Strategic plant upgrades or optimization initiatives can come in all shapes and sizes, and vary dramatically from factory plants to process industries. Undergoing these projects, manufacturers evaluate assets and look to internal automation standards as guideposts for enterprise strategies.
For pharmaceutical or automotive manufacturers, optimization of similar applications across multiple sites often requires development of and strict adherence to internal automation standards that leverage the scale of operations. Small manufacturers or process operations, however, need flexibility with automation standards in order to accomplish immediate operational upgrades and facilitate better remote monitoring or network security.
Currently, corporate management in a variety of industries is identifying immediate real-time operational visibility into multiple manufacturing sites as a top priority. Legacy automation platforms are being evaluated and enhanced to provide that functionality.
“One call we’re getting is for middle- ware, where a company is asking for some enabling technology to help them get data out of their existing system,” says Mark Lewis, technical services group manager for Beckhoff Automation (www.beckhoff.com). Using PC-based control tools and EtherCAT industrial networks, “we can plug into their existing legacy control systems, draw the data into our system, and then push that data out to the cloud via OPC UA, with its built-in security and authentication,” he says.
For real-time production line monitoring, bigger manufacturers are also pushing data directly from the factory floor, from industrial fieldbuses into SQL databases, Microsoft SharePoint or SAP enterprise systems, which can connect to external databases.
A strong central manufacturing IT group is an asset when it comes to optimizing multi-site operations and making the best use of cloud computing, enterprise software and other technologies. It also could mean resources are more readily available to optimize individual site operations. But optimizing operations and maintaining internal standards for a multi-site control infra- structure are real challenges for smaller companies with fewer resources. They often seek help from control system vendors and system integrators.
“Legacy control consistency between sites is a major issue due to fewer central engineering groups within a company,” says Colm Gavin, product marketing manager for engineering software at Siemens Industry (www.industry.siemens.com). Gavin says Siemens’ Totally Integrated Automation (TIA) Portal, a software platform that provides one integrated engineering framework for all automation tasks, is one possible solution to this particular challenge.
Siemens TIA uses a “corporate library” concept, in which all library components are maintained on and shared via a corporate network that can be accessed by all manufacturing sites. The portal handles document and software version control, and provides a method to update and release any manufacturing system changes.
Chrysler’s internal standards
In 2009, management for Auburn Hills, Mich.-based Chrysler Group (Chrysler Group LLC, www.chrysler.com) decided that vital strategies for improving time- to-market and quality levels for its auto- mobiles required consistent internal standards and processes for its three body shop, or “body-in-white,” operations. Body-in-white plants attach body panels via a series of highly automated, assembly-line-like, robotic welding cells. At the same time, Chrysler and Italian automaker Fiat (www.fiatusa.com) began a global alliance.
The body-in-white standardization strategy looked to provide flexibility and cost reductions through the ability to build model derivatives—three or four different models—of its Compact U.S. Wide architecture much quicker. That architecture encompasses Chrysler’s Dodge Dart, Jeep Cherokee and Chrysler 200 vehicles.
“Chrysler had many different product architectures across our plants, and that drove different solutions,” says Bernie Mitchell, Chrysler Group director of manufacturing engineering for body-in-white. “In the past, different product architectures drove our manufacturing engineering teams to really engineer different solutions. So we needed to standardize for obvious reasons.”
Chrysler Group began its body shop standardization strategy with a $700 million investment at its plant in Belvidere, Ill., adding a new body shop and equipment. The second body shop was built in Toledo, Ohio, with an investment of $500 million, and $165 million was spent on equipment for a third new body shop at an assembly plant in Sterling Heights, Mich. The goal of these comprehensive upgrades was to standardize equipment, key performance indicators (KPIs) and measurement standards for all parts, components and completed car bodies.
Besides emphasizing parts standardization with suppliers, Chrysler leaned on its suppliers to develop vision-guided robots to accurately locate closures on its completed car bodies. Using measurement lasers, four robots measure the car’s body shell upon entering the station and that data is applied to set the location of the deck lid, doors, fenders and hood.
Chrysler also introduced two new technologies to its body assembly operations’ core competency: laser brazing and welding of doors.
Laser brazing shoots an intense laser light beam to melt a piece of silicon wire that robots applied to a predetermined location between the body side aperture and roof panel. This process cuts variation and eliminates the need to cover the attachment area with a secondary trim component.
“The product design department decided they wanted this aesthetically pleasing laser braze joint,” adds Mitchell. “We first applied this technology on our 300 car model, which just preceded Belvidere standardization. Building on the experience of Fiat colleagues in Europe and those at our 300 plant in Brampton, Ontario, we were able to increase our laser knowledge as we cascaded this technology through our three new body shops along with the laser welding of doors.”
Invested in quality improvements
As with some plant upgrades or optimization projects, enterprises find more improvements to make as projects develop. In Chrysler Group’s case, systematic quality improvements were driven by standardizing internal processes and metrics, and verified by its metrology centers.
Chrysler Group invested in new metrology technology as part of the body shop upgrades. The metrology centers measure incoming parts—whether they come from Chrysler’s in-house stamping team or from third-party suppliers—to ensure that they meet specifications and quality standards.
These measurement centers use blue-light laser scanners, among other technologies, to produce a three-dimensional measurement. This measurement identifies deviations and their root causes in the plant processes or incoming supplier parts starting with the early pilot builds. “We take those parts and build them up into a sub-assembly or a complete body, and the output from that process goes back to metrology and they provide feedback,” Mitchell says.
Chrysler uses Process Capability (CP) and Process Capability index (CPK) metrics to measure supplier components. CP is the stability of the process, or how repeatable the process is; and CPK measures how repeatable, accurate and close to nominal the process is.
“We saw a significant improvement in the quality of our bodies being delivered to general assembly as an output from the body shop,” says Mitchell. “It was significant, north of a 20-25 percent improvement.”
Overall, the improvements in quality have been strong and Chrysler Group has become more nimble. Before the investments, Chrysler Group’s program execution time, from program approval to launch, was more than 30 months. Now, it’s down to less than 22-24 months, says Mitchell.
Needle in a manufacturing haystack
Incremental improvements to legacy systems can have just as big an impact, so it’s important that plant managers realize that big investments are not necessary. “Many of our customers have parts of their plants that look like museums and haven’t been optimized for more than 30 years,” says Mike Burrows, director of market development for Rockwell Automation (www.rockwellautomation.com).
Rockwell found through a recent study that most manufacturers or process plant operators are still doing return-on-investment (ROI) calculations based on the engineering development costs only. “We found something like two-thirds of the ROI assessments were not total cost of ownership based,” Burrows says. “They weren’t looking at the ROI of the total investment.”
That means when considering a system upgrade they are only asking, “What are my opportunities for reducing my engineering costs?” instead of “How will this upgrade help me make and sell more?”
Recently, a multinational food industry client of Rockwell Automation’s examined its multiple packaging operations and wondered how to increase output without a massive capital investment. The challenge—and opportunity—was to find operational commonality among numerous plants.
With the help of Rockwell Automation engineers, they identified one packaging machine that was running an older SLC-500 programmable logic controller (PLC). The food manufacturer upgraded the PLC and then benchmarked the output. By upgrading the PLC on all 80 units installed across the enterprise, this multinational met its mandate to increase parts-per-minute output without large capital out-lays for new equipment.
Upgrading continuous process plants
Multiple-site legacy architectures— and opportunities for incremental improvements—also can be found in continuous process environments. “We realized about 3,000-5,000 customers of our installed base [of continuous process plants] are still running on unsupported Microsoft XP versions,” says Roy Tanner, system marketing manager for automation vendor ABB (ABB Group, www.abb.com).
Given automation technology advances, control system version updates now offer much more functionality out of the box compared with just 10 years ago. That includes the latest secure operating system, faster access to the latest security patches, and the ability to manage multiple applications by way of virtualization. This functionality can optimize multi-site operations with minimal investment.
Advances in multi-core processors, for instance, have allowed virtualization or thin-client technology to reduce the number of PCs at process monitoring sites for applications in the oil and gas and chemical industries. In a chemical plant environment, many system components can run one physical piece of hardware with a quad-core processor and five virtual PC shell machines. Applications can also be delivered from one central PC via software to other thin-client PCs that contain no hard drives, storage or operating systems. These technologies make installing and managing changes for multiple locations very easy and uniform.
As Chrysler Group showed, system upgrades offer opportunities to solve legacy challenges. In chemical plants, alarm rationalization projects are a classic way to optimize multi-site operations.
“Especially on multi-sites, operators want to have a standard across the board so they can report the status of their alarm management system within their process control system to a central control room,” Tanner says.
Centralization of alarm reporting provides visibility of KPIs and a clear way to identify alarm distractions. Alarm-reporting KPIs can include the number of alarms in a 10-minute period, the number of alarms per day that come into the system, and the priority mix of those alarms.
Allowing flexibility among sites
Optimizing operations at multiple facilities is even more difficult when your process plant is never turned off. The municipal entity Metropolitan Council Environmental Services (MCES), for example, consists of eight wastewater districts around Minneapolis/St. Paul. Management there recognizes that the challenge of optimizing and/or upgrading the control systems lies more with the process than with the actual automation technology.
“The main metro plant is the biggest by far, but they all have pretty much the same automation technology. It’s just more volume at different places,” says Roger Knuteson, process computer manager for MCES.
With plant size so significantly different for each wastewater plant, MCES chooses flexibility over strict internal automation standards for automation upgrades across all of its wastewater plants. Its strategy for success emphasizes technician training and feedback after changes.
“We use similar software at each plant, but each wastewater plant is unique, and that’s the nature of software. The specific applications are all different, so [everything] has to be tested,” Knuteson adds.
With no outside engineering resources to lean on for upgrades, MCES learns a good deal of information by prototyping. “We’re always at the mercy of the plant and continuous operations,” says Knuteson. “After we [management] test new software and hardware, I’ll let operators just play with it for a week or two—most times in parallel with an existing system—and try to find out if there are any bugs.”
MCES recently tested a Schneider Electric Wonderware workstation prototype at one wastewater plant. It uses Microsoft’s Windows 8.1 operating system and the Wonderware 2014 InTouch software running on HP 800 Mini tablet computers.
“We have eight or nine [workstations] that we’re going to replace with tablets in the control room, rather than using a regular PC, and they will be connected to a screen,” says Knuteson. “But the idea is for operators to have the tablet out in the field with them when they leave the control room.”
The overall upgrade strategy is to replace all of the Wonderware workstations with tablets, while a recent mobile information technology project uses Citrix clients on workstations and tablets to allow operators to view work orders, safety information and other business information in the field.
“The plants kind of leapfrog each other in terms of newer technology,” Knuteson says. “And when it comes to a specific plant, we make sure that all the technology at any one specific plant follows the standards of that plant.”
Despite the flexibility allowed, MCES does have some internal automation standards that it enforces for all sites. Uniform safety training is one, as is a uniform approach to network security. “It’s been a pretty big thing for us in the last two to three years, and we are continuously improving security,” Knuteson says. “The plants have adopted a defense-in-depth security strategy by way of virtual local area networks and more firewall protection.”
So whether your industrial operations are large or small, encompassing two sites or 20, plan to review and optimize systems across sites. The investment doesn’t have to be large for the benefits to multiply.
Companies in this Article
Sponsored Recommendations
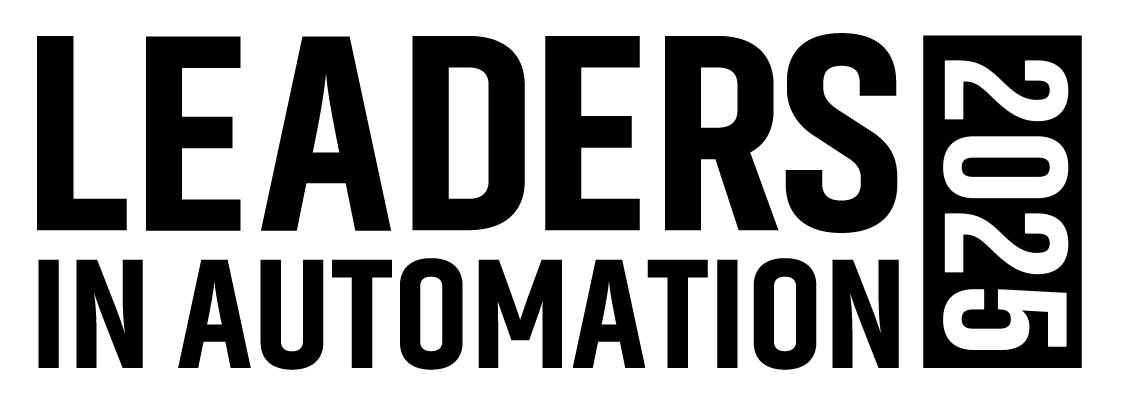
Leaders relevant to this article: