Interested in maximizing productivity? Look no further than predictive maintenance. Predictive maintenance applies failure prediction techniques to detect equipment issues that could cause unscheduled downtime. By identifying problems early, organizations can strategically plan maintenance and increase uptime. The result is higher throughput, improved quality, and reduced cost of ownership. This is not a description of some future technology predictive maintenance can be enabled within drives, sensors, and encoders today. In fact, it may be embedded in components you already own or use. All you have to do is take advantage of it.
Manufacturing is challenging
Despite the booming economy, manufacturing remains challenging, both for producers and the OEMs who serve them. Consumers demand high performance and customization at a rock-bottom price. In response, manufacturers seek to maximize the throughput and availability of their equipment, as well as its ability to produce quality product. These factors can be monitored using a metric known as operational equipment effectiveness (OEE). Minimizing downtime is a core tenet of OEE and is part of an overall drive to produce overall cost of operations. Manufacturers look to OEMs and machine builders to deliver.
The role of OEMs has always been to build equipment that performs and that addresses customer pain points. To improve OEE, machine builders need to find a way to increase uptime without also increasing the cost of the equipment and support. The latter is an important issue. In the aftermath of the economic downturn, manufacturers have stripped down their engineering departments. Rather than maintaining large maintenance staffs, they work with small teams and depend upon their machine builders and integrators to fill in the gaps. Although OEMs will happily take on maintenance and support duties, it can be challenging and expensive to be responsible for large numbers of machines deployed at a distance. Predictive maintenance provides a good solution for end-users and machine builders, alike.
Inside predictive maintenance
Preventative maintenance has been the go-to approach for organizations seeking to maintain uptime in their equipment. The problem is that it is based on usage models that may not necessarily reflect actual operations. It also assumes proper execution of maintenance tasks, which is by no means a given. Preventive maintenance is based on what should be happening. Predictive maintenance is based on what is actually happening.
Preventative maintenance involves predicting failure by analyzing changes in key metrics like friction, vibration, and positioning error. Sudden changes in any of these characteristics can provide advance warning of issues such as bearing defects, lubrication breakdown, guide wear, etc.
It is particularly important to apply predictive maintenance to critical assets that are the chokepoints of an entire process. If the motor on a depalletizing conveyor fails, for example, it may shut down the entire operation. A cloud-based predictive maintenance solution can send alerts to the on-site maintenance department and the OEM, enabling them to immediately assess the data and determine an appropriate response. In some cases, the issue can be solved by downloading a software patch or updating firmware. In other cases, the OEM support member may still need to travel to the customer, but this time they have all the relevant data at their fingertips and can rule out common issues even before leaving the office.
Predictive maintenance has potential to radically change the OEM business model. It becomes easier to support service-level agreements. They can use data to potentially track whether the equipment is being operated appropriately or whether the user has violated specifications or warranty conditions. The data captured on deployed machines can provide insights for the design of future platforms.
The truth about predictive maintenance
Given the benefits for both end-user and OEM, predictive maintenance should be commonly deployed. Certain forward-looking sectors like semiconductor fabrication and automotive have been implementing predictive maintenance for years. For the most part, however, adoption has been slow, based in large part on misconceptions:
One misconception is that predictive maintenance is complicated. In the current market, many machine builders are running flat out. They may have so many orders that they feel they don’t have time to build more versions of their current platforms, let alone revise them to include new technologies. The truth is that they don’t have to. With today’s smart components, they may be able to implement predictive maintenance with the equipment they already use. In certain Mitsubishi MR-J4 drives, for example, predictive maintenance functionality is built in (see sidebar). The drives only require simple configuration to properly activate and deploy. Application parameters can be changed through the user interface or HMI to enable this useful feature. There is no need for additional sensors, software, or analysis.
Figure 1: Another misconception is that the technology is expensive. Budget is always a concern in the industrial environment. Machine builders don’t want to increase cost or pricing. Built-in functionality means that the technology is available without any additional investment. This is an important attribute. It enables OEMs to:
• add value to their machines without increasing cost or price
• increase features for customers on machines those customers already own
• save money by reducing support costs on new machines and those already in the field
The benefits of predictive maintenance for end-users and OEMs are undeniable. Smart drives with built-in predictive maintenance functionality deliver those benefits with no increase in cost or complexity. These drives equip OEMs to add predictive maintenance to new machines without changing their BOM. They can give customers predictive maintenance capabilities with no additional cost. Given that, we predict that broad deployment is ready to happen.
Product Spotlight: MELSERVO-J4 features built-in failure prediction
For companies wishing to try out predictive maintenance, of the MELSERVO MR-J4-GF(-RJ) servo drive provides an ideal entry point. The MELSERVO MR-J4-GF(-RJ) offers full AC Servo drive functionality with an important additional feature: comprehensive built-in failure prediction capabilities. This 24/7 monitoring functionality enables asset owners and end-users to detect equipment problems well before they progress enough to cause unscheduled downtime. The maintenance team can diagnose the problem early and schedule repairs at the time that least impacts throughput. The failure prediction function delivers reliable protection in an easy to implement solution that requires no additional investment by OEM or owner.
The MELSERVO MR-J4-GF(-RJ) provides information on machine condition without any need for additional sensors. It applies sophisticated algorithms to standard drive data such as positioning error and torque increase. Capabilities include:
• Friction failure prediction function: The drive predicts failure that would be caused by changes in the coulomb and viscous friction of the guides and ballscrews
• Vibration failure prediction function: The drive models changes to magnitude and frequency of the vibration spectrum, using it to predict failure based on aging in guides, ballscrews, and belts.
• Total distance failure prediction: In the drive applies data on lifetime travel distance of the servo motor to identify when ball screws and bearings are approaching end of product life.
Figure 2: MELSERVO MR-J4-GF(-RJ) drives analyze standard torque and feedback data to diagnose issues that could lead to premature failure and unscheduled downtime.
The drive can send alerts to the graphical operator terminal (GOT) or HMI. Depending on the implementation, it can be used as part of a cloud-enabled predictive-maintenance system that allows the OEM to monitor alerts and access current and historical machine performance data to determine root cause.
The MELSERVO MR-J4-GF(-RJ) also incorporates auto tuning capabilities. These functions allow the drive to automatically compensate for the detected errors to maintain optimal performance until such a time as maintenance addresses the true issue.
The failure prediction function is available on MELSERVO MR-J4-GF(-RJ) servo amplifiers with software version A3 or later.
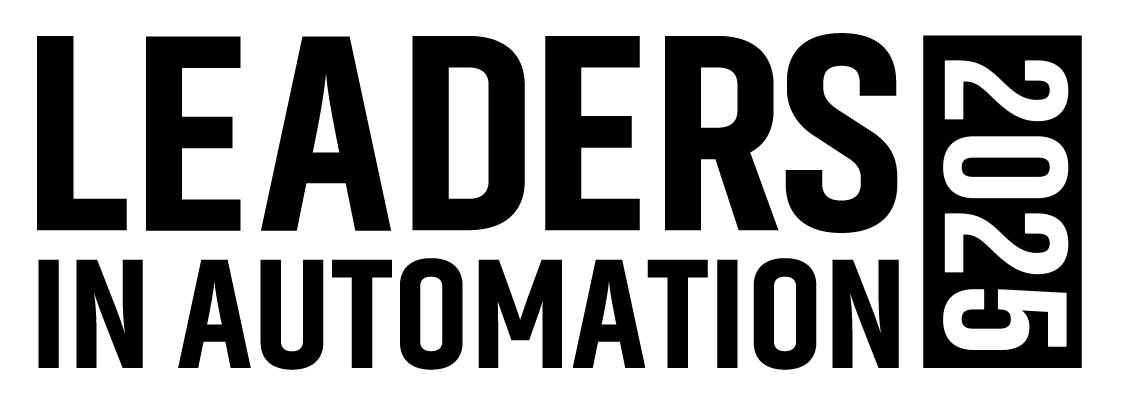
Leaders relevant to this article: