Human machine interfaces are expanding their role, moving from basic control panels to gateways where operators can see and respond to alarms, check component health and safeguard the company’s computer networks. At the same time, HMIs are using higher resolution displays to allow users to see more useful information.
These technical advances will help operators and managers improve efficiency in their facilities while providing a central point where they can get more information and perform more jobs. What should you expect from HMIs when looking at your next equipment upgrade or acquisition?
HMI Trends to Watch
Consider the following six areas where HMIs are making significant advances.
Bigger, sharper displays. “High-resolution monitors allow operators to see more information, so it’s easier to understand what’s being shown,” says Lee Cheung, Product Marketing Engineer at Mitsubishi Electric Automation. “For example, operators can see fluid level changes, study animations with flow meter, and access changing data points so they can see how parameters are changing over time.”
Intuitive alarms. Another major change for operators is the trend toward intuitive alarms. These alerts aren’t just designed to be easy to understand. They also provide a lot more information than flashing lights or the often-confusing error codes of the past.
“When alarms happen, operators can check the HMI to see the severity of the alarm, identify in which area it occurred and even pinpoint the exact location within the machine. The machine can keep track of the time of error occurrence, along with data that preceded the alarm,” notes Cheung.
Yet another trend will further ease the workload for operators. Alarms aren’t just becoming easier to understand, they also are decreasing in number. Many messages will be sent from the machine directly to technicians and others who need to examine when problems arise.
“Alerts can now be pushed out to engineers or specialists,” Cheung says. “Alerts can also be sent directly to maintenance, so operators don’t need to stop what they’re doing to notify maintenance every time there’s an alarm message.”
Predictive capabilities. These improved interactions between humans and machines aren’t the only way that HMIs are expanding their capabilities. HMIs also are helping equipment makers and users move into the world of predictive maintenance, in which digital systems monitor operating parameters to determine when components may be nearing a failure point.
HMIs can now display alerts that are tied to the health status of components within the equipment. Such integration allows maintenance staffs to predict when repairs are needed rather than waiting until a machine breaks down. With this information, technicians arrange timetables for repairs so they can replace components before faults occur. Another benefit of predictive maintenance is the ability to better manage the inventory of replacement parts.
Easier upgrades on legacy equipment. Intuitive alarms can be installed with just a software upgrade, so this functionality can be added to any HMI. Assuming the hardware has the necessary capabilities, it’s fairly straightforward to upgrade existing equipment with these new features. HMI software with the desired alerts and alarms can be downloaded over networks or by using USB ports. On many systems, USB ports are located on the front of the HMI, so users don’t even have to open cabinets to install new software. Updates transferred over industrial networks are equally seamless.
Cohesive protection. HMIs also play a role in cybersecurity, an issue that’s become a major concern for a rapidly growing number of industrial companies. It’s increasingly common for companies to move data between the corporation’s information technology (IT) networks and the operational technology (OT) networks that connect plant floor equipment.
Often, HMIs sit between the IT and OT networks, serving as a gateway. These gateways can help isolate the two networks, so problems on one won’t impact the other. These gateway functions also enable companies to easily deploy Industrial Internet of Things (IIoT) solutions on existing or new assets, while keeping the assets secure.
Integrated data gathering and sharing. Another benefit of advanced HMIs is that they can simplify operations by gathering data from a range of automation components . The HMI can be connected to all the equipment, or just the main automation controller; it can serve as an access point for equipment that isn’t directly connected. For example, a PLC may need information from some equipment that’s configured behind the HMI. Though the HMI may not have a direct connection to the hidden equipment, it can tunnel through the PLC and network to access equipment like a servo, eliminating the time and cost of reconfiguring the equipment that would otherwise be needed.
In most systems, the workstation HMI is not the only place to see alerts. Information generated by the HMI can also be connected to the manufacturing execution system (MES) or via smart Web servers. With Web servers, more detailed information can be presented to engineers versus the operator, making it easy for the engineer to make more informed decisions before they even reach the machine’s location. Alerts and reports can also be sent automatically via email to specific people, for example telling a plant manager when there’s a problem that may have major impact or alerting the quality control group when certain thresholds are nearing limits.
With MES-based systems, data can be sent, or read directly from the database, where anyone with access can examine the performance and operating parameters of any connected equipment. Such capaibilties allow managers to gain access in different locations and analyze performance or manage changes – whether they’re in a coffee shop nearby or at the corporate facility that’s based on another continent . When data is stored in the MES system, managers can monitor data over long periods to see which machines have frequent problems.
HMIs Playing an Increasing Role in Performance Excellence
HMIs are no longer simply the means to monitor and control machines. Instead, they are playing a key role in competitive differentiation. Users of the latest technologies have far more opportunities than peers to make decisions based on comprehensive information that’s easier to analyze and put into practical use, regardless of location.
See the latest in Mitsubishi's HMI-GOT Series here.
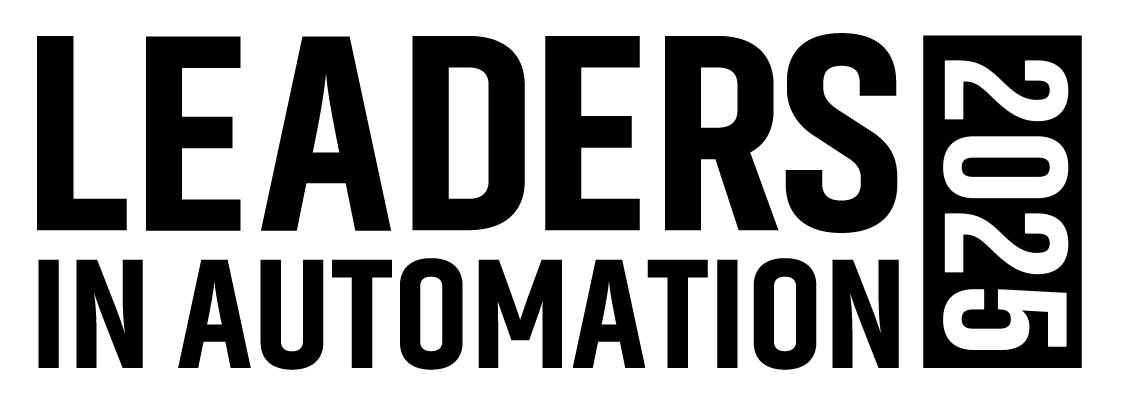
Leaders relevant to this article: