It’s a challenging time to be energy-conscious in the U.S. Sustainability and the desire to reduce energy consumption—whether for philosophical or economic reasons—has permeated the national consciousness. And, given that industrial processes are some of the most energy-intensive operations on the planet, the push to be more energy-efficient is greater in the manufacturing sector than in almost any other. As a result, nearly every new device, machine and system is touting its energy efficiency.
But how do engineers and plant managers evaluate those claims? Can they be believed?
“A lot of our customers have the same question,” says Phil Kaufman, energy technology manager for Rockwell Automation. “We’ve heard that from customers who try to bake off [compare and eliminate] a variety of competitors by including energy-saving estimates.”
A customer will say, “I like your feature set and your cost, but I don’t like your energy usage,” Kaufman explains. “But the product that consumed less energy had fewer features and less mean time between failure (MTBF)—so none was the clear winner. Features improve performance, and that consumes more energy. And that MTBF number was because the manufacturer oversized the motor.”
Unlike China, India and the European Union, which have laws about energy-efficient industrial machines, in the U.S. there is no requirement. There is also no test for industrial devices analogous to the U.S. Environmental Protection Agency’s fuel economy estimates for comparing machines based on energy efficiency. The EPA’s Energy Star label first began appearing on a few computer monitors back in 1992. Today this certification of money-saving energy efficiency and earth-saving environmental “greenness” applies only to consumer products—and adherence to it is entirely voluntary.
“We don’t have laws that mandate a certain energy efficiency, but manufacturers are seeking out energy-efficient products to get costs lower,” says Arnie Mueller, director of service for factory automation for Bosch Rexroth. “As for whether a product’s energy efficiency claims can be believed, if the product manufacturer states those efficiency numbers, you can trust them. But you also have to remember that one piece of the puzzle doesn’t solve the whole. It’s not only the cost of the machine, it’s the cost of running the machine.”
To be clear, when we talk about energy, we’re talking about electricity. Pneumatic and hydraulic systems, although energy-producing themselves, still require electricity to drive a pump. “So, even if the machine systems are hydraulic, 60 percent of the time you’re really relying on electricity, so you have to look at the whole system,” Mueller says.
Markus Tegethoff is product manager for Bosch Rexroth electro-hydraulic solutions, including Sytronix variable-speed pump drives and variable-frequency drives (VFDs). “When an industrial product vendor like Bosch Rexroth gives energy-efficiency specs for an electro-hydraulic system, we are calculating the power consumption and the efficiency of the components: the hydraulic pump and motor combinations, VFDs or servo drives, valves, cylinders, hydraulic motors, oil-coolers (chillers), etc.,” he explains. “For a customer to know what the benefit is, they have to know what their process is.”
Most electro-hydraulic systems are using energy while not doing any work, Tegethoff says. “You’ll hear the pump motor running, although the process center or actuators are not doing anything,” he says. “Our system is designed to only use energy when it is demanded in the application. Potentially, we can use a smaller motor in certain operations, where larger motors had been specified in the past.”
Says Mueller, “For an injection molding machine or a 4,000 ton press, you need a lot of energy in a small space. When I have the stroke, I need a lot of pressure. Then during the dwell, I need to maintain the pressure, but I don’t need to accelerate. On the return, I can coast. I don’t need as much power.”
An application’s cycle time might require electricity only 25 percent of the time. “You can get that variability with a servo system or VFD, but not with a pump that runs continuously,” Mueller says. Depending on the application cycles, proportions of partial load operation and the waiting/dwell times required, the energy reduction can be 10-70 percent for hydraulic systems using Bosch Rexroth components, Tegethoff adds.
Machine builder’s dilemma
Other types of machines and industrial processes can see similar savings when electricity use is monitored and optimized. But it can be up to the machine builder to explain the details. “My customers are asking for low power states when a motor is not being used,” says Rockwell Automation’s Kaufman. “But the window of time is 30 minutes and it takes 45 minutes to stabilize the heating element. You can’t go to a low power state unless your responses are fast enough. Those types of things are unseen, and it’s up to the machine builder to point that out. Use of a higher-performance component in this case is not a case of oversizing—it’s rightsizing.”
Higher-performance components can make the overall system more energy-efficient, but are usually more costly. “The OEMs are caught in the crossfire,” Mueller says. “They want to offer energy-efficient products, but end user purchasing departments are still looking at the cost of the machine, rather than the total cost of ownership.”
Every large manufacturer like Procter & Gamble, General Mills or Ford has some energy-reduction goals, and shop-floor personnel in these companies usually understand the tradeoffs. “We can talk to the plant guys and they get that this machine has an initial 10, 20 or 30 percent higher cost upfront, but it will save money over time,” Mueller says. “They’re usually the ones who have to sell the idea up to their management.”
Schneider Packaging Equipment builds a lot of customized equipment, so “for the type of OEM we are, it is very difficult to have any metric against last year’s machines,” says Pete Squires, vice president. “A lot of people in secondary packaging are similar.”
Squires says his company uses Rockwell Automation’s 5500 drive—an energy-efficient shared drive—and “we turn off all unnecessary motors. We look for efficient electrical products. We turn off conveying systems when not needed—but we had to add a couple of sensors to do that. We have discussed ways to show the savings, and have dabbled with some energy monitoring devices, but we’ve struggled with the cost of those devices.”
Where his company has been able to show savings is with installed machines, Squires says. “As a machine ages, air systems age and become less efficient,” he says. “Things start to leak and filters get dirty.”
SMC Corp., a Japanese company that specializes in pneumatic control engineering for industrial automation, has a very good program for auditing existing machines to show how much air is not being consumed, Squires says. Bosch Rexroth offers a similar auditing service for hydraulic systems.
Energy monitoring
Manufacturers can monitor a machine’s energy use themselves, either through systems embedded in a machine’s control system or by using external tools. Beckhoff Automation’s EtherCAT I/O system and TwinCAT PC-based control software integrate power monitoring into the same system used for machine control, motion control and more.
“Beckhoff manufactures four power monitoring I/O terminals that measure either three-phase or single-phase power. These terminals are in the same standard I/O format on the same rack—it’s not a separate system,” says Kurt Wadowick, I/O product specialist for Beckhoff. “One of these power monitoring terminals is an XFC terminal—XFC stands for eXtreme Fast Control—providing high-speed monitoring to collect data in between PLC scans. These devices go as low as the microsecond range to detect harmonics. This is important because more harmonics means more heat, which translates into wasted energy.”
Wadowick notes that such integrated power monitoring can be a boon for OEMs, because “non-Beckhoff three-phase power monitors generally run in the thousands of dollars range, where ours are typically a couple hundred dollars per terminal. Data processing is accomplished via a PC-based controller, providing significant cost savings.”
To monitor energy accurately, you have to be very fast in sensor and network technology. “The faster the response time, the less energy you waste,” Wadowick says. His monitoring products offer sub-millisecond response times, which are a function of the high performance and accuracy of the EtherCAT network and TwinCAT software platform.
Beckhoff’s control software also includes a condition-monitoring library, so it can analyze energy data on the fly from many types of sensors and assist with predictive maintenance decisions. In the case of a bearing vibration sensor, for example, greater harmonic distortion might indicate a bearing about to go out, which causes the motor to work harder and waste energy.
In addition, new developments in vector control of stepper motors provide servo-like response when used in conjunction with Beckhoff’s TwinCAT control software. “The amount of heat/energy required to make that motor move has been reduced because of this technology,” Wadowick says. “You’re only using just enough energy to get the job done.”
Energy in OEE
Embedded energy monitoring can provide real-time production and energy-use numbers, enabling a proactive plan for energy reduction. For example, if you find that a system used 30 kW one day and 60 kW the next, you can dig deeper to find out why.
“Gathering energy usage data at this level of granularity, and making it available across the system, all through a standard system, really sets the stage to ask and answer questions that we haven’t been able to resolve before about energy use,” Wadowick says. The Beckhoff control system uses OPC UA connectivity to deliver energy data securely to mobile devices like smartphones.
Kaufman is similarly enthusiastic about how energy use information can play a role in optimizing manufacturing. His responsibility at Rockwell is “embedding energy functionality into all business. We want energy management to be native in everything we do, life safety and security,” he says. “And we’re not talking about power quality; we’re talking about total energy used. We want to be able to visualize the intensity—how much energy per product output is being used—and also be able to visualize efficiency.”
Like others, Rockwell’s goal is to see energy use as part of overall equipment effectiveness (OEE) calculations. “Total energy is comprised of all energy used in a process: during hold periods, changeovers and launch, as well as during production,” he says. If a machine is running 60 percent efficient, but over lunch and by the end of the day with changeovers you’re only running at 40 percent efficient, you want to know that.”
If upgrading a control system to include integrated energy monitoring, analysis and feedback doesn’t seem feasible, you can always use external energy-use monitoring to create a baseline and measure progress. “If you’re going on a diet, you weigh yourself regularly. Same thing with energy use,” says Wade Thompson, power and energy specialist for Fluke. “Our tools quantify efficiency and verify the electricity you’re actually using.”
Thompson says you want to hook up power meters at several points and multiple levels throughout the plant. “You want to break apart the overall system in discrete enough chunks so you can really target where the opportunity lies for energy savings—departmental level, production line, piece of machinery, etc.”
Fluke’s 1730 Energy Logger is an easy-to-use energy monitor, with power-quality information stripped out so users can just focus on usage. The other thing Fluke energy monitors and power meters do, he says, is measure electricity in kilowatts, just like the utility does, so all the data lines up against the master bill for easy comparison.
Companies in this Article
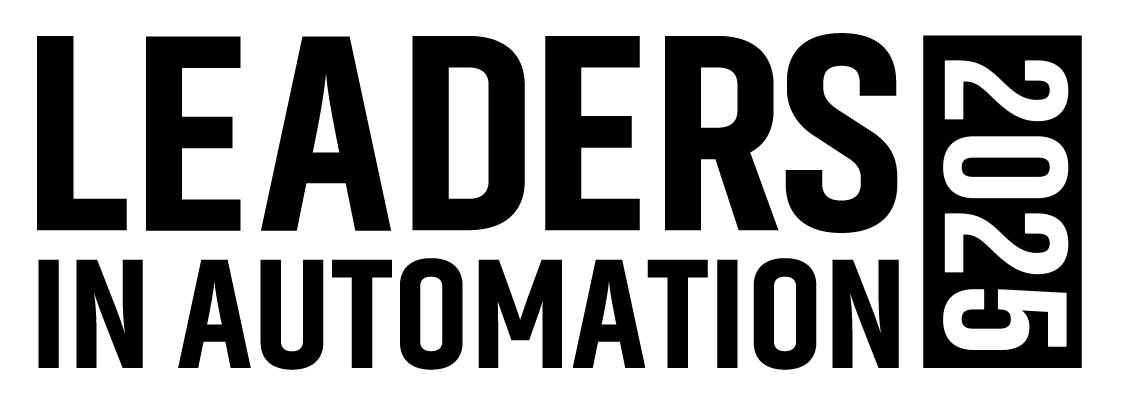
Leaders relevant to this article: