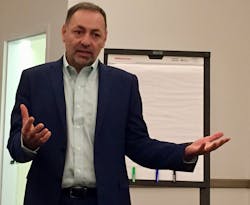
Technology-enabled collaboration has been one of the long-promised but seldom delivered benefits of enterprise-level software. Among the primary reasons why collaboration has been so difficult to deliver are cultural issues and support from senior management. An equally important factor is the lack of connection between functions across the value chain.
Connecting these dots is what AVEVA is focusing on with its Value Chain Optimization solution.
During a presentation at the AVEVA World Conference in Orlando this week, Harpreet Gulati, Senior Vice President of Planning & Operations at AVEVA, noted that AVEVA is the only software company delivering end-to-end value chain integration and collaboration capabilities.
AVEVA Value Chain Optimization is delivered across industry verticals in packaged software stacks featuring industry-specific templates so that users can apply the best practices relevant to their vertical. “We differ from other technology suppliers in the market in that we connect multiple tools—from production planning and monitoring and control to corporate and investment planning—to link operations analytics, targets, and plans to actual operations data, fiscal targets, and strategic decisions,” Gulati said. “We condense these functions into a unified value chain for one version of truth contained in one database with hooks between business and operations modules as well as external systems. We’re doing the same thing SAP did for the financial industry by connecting and integrating operations that were historically separate.”
Connection of value chain activities for collaboration is critical because “everyone in the plant is trying to maximize what they do with their own tools, while management wants to look across it all,” said Gulati. “As a result, the business workflow view doesn’t match reality because legacy point solutions require manual data transfer as well as custom codes and support. Value Chain Optimization is designed to reduce these siloes. By connecting the entire value chain, we can enable collaboration across functions both upstream and downstream.
Gulati noted that AVEVA Value Chain Optimization also extends to its mobile solutions. This connection to workers in the field advances digital workflow management and includes automated procedure triggering to accelerate process improvements. Detailed analysis and reporting connect the mobile-enabled field worker’s input into the entire value chain. Custom apps can also be created to streamline mobile workers’ actions with required workflows.
Another unique aspect of AVEVA Value Chain Optimization is its Enterprise Knowledge Management feature—a database where specific points of knowledge can be stored and searched. Gulati explained that user insights are added to the database whenever a user adds an alert or note in the software. As other users interact with these applications, alerts—driven by these previously entered notes—are sent to users based on relevance to their job duties.
“Throughout the connected value chain today, there are still many manual processes,” said Gulati. “Realizing this, we asked: Why can’t we learn from past experiences to make recommendations to the user? That’s what we’ve enabled with this Enterprise Knowledge Management database. And we’re managing its application with artificial intelligence and machine learning to continuously improve its application. No one else in the market is building artificial intelligence into the context of decision making.”
“ADNOC estimates that it saved between $60 and $100 million in optimizations from a single run of AVEVA’s software here,” said Gulati. “This was value leaking from the company that had not been realized before,” he said.
Companies in this Article
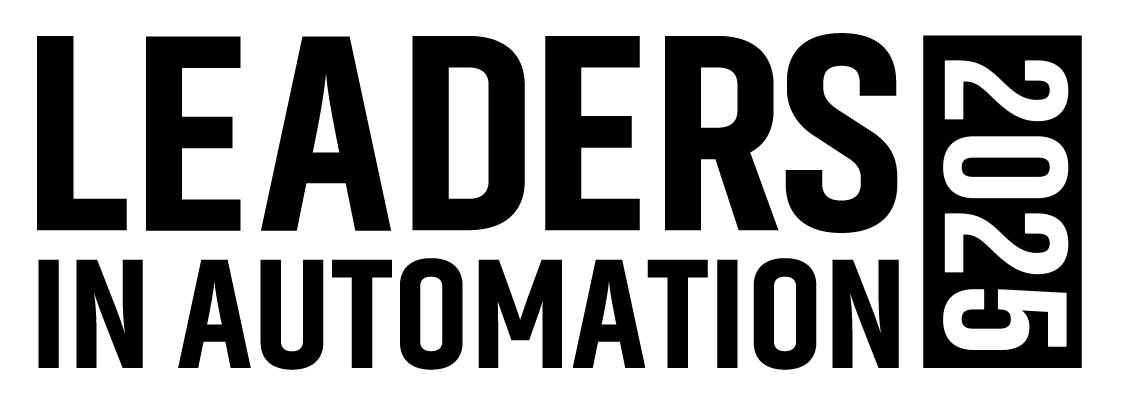
Leaders relevant to this article: