Over the last few decades, the progression of industrial robotic technologies has continued to advance at a rapid rate—even long after the robot boom of the 1980s in the automotive industry. Now, many robotic industry players view autonomous mobile robots (AMRs) as the next big movement in industry to address labor shortages, the growing demand for customized order fulfillment, and increasingly dynamic production environments that are pushing manufacturers to employ ever-leaner, more agile technologies.
Most robot industry insiders see AMRs as a replacement for the lengthy conveyor belt lines and automated guided vehicles (AGVs) used to automate material handling tasks in the past. AMRs are seen as a good replacement for AGVs because they do not require permanent wire strips or magnetic tracks along the floor to guide their path. Instead, AMRs navigate through the use of light detection and ranging (LIDAR) technology, and on-board intelligence and collision-detection safety systems that allow for the real-time selection of the most appropriate route to any given destination at a particular moment in time.
The benefits of AMRs aren’t difficult to imagine. For one, the lack of infrastructure required to deploy AMRs reduces upfront costs, allowing for a much faster return on investment. Beyond that, the flexibility of being off a fixed track can maximize the use of space in a large plant, and help meet the changing needs of an increasingly adaptive manufacturing landscape.
“Manufacturing has really changed, and as the need for adaptive manufacturing has become higher and higher, real estate has become more and more expensive, so plant floor space is now a valuable commodity,” says Ed Mullen, vice president of sales—America for Mobile Industrial Robots (MiR). “Being able to shrink everything down and make changes on the fly is really going to start paying dividends, and AMRs allow for that.”
Melonee Wise, CEO of Fetch Robotics, a company that offers Robots-as-a-Service (RaaS), concurred, noting that, aside from the cost savings AMRs entail, the changing demands of industry itself will increasingly require them.
“If you look at the environments that they’ve [AMRs] been deployed in for manufacturing, especially in the realm of consumer electronics, the flexibility is really key. They change their work cell configuration and their line plan delivery configuration sometimes every several months or even weeks,” Wise said. “Having the ability to completely change the routes that the [AMR] fleet is moving along quickly is going to be a big win.”
Spurring Broader Adoption
As clear as the benefits may be for AMRs, manufacturing remains a risk-averse industry. While adopting new technologies is required to maintain a competitive advantage, doing so too soon can lead to unexpected losses, says Matthew Rendall, CEO of Otto Motors. This is major reason why the proliferation of AMRs has proceeded slowly to date. However, Rendall and others feel that the market is finally beginning to shake-out its kinks, and a proverbial tipping point is just around the bend.
In particular, the shift toward multi-modal functionality has strengthened the value proposition of AMRs. Take for example Staübli’s HelMo robot, which features a robotic arm mounted on top of an autonomous mobile cart. In the past, an autonomous mobile cart may have offered tremendous time savings just by moving materials throughout a plant. But the picking, loading, and unloading tasks still had to be carried out by humans. With the addition of a robotic arm, HelMo represents an autonomous mobile asset with multiple uses, and thus a stronger case for investment.
“What we see from time to time is that people have a hard time justifying the use of a robot for a single purpose,” says Sebastien Schmitt, robotics division manager of Staübli North America. “With more robotics coming into play, you no longer have the problem of getting parts loaded from the station to your cart or unloaded from your cart to your station, and AMRs have truly come into their own as a product.”
MiR is also looking to capitalize on the prospect of a flexible AMR capable of performing various functions to help justify its upfront costs, but its approach differs from Staübli. Rather than offering a general-purpose robot like HelMo, MiR favors a modular approach, whereby their various AMR offerings act as blank slates that other pieces of hardware can be integrated with.
“We’re really targeting verticals in manufacturing because that’s where our low-hanging fruit is, but we’re [also] opening up our product to many different industries, including hospitals, airports, and logistics. That’s why we’re starting to see an eco-system of third-party companies looking to build various accessories for the tops of our vehicles,” Mullen says. “So, instead of being a company that says: ‘Here is a solution, make it work for your application’; we say: ‘Here’s a tool, and let’s develop the right solution for your application.’”
Perhaps the most compelling business model for the evolving AMR space is robotics-as-a-service (RaaS), which allows companies to contract third-party robots that can be rapidly deployed for a temporary period of time, while also attaining product expertise to assist those who may be unfamiliar with the technology. (See the November 2019 Automation World feature article “Robots at Your Service”: http://awgo.to/raas).
Fetch Robotics’ Wise, along with Lior Elazary, CEO and co-founder of inVia Robotics, another RaaS provider, both contend that the unique RaaS model, largely enabled by cloud computing, can ease the learning curve for companies poorly versed in robotics and provide a quicker, more discernible return on investment.
inVia, for its part, drives this point home by employing a billing model that charges per item moved, rather than per robot, an economic choice that places the onus on inVia to move products more efficiently, rather than merely deploying more robots.
“In the past, if you look at some robotics companies, they’ve sold a bunch of robots, which was great for them, but at some point their sales flat-lined because the customers didn’t really know how to best utilize the robots,” Elazary says. “[Our model] gives them great cost certainty, as well as the reliability that if they need half a million units moved, we can support that.”
Yet, according to Elazary, an even greater benefit offered by RaaS is that it opens up the AMR market to small- and medium-sized businesses by removing risk, reducing upfront capex costs, and allowing for rapid scalability.
“If you look at Amazon, they had to pay the ultimate price. They actually bought an entire robotics company—Kiva Systems—for $700 million. Most of our customers, even at the highest enterprise level, can’t afford to do that,” he says. “What we’re allowing them to do is basically have that throughput now and see almost immediate ROI without having to project so many years into the future.”
The Importance of Software
Elazary, Wise, Schmitt, and Mullen all contend that the most promising developments in the AMR space will be found in the domain of software, rather than hardware, with cloud computing, machine learning, and more sophisticated fleet management solutions all taking center-stage as the market heats up.
“I think it’s important to realize that the warehouse is actually the wild west, whether it’s a manufacturing or distribution facility. There is a lot of complexity and difficulty there, and this is not a solved problem. If you look at the algorithms and the machine learning that we do today, it’s pretty sophisticated,” she says. “That’s really enabled by the cloud, and if you’re not in the cloud, you’re going to miss a lot of that opportunity.”
To surmount the robotics skills gap, several companies, such as Omron, have designed AMR software that can create an internal map of an environment by being driven around with a joystick. According to Darrell Paul, market manager for robotics and motion at Omron, the process is no more difficult than playing a video game. Once an initial tour of a plant floor is complete, Omron’s fleet management software can designate zones within the space where different rules are applied, such as speed limits, stopping at intersections, or only moving in one direction down certain corridors.
Elsewhere, startup companies such as California-based Formant are offering the promise of a general-purpose fleet management platform that can integrate many different types of AMRs into a single system.
Labor Concerns and The Reality of Automation
While the accelerating pace of development in the robotics space may excite engineers and technologists, some fear that the growing prevalence of automation could pave the way to the displacement of human workers by machines. In reality, many of the jobs that AMRs are performing are not being adequately addressed with human labor. In fact, according to Wise, one of Fetch’s largest clients—a large automotive facility—typically sees between 30-40 of its 160 workers absent from any given shift. As a result, robots are increasingly viewed as critical components of production uptime.
Moreover, as robots move into the workplace, humans in the facility will be able to focus on more fulfilling, value-added tasks.
“We’re working now in a small manufacturing community in Wisconsin, and we were very successful retraining everyone to work with our Ottos. The maintenance personnel and the electricians all used to work with PLCs and conveyors, and after going through our retraining program, they’ve leveled up their career and are now one of the first groups in the region to be skilled in AMR maintenance,” Rendall says. “That’s a really marketable skill, and I think it’s going to do well for them in the foreseeable future.”
For all the material progress that’s been made in the past century, the sad truth of early industrialization is that it made man the slave of the machine, chained to immovable production lines and conveyors that trudged forward with a steady, unrelenting rhythm. Now, the emergence of AMRs and other advanced robotics is unshackling the labor force from the static production methods of the past and helping put people back at the helm of operations.
Companies in this Article
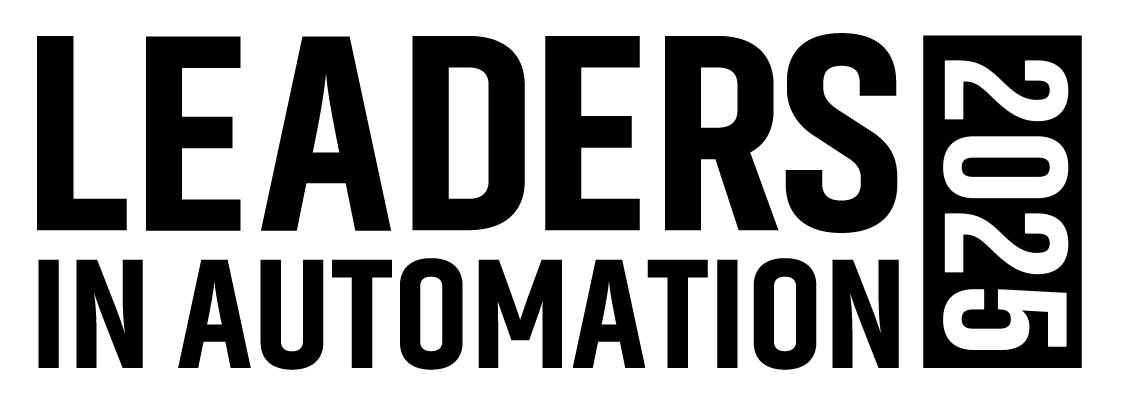
Leaders relevant to this article: