Roche Diagnostics has adopted a dedicated resource approach. John Dzelme, CPIM, applications specialist, is a computer systems analyst who uses a Manufacturing Execution System (MES) to drive improvement. “Operational excellence need not be subjective,” he says. “You can claim operational excellence when you achieve such a high level of success that other peers are willing to tag your work as a best practice or benchmark. Toyota is a standout in this regard—and note that while they’re number one in consistent quality, they state categorically that they need to improve more.” Given Dzelme’s reference to Toyota, it is not surprising that Roche pursues Lean Manufacturing approaches. “We are firm advocates of continuous improvement,” he says. “We have gained huge returns on investment in the Toyota system along a number of fronts.” In addition to general process improvements, these include medical device manufacturing compliance initiatives, product mix decisions, and controls and process validations – every action, machine, and measure in medical manufacturing has to be standardized in ways acceptable to the FDA. “We work from the business strategy on down,” Dzelme says. “If you implement solutions that don’t parallel overall business plans, you jeopardize losing direction or funding from stakeholders, or find yourself with a solution that just doesn’t add value to the organization.” Roche applies rigorous systems analysis, familiar to those who build large software applications. “Our approach is as holistic as possible,” Dzelme explains. “We look at business strategies and directions, regulatory aspects, data collection and management strategies, and end-user adoption. You have to make life easier for the end-user, or you’ll face rejection.” This systems approach enabled Dzelme to work with its MES provider to create functionality within the system. Roche uses a system from Camstar, Charlotte, N.C., and Roche’s first line of attack after installation was to reduce the cost of compliance. “We had a robust quality management system, because everything out the door has to be 100 percent in compliance with specifications. But it was manual, and the 170-plus pieces of paper that went into batch records were a burden. MES data collection can record steps as they happen, and in fact, enforces specifications, because things must be signed off before products are released to the next stage. Because of this, we’ve dropped to 12 records per batch that take less than half an hour, compared to more than two hours for the previous manual system. Plus, the savings are cumulative. We’ve cut more than four days from the overall batch release time, and we’re now working to eliminate even these 12 records.” “Camstar helped us with our initial implementation about two years ago,” Dzelme says, “Since then, our teams have designed, built and implemented a range of enhancements to the MES to support continuous improvement efforts. Our Roche MES development team is currently working on extremely promising projects for machine integration, packaging, compounding, Kanban queuing and scheduling. The objective for all is yield improvement.” Creating visionaries Dzelme works with changing teams for projects, drawing from what he calls visionaries and sponsors, both drawn from a growing list of candidates that he has amassed. Visionaries are personnel that demonstrate a strong grasp of business strategy and how it relates to manufacturing activity. “More specifically, visionaries help us see where we need to be in five years and are willing to explore avenues for reaching that destination,” Dzelme says. Sponsors tend to be high-energy players who have a firm grasp on the benefits of improvement initiatives. They are willing to help drive events or to evangelize, creating a steadily-growing climate of continuous improvement. “I’m always interested in people who step back and look for answers that are broader than the fix of the moment,” Dzelme explains. “We want people who won’t put up with a failed quality check, who know that if you monitor processes, get into the details, and step in when key indicators first begin to move out of line, quick corrective action is possible.” One common theme runs through initiatives managed by Dzelme’s teams: they all involve the end-user, whether that is the business manager or an operator on the line. “People dislike being force fed,” he says. “But if you let them plan the menu and do some of the cooking, they’ll build an appetite. Besides, who knows better about an issue than those who live and breathe it day in and day out?” In all of this, Dzelme says, “you have to accept the fact that some people just don’t get it. The good ones can be moved to operations that have already been standardized, where things are relatively static and mature. Nay-sayers, people who interfere with the ability of others to understand best practices, need to be removed. Visionaries are prime candidates for new efforts or new product lines or processes.” Dzelme has hammered out three rules for program success. First, when you initially bring technology to bear on a given operational detail, take a long look at the process. If you have many steps, determine whether the activity is actually complex, or whether the steps have proliferated simply because the process is manual. Simply automating the manual steps may bring no benefit. Second, when selecting technology, dig into vendors’ experience in your industry, and opt for a supplier that can show you relatively short initial projects with appreciable returns—and a product architecture that supports modular installation and development. “You gain sponsorship when you show an immediate benefit,” Dzelme says. Finally, ensure that the architects of the new systems are providing solutions that align with overall business needs. “It’s better to be open-minded about what good architects are telling you,” Dzelme says. “We pushed ahead with modifications at the beginning, over the recommendations of Camstar—and from this, we’ve learned that we were not the MES experts. A couple of our current projects are focused on undoing what we did then.”
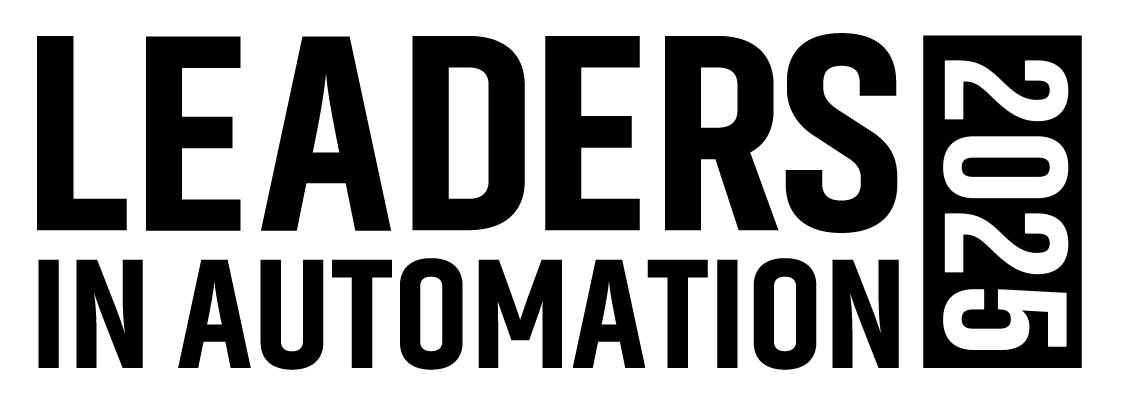
Leaders relevant to this article: