Together, the last two years have netted only modest growth in North American sales for the robotics industry, largely due to fluctuating demand from its largest customer, the auto industry. The bright spot has been sales of robots for packaging and palletizing applications, which continued to grow in 2007. This comes on the heels of a whopping 150 percent growth in this area from 2001 to 2006.
What’s fueling this growth? “Robotics offers flexibility. That’s one of the prime reasons for the increase of robots in packaging that we’ve seen over the last few years,” says Jim Cooper, manager of packaging distribution, Fanuc Robotics America Inc., Rochester Hills, Mich. “Consumer goods products and food processing companies are feeling more pressure from their customers and their own marketing departments to change package configuration for greater product differentiation and consumer appeal.”
Cooper cites the influence of the club or warehouse stores in this regard. “There, you are seeing an increased use of display pallets, or what’s referred to as shopable pallets, with two or three different flavors on a single pallet, and all flavors accessible from all sides. In the past, loading these nonstandard pallets was done manually in the factory, or else it was outsourced for repackaging to co-packers. Either way, it is all added cost to the producer.” Today, these pallets are increasingly being loaded by robots.
“These industry trends have had a significant impact on producers,” Cooper continues, “and are increasing producers’ need for flexibility both in their production and their palletizing. Typically, the most effective way of achieving that flexibility is with robots.”
This upswing has led to an increased emphasis by system integrators on engineering and marketing packaging and palletizing solutions, and by robot vendors on developing products specifically for these applications. Fanuc, for instance has designed its M-430iA/2F robot with a sleek profile with no food particle retention areas, in order to resist bacteria growth and rust. The robot also features special coating, materials and seals to withstand the caustic food industry cleaners and acids used in food plant washdown operations. Even the grease used in its moving parts is U.S. Department of Agriculture (USDA) certified “food-grade” grease.
Robot vendors’ software tools also reflect their growing interest in these applications. Last year, Adept Technology Inc., Livermore, Calif., introduced a packaging manager software product for its robots. According to Adept President John Dulchinos, it’s “an all-in-one packaging solution” for picking, placing and palletizing applications. “Until now, packaging customers had to rely on multiple software platforms to complete the multiple tasks involved in the packaging process.” The new package, on the other hand, integrates Adept’s robot control platform with conveyor tracking and vision.
Of course, adding robots to a packaging or palletizing operation entails a sizeable investment. But as Fanuc’s Cooper points out, there are different ways to look at cost. “Cost is actually one of the aspects that are driving the increase in robotics use. The value-based cost, which is a measure of the price of the robot, including performance, continues to come down. Every new version of a robot that comes out, whether it be our robots or our competitors’, is faster, has more payload, is more flexible and is at the same or a lower price point. So if you factor in all those performance factors, the value-based price of a robot has been coming down for years.” The result, he claims, is that robotic packaging and palletizing applications are easier to justify than ever before.
Rami Al-Ashqar, motion control product manager for automation vendor Bosch Rexroth Corp., Hoffman Estate, Ill, views the cost issue in similar terms. He first notes that today’s robots are, by nearly any measure, better than yesteryear’s models.
“They are now faster and more rigid, with faster and more accurate drives and motors and better motion controllers,” says Al-Ashqar. While he admits that in some situations, robotic solutions are more expensive than the alternatives, Al-Ashqar contends that in terms of up-front costs, a robot will eventually prove to be more cost effective than traditional solutions. “You will have greater predictability, higher quality and manual labor requirements will be reduced.”
Over the long haul, Al-Ashqar maintains, the cost of robotic maintenance is also a plus when compared to many other options. Fanuc’s Cooper agrees. “End-users need to be looking at the total cost of ownership of what they are purchasing. Maintenance is a part of this, and it’s also an area where robotics is superior to legacy type automation solutions. Virtually the only maintenance that is required on the robot itself—not the total system because there are going to be other components in the solution, such as conveyors and tooling—but on the robot itself, is basically greasing the zerk fittings and changing grease in the zerk fittings. Depending on the application, on how many shifts are running and other things, that could be once a year or even greater.”
The flip side of maintenance is reliability, and here, too, today’s robots excel, say industry sources. “Our robots are now at 72,000 hours mean time between failure. That’s 37 to 38 man years on a single-shift operation,” Cooper declares. “This is for the robot itself, certainly not the total system and its various components,” he is quick to add. “But having that type of mean time between failure for the robot, which is the major component of these systems, is significant when you compare it to conventional or legacy type automation solutions, which are nowhere near that level.”
Cooper is confident that this sort of reliability and its impact on the total cost of ownership is another factor driving the increased use of robotics at consumer goods and food companies.
If concern over the cost of a robotic packaging or palletizing system is less of an inhibiting factor than in the past, what about complexity, specifically the complexity which the additional programming entails? This is another historical concern that robotics professionals today feel is no longer a significant stumbling block.
“A lot of things have been done to make programming easier,” says Adept spokesman Jay Sachania. “Canned application programs, examples, and expert systems have all combined to make programming easier.”
And as Bosch Rexroth’s Al-Ashqar points out, “Anything you bring into the plant that interfaces with a computer requires programming, and robots are just another example. In addition, the development of programming standards and the use of function blocks is making it simpler to program robots.”
Software tools from the leading robot vendors also ease programming complexity, and today, those software toolkits typically include a vision component. In the 1990s, vision-guided robots were the mark of a high-end application, but now those applications are becoming increasingly common. One sign of this is the fact that robots today are frequently shipped “vision-ready” with a vision plug-in port on the processor board and vision software embedded in the controller. Fanuc, in fact, has begun to ship all of its robots vision-ready.
The reasons for this proliferation of vision-guided robotics in packaging, and in other applications, lie in the benefits vision can bring, and in the changes the technology has undergone.
Primary among those benefits is the fact that vision can provide 100 percent inspection and product verification, vital in today’s packaging operations. Also, vision makes the flexible robot even more flexible. The vision-guided robot doesn’t require costly precision fixtures to hold parts, or additional labor or complex engineering to orient parts, and it doesn’t need to depend on upstream actuators, sorters and feeders to separate parts for processing. Thus, it can process a variety of parts without tooling changeover. Plus, vision provides the added benefit of automatic collision avoidance for safer work cells.
As for changes, Cooper notes that “vision-assisted robots have been used in packaging for years, but it is the fact that vision has become more cost-effective, easier to integrate and more robust that has resulted in the substantial growth that we have seen in the last few years.”
Robustness in the vision world typically springs not from physical qualities but from algorithms. Randy Kemmerer, machine vision promoter for automation supplier Siemens Energy & Automation Inc., Alpharetta, Ga., began his career as a vision application engineer. “In the early days,” he recalls, “vision systems just basically counted pixels. You had an image and the system would just count pixels to find defects, to find edges. Now, because of application development and the growth in processing power, the algorithms are a great deal more intelligent,” Kemmerer says.
“These newer algorithms are able to minimize many traditional lighting problems. For instance, we can do a lot of things now with pattern matching for robotic applications, and pattern matching is relatively immune to lighting changes.”
Geometric pattern matching learns a part's geometry using a set of boundary curves that are not tied to a pixel grid, and then looks for similar shapes in the image without relying on specific gray levels. The result is a dramatic improvement in the ability to accurately find parts despite changes in angle, size and shading.
“I don’t want to downplay the role of lighting, because it’s still a huge factor in any vision application, but with correct lighting, we can now do applications that we couldn’t do five or 10 years ago.”
Integrating vision into robotic applications has been eased in a number of ways. For instance, one of the essentials for getting a vision-guided robot application up and running is calibrating the vision system’s pixel-based coordinate system with the robot’s coordinate system. Whether the application involves conveyor tracking for pick-and-place, palletizing or component assembly, vision-to-robot calibration is required to maintain system accuracy and repeatability.
“Calibration is one of the biggest challenges,” notes Bryan Boatner, product manager for In-Sight vision sensors, Cognex Corp., Natick, Mass., “because it involves more than coming up with a scaling factor that relates pixels to a measured dimension. If there’s optical distortion from the lens, or perspective changes due to camera mounting angle, the vision software must include special algorithms to correct for these distortions in the image.”
In the past, Boatner explains, calibration has often been time consuming and difficult. Now, however, “standard practices have evolved to facilitate the task. The most advanced vision software now incorporates step-by-step “wizard” functionality to guide users through the process of correlating image pixels to robot coordinates using a variety of techniques including grid-of-dots, checkerboard or custom calibration plates.
“Newer software also supports multi-pose 2D calibration to optimize system accuracy and enable the use of a smaller, more manageable calibration plate in large field-of-view applications.”
Integration tasks can also be eased by the software packages supplied by robot vendors. Fanuc’s iRVision is a case in point. It features a 2D robot-guidance tool to accomplish part location, error proofing and other operations that normally require special sensors or custom fixtures. Though tools like this aren’t designed for complex applications, they can help users get basic applications up and running quickly.
There is also the “been there, done that” factor. As Siemens’ Kemmerer explains, “Because vision has been around for a while, more people have had time to become familiar with it. They have had time to learn by experience what the pitfalls are and what it takes to make an application a success.”
As for cost, vision system prices have declined relative to performance—and often in absolute terms as well. A prime example of this is the smart camera. Capable of handling a variety of mid-range applications, these cameras both capture and process images without being tied to a personal computer (PC). Prices vary, but these cameras can often be purchased for around $5,000.
Cheaper still is the vision sensor. These devices can be deployed relatively quickly and perform a variety of essential tasks such as verifying presence/absence, fill level or label positioning. Importantly, the smart cameras and vision sensors on the market today often boast an IP65 rating, meaning they can withstand contact with water, or even an IP67 rating, signifying they can withstand submersion.
The picture, then, is of two linked technologies, both of which are increasing in performance while getting ever more affordable. Couple this with the frenetic pace of product and package change that characterizes today’s retail market, plus government and market demands for safety and traceability, and growth in vision-guided robotic packaging and palletizing applications looks like a safe bet.
For an informative Webcast “Packagers Turn to Robots for Flexibility and Price,” visit www.automationworld.com/view-3043.
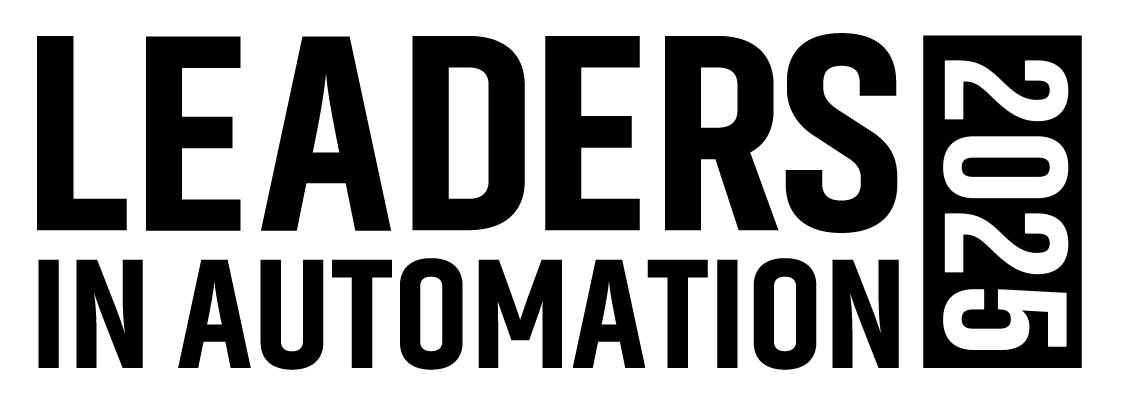
Leaders relevant to this article: