environment.
“The biggest challenge is still getting factory floor and IT to work together. The automation guys like the way things have been done, and the IT guys are interested in security and getting everything into a Web-type data structure,” says Joel Young, chief technology officer (CTO) at Digi International Inc., a Minnetonka, Minn.-based supplier of device networking products.
One of the key reasons companies are restructuring their networking groups is that in industrial environments, Ethernet makes it easier to link disparate products together. Automation equipment typically comes from a range of suppliers, and software throughout facilities is rarely homogenous.
“The biggest problem is that we’re maintaining multiple programmable logic controllers (PLCs). Every site is a one-off,” PGE’s Osborn says. “We’re programming PLCs that aren’t standard, many are older systems and the documentation is not there. Figuring out the coding for a new site can take hours.”
Using Ethernet and transmission control protocol/Internet protocol (TCP/IP) provides a single, well-known target for programmers, eliminating the confusion that reigns when these disparate systems are attached to a number of incompatible fieldbuses. It’s not just the factory floor equipment that provides incompatibilities that keep engineers employed.
Manufacturing execution system (MES) software and enterprise resource planning (ERP) tools also come from a range of suppliers, so there’s little compatibility in those areas. Even when companies buy MES and ERP tools from a single supplier, incompatibilities arise as different versions are used over the years. Standardized networking throughout the enterprise helps alleviate these incompatibility issues.
“Anyone who wants to implement MES or ERP throughout a factory needs a solid foundation to work with. Often, it’s the network infrastructure that provides that foundation. You need an infrastructure that’s built on standards, because there are a lot of proprietary things in most factories,” says Brian Oulton, networks marketing director at vendor Rockwell Automation Inc., in Mayfield Heights, Ohio.
Tough sledding
Though these incompatibilities are being reduced as more standards emerge, change is slow. Most vendors acknowledge that these differences will be tough to overcome. “There’s still a lot of room for improvement in this area,” says Wonderware’s Abildgren.
Improvement may be slow to come. MES and ERP are inherently different, meeting needs of distinct environments. “Data modeled in plant systems for MES is more granular than ERP data. This discontinuity in data models will continue for some time,” Abildgren says. “The industry has responded by adopting industry standards like ISA95 for terminology.”
That standard is one of a handful that reduce confusion by creating a single definition for a single term. They have enabled huge improvements in compatibility, but inherent differences remain. Front-office terms may relate to a single task or instruction, but when these instructions flow to the factory floor, a number of actions may be required to implement them.
“Some of this is not so much a technical issue as a semantics issue. Once you have a common language, you may find that the requirements at the business level may need to be broken down into five different jobs,” Abildgren says.
These issues are not going to go away soon, if ever. Most observers agree that Ethernet provides a common target that helps system managers overcome these software incompatibilities, as it does for hardware. Programmers know which hooks to use to link their programs to the ubiquitous network.
“When you’ve got various versions of MES or ERP software, you need a solid infrastructure, or there’s no chance of having a viable deployment. With a good infrastructure, you know what you’ve got and how to change it. Without a good architecture, you can deploy it effectively the first time, but then things start to diverge,” says Rockwell’s Oulton.
Despite the many benefits gained by using Ethernet throughout a plant, it’s not always practical to eliminate the fieldbuses that run down to I/O points. When economic conditions don’t make rewiring viable, there are a number of options. Gateways handle the transitions to TCP/IP formats needed throughout the rest of the network.
“When companies have a standard fieldbus on the factory floor, instead of replacing everything, you can replace PLCs with gateways that are effectively fieldbus masters,” says Nick Clute, network I/O specialist at automation products supplier Turck Inc., in Plymouth, Minn. “On the device side, our tools let people pull information from sensors and other devices and pop it into a gateway, converting it to IP,” Young says. Those gateways use OPC (an open connectivity standard) to port communications to formats that are useful in front-office applications, he adds.
Easier, not easy
Building Ethernet networks is simpler than working with various fieldbuses, but that doesn’t mean it’s simple. Factories often have far more I/O points than office networks, broadening the challenges that come with the range of equipment in industrial environments.
The PGE network is limited in scope, but as more generators have been added, the network has expanded to about 5,000 I/O points, some of them as far as 70 miles from the main site. Though sending messages over long distances isn’t a highlighted strength of Ethernet, the network is fast enough for this application.
“Ethernet has plenty of speed for the requirements. But for some of the large hospitals with multiple generators, we’ve gone to T1 lines to get enough bandwidth,” says Rod Parry, President of Factory IQ Inc., an integrator in nearby Sherwood, Ore., that used Wonderware software to help set up the PGE network.
One reason PGE needs so much bandwidth is that the central controller polls its 5,000 I/O points for updates every quarter second. When they’re providing power, managers can get real-time information on fuel management and the amount of power being exported, Osborn explains.
Another factor that increases bandwidth demands is PGE’s maintenance of those diesels. The utility handles maintenance for the companies that share their diesel generators. That’s a big incentive for those companies, and it assures PGE that everything will be ready when power is needed.
“In a hospital, it’s not likely that anyone would be in the generator room when an alarm goes off for a dead battery. It won’t start if the battery’s dead. If there’s a critical alarm, we can send our maintenance crew out,” Osborn says.
Avoiding situations that set off alarms has become an issue in networking, now that Ethernet links use Internet protocols. Security is still a nascent issue in most manufacturing plants, where the threat of viruses and hacker attacks is still ignored by many overworked networking groups.
But it’s become a high priority in the utilities industries after a number of brownouts and the 9/11 terrorist attacks. The North American Electric Reliability Corp. (NERC) has issued a number Critical Infrastructure Protection requirements in recent years. Osborn notes that the networks are all partitioned so they’re isolated from the Internet, resolving the utility’s cyber-security concerns.
Though security is still overlooked in many manufacturing facilities, observers note that it’s becoming a factor in more networking plans. The number of cyber attacks on industrial applications is rising, creating a greater sense of urgency throughout the field. “Security is becoming a bigger issue. In many plants, no one can get access without a password, and everyone needs to follow policies for security and access,” Abildgren says.
Companies in this Article
Sponsored Recommendations
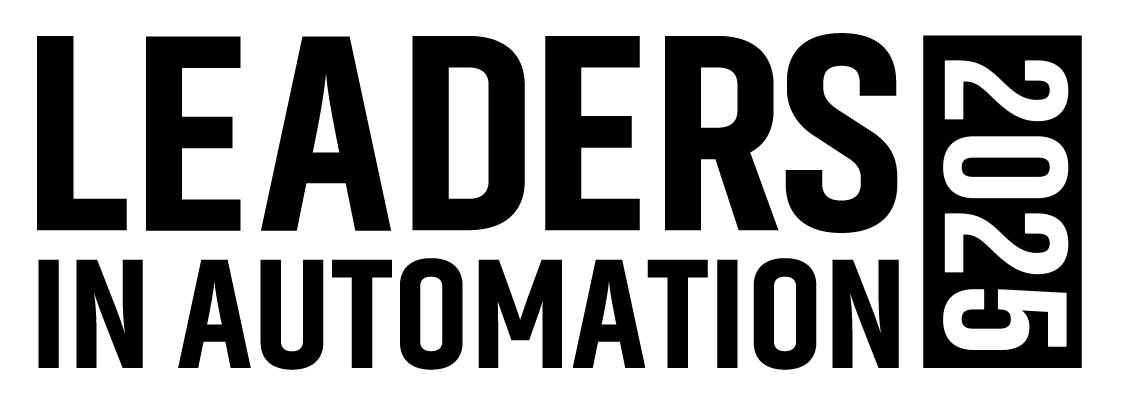
Leaders relevant to this article: