Things have been moving quickly in the realm of packaging industry safety. Take standards for instance. It was only on January 1, 2012 that ISO 13849 officially replaced the widely used EN 954 safety standard. Original equipment manufacturers (OEMs) wishing to sell their equipment in the European Union must be able to show that their equipment conforms to the new standard.
ISO 13849—or to give it its official name, EN ISO 13849-1:2008—governs safety functions in machine control systems. It is comprehensive, covering all safety-related components in all types of machines regardless of whether they are electrical, pneumatic, hydraulic or mechanical.
This holistic, cradle-to-grave standard governs all stages of the machine’s life, from design through operation to decommissioning. Like IEC 62061 and related safety standards like ANSI/PMMI B155.1-2011, which is focused specifically on the packaging industry, ISO 13849 is more a methodology than a recipe. It employs probabilistic, analytical procedures to maximize safety while minimizing proscriptive, one-size-fits-all mandates. The aim is to improve safety, of course, but with the added benefit of often improving the overall functioning of the machine or system as well.
“The process inherent in the new crop of standards—what we at Rockwell Automation are calling functional safety management—increases safety not simply when the machine is new, but across the entire lifecycle of the machine while also tending to increase productivity, says Mike Miller, FS TÜV expert, global safety market development, Rockwell Automation (www.rockwellautomation.com), Milwaukee.
John D’Silva, business development manager for safety integration at Siemens Industry Inc. (www.usa.siemens.com/industry), Alpharetta, Ga., holds similar views. “Since they are newer standards that allow the use of better technology like safety PLC’s, wireless safety, and PC-based safety, they allow the safety designs to be more cost-effective, and make the machine much safer than using hardwired logic.” He adds, “In all cases a risk assessment is mandatory for the machine manufacturers and users so that the safety standards most applicable for their specific machine and country are not overlooked.”
Risk assessment, required by the new crop of standards whether North American or European, is a standardized procedure for determining the level of risk presented by a machine or system and its components.
Rockwell Automation’s Miller confides that he has occasionally heard manufacturers grumble about the time—and thus engineering cost—involved in the process. “I say to them, how do you know your machines are safe if you don’t do a risk assessment? It’s also important from a competitive standpoint, especially if your peers are doing a risk assessment. Plus, if you want to sell globally, it’s required.”
Not only required, but useful in helping companies arrive at the most cost effective design for the needed level of safety, something that can pay dividends not only initially but throughout the life of the machine as well. How? Rockwell Automation’s Leo Petrokonis, business development manager for North America packaging industry, provides one common example. He notes that when in doubt about safety, machine builders have tended simply to add extra guarding. The operators, when they need access to the machine, frequently need to shut it down in order to remove or disable the guarding, decreasing production.
Conversely, “Operators sometimes remove or tamper with the guarding to make the machine easier to operate.” Production is maintained but safety is compromised. “Wouldn’t it be better,” Petrokonis asks, “to design it with the appropriate level of safeguards so that the operator didn’t need to remove the guarding in order to operate the machine efficiently?”
John Kowal, market development manager, packaging solutions group, B&R Industrial Automation Corp. (www.br-automation.com), Roswell, Ga., offers this telling instance of design changes, facilitated by risk assessment, improving both safety and productivity. “The most common example is control of nip rolls or similar mechanisms so that in safe operating mode, the area of the rolls that is accessible can only turn away from the point of contact, so it is not physically possible to catch a finger or tie and draw it into the pinch point.” This permits maintenance and production-related changes to take place with the power on, “making the job easier, faster and safer.”
Mean time to fail dangerous
The productivity enhancing aspects of the new approach to safety have impressed Tony Rigoni as well. Rigoni, a safety expert with Beckhoff Automation LLC (www.beckhoff.com), Burnsville, Minn., observes that “ISO 13849-1 adds another parameter to the safety mix: MTTFd (Mean Time To Fail dangerous) to calculate a Performance Level rating.”
Why is this important? “Under the previous standards, two identical parts could have the same safety rating, yet one might clearly fail before the other, causing machine downtime. By incorporating MTTFd we not only know the safety level of a product, but how it will perform.”
Machine builders, he maintains, have traditionally prioritized throughput with safety as a bit of an afterthought, albeit a necessary one. Now, however, he says that customers are increasingly asking for a greater degree of safety incorporated into their machines and he gives part of the credit for this to the new generation of standards. “Designers are starting to recognize this trend and look at safety solutions that not only safeguard their machines, but also increase productivity.”
Rigoni sees these productivity increases as largely the result of the ability of the new generation of standards to facilitate a greater degree of necessary man-machine interaction while still keeping operators safe, which in turn helps increase productivity. He adds, “It’s no longer mutually exclusive for machines to be faster and safer!”
It’s the potential functional improvements that really impress John Kowal: “When packagers find integrated safety provides them the ability to zone sections of machines or lines for maintenance or changeover without stopping the entire line, and to cycle devices such as robot arms at safely controlled speeds and torques for setup and maintenance—and when the cost and troubleshooting difficulty of hardwired versus network cable is considered—that is when specifications will change in earnest.” This he views as part of a convergence in automation technologies.
Flexibility imperative
Siemens’ D’Silva expands on that point. He notes that OEMs are being challenged to incorporate additional automation and/or motion into their machinery to address the flexibility demands of the packaging industry. “Using functional safety has helped address the complex safety issues created by this demand, by providing safe functionalities that can, for example combine automation and motion in one controller or platform and in addition ensuring the safety of machine operators.
“The biggest benefit,” he continues, “is much safer machines.” But there are others, and he lists “cost reduction brought about by faster engineering due to improved usability, and faster trouble shooting leading to less downtimes and increased productivity.”
However, it’s not all smooth sailing for the functional safety approach embodied in the new standards. Apart from bureaucratic inertia, there are real questions among the packaging engineering community about the right way to perform structured risk assessment, a process that is spelled out in two different standards, ANSI B11.0 and ISO 12100. It’s a process that is new to many. The Packaging Machinery Manufacturers Institute, (PMMI) (www.pmmi.org), has stepped in to fill the gap with a series of risk assessment seminars.
>> Click here to read a case history about how an integrated safety system solved an e-step problem.
Software packages have also been created to lead users through the process, most notably the PackSafe program from PMMI. Many users have found these programs to be just what the doctor ordered. Others are not fans. Says D’Silva: “The software based approach is generic and is typically not flexible enough for special situations or functionalities as required by the application.”
D’Silva goes on to note that unless a software is frequently updated, it may not contain the latest applicable safety standards information for the application. He says risk assessment training is “the most productive and safest direction forward.”
As mentioned above, two different standards outline the required risk assessment process. Does it make any difference which one you use? On this question the consensus among safety experts is: “Nah… not really.” Both provide the user with comprehensive guidance on conducting risk assessments and result in valuable analyses, which make packaging machines both safer and compliant.
>> What about Integrated Safety Networks? Click here for more information.
Companies in this Article
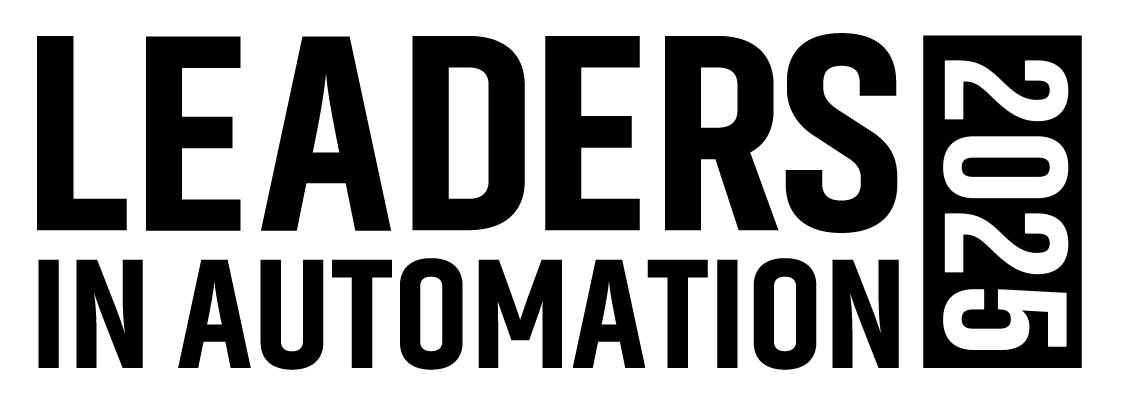
Leaders relevant to this article: