There was a time diagnosing faults, optimizing throughput, or just viewing performance data required a live person standing at the machine. With the advent of industrial networking, that changed. The technology enabled machine builders and maintenance to access wired devices, but it was a point-to-point connection, and frequently only established for situational troubleshooting. More recently, purpose-built appliances, web services, and improved remote connectivity make it possible to access, monitor, and even program equipment from anywhere. By converting data to insights, the platforms enable machine builders, integrators, and factory staff at all levels to make rapid, informed decisions to streamline operations and improve productivity.
HMIs To Go
At its most direct, remote connectivity gives industrial users the ability to monitor their worksite at a distance. One way to do this is through Web server technology. Coupled with a wireless LAN, a smart HMI can serve up screens that multiple users can access from mobile platforms. The person using the device sees exactly what would be displayed on the HMI, and they can operate the machine as though they were beside it.
The classic use case for the mobile HMI is the maintenance engineer who can check error codes for a fault from the other side of the plant. In reality, there are many other productivity-enhancing examples that take place in much closer proximity. Setting up a large machine can be a time-consuming process, forcing operators to scroll through multiple screens to change parameters and check settings. Because web-server technology leverages a one-to-many architecture, it enables multiple users to view the same connected device at the same time. That means that a team of operators, each with a tablet, could do the changeover together, each of them working on a different screen simultaneously.
Recovering from a fault frequently requires the operator to look up the error code in a manual and follow the directions to recover. Today’s smart HMIs with memory can store operating manuals as PDFs to be viewed from the screen. That’s not necessarily helpful if the jam you need to clear is 30 feet away, however. A remote HMI solution enables the operator to carry the mobile device down to the jam and have the recovery instructions at his fingertips. The result is faster resolution, reduced downtime, and less frustration for the staff.
Remote access to an HMI can enable operators to monitor equipment in a clean room from the outside, reducing the risk of contamination and making life easier for the worker. It simplifies displaying HMI information on an Andon screen on the factory floor to keep staff as a group focused on performance metrics.
These are just a few of the ways a mobile HMI can streamline operations and increase productivity. To successfully realize these benefits, a solution needs to be:
- Accessible: Multiple clients need to be able to login and view different screens on the same HMI simultaneously.
- Secure: It should not only have secure sign in, it should have multiple levels of permissions so that each person sees only what they are authorized to see. Maintenance, for example, would need the ability to change parameters and potentially reprogram the machine while an operator may only be given viewing privileges.
- Flexible: In a given factory, users might be equally as likely to view the HMI from a 52-inch flat screen monitor as from a smartphone. The mobile viewing interface needs to be reconfigurable for different form factors and dimensions.
Shop Floor Data in the Cloud
Part of the value of the industrial Internet of Things (IoT) is the ability to mine data from across the operation to generate insights to support real-time operational and business decisions. Data is only useful to the degree you can access it, however. By leveraging remote connectivity, IoT gateway appliances can make it easy to port data from networked PLCs to the cloud for outside access by asset owners, machine builders, and others.
With the use of an IoT gateway, OEMs can now have access to equipment 24/7, whether it is located in another town or across the globe. They can securely monitor machine characteristics, looking for anomalous readings that might indicate health issues and troubleshooting faults. In the case of OEMs who make most of their profits on consumables, like beverage packaging machine builders who also sell cartons, the gateway makes it easy for them to check supplies to see when the customer is ready for a refill.
Manufacturers can use the IoT gateway as an easy method to send data from the shop floor to their manufacturing execution system (MES) or business intelligence software for data analytics. At that point, they can monitor quality, track downtime, schedule maintenance, or reorder consumables. The data can also be used to build customized cloud-based dashboards for specific purposes like energy management or OEE monitoring.
The same connection can be used in reverse to send updates from the enterprise network to the machine. This can be helpful for changes in production, for example if a new order comes in that requires changes to the schedules on the floor. The use of an IoT gateway can make this happen immediately.
Making the Right Connections
Few people would argue the value of remote access and the insights it enables. The challenge is finding a way to execute it efficiently and effectively. One approach is to build a VPN over a cellular connection, but that can be complicated and expensive. It’s not just a matter of establishing robust connection but ensuring that it does not expose enterprise and factory-floor assets to outside incursion. An IoT gateway provides a secure, resilient, and more economical solution.
An IoT appliance is based on a cellular connection the cloud. Once that link is established, the gateway logs data from connected PLCs. It can be set to perform some preliminary processing before uploading the results to the cloud. The paradigm enables multiple users to simultaneously access the data, which is often presented as preconfigured charts tailored to the job role.
With remote connectivity, everyone in the food chain gets the information they need. The best person to solve the problem at hand is now available at a moment’s notice. With proper attention to architecture, permission, and security, the technology can deliver significant increases to operational equipment efficiency and overall productivity.
Previous issues of Creating Productivity
Making the factory of the future, today
Cutting Total Cost of Ownership
Meet the Tools: GOT Mobile
Mitsubishi Electric’s GOT Mobile enables operators, maintenance, and management to access a GOT2000 graphic operator terminal remotely from anywhere in the factory. The mobile viewer uses web server technology and a wireless LAN to link to the HMI. Connecting is as easy as opening up a web browser and logging in. It offers an easy way to improve functionality, reduce downtime, speed set up procedures, boost production rate, and streamline maintenance.
Up to five users can view different screens on the same GOT2000 simultaneously, and from a variety of device types: tablets, smart phones, laptops, desktop computers, and flat-panel displays. Sophisticated yet easy-to-use security and permissions settings limit user access to only the authorized screens and actions. Lockout technology prevents two users operating the same screen at the same time.
GOT Mobile is compatible with Apple and PC technology; supported browsers include Google Chrome and Safari. The GOT screen design software, GT Works3, enables the display to be easily reconfigured for different sizes and form factors. In addition the screens from multiple GOT2000s each devise can be displayed on a single user PC or flat-panel screen.
Meet the Tools: e-F@ctory IoT Gateway
Targeted at energy management applications, the Mitsubishi Electric e-F@ctory IoT Gateway provides an easy, secure method for linking factory assets with the cloud. Macro-processing capabilities streamline converting the data into useful information before transmitting it to the cloud. Once there, it’s repackaged into customizable dashboards that highlight key performance indicators. Rapid access to usage data enables OEMs, maintenance, and facilities managers to easily identify and target waste, faulty equipment, and opportunities for savings across a facility or an entire operation.
The IoT Gateway maintains the security of factory and network assets by using separate ports for the local-area factory network and the connection to the cloud. Customizable security policies can be set to assign access and levels of authorization for each user and job role.
The platform is scalable and includes 1 GB of data storage The graphical configuration tool eliminates the need for custom programming and simplifies the process of connecting to equipment and SCADA systems from different suppliers. Preinstalled driver options make the device compatible with automation products from vendors like Honeywell, Rockwell Automation, Schneider Electric, Siemens, and more.
Inside the Solution: Remote Access Through Secomea
With the use of a VPN router, remote connectivity can also enable an off-site engineer to access equipment as though they were in the factory. e-F@ctory Alliance member Secomea uses a three-part system consisting of the GateManager, the SiteManager, and the LinkManager. The GateManager is the hub and control structure of the architecture. It can be located in the cloud or on a server at the customer site. The system administrator uses the hub to create accounts for remote users, defining access and establishing permissions. The latter quality is key. “With the administrator portal, you can configure very detailed and fine grained which user has access to which PLC at the other end¾you can give access to certain factories or devices, or you can give access to only certain services on a device,” says Peter Koldig Hansen, CTO of Secomea. “The solution has to be able to act as a broker for this multidimensional communication relationship in order to fully comply with the standards of the fourth industrial revolution, referred to as Industry 4.0. It should be fully controlled and managed centrally. That is becoming more and more critical.”
On the factory side, the SiteManager facilitates data capture from IIoT smart components while also allowing full tunneling access for corrective service. The SiteManager connects securely to the central GateManager via wired connection or 3G/LTE cellular network.
When an engineer is cleared for remote access, the GateManager sends a link to download the client software, LinkManager. The engineer then uses LinkManager to connect to the device of interest. At this point, they are connected to the machine in the same way it would be if they were physically present in the factory. They can start troubleshooting and use analysis programs in the very same way.
When customer assets are involved, secure connectivity is essential. At the same time, the product needed to be easy-to-use for automation suppliers focused more on motors and gear ratios than encryption. "A large part of security in this context is actually the ability of the solution to prevent breaches caused by user neglect or misuse or lack of knowledge, misconfiguration,” says Hansen. “It has to be easy to work properly, and if you work it properly, it is secure.”
Inside the Solution: Remote Access Through eWON
Connectivity can bring big benefits but customers need to look for the right attributes, says Dominique Blanc, general manager of e-F@ctory Alliance member eWON. “You need to find something that works but also something that can be deployed on hundreds and thousands of machines,” he says. “You will have a machine for 10 or 15 years at least. You need a solution that can evolve to do something that might not be important today but will be tomorrow.”
eWON delivers remote access and monitoring using a cloud-based connectivity hub called Talk2M. Customers use an industrial VPN router to collect local data at the facility. Engineers needing to access equipment remotely leverage a web-based interface. They configure the portal to authorize access with varying levels of permission. Using M2Web, the web based interface, engineers can interact with their HMIs and view their data. The data can also be transmitted securely over the VPN tunnel to the service center or data center of the customer’s choice for data analysis and reporting.
Security is essential – equipment needs to provide a layer of protection between the plant network and general Internet access. “we use encrypted connectivity andOpen VPN to ensure that the connectivity will be a secure channel,” says Blanc. “You need to make sure that the remote person can only reach what’s connected behind our devices, which means that they don’t have access to the rest of the customer network.”
Another important consideration is to look for routers with local buffers so that data is not lost in the event of conductivity problems. “Next time communication becomes available, [the router] will be able to push the backlog and be able to continue,” says Blanc. “Engineers are very concerned about losing data. The buffer is very useful.”
Sponsored Recommendations
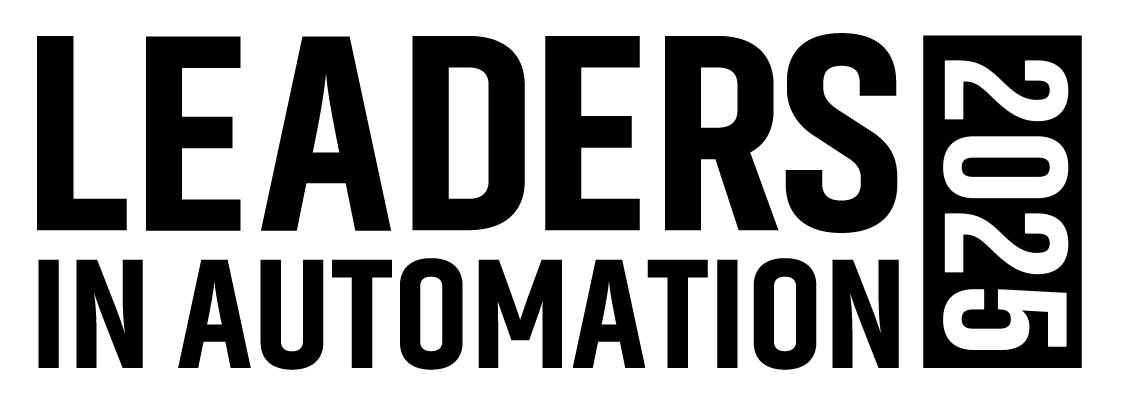
Leaders relevant to this article: