The increasing complexity of automated industrial operations makes it critical to have technologies that make it simpler to link together equipment from many suppliers. FDT, which has helped scores of equipment suppliers and integrators make these connections for years, has been upgraded to provide more benefits.
FDT, which originally stood for Field Device Technology, provides a standardized communication interface between field devices and control or monitoring systems. Over the lifecycle of a facility, it simplifies the task of configuring, operating, maintaining and diagnosing intelligent field instrumentation assets for both factory and process automation applications.
The technology, recognized by standards organizations such as IEC 62453 and ISA103, supports 17 tethered and wireless industrial communication networks. That’s prompted more than 90 equipment suppliers to implement Frame Application and device drivers, known as DTMs that support more than 5,500 devices utilized in installations globally.
The key features of FDT include its independence from any communication protocol and the software environment of the host system. FDT Technology allows any FDT enabled device to be accessed from any compliant host using any field communication protocol.
Two main components, the Frame Application and the device type managers (DTMs), are at the core of FDT. The Frame is either an embedded component of the control system suite or a standalone application. Most modern control systems support FDT Technology.
The DTM is a device‐specific application that launches within the Frame itself. Simply put, DTMs give device manufacturers complete control of the attributes displayed for their device in any host Frame Applications, thus providing the user with access to the full power and capabilities offered in their device.
Widespread Usage
KUKA Robotics and PZ Cussons are typical of the many companies that use FDT. KUKA makes industrial robots that are typically integrated into larger industrial environments where multiple fieldbuses are used. Several different busses connect the robot’s drives, peripheral devices, customer-specific devices and a handheld teaching pendant.
The KUKA FDT application saves all fieldbus-specific information generated during commissioning in a shared project. All FDT DTMs work with one another, even though they’re written by many different manufacturers. Complex bus scenarios across multiple gateways can be configured without difficulty thanks to the nested communications capability built into the FDT standard.
PZ Cussons, a large international manufacturer of soaps, shampoos and other personal hygiene products, typifies the end user benefits gained with FDT. The British company made FDT Technology a centerpiece of an extensive overhaul and modernization of its UK production facilities. That included updating most of its process equipment, which was not up to the demands of a modern manufacturing environment.
The company’s new processing and production operation was built around equipment, instruments and fieldbus networks from multiple suppliers. Integrators used FDT enabled applications in order to get the flexibility and reliability of the control system. PZ Cussons managers note that they now have process visibility and control that’s far beyond the capabilities of the older plant.
The industrial specialists at the ARC Advisory Group have repeatedly noted that astute users who adopted FDT Technology will continue to enjoy the benefits of open access to field device information in the future.
A recent report on FDT by ARC Advisory Group noted that “FDT had been associated largely with process automation and process field devices, but this is no longer the case. Suppliers in the factory automation space are now adopting FDT because they find it affords them the technical flexibility needed to deal with the wide range of product configurations their customers demand.” As noted above, KUKA Robotics is an example of such a factory automation supplier.
ARC Analyst Harry Forbes notes that “FDT Group continues to ensure that FDT Technology remains backward compatible, providing users who adopted FDT the benefits of open access to field device information in the future.”
More Benefits
Last year, the FDT Group that manages the specification completed development of FDT2™, which brings significant upgrades. The new version incorporates a host of new features including security enhancements and improved performance.
One central aspect of FDT2 is its use of Microsoft .NET technology, which enables fast and easy access to data while providing a stable platform for future enhancements. The adherence of FDT2 to backwards compatibility means users can keep all their existing software when they migrate to the latest version, making it easy for them to make enhancements at their own pace.
Let’s take a closer look at these improvements. Security has become an important issue in industrial environments. FDT2 uses two techniques to ensure that applications are stable and secure.
First, all compliant applications are digitally signed, making them indisputable and tamper proof. Additionally, there is more granular DTM security with enhanced user rights and privileges added to the security settings. Users can define who can have access to certain items, putting the level of security into the hands of the user.
The FDT Group has also incorporated a new security feature that is implemented during the certification process for compliant DTMs. Certified DTMs will contain an embedded digitally signed certificate from the FDT Group. They cannot be forged because they’re encrypted and signed by the FDT Group. The Frame Application can ensure the integrity of the DTM, giving users a high level of confidence that their installations are secure.
Performance is enhanced by using more granular data for faster data storage. Additionally, the business logic (or device model) and the graphical user interfaces have been separated so the business logic can run without starting the DTM. This allows the server to be used for other tasks such as asset management applications without showing any graphics from the DTM.
More performance improvements are gained by dividing device parameters into data blocks that can be dynamically loaded during use. One instance does not have to immediately upload the entire data record of a DTM. The DTM is initially started by accessing only the data and parameters of the DTM User Interface. Additional user interfaces are loaded only after the user calls for additional data records.
The DTM architecture has also been split into two sections to make DTMs easier to work with. The graphical user interface is one section, the other is the device model or business logic.
Separating the graphical user interface from the business logic creates a lightweight client which can be distributed throughout the facility. This distributed architecture lets users load a DTM on only one server, which can then provide access to all clients on the network. The DTM can then be automatically updated when a new version is released via the web with security provided by an authenticated signature.
FDT also makes use of a powerful data management tool. Utilizing Microsoft .NET technology enables fast and easy access to data while providing a stable platform for future enhancements. Microsoft .NET 4.0 is independent of hardware architectures and operating systems, which means future changes made by companies including Microsoft won’t impact existing installations.
A key element is the .NET common language runtime (CLR). Itis a virtual machine component that manages the execution of .NET programs and handles services including memory management, type safety and exception handling. While it brings many benefits, .NET is backwards compatible with older technology such as COM / ActiveX that are widely deployed in industrial environments.
Going forward, FDT Group and ODVA have begun developing an annex to FDT2 for ODVA’s family of CIP Networks. This annex will ensure that support for an FDT-compatible Device Type Manager is available for users of EtherNet/IP, DeviceNet, CompoNet and ControlNet.
FDT2 Products Shipping Today
The vendor community has already responded to the demand for FDT2 products as new FDT2 enabled products, both Frames and DTMs, are shipping from major vendors. With its enhancements, FDT2 is the perfect technology platform for applications in factory, process and hybrid automation. The scalability of the technology also provides security for the future, such as the integration of future FDI device packages for process control networks. End users can therefore immediately capitalize on the many enhancements FDT2 to help improve plant up time and reduce maintenance costs while using technology today that is ready for the future.
For more information, please visit www.fdtgroup.org or email Dan at [email protected].
Companies in this Article
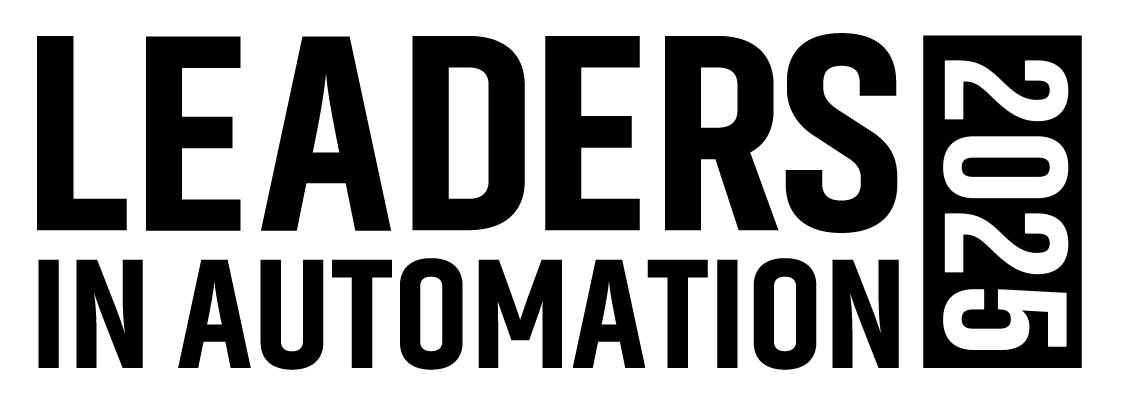
Leaders relevant to this article: