Although the Internet of Things has only more recently become a “thing,” anybody in industry well knows that manufacturing operations have been gathering reams of data for decades. But truly taking hold of the capabilities that data has to offer is what has become an ever-nearer reality as connectivity and analytics improve.
Predictive analytics and their ability to enable predictive rather than reactive maintenance is a big game changer for manufacturers. Schneider Electric has been putting a lot of emphasis on optimizing the enterprise asset performance management (APM), and its Avantis PRiSM is the latest addition to that effort, capturing all the high-fidelity process data to diagnose asset health, noted Rob McGreevy, vice president of information, asset and operations software for Schneider Electric Software.
Avantis PRiSM predictive analytics monitor the real-time health and performance of critical assets to predict equipment failure or decay points. The capabilities provided by artificial intelligence, advanced pattern recognition and sophisticated data mining can reduce maintenance costs and increase availability, reliability and capacity.
In a Tuesday morning session at the Wonderware Conference, titled, “Past, Present, Predict, Prevent” (OPS/INFO-03, Sept. 22, 10:45 a.m.), Keith Chambers, Sean Gregorson and Paul Shelton will explain how Avantis PRiSM can help you achieve greater reliability and performance from your production assets.
Avantis PRiSM can provide early warning notification and diagnosis of equipment issues days, weeks or months before failure—warnings that could go unnoticed by traditional maintenance practices.
“The value prop on this is super high,” McGreevy said, speaking to industry media and analysts during a briefing at Schneider Electric’s 2015 Wonderware Conference. “93 percent of our customers have reported equipment failures.”
In one case, for example, a utility was experiencing sporadic issues with a steam model turbine; the condition escalated and eventually resulted in the shutdown of the unit for corrective action. But upon completion of the maintenance, a similar cycle of sporadic issues began again, in addition to new problems.
Analyzing the unit’s raw historical data with Avantis PRiSM, it was clear that such a tool, had it been in place, could have provided early warning that turbine thermal expansion issues were developing and becoming chronic over the year. Through a modeling exercise, the tool was able to detect the fault patterns with early warnings six months prior to failure. The model showed that the bearing vibrations were a symptom while thermal expansion issues were the primary cause of the problem. Proactive remedial maintenance would have corrected the thermal expansion problem before it led to bearing vibration issues and the shutdown of the unit.
Not only would significant maintenance costs have been avoided, but the utility would have increased sales through increased unit availability. Estimated savings in this case are in the millions of dollars—a result of 35 days of avoided downtime and associated repair costs.
Companies in this Article
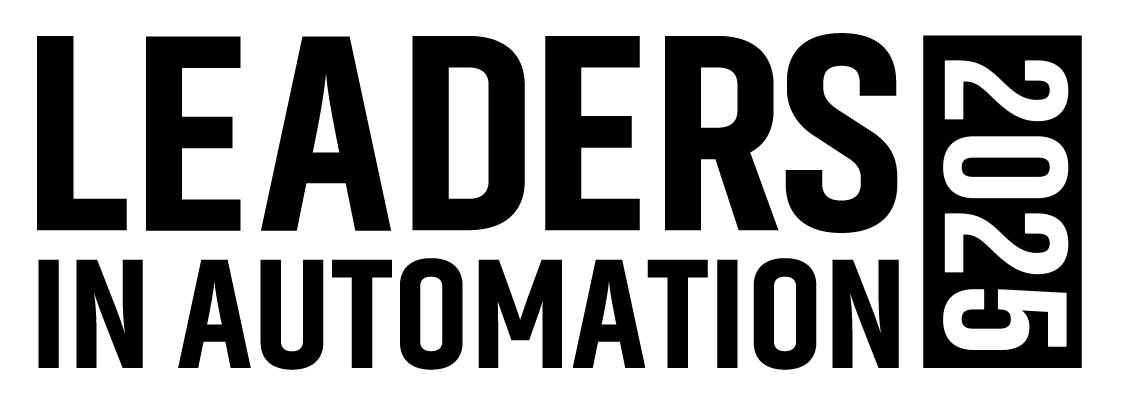
Leaders relevant to this article: