FDT/DTM Solutions Offer Great Promise for Automation Suppliers
From the outset, the FDT Group and its members worldwide have shared a common goal: open integration of control systems and instrumentation in multi-vendor environments, with the resulting benefits of freedom of choice, reduced integration costs and, most importantly, the advantages of continuous innovation.
The FDT Group’s standard unifies and empowers today’s industrial automation infrastructure: it provides an open, vendor-neutral software interface for accessing and organizing modern instrument intelligence. This includes a common environment for accessing the most sophisticated device features. The technology enables configuration, operation and maintenance through a single, standardized user interface – regardless of supplier, device type/function or communication protocol.
Growing Market Demand
FDT is well established around the world and incorporated in major international standards. More than 8,000 devices currently employ the technology, making it the most widely adopted standard for integration of assets in plant and factory automation systems for information-driven operations.
The FDT/DTM solution (i.e., FDT Technology) is well suited for the most demanding automation applications. It was specifically designed to free end users from the constraints imposed by field communication protocols, control platforms, instrument suppliers, and the manufacturing enterprise— whether it be process, factory or hybrid.
FDT Technology supports the demands of users from legacy facilities to modernized infrastructure. Recent developments enable faster execution for mega installations incorporating thousands of input/output (I/O) devices, as well as improved control system security.
With announcement of the updated FDT2 standard as the FDT Group’s “active” technology, there is an even more promising future for automation suppliers. Developed to leverage Microsoft interoperability, FDT2 supports an enhanced user interface with graphical representations of device parameters. It maintains proven FDT heritage, but includes numerous performance improvements. It provides backward compatibility with the existing installed base eliminating “rip and replace” scenarios when utilizing different eras of field equipment allowing new and existing software to coexist.
For developers of advanced industrial automation products, migration to the FDT2 solution is a forward-looking strategy with the promise of significant business benefits supporting the new era of automation.
Background for Developers
A “who’s-who” of major automation companies worldwide have adopted FDT, and with release of the FDT2 updates, a growing number of suppliers want to develop products compatible with this robust technology. Fortunately, the FDT community has several methods to help you bring products to market quickly – ranging from outsourcing to using a well-tested developer’s toolkit.
There are two major deliverables that make up the FDT standard. One is called a Device Type Manager (DTM) – this is the “device driver” for a single device or a family of devices that make it work with the FDT standard. You usually do not need to make any changes to the device itself – just supply the DTM that supports your device. Because the FDT standard has been specifically engineered to be compatible with all major industrial networking standards, there’s no need to worry about what network(s) your device is on – the DTM can be written to work with any or all of them. There are also special DTMs that support network access devices like gateways or interface devices. They are known as communication DTMs.
The second part of the FDT standard is called a Frame Application. This is any application that wishes to access intelligent devices using one or a collection of DTMs – and any other device driver available on the market (e.g., DD, EDD, FDI Device Packages). The Frame Application could be a PLC programming tool, a DCS, an asset management system, a standalone configuration tool, or just about any other type of engineering application that needs seamless access to the installed base of intelligent devices across multiple networks.
An organization interested in developing an FDT Frame Application has several options available. You can license a complete, stand-alone Frame Application that can be branded as your company’s product. There is also a consortium of firms (PACTware) where you can join as a member to obtain an FDT-enabled open source configuration platform. Many service providers offer consulting and engineering services to assist in building Frame functionality into a new or existing product. Lastly, you can directly license the FDT Group Frame Common Components to build Frame functionality into your engineering environment.
Together, a Frame and a collection of DTMs and/or other device drivers create an FDT-enabled application, which can be scaled from a small collection of devices to tens of thousands of devices controlled by a single Frame throughout the automation communication pyramid.
Employing FDT Common Components
The FDT standard enjoys more than 10 years of industry adoption and enhancements, so it supports a robust and rich set of features. The FDT specifications are all meticulously described in PDF documentation as well as in the Visual Studio environment. You will find downloads of this material on the FDT Group website if you desire more details.
When the FDT Group was preparing the latest version of its standard, our vendor community worked together to create a comprehensive toolkit known as “Common Components,” which supports all basic low-level developer requirements. This solution not only frees up the vendor’s developers to focus on unique differentiating features, it also provides a well-tested code base that speeds time to market.
FDT Common Components create a library of routines to simplify the development of compliant products. There are two parts to the Common Components: one is used for developing Frame Applications, the other is for developing DTMs. Each Common Component supports all basic features and interfaces required to be compliant with the FDT standard. This saves countless engineering hours when creating FDT-enabled solutions.
A key advantage of Common Components is that they have been extensively tested with each other through a rigorous battery of regression tests. This ensures DTM and Frame products built using the Common Components will interoperate more seamlessly when they arrive in the field.
Finally, the use of Common Components expedites testing through the certification process. FDT-enabled solutions that employ them are automatically green-lighted for a wide range of test cases that would otherwise need to be performed on an individual basis.
Streamlining Testing and Certification
The FDT standard is all about interoperability – between vendors, networks, devices, and host systems. However, many end users do not want to rely on a vendor’s implementation of the standard to guarantee that all pieces work together. That is why the FDT Group established an independent testing process, where test labs equipped with the dtmINSPECTOR tool, tests DTMs for compliance against the FDT specifications.
Using the newly released dtmINSPECTOR4 as part of a comprehensive test program will help meet market demand for FDT Technology and certified FDT2 DTMs. This testing solution enables interoperability between automation systems and field devices, providing end users with greater peace of mind.
For automation suppliers, dtmINSPECTOR4 – aligned with the Common Components toolkit – will drive the growth of FDT2-based products. The testing software tool determines the conformance of all types of DTMs, including test cases to determine compliance with the FDT specification, Common Components and Style Guide—maximizing interoperability success. Once an FDT-accredited test site determines that a DTM has “passing results,” they notify the FDT Group certification office. The DTM then receives the official electronic certification mark acknowledging specification compliance.
Besides the necessary functionalities for certification, dtmINSPECTOR4 delivers all the properties to effectively ensure DTM development compliance. The tool’s scripting engine enables developers to write their own functional test cases for a device. In doing so, the developer can create a powerful test environment providing optimal support throughout the DTM development process.
The new dtmINSPECTOR4 tool is available to all FDT Group members on a no-charge basis with only an annual maintenance fee to provide for ongoing support. Members in good standing may receive an annual license key and download information by contacting the FDT Group Business Office at [email protected].
Please visit the FDT Group website for more information about DTM certification.
Utilizing Expert Services and Support
Regardless of whether you decide to outsource or insource product development based on the legacy FDT1.2 standard, or move forward with the newer FDT2 version, several service providers offer a wide range of development services and support. Leading companies like CodeWrights, ICS GmbH, ifak system, M&M Software and Utthunga are active members of the FDT Group, who stay up-to-date on the developments and trends. Their experience and knowledge are worth tapping into.
For example, service providers offer training and workshops to teach customers everything they need to know about FDT. They can advise about system and device integration and help suppliers future-proof their device management strategy. These specialists use the latest technological developments and trends such as FDT2, linking FDI within an FDT environment, OPC UA sensor to cloud integration and mobility options for smart automation optimization. Those looking to deploy a full-blown Frame Application and/or Device DTM(s), can use their turnkey development services enabling automation suppliers to get the fastest, most reliable and standard-conformant implementation of FDT for third-party components along with their own devices. Additionally, these firms serve as official test laboratories for the FDT Group and can help customers prepare their DTMs for trouble-free certification.
The FDT Group business office can also help support your entry into developing FDT-enabled solutions. Simply email [email protected] with a description of your needs.
Conclusion
The FDT Group’s standard has been widely adopted across the automation industry for more than 10 years. Our organization, supported by the vendor and end-user communities, continues to develop, improve, and enhance FDT while maintaining backward compatibility.
The current version of the FDT standard, FDT2, has been carefully engineered to take into account lessons learned from years of practical field experience—resulting in a solution that supports modern operating environments, delivers significant new features, and is highly extensible in order to meet future requirements.
Companies seeking to develop FDT-enabled products will find a wealth of supporting consulting services, tools sets, and turnkey development resources to help optimize their R&D efforts. By leveraging this broad pool of expertise, you can realize the promise of FDT Technology!
Companies in this Article
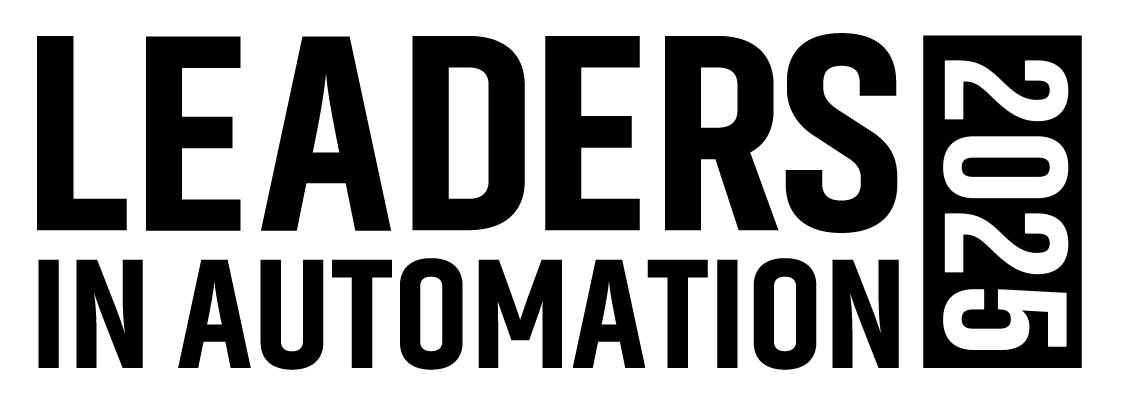
Leaders relevant to this article: