Now that Ethernet has become the backbone of choice for industrial facilities, the network is extending its reach by taking on entrenched fieldbus technologies. Though that effort is bearing fruit, fieldbuses are maintaining solid growth.
Ethernet is addressing a huge range of applications, from conventional processing plants to those little known for electronics. For Anguil Environmental, a Milwaukee company that installs equipment that helps factories reduce air pollution, the local area network (LAN) provides many solid benefits. Many of its installations span large facilities, with equipment in hard-to-reach areas such as smokestacks.
“We used to do a lot of hard wiring from inside the control panel to the machines, which had a number of I/O (input/output) points and two or three variable frequency drives for their fans. Ethernet eliminates a lot of wiring and also lets us attach things like a chart recorder directly to the network so the company can gather data to send to the Environmental Protection Agency,” says Luke Warnes, control systems designer at Anguil, which uses a number of Rockwell Automation networking products.
Eliminating the time-consuming task of hard-wiring many different products has a huge payoff. “The component costs are slightly higher, but you can save a ton of money on installations. On a big facility, we can save from $5,000 to $15,000 just on the cost of wiring from the main controller to the I/O points. Spending $1,200 on hardware to save $15,000 is a pretty good value proposition,” Warnes says.
In other applications, Ethernet is proving that it’s come a long way since detractors said that the office network wasn’t rugged enough to operate in nasty industrial environments. For example, few applications need more sealing protection than a car wash, where components are exposed to heat, water and detergents most of the day.
When Atlanta-based Auto Data Inc. decided to get into the car-wash market last year—expanding beyond its core business of providing point-of-sale systems to quick lube stores and others—design engineers needed an easy way to link programmable logic controllers (PLCs) to sprayers and other components. To maintain its reputation for reliability, the company opted to employ industrial grade PLCs instead of the personal computer (PC) technology used by many entrenched competitors in the automated car wash business. Those PLCs control a number of valves, timers and other components that operate in very rough environments in vastly different geographies and climates.
Auto Data has experience with Ethernet technology, using it to tie its front-office systems together and link them to remote headquarters. That made it an easy decision to use equipment from Modbus originator Schneider Electric, of Rueil-Malmaison, France, to create “an environment where the whole car wash is Ethernet and Modbus. Modbus over Ethernet lets us talk to anything on the Internet,” says Auto Data owner Bill Schad.
Modbus was necessary because some of the starters and other specialized equipment used older serial Modbus technology. Schad expects to extend Ethernet’s reach in the future. “We’re happy we’ve chosen this because more doors will open. Serial implementations are a dead end,” he says.
Roadblocks
That inability to find low-level components that are Ethernet compatible is one of the biggest obstacles preventing Ethernet from completing its takeover in the factory. Even those who are bullish about using Ethernet for all types of networking acknowledge this shortfall. In some areas, only a few device-level products offer Ethernet compatibility. “Valves are the only devices becoming Ethernet-enabled at a low level now, but I expect to see more products moving that way,” says John Rinaldi, networking project manager at Real Time Automation, a Wauwatosa, Wis., contract service provider that also makes gateway boards and modules.
However, he notes that there’s a powerful non-technical issue that’s helping to change this. “Customers love Ethernet,” Rinaldi says.
He’s not the only one who sees strong support that has nothing to do with technical performance. “There’s a strong non-technical driving force: Many people feel Ethernet is better,” says Carl Henning, deputy director of the Profibus Trade Organization (PTO), in Scottsdale, Ariz.
Not ubiquitous
PTO is making the transition to Ethernet compatibility with Profinet, predicting that it will one day replace the fieldbus network that’s gained a huge following over the past several years. But estimating a date for that prediction remains a difficult proposition. “Eventually, over many years, Profibus will fade out, as will all fieldbuses. But usage is not fading nearly at the rate we expected. Profibus is still growing at around 25 percent,” Henning says. That growth is partly because there are a few thousand Profibus devices, but Profinet offerings are still counted in hundreds, he noted.
Some equipment makers feel that the transition may take many years. Woodhead Industries, a Northbrook, Ill.-based division of connector maker Molex Inc., makes a number of Ethernet products. Though its factories have Ethernet backbones, the manufacturer believes that efforts to move it to the next level are bringing more headaches than success stories.
“Most of the people trying to push it down fruitlessly are at the bleeding edge. We have no immediate plans to use Ethernet to go down to the controller or sensor level in our plants. The cost points are not there yet,” says Ed Nabrotzky, group product manager, Industrial Communications Products, at Woodhead.
Many observers note that sensors, actuators and other fairly simple components won’t see any solid benefits by adding the overhead associated with Ethernet and transmission control protocol/Internet protocol (TCP/IP) or other protocols commonly associated with the LAN. Components that only send tiny amounts of data will be adding a lot to network bandwidth, which can be an issue at times.
“Internet protocols have minimum packet sizes of 1,280 bytes without the checksums and other overhead. In practical terms, if you’re using a network to turn on one I/O point and you need to send 1.4 Kbytes, it’s not that necessary,” says Scott Hibbard, technology vice president at automation components supplier Bosch Rexroth Drives and Controls, of Hoffman Estates, Ill.
For these kinds of applications, conventional fieldbuses such as DeviceNet, Modbus and Profibus aren’t the only existing alternative. The AS-Interface popularized in Europe is gaining solid acceptance worldwide. “The AS-Interface is still effective as kind of a one-bit network for on-off stuff like a solenoid switch. Ethernet is still not inexpensive enough to replace it,” Henning says.
Many protocols
While executives endorse the concept of a single network that spans the enterprise, engineers know that goal is rarely accomplished. While the cabling, chips and connectors are the same, many industrial networks aren’t compatible with front-office LANs.
That’s because Ethernet doesn’t offer the determinism typically needed in the factory. So there are a number of alternative technologies that use alterations to provide determinism or even real-time performance. Some vendors feel this removes many of the advantages gained by using a single network throughout the corporation.
“If you only use Ethernet’s physical media, and alter the open stack to get real time or determinism, you’ve corrupted things. Using an unmodified stack is critical if you want to get all the benefits,” says Joe Kann, vice president of business development at vendor Rockwell Automation Inc., in Milwaukee.
But others contend that getting the desired performance level is more beneficial than letting a packaging machine send messages to the chief executive officer. They say that users should pick the protocol that meets their needs just like they pick hardware that meets their requirements. “People need to understand what type of performance they need and what they can get from Ethernet, then select their protocols based on that,” says Skip Hansen, I/O systems product manager at vendor Beckhoff Automation LLC, in Burnsville, Minn.
Others note that it’s not difficult to convert data from one format to another when it is necessary to send messages to nodes that use a different protocol. That was a key part in the development of Profinet. “Profinet has proxies by design. With this proxy concept, someone with Profinet can go through the proxy to move from production systems to the front-office space,” Henning says.
Even proponents admit that the variants have a strong position that isn’t likely to see erosion. Charlie Piper, fieldbus product manager at automation vendor Invensys Process Systems, in Foxboro, Mass., cites a number of benefits gained by using compatible Ethernet protocols throughout a plant. But he also admits that there’s little chance that Ethernet TCP/IP will replace alternative protocols. “Without a single standard protocol on Ethernet, the industry is unlikely to see a single open gateway or linking product to gather fieldbus data onto Ethernet networks,” he says.
When that protocol issue is combined with the task of getting companies to make components that are Ethernet compatible, the result will probably be slow expansion of Ethernet in fieldbus applications. Managers who can’t get hardware won’t have to worry about which protocol they pick. “I don’t see things like pressure sensors becoming Ethernet compatible overnight. Fieldbus protocols are not in danger of being displaced for some time,” says John Yingst, product manager at vendor Honeywell Fieldbus Systems Solutions, in Phoenix.
Minimizing mischief
While Ethernet compatibility lets people tap into systems easily to do things such as remote diagnostics, this easy access highlights an Achilles Heel. Network managers have to figure out how to make sure only authorized people can get in and make changes.
Security techniques must prevent hackers and other outsiders from getting in to do damage. These threats range from mere mischief makers to those who try to extort companies by taking control of their production lines. But system developers note that disgruntled employees can also wreak havoc on the plant’s operations. “That’s an often unknown factor; you’re more at risk from internal people who want to make mischief,” says Rinaldi, at Real Time Automation.
One positive is that tools developed for front-office systems have become fairly sophisticated, so they can spot potential problems before things get serious. “There are a lot of great diagnostic tools for things like monitoring traffic. They can trigger alarms when abnormal traffic patterns occur,” says Brian Oulton, network marketing manager at Rockwell Automation’s Mayfield Heights, Ohio, operation.
Another internal threat can come from the network managers in charge of protection. The techniques they use to protect front-office machines from outsiders can cause problems in the plant, where tying up equipment unexpectedly for even a few milliseconds can cause major issues. “There can be problems with virus updates. They can’t just happen any time information technology (IT) picks. You need firewalls so everything in the plant isn’t treated as just another Ethernet node,” says Woodhead’s Nabrotzky.
That underscores the need for IT managers and control engineers to understand requirements on either side of the system. Though many corporations tout programs in which all groups work together for the common good, that’s often easier to mandate than to implement. “We still see companies where there are almost fights between control engineers and IT people. The control engineers want six IP addresses and the IT people don’t see why they need so many,” Rinaldi says. On the factory floor, some engineers want to have extra addresses to add hardware, and they don’t want the changes that routinely occur when front office networks are reconfigured, he explains.
Health monitoring
Along with compatibility, a key benefit of putting individual devices on Ethernet is the ability to monitor their health and performance. The available tools provide far more options than those available for more specialized fieldbus architectures.
Observers note that these tools give managers capabilities that simply aren’t possible with older architectures. “Ethernet gives you a world of capabilities like remote analysis and troubleshooting. When you have XML (Extensible Markup Language), you can talk to other devices, doing things like sending out statistical data,” Rinaldi says.
These diagnostic capabilities are important for any operation, but they’re particularly helpful in regulated fields such as pharmaceuticals. There, automating the data-gathering process can provide big benefits.
“In regulated industries, companies can do scheduled checks and provide diagnostics, which isn’t possible without Ethernet. That really helps in compliance with Environmental Protection Agency regulations,” says Kevin Summ, marketing manager at Anguil.
Ethernet compatibility also opens access for the many engineers and technicians who know how to make repairs but haven’t worked with fieldbuses. “The main attraction is that the minute someone sees an RJ45 connection, they know they can do anything, hook up a laptop and do tricks they couldn’t do before with the same tools they use across the enterprise,” Hibbard says.
For more information, search keyword “Ethernet” at www.automationworld.com.
Sponsored Recommendations
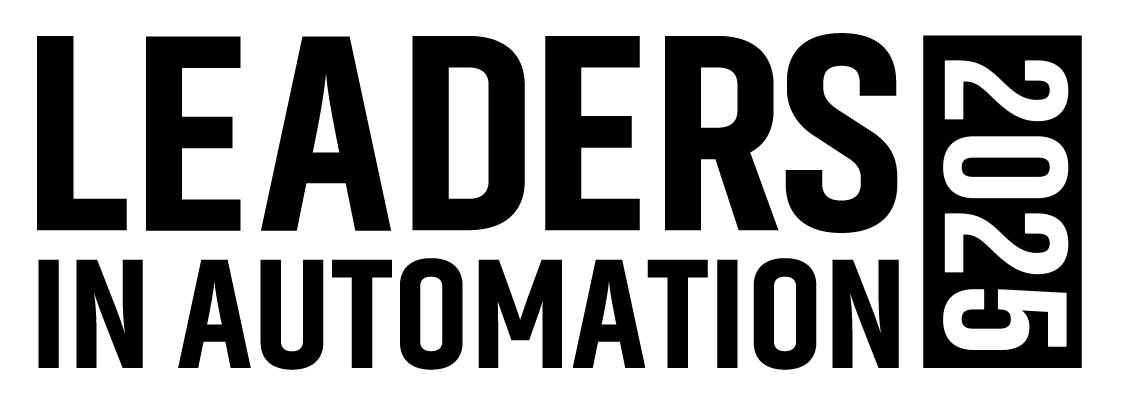
Leaders relevant to this article: