Extreme Materials white paper profiles specialty blends to award winning connectors
Aggregating decades of interconnectivity knowledge, Northwire, Inc. (NWI) along with its partner The LEMO Group, has released Part IV of their “Extreme Environments, Complex Requirements” white paper series, titled “Extreme Materials: Robust Performance from Cable to Connector.”
By gleaning understanding from teams of NWI custom cable and LEMO precision connector Subject Matter Experts, the white paper details critical considerations in the design of cutting edge connectivity technology. Solving complex and continually evolving wire and cable assembly challenges, Northwire’s cable designers partner with connector specialists at LEMO to provide customized solutions for extreme and diverse applications.
Immersing themselves fully into the end application with a comprehensive understanding of the product’s required functionality, NWI and LEMO SMEs critically assess the complex factors that will contribute to the attainment of each customer goal.
The Extreme Materials white paper identifies the cable and connector attributes contributing to highest performance and reliability while abating the environmental challenges associated with medical cable, underwater cable, industrial wire and cable, and heavy duty cable and connector applications. Just some of the critical factors detailed within the Northwire-LEMO Extreme Materials white paper include:
Inside-Out Cable Construction
Dissecting foundational cable engineering elements and their contributions to high performance, reliability, and longevity in cable life, the following components are detailed within the white paper:
- Copper Stranding
- Strength Member
- Breather Tube
- Water Blocking Material
- Fillers
- Barriers
- Shielding
- Jacketing
Applied in conjunction with resilient and durable cable assemblies, water blocking agents are integrated to mitigate failure in the event the cable assembly is compromised. Water blocking agents quickly react to moisture seeping into a damaged part of the cable, sealing off the leak, and preventing migration of the liquid. Northwire capabilities reducing risk of leaks within underwater cable and wet environments are featured within Extreme Materials along with LEMO’s NiCorAl surface treatment for rugged connectors which protects cables from salt water corrosion.
NiCorAl lengthens the life of aluminum components and passes the 500 hours salt spray test under AECTP 300 / MIL-STD-810 / MIL-STD-202 standards. It is also RoHS2 and REACH 2017 qualified. NiCorAl was honored as second runner up in the 2016 i-NOVO Awards for the Tech Category with LEMO’s HALO LED connector winning the i-NOVO Award for Design recognizing the product’s cutting edge design trends, attention to ergonomics, and exceptionally innovative solutions.
This LEMO HALO LED connector includes an LED light flange which displays connection status and offers compatibility with the existing 1B, 1K, and 2K Series. The connector will be available in crimp or solder contact versions. The HALO LED connector efficiently displays connection status helping to prevent counterfeit functioning, unauthorized use, and mis-mating, only applies power when allowed, and records usage along with other benefits and features.
Important use and environmental considerations when selecting cable are detailed within the white paper including whether the cable will be utilized within high flex cable and constant motion applications and subjected to extreme temperatures and environmental factors including contact with oil, chemicals, welding slag, etc.
The Extreme Materials white paper presents multiple levels of cable design considerations explaining Concentric, Unilay, and Rope Lay stranding configurations and copper as the standard for measuring conductive materials and its attributes. The role of the cable assembly’s strength members in protecting connectivity and their contributions in providing unique solutions such as pull strength, push strength, mechanical strength, or rigidity is summarized along with application for common types including fiberglass rods, steel strength members, and aramid fiber.
Extreme environment protection from high heat, pressure, oil, water, chemicals, flame, and abrasion is provided by integrating the appropriate breather tube for the cable application. Direction is provided for navigating the wide range of sizes, durometers, and material options such as PE (Polyethylene), nylon, PVC (Polyvinyl Chloride), PUR (Polyurethane), and PTFE (Fluoropolymers).
With a primary function of filling space between components to secure the desired cable form, filler materials and their associated benefits are noted. Important considerations when selecting filler materials include the need for moisture, flame, shrinkage, and heat resistance, increased strength and insulation factors, infusion with water blocking chemicals, and cost effectiveness.
Given the importance of a cable’s jacket for its performance and role in protecting critical internal components from extreme environments throughout the life of the cable, materials that excel in extreme temperatures are summarized within Extreme Materials. Northwire’s fluoropolymer jackets rated from -200°C to 260°C, polyethylene jackets that perform up to 125°C, and a wide range of specialty PVC and TPE blends that can be rated from -60°C to 105°C are featured. Cut, crush, and abrasion resistant cable jacketing utilizing fluoropolymers and TPUs along with Hytrel® (thermoplastic polyester) that allow for ease in coiling offer additional damage control options. The need for high performing Low Smoke, Zero Halogen cable (LSZH cable) is increasing. In response, Northwire offers a commercial TPU to meet or exceed requirements with additional options including rigidity, flexibility, oil and chemical resistance, and varying flame resistance.
Customization and specialty blends are regularly developed by NWI’s cable design engineers for specific applications. One such example was a new jacket material that achieved a direct burial rating. This rating requires a 1,000lb weight to be applied to the cable over a 1Ž2” steel rod and held for one minute without any tears in the insulation or jacket material. NWI’s materials engineers designed a unique material blend that passed this intense direct burial rating.
In addition to ensuring that the cable can withstand extreme environments, consideration should be given to the connector and assembly manufacturing. The connection is often more vulnerable to the elements than other parts of the assembly. Together, Northwire and LEMO provide completely integrated customized cable and connector solutions.
>>For more information, click here.
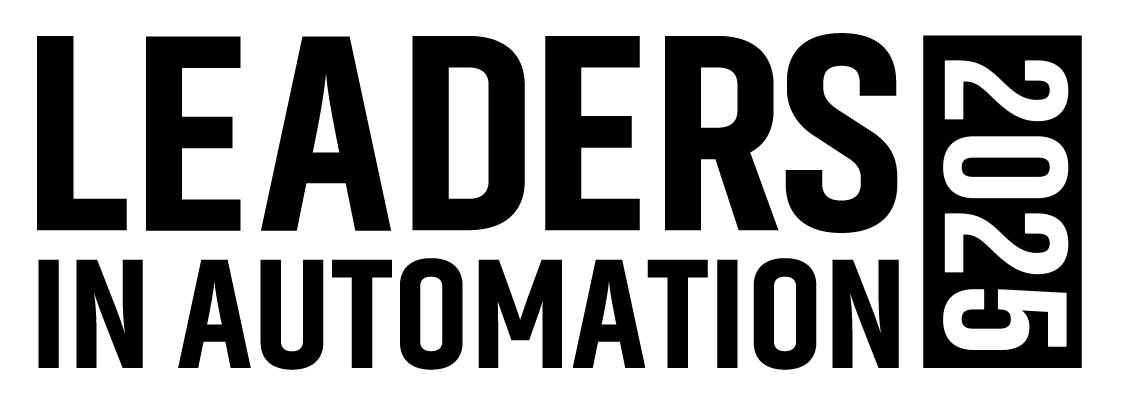
Leaders relevant to this article: