To get an inkling of the impact that advances in motion control technology have had on packaging, step into your local supermarket, stroll over to the snack aisle and look at the chips. Odds are you’ll find some variety packs—you know, four different flavors, each with its own bag design, all enclosed in a single package. Perform that same stroll in different parts of the country and you will notice that the contents of that variety pack change, based on regional preferences, as determined by market research. And if you find a combination of flavors that you like, better stock up, because tomorrow it might be yanked off the shelves for a new mix.“Today, it’s all about time to market, configurability and being able to grow with your market,” says Mike Wagner, business development manager for the Global OEM Team, for vendor Rockwell Automation Inc., Milwaukee . This requires packaging equipment that is flexible enough to permit rapid changeover from one type of packaging to another.OK, the credit (or blame, depending on how you feel as a consumer) for this hyperkinetic flexibility can't all be laid at the door of motion control technology. Innovations in motion control play out within a nexus of interlinked technologies. Still, motion control can be seen as both an enabler and a symbol of the wider changes affecting the packaging realm.Small and smartThe key word for packaging today is integration, and it’s evident in the new generation of servo modules that combine the servo motor and drive into a single compact package. Attempts to combine these components began more than a decade ago, with varying degrees of success. Recent advances in semiconductor technology, however, have allowed technology providers to make these units smaller and, more importantly, smarter. Case in point: the GenNext series from Bosch Rexroth Corp., Hoffman Estates , Ill. GenNext is a series of motion and control products whose hallmark is distributed intelligence. “With GenNext, the processors are in the drive itself,” explains Al Morin, packaging industry specialist for Bosch Rexroth. “As the electronic components became lower cost and you could get more functionality out of them, it only made sense to put more intelligence in the drive.” While some might think that this would add more cost to the system, the opposite is actually true, according to Morin. “It actually gives you a lower-cost system because now you don’t have to be concerned with how many processors you need to run a big system,” he notes. “With a system like this, you can run from one up to 64 axes with one control, so the cost doesn’t go up on the control end; you’re just adding drives as you need them for your application.“Of course, when you add additional processors, you have to do additional programming,” adds Morin. “You have to get those processors talking to each other, you have to coordinate them. But as far as performance goes, you are not going to see any degradation in the controller as you add axes, because each axis brings with it its own intelligence. And of course, you’re not going to see any degradation in machine performance either, and machine performance translates into throughput.”Integrated servo modules can potentially help reduce the time it takes to build a machine, and decrease its installation time and cost. As Morin points out, they can in some cases reduce control costs. Importantly, integrating drives with motors also reduces cabinet space.Targeting cabinet space"I’ve been involved in motion control for my entire career,” says Rockwell’s Wagner, “and there is no doubt that the proliferation of servos has been great in terms of flexibility, cost and accuracy. The problem is that you've ended up with so many servos that the cabinet becomes bigger than the machine itself. That's a real problem, given the fact that plant floor space is a limited and valuable commodity. Where do you put all these large, bulky cabinets? It kind of defeats all the effort that has gone into shrinking the footprint of the machines.”Elau Inc., a Shaumburg, Ill. , packaging controls vendor, claims a reduction in cabinet space with its new iSH integrated servo module by, in some cases, as much as 16 to one. A concomitant benefit is the reduction in wiring. This is a benefit that adheres to all integrated servo modules. The iSH seeks to up the ante, by replacing the three separate cable drops typically required for power, input/output (I/O) connections and synchronized motion with a single cable attached to a distribution module that, in turn, can handle up to four servo modules. Along with further reductions in wiring time and cost, this approach obviates the need for daisy chaining servo modules, which can lead to a single point of failure for an entire system. And any wiring connection is a potential point of failure.“If you look at MTBF (mean time between failure) calculations,” notes Wagner, “most of them are closely related to the number of connections, so any time we can reduce the number of connections, you can see significant decreases in MTBF. You're also reducing a potential cause for failure on installation and start-up, which is significant because development time is becoming a crucial consideration these days.”Sue Dorsheid, product line manager for supplier Danaher Motion, Wood Dale, Ill., agrees that reducing wiring is one of today’s top priorities, and stresses that it’s the digital nature of today’s motion control components rather than a particular product configuration that’s the real enabler. “Customers want to reduce the amount of wiring on a machine, and one of the easiest ways to do that is to go from an analog interface—the +/-10 volt interface between the control
and a servo amplifier—to a digital interface, where instead
of having, say, eight wires going back and forth with the encoder feedback and the analog output, you have a single ‘CAT 5’ Ethernet cable. At that point it’s plug-and-play.”Dorsheid cites some other advantages of going digital. “First of all, you get better noise immunity. Also, you can typically have a little bit longer cable runs, which gives you more freedom in distributing the drives on the machine.” This can often make the design and installation of the machine a little easier, she notes. “Lastly, the amount of data that can be transferred over that digital network as opposed to hardwired signals is just enormous—head and shoulders above the amount of information you used to be able to get,” Dorsheid points out. “Now you can get actual real-time information from the drive, you can launch your current torque in real-time, you can get diagnostic information from the drive that is very detailed, and you can get an entire fault history as opposed to just indicating that the drive has a fault.” There are many benefits of going to a digital control network, which, according to Dorsheid, is why most control vendors are now migrating to this approach.The PackML effectWhenever the subject of innovation in motion control arises, it’s a good bet that mention of PackML is not far behind. These packaging machinery language guidelines, promulgated by the Packaging Workgroup of the Open Modular Architecture Control Users Group (OMAC), adapt the existing state model to the specifics of packaging machinery, adding new data definitions, or pack tags, to describe the basic states that all packaging machinery undergo. These guidelines are generally implemented with the aid of IEC 61131 programming languages. Developed by the PLCopen organization, this suite of languages, adopted as an international standard by the International Electrotechnical Commission, contains the familiar ladder diagram, but also includes higher level languages that permit “modular” programming, such as the use of function blocks, or software objects, containing subroutines for specific tasks that can be reused as standardized modules. Importantly, the IEC 61131 languages can be nested within each other. Taken together, these two software standardization initiatives permit automated packaging equipment, particularly today's digital motion control products, to attain the full measure of the flexibility that is built into them. It’s a promise not lost on Mike Lamping, technology leader for Procter & Gamble, the Cincinnati-based consumer products giant.“The reason we are trying to use PackML is that we know it will lead to lower costs,” notes Lamping, “lower costs for engineering, lower costs for maintenance and lower costs for operation.” The idea behind PackML is to provide a common look and feel amongst all packaging machines, Lamping observes. “And if you have this common look and feel, and you are using IEC 61131-type functional programming rather than monolithic-type programming, then it should be easier to understand how a machine is operating, and then easier to understand how to troubleshoot that machine as well.“For instance, if you look at some of the PackML-
compliant code that's written in Sequential Function Chart (an IEC 61131 program organizing principle), it’s a lot easier to understand how that code is operating than it is with standard ladder logic, primarily because the function charts point to where the code is actually being executed,” Lamping says. “So, if you’ve got a machine that's got quite a bit of logic in it, the function charts actually point to where the logic is being run, making it a lot easier to troubleshoot or nail down a problem very quickly vs. trying to troubleshoot all the code at once.” This kind of code is easier to troubleshoot, easier to replicate, and a lot easier to start up for the first time, according to Lamping.Rockwell’s Wagner agrees, especially when it comes to maintenance. He cites an instance in which an original equipment manufacturer (OEM) shipped toAustralia a machine equipped with Rockwell control and motion technology, including PhaseManager. PhaseManager embeds PackML-compliant code into Rockwell’s Logix family of controllers, and allows sections of the code to be isolated and viewed through a built-in PhaseMonitor.The machine developed a motion-related glitch during commissioning. “Fortunately, we had somebody over there who was doing training. This was just basic training on our software, they weren’t expert in that application or in motion, but they understood PhaseManager. As a result, they were able to narrow things down and focus in on the problem and successfully diagnose it—without even understanding the application.”What’s next?That’s a look at some key aspects of the present, but what does the future hold for motion control and, by extension, the systems it integrates with? Drag and drop, responds Tom Jensen, senior technology evangelist for Elau. “One of the promises of Make2Pack (an initiative of the SP-88 committee of the Instrumentation, Systems and Automation Society, ISA) is software modularity. And software modularity is the key to programming that is easily navigated,” Jensen says. “We’re big supporters of that, and we're working to make it even easier.” Elau has developed a template that allows more drag and drop, more parameterizing, and less programming, Jensen says, adding, “We’ll see more of that in the future.”For P&G’s Lamping, the future holds more use of standardized panels. “In the long term, I think we’re going to end up with standardized panels that are pre-wired, because what you would like to see is a panel that could serve many different functions or many different kinds of machines,” he observes. This might mean drive panels for four drives, eight drives, 16 drives, whatever the required number was, for example, which could be used on almost any packaging machine that required multiple drives. Lamping forsees each panel having the safety system, the power system, the I/O system, the human-machine interface, or whatever was required, built in. Farfetched? Lamping insists it’s not. “I've seen some indication that some of the control vendors are moving to panels and software that would be basically off-the-shelf, so you wouldn't be going through a huge engineering cycle every time you had to build another machine,” he says. “You’d have a base to start from.” Such an approach would pay benefits by extending the standard look and feel concept down into the machine wiring and control systems, Lamping says,enabling maintenance to be performed by simply replacing standardized cabinet sections. Lamping cites the example of automobiles. If a component, such as a fuel pump, fails, the owner doesn't need to try to rebuild it; he or she can simply elect to have the old one pulled out and a new one put in.Based in part on his previous experience in the semiconductor industry, W. Jarrett Campbell, packaging segment manager for automation vendor Schneider Electric, in Raleigh , N.C. , foresees greater networked connectivity and access to data from the drives or anywhere else on the plant floor. In addition, he sees modular, object-oriented programming influencing packaging machine design and capability as it facilitates what he calls “the move away from cam-driven machines to completely robotic machines. This will open up an array of possibilities, because if you’ve got those extra degrees of motion, you’re going to ask yourself, ‘What else can I do with this machine?’ It’s all just software at that point.”Vision systems are capable of reading a variety of codes and characters—both for verification and for data collection. Source: Cognex Corp.For more information, search keywords “motion control” and “packaging” at www.automationworld.com.
and a servo amplifier—to a digital interface, where instead
of having, say, eight wires going back and forth with the encoder feedback and the analog output, you have a single ‘CAT 5’ Ethernet cable. At that point it’s plug-and-play.”Dorsheid cites some other advantages of going digital. “First of all, you get better noise immunity. Also, you can typically have a little bit longer cable runs, which gives you more freedom in distributing the drives on the machine.” This can often make the design and installation of the machine a little easier, she notes. “Lastly, the amount of data that can be transferred over that digital network as opposed to hardwired signals is just enormous—head and shoulders above the amount of information you used to be able to get,” Dorsheid points out. “Now you can get actual real-time information from the drive, you can launch your current torque in real-time, you can get diagnostic information from the drive that is very detailed, and you can get an entire fault history as opposed to just indicating that the drive has a fault.” There are many benefits of going to a digital control network, which, according to Dorsheid, is why most control vendors are now migrating to this approach.The PackML effectWhenever the subject of innovation in motion control arises, it’s a good bet that mention of PackML is not far behind. These packaging machinery language guidelines, promulgated by the Packaging Workgroup of the Open Modular Architecture Control Users Group (OMAC), adapt the existing state model to the specifics of packaging machinery, adding new data definitions, or pack tags, to describe the basic states that all packaging machinery undergo. These guidelines are generally implemented with the aid of IEC 61131 programming languages. Developed by the PLCopen organization, this suite of languages, adopted as an international standard by the International Electrotechnical Commission, contains the familiar ladder diagram, but also includes higher level languages that permit “modular” programming, such as the use of function blocks, or software objects, containing subroutines for specific tasks that can be reused as standardized modules. Importantly, the IEC 61131 languages can be nested within each other. Taken together, these two software standardization initiatives permit automated packaging equipment, particularly today's digital motion control products, to attain the full measure of the flexibility that is built into them. It’s a promise not lost on Mike Lamping, technology leader for Procter & Gamble, the Cincinnati-based consumer products giant.“The reason we are trying to use PackML is that we know it will lead to lower costs,” notes Lamping, “lower costs for engineering, lower costs for maintenance and lower costs for operation.” The idea behind PackML is to provide a common look and feel amongst all packaging machines, Lamping observes. “And if you have this common look and feel, and you are using IEC 61131-type functional programming rather than monolithic-type programming, then it should be easier to understand how a machine is operating, and then easier to understand how to troubleshoot that machine as well.“For instance, if you look at some of the PackML-
compliant code that's written in Sequential Function Chart (an IEC 61131 program organizing principle), it’s a lot easier to understand how that code is operating than it is with standard ladder logic, primarily because the function charts point to where the code is actually being executed,” Lamping says. “So, if you’ve got a machine that's got quite a bit of logic in it, the function charts actually point to where the logic is being run, making it a lot easier to troubleshoot or nail down a problem very quickly vs. trying to troubleshoot all the code at once.” This kind of code is easier to troubleshoot, easier to replicate, and a lot easier to start up for the first time, according to Lamping.Rockwell’s Wagner agrees, especially when it comes to maintenance. He cites an instance in which an original equipment manufacturer (OEM) shipped to
Sponsored Recommendations
Sponsored Recommendations
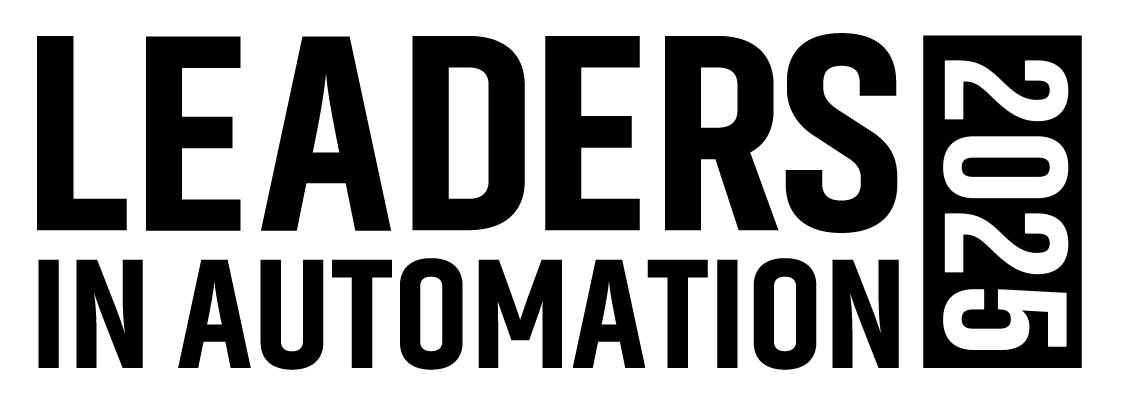
Leaders relevant to this article: