Nine strategies for achieving your energy management objectives
July 11, 2013
1. Choose the right tools. A comprehensive energy management program is quite challenging, since every aspect of a manufacturing facility is an energy consumer (processing, packaging, warehousing, utilities and even the building itself). A common mistake is to expect a traditional process or machine automation system to be pressed into service for energy management applications (EMS). Instead, purpose-built EMS systems are designed to provide the right tools for energy analysis and reporting.
2. Side benefit. Energy management programs that achieve the most significant savings are typically those whose original goal was to improve control of production processes. The energy savings achieved as a result of improved production processes often covers all or part of the cost of those improvements, which makes it easier to get management and financial support for adding energy reduction activities to automation projects.
3. Involve production, not just facilities management. Involve people responsible for production processes in energy management activities, since up to 90 percent of energy is consumed by production equipment. They will help you ensure that proper steps are taken to understand how process energy consumption can be reduced without affecting the productivity of expensive production assets. The primary reason most companies focus their energy-saving activities on the facility is that facility management personnel are often given the responsibility for reducing energy costs. Not only is the facility in their comfort zone, but it's often the only area where they have the institutional authority to make changes. By involving production, you can address all the areas of your operation that consume energy.
4. Use interns to collect data. It's fairly simple to identify viable energy management projects, but it takes real engineering to develop the business case. Use interns from local universities to collect the actual data points needed to develop a well-founded business case.
5. Avoid duplication. Many motor control devices now have network connections that pass along energy data. There's no need to duplicate these data-generating capabilities by installing power monitors over the top of intelligent motor control devices.
6. Take advantage of incentives. It can often be difficult to find the funds to invest in projects that will reduce energy consumption by your plant. Federal, state and local governments offer a range of incentive and rebate programs for energy saving projects and using alternative energy sources.
7. Be prepared. Before planning for any energy management purchase, it's important to first gather your data. It must cover the entire usage pattern of the equipment. Based on the requirements, choose the technology (hardware and software) that will help in analyzing a combination of parameters instead of a single parameter. Monitor the results and associate operational conditions with energy consumption.
8. Start with your power bill. Look for peak demand charges or power factor charges. If you have a shift come in and get the facility running from a dead stop, this can create a big grid load for a short time and lead to additional kw/hour charges due to the short period amp draw. Work with your facilities to stagger the starting of equipment and lights. When possible, use soft starts or VFDs on large horsepower motors to reduce large start-up currents. Utilize lighting vendors and not just an integrator or electrical contractor to create ROIs based on the real-world numbers you can give them from your power bill and a walk though of your facility. Although the power bill is not always correct, it is the key to cost savings as it is the perfect metric for measurement.
9. Track big consumers. Always make sure you have the means to track the energy performance of large energy consumers. The term "large" can be determined by using a simple Pareto analysis. Make a list of all of your energy users and section off the top 20 percent. This will identify a large portion of your energy usage, as well as the focus of your maintenance activities.
Five ways to manage energy costs
Reducing energy costs from production processes requires managing the five most important factors that determine both utility charges and total energy consumption:
1. Energy event management - Detection and analysis of process changes that cause consumption to exceed forecast.
2. Peak demand management - Minimizing peak demand, which triggers higher utility rates or penalties.
3. Scheduled demand management - Minimizing costs by shifting demand to lower cost time periods.
4. Idle state management - Minimizing energy draw during idle process conditions.
5. Demand/response management, - Offering energy capacity back to the grid on request in exchange for incentives.
Energy assessments and audits can help companies identify a wide range of changes they can make to help reduce their consumption. Audits can be simple, such as a walkthrough of a building or facility to identify quick-hit opportunities, or much more detailed efforts. These are not one-time projects, but rather ongoing efforts to identify variables, such as how seasons might affect production costs and whether previously implemented improvements are continuing to perform as planned.
Such assessments can help to establish the scope of an effort to reduce energy consumption, define key metrics and put resources in place that can take a holistic view of energy for the organization. Recommendations may include low-investment modifications, such as shifting maintenance operations to non-peak times, or may be more involved, such as programming changes to equipment. Evaluation and prioritization of capital improvement opportunities can also be included in the analyses.An assessment, regardless of scale or scope, should help answer the following key questions:Where am I likely to find quick returns?What key metrics should I put in place?How can I encourage ongoing improvements?
2. Side benefit. Energy management programs that achieve the most significant savings are typically those whose original goal was to improve control of production processes. The energy savings achieved as a result of improved production processes often covers all or part of the cost of those improvements, which makes it easier to get management and financial support for adding energy reduction activities to automation projects.
3. Involve production, not just facilities management. Involve people responsible for production processes in energy management activities, since up to 90 percent of energy is consumed by production equipment. They will help you ensure that proper steps are taken to understand how process energy consumption can be reduced without affecting the productivity of expensive production assets. The primary reason most companies focus their energy-saving activities on the facility is that facility management personnel are often given the responsibility for reducing energy costs. Not only is the facility in their comfort zone, but it's often the only area where they have the institutional authority to make changes. By involving production, you can address all the areas of your operation that consume energy.
4. Use interns to collect data. It's fairly simple to identify viable energy management projects, but it takes real engineering to develop the business case. Use interns from local universities to collect the actual data points needed to develop a well-founded business case.
5. Avoid duplication. Many motor control devices now have network connections that pass along energy data. There's no need to duplicate these data-generating capabilities by installing power monitors over the top of intelligent motor control devices.
6. Take advantage of incentives. It can often be difficult to find the funds to invest in projects that will reduce energy consumption by your plant. Federal, state and local governments offer a range of incentive and rebate programs for energy saving projects and using alternative energy sources.
7. Be prepared. Before planning for any energy management purchase, it's important to first gather your data. It must cover the entire usage pattern of the equipment. Based on the requirements, choose the technology (hardware and software) that will help in analyzing a combination of parameters instead of a single parameter. Monitor the results and associate operational conditions with energy consumption.
8. Start with your power bill. Look for peak demand charges or power factor charges. If you have a shift come in and get the facility running from a dead stop, this can create a big grid load for a short time and lead to additional kw/hour charges due to the short period amp draw. Work with your facilities to stagger the starting of equipment and lights. When possible, use soft starts or VFDs on large horsepower motors to reduce large start-up currents. Utilize lighting vendors and not just an integrator or electrical contractor to create ROIs based on the real-world numbers you can give them from your power bill and a walk though of your facility. Although the power bill is not always correct, it is the key to cost savings as it is the perfect metric for measurement.
9. Track big consumers. Always make sure you have the means to track the energy performance of large energy consumers. The term "large" can be determined by using a simple Pareto analysis. Make a list of all of your energy users and section off the top 20 percent. This will identify a large portion of your energy usage, as well as the focus of your maintenance activities.
Five ways to manage energy costs
Reducing energy costs from production processes requires managing the five most important factors that determine both utility charges and total energy consumption:
1. Energy event management - Detection and analysis of process changes that cause consumption to exceed forecast.
2. Peak demand management - Minimizing peak demand, which triggers higher utility rates or penalties.
3. Scheduled demand management - Minimizing costs by shifting demand to lower cost time periods.
4. Idle state management - Minimizing energy draw during idle process conditions.
5. Demand/response management, - Offering energy capacity back to the grid on request in exchange for incentives.
Energy assessments and audits can help companies identify a wide range of changes they can make to help reduce their consumption. Audits can be simple, such as a walkthrough of a building or facility to identify quick-hit opportunities, or much more detailed efforts. These are not one-time projects, but rather ongoing efforts to identify variables, such as how seasons might affect production costs and whether previously implemented improvements are continuing to perform as planned.
Such assessments can help to establish the scope of an effort to reduce energy consumption, define key metrics and put resources in place that can take a holistic view of energy for the organization. Recommendations may include low-investment modifications, such as shifting maintenance operations to non-peak times, or may be more involved, such as programming changes to equipment. Evaluation and prioritization of capital improvement opportunities can also be included in the analyses.An assessment, regardless of scale or scope, should help answer the following key questions:Where am I likely to find quick returns?What key metrics should I put in place?How can I encourage ongoing improvements?
Energy-saving incentives
For information on the energy incentive programs available in your state or region, go to http://awgo.to/021
Source: U.S. Department of Energy
Liked this article? Download the entire playbook here
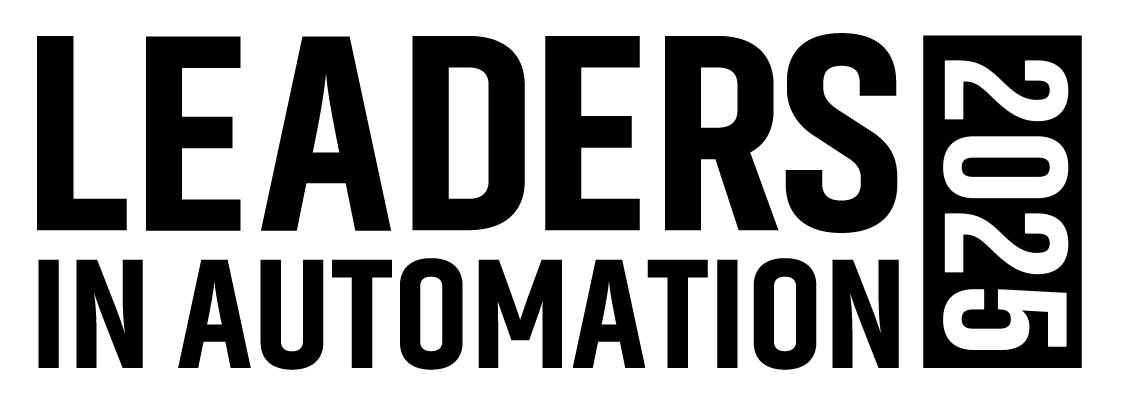
Leaders relevant to this article: