A solid argument could be made that packaging equipment should not only be the first factory floor systems on the manufacturing network, but also the first to be linked to the enterprise network as well. Packaging operations, after all, could be a fairly effective indicator of a manufacturer’s end-stage operations. Packaging data, of course, can tell you how much good product is coming off the line. More importantly, these data can offer a window to trends to be avoided, such as growth in finished goods inventories—and to trends of joy, such as on-time availability of product urgently wanted by customers. Possible also are insights into quality assurance and traceability. Finally, networked packaging allows you to extend methodologies used for productivity improvement and capital efficiency in other parts of the factory to the packaging line as well. Unfortunately, however, the results of one recent survey indicate that many manufacturers are out of touch with these benefits, in more ways than one. The OMAC Users Group Packaging Workgroup’s Packaging Automation Survey indicates that more than 60 percent of end-of-line equipment is not networked. The OMAC (Open Modular Architecture Control) Users Group and Packaging World put together the survey, the results of which were announced this year. OMAC describes itself as dedicated to the development and use of open, interoperable control and automation systems for end-users, technology providers and original equipment manufacturers (OEMs).End-users are the primary source of input for requirements, and OMAC’s end-user community covers a broad spectrum of large manufacturers and processors in food and beverage, pharmaceutical, automotive, chemical and hydrocarbon processing segments. OMAC merged with the Instrumentation, Systems and Automation Society (ISA) in 2005.Lost opportunityThere is some good news—since the previous Packaging World survey done in 2002, the percent of networked packaging equipment has doubled. The fact remains, however, that many packaging lines have no data collection. “There is an obvious network outage here,” says David Bauman, OMAC Technical Director. “The lack of reliable data collection represents a huge lost opportunity in the measurement of overall operational effectiveness.”Why is a machine on a packaging line not just another machine, easily integrated, easily networked? There appear to be two main reasons: the number of widely different machines involved in packaging lines, and the way manufacturers approach packaging operations. The OMAC survey reveals that more than half of the packaging lines of survey participants were clusters of five or more machines, and 77 percent of these had two or more control providers. Fully 20 percent had five or more different controls. Bauman notes, “When manufacturers purchase a packaging line, they choose the best machine for the job. Since packaging machine builders tend to be small and specialize in a certain area—filler, labeler, casepacker and the like—it is common to have each element of a packaging station supplied by a different machine builder.”Yes, but it'll cost youOf course, each machine builder integrates its own choice of controls, making (at the moment) homogeneity of controllers and communications a matter of luck. “You can always ask the builder to convert to a controller you know will network easily, but the machine builder is likely to levy a significant upcharge to do that—upwards of 25 percent of the cost of the machine.”Brian Owens, segment manager, Industry Process, for Schneider Electric US, a Palatine, Ill.-based automation supplier, points out an additional, organizational source for this disconnect: Packaging lines are often under the purview of people outside of the manufacturing mainstream. “When packaging is managed by a group that’s separate from production—for example, shipping—that group may not understand the benefits of direct networking with production,” Owens says. “There are differences in requirements as well, with manufacturing emphasizing reliability, rescue management and throughput, and packaging emphasizing flexibility and speed. In many cases, you might have to go up the ladder to the business system level before any obvious disconnect becomes apparent.”Without awareness of upstream networking benefits, Bauman says, “the easiest way is to hard-wire packaging machines together with a couple of signals, or let each machine operate standalone with a couple of sensors, say, to detect starved or blocked conditions on the machine. Unfortunately, when you do this, you lose some of the functionality available to networked machines, especially intercommunication between machines. Of course, the absence of networking ultimately limits the ability to tie packaging into MES (manufacturing execution systems) and line operator interfaces.”One key benefit of networked packaging equipment is meaningful metrics that can, when positive, corroborate production effectiveness, and, when negative, flag system problems. Another benefit is time savings. If configuration or programming changes can be administered centrally, setup time is reduced, allowing more product to reach shipping status. A third advantage comes at the packaging operational level. Bauman adds, “Machine-to-machine communications are as important [in packaging] as anywhere else in production. And a high percentage of packaging lines can benefit from both the ability to trigger changes in upstream processes as well as coordinate motion control within packaging workstations for critical queuing, sequencing and timing.”Two classes of manufacturers in particular benefit from easily configured machine-to-machine communications—contract manufacturers and those working under lean principles. For both, there is a continuous need to switch equipment in and out, and to change the flow of product queuing, processing and exiting.So, what would it take to more effectively extend networking to packaging machines? Better network topologies—that is, topologies that are easy to connect together. The OMAC Packaging Workgroup defines this as:· standardized networks to connect systems· standardized machine language by which to communicate· standardized programming· harmonization with ISA-88 and ISA-95 standards.Generally speaking, though the concept has been discussed for several years, this is a new, plug-and-play world, where modules may easily be switched out and others easily switched in. But new is not a favorite word in manufacturing. If a new thing does not work out, manufacturing does not have a “learning experience,” it has a deficit on the bottom line. The result: While significant pieces of the modular packaging world are in place, a significant proportion is still an objective seeking a solution. “The ideal would be to turn every machine—everything, not just packaging machines—into a component,” says Jeremy Bryant, automation market network specialist at automation vendor Siemens Energy & Automation Inc., Alpharetta, Ga. “That way, rather than connecting hundreds of interacting machines and control bits and pieces, you can connect component activities and objectives independent of the control systems and approaches inside each machine.”High-level abstractionIn other words, modularity offers high-level abstraction, a familiar concept in computer science, where a single function call in a high-level language can spawn hundreds of machine-code actions. Bryant points out that, yes, every machine is different, and every workstation in a process has different operations and parameters, but that there is a fairly circumscribed number of values that are needed to make today’s machines work to plan. “You can’t gain much traction by manually setting signal timings and pulse widths,” he says. “You need to work with high-level representations of machines, and let those representations automatically supply all of the hard-core ones and zeroes that make up the actual control data flow.”From user input, OMAC has settled on three primary network architectures for modular implementation: PC-based, controller-based and drive-based. In the OMAC world, five buses carry data from network node to network node:· The enterprise resource planning (ERP) bus for non-real-time data exchange from packaging machines to management and finance· The cell bus for non-real-time data exchange and interlocking between machines, intelligent devices, controllers and human-machine interfaces (HMIs) on a machine· The field bus for data exchange and interlocking between controllers and devices with real-time requirements· The motion bus for real-time data exchange and synchronization between motion control and axis loops, or between motion controllers· The input/output (I/O) bus for real-time data exchange between controllers and I/O level needs.OMAC focuses on functionality, not network type. The specifics of how the three types of controller technologies play in the five buses, of course, varies widely, and those interested in more detail can turn to the OMAC Web pages for PackConnect, the OMAC initiative focused on “plug & pack” interoperability. Suffice it to say that a number of vendors have joined the modularity bandwagon.“The most interesting challenge in this,” says Bryant, “is not how I/O or networking in controller modules can hook into fieldbus, but how modules of any sort—controller, drive, PC, PLC—can make one machine work with others around it.” Siemens offers an engineering tool, Simatic iMAP, that provides a graphical interface to cross-vendor programming of distributed systems in what the company calls component based automation (CBA).Similarly, packaging-control specialist Elau Inc., Schaumburg, Ill., recently introduced its new PacDrive iSH Series Intelligent Servo Module, offering modular automation in packaging equipment. “The result is a highly simplified connection,” says John Kowal, global marketing manager for Elau. “There is a single cable for power, motion control and I/O, which plugs into a distribution box. It’s a self-contained system that potentially reduces the number of terminations, cables and networks involved in packaging automation.”Next stepsAs manufacturers move off the fence toward modularity, what is the best way to begin thinking about a modular packaging automation project? Greg Dixson, product manager for automation systems at Phoenix Contact, an automation components supplier with U.S. headquarters in Middletown, Pa., counsels, “The critical issue to understand about the OMAC approach, which we have actively supported for years, has two sides. It brings tremendous power and flexibility, but it also requires awareness of responsibilities. With open equipment, you have almost unlimited freedom for topology and function. You can gain access to any node on your network from anywhere in the world. But you now need to consider subnetwork realities, redundancy, security and the like.”He cautions, too, that the chief executive officer does not need to check the digital output of every node. “You can overdo shop floor-to-top floor. The
bigger-picture analysis is usually all the business side wants,” he points out. The biggest problem area? “Ensuring compatibility with the IT (information technology) department. IT doesn’t want proprietary solutions cooked up onthe factory floor. IT-compatible technology is an important focus of the OMAC group.”Ultimately, connecting packaging to production on the network offers lower engineering costs and faster time to package than non-networked equipment, a gain that continues to play out with every change of package form factor. OMAC cites one large, unnamed company that accrues an annual $15 million savings attributed to its adoption of packaging equipment networking. But, large or small, given the growing number of network-ready machines and controllers, a little extra focus on networking during system specifications can pay off.
bigger-picture analysis is usually all the business side wants,” he points out. The biggest problem area? “Ensuring compatibility with the IT (information technology) department. IT doesn’t want proprietary solutions cooked up onthe factory floor. IT-compatible technology is an important focus of the OMAC group.”Ultimately, connecting packaging to production on the network offers lower engineering costs and faster time to package than non-networked equipment, a gain that continues to play out with every change of package form factor. OMAC cites one large, unnamed company that accrues an annual $15 million savings attributed to its adoption of packaging equipment networking. But, large or small, given the growing number of network-ready machines and controllers, a little extra focus on networking during system specifications can pay off.
● For more information, search keyword “OMAC” at www.automationworld.com.
Sponsored Recommendations
Sponsored Recommendations
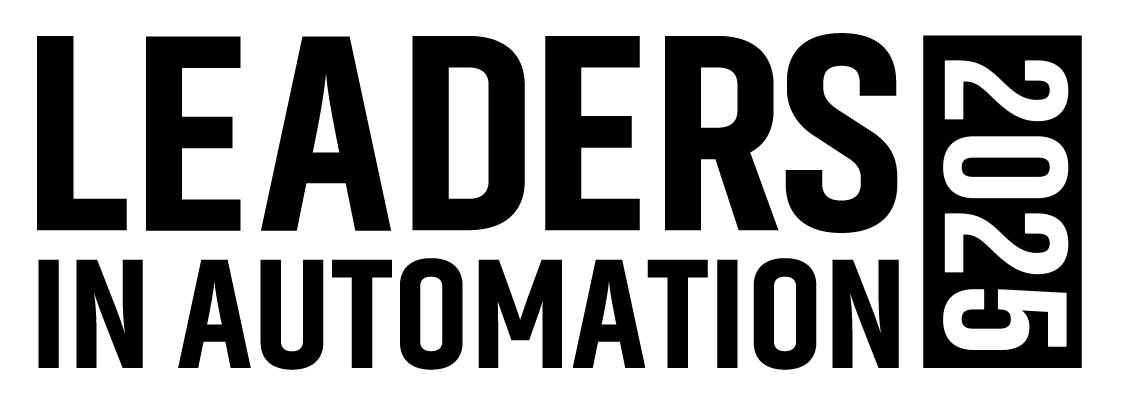
Leaders relevant to this article: