The most important challenge presented to those who are in charge of producing materials and products today is plant performance. At the level closest to the action, there are two main areas of responsibility—operations and maintenance. Another way of stating these areas is utilization and availability. One group is responsible for getting maximum utilization from plant assets. The other is responsible for assuring that plant assets are available for production. These are often contradictory responsibilities. As Peter Martin, author and vice president of automation supplier Invensys Operations Management, in Foxborough, Mass., is fond of saying, “If you car is in the garage, it is available, but not used. If you are driving it, it is used but not available.” If maintenance wants to shut down an asset to perform some sort of upgrade work, then that asset is not utilized for production. It’s like two vectors pulling in directions that potentially reduce overall plant performance. So how do we combine those vectors in order to achieve maximum overall plant performance?Coordination neededSid Snitkin is vice president of supply chain and asset lifecycle strategies at ARC Advisory Group Inc., in Dedham, Mass., and has been studying these phenomena. “Everyone can do maintenance, and everyone knows operations,” he says. “But, can they coordinate? I’ve seen people change the way they view asset performance management (APM) as they now look to optimize performance.”Barry Lynch, global Proficy product manager at automation supplier GE Fanuc Intelligent Platforms, in Charlottesville, Va., states, “We’ve seen a gap for real-time information sharing between operations and maintenance, which we call latency. Customers have been building their own point solutions between their production systems and their computerized maintenance management systems (CMMS) or enterprise asset management (EAM) systems, but these can be costly for them to build, implement and maintain. So we have introduced a product that flows into the production systems, allows them to plug into data with a rules engine that can then plug into the CMMS or EAM system. In fact, we’re seeing this trend toward gathering and using real-time information gaining momentum. A complementary trend is the adoption of server-based, centralized EAM. The biggest issue software developers face is the number and cost of interfaces.”A longer discussion of how some visionary people and companies are dealing with these interfaces is below in the description of the Open O&M Initiative group’s demonstration at ISA Expo 2009 on Oct. 6. First, some context for the discussion. Snitkin notes, “Research shows that organizations pay incredible costs for poor management of their processes that create, use and care for assets. ARC’s own research indicates that traditional approaches to Asset Lifecycle Management actually encourage this dysfunctional behavior. I have released a report that continues our effort to rectify this situation by offering a new, richer vision for Asset Performance Management that integrates key people, processes, technology and information.”Groups of engineers, information technology (IT) professionals and other manufacturing experts have been thinking about how to put all of this together for years. One result is the ISA95 standard for the integration of enterprise and control systems promulgated by the International Society of Automation. Another group that focuses on maintenance areas is the Machinery Information Management Open Systems Alliance (MIMOSA). Then there is the Open O&M Initiative, a nonprofit organization dedicated to the development and use of a harmonized set of standards for the exchange of Operations & Maintenance (O&M) data.Some expect the results of these efforts to be a “shrink-wrapped” set of software tools that can be incorporated into a sort of nirvana of data interoperability. But Snitkin explains these “are more a method of thinking than a slap-in piece of software.” But putting all this data together is more than just an exercise in software creativity. Adds Snitkin, “It’s about the information you need to do your work. When the plant goes down and you don’t have information about how things work, it’s not good.”There is a need for something to help close this performance loop, and analysts and suppliers are quick to pick up the moniker “Asset Performance Management.” The question remains: Just what is APM? Snitkin says, “APM has become a popular catchphrase for strategies to help asset-intensive organizations get more value out of their costly equipment investments. But it is rare to find two cases where APM means the same thing. So it is difficult to compare approaches and evaluate solutions. ARC’s vision for APM follows the spirit of those with the broader, combined focus, but covers all areas, technologies and industries. It is also firmly grounded in the extensive research that we have done in Asset Lifecycle Management (ALM) and Asset Information Management (AIM). This provides valuable context for understanding the role of APM and a solid basis for clearly delineating its boundaries.”Supplier thinkSuppliers are clearly thinking about this new reality. Tim Sowell, vice president of product and solution strategy at the Invensys Operations Management unit of Invensys plc, in Lake Forest, Calif., reveals some discussions of the “Invensys Fellows,” a group of thought leaders within the company. “We take a look at what is happening in the market, transformations that dictate competitive and growth positions. When companies put their automation systems in place, the objective was to reduce labor. Now, we’re finding that much of that is done. Leading companies are taking a fundamental shift. Automation, manufacturing execution systems (MES) software and information systems are now used to empower the worker. They become performance managers. They are more educated, and now we can deliver more information to them that can affect performance. They are not just waiting for exceptions. They have dashboards and operator controls to help them run the ‘golden batch.’ ”So far, the discussion is about the broad categories of operations and maintenance, but there are many types of performance within those two categories. Louis Meyer, director of global industry solutions for Invensys, based in the United Kingdom, defines several types of performance, and singles out areas where performance issues stand out now. “Energy performance indicates when a unit is not performing well. Look at heat exchangers, reactors and the like for sudden characterization changes,” states Meyer. “Unless you manage the correct things, your energy usage will suffer. Of course, your mechanical components must perform consistently. Balanced scorecard and Overall Equipment Effectiveness (OEE) can give you the bigger picture of the availability/utilization curve. Remember that 100 percent availability is not necessary if you only need 80 percent. Quality and environmental performance are also indicators of a well-run plant.”Among other performance areas cited by Meyer is the control. How well process control performs impacts energy, quality and throughput. “The problem of control performance,” he says, “is that from a business plan perspective, you never see it if it’s efficient.” Related to this is operator performance. “Do we rate operators to make sure they are in alignment with things that make sense,” asks Meyer. “Do we have the metrics to judge people on what matters for overall plant performance?”Another essential area of performance is delivery to due date—schedule performance. Maybe there is a mismatch of scheduling and production systems. When schedules are missed, people scramble to keep up and sometimes make bad decisions. Meyer lastly mentions yield performance. This is a derivative of other performance factors, but it is something that impacts plant performance and profitability.The key to overall plant performance, concludes Meyer, is to align all of the various factors. “Whatever metrics you use to evaluate performance, assure you pick for each function only those metrics that drive human performance. It should be a business management loop, just like a multvariable control problem. Metrics can fight each other, kind of like in advanced control, so get them aligned.”What's happening?Effective real-time information communication and consistent metrics result from the development of data models and communication standards. Much work has been done in developing just these technologies. They are starting to work in real applications. Invensys’ Sowell cites the example of a fleet of power stations where management was trying to understand what was going on among its array of stations. Each of the stations had its own set of controls and information systems. So, the company built an information system on top that applied common standards on how to measure units and equipment. “Now they can see how all plants are running across one country and all the variables and performance. It is now closing the performance loop,” says Sowell.One organization that is trying to put all the standards together is the Open O&M Initiative. Headed up by Alan Johnston, who is also president and chief executive officer of MIMOSA, its member companies and engineers continue to add to an interoperability demonstration displayed annually at ISA Expo. Johnston describes what the organization is doing and what was involved in the demonstration in October in Houston at ISA Expo 2009:“We are finally moving toward the connected, real-time enterprise in a more tangible fashion, where the people, processes and technology must all interoperate,” says Johnston. “This really requires the participation of the key IT players, the automation/controls players and the lifecycle engineering oriented firms (EPCs, or engineering, procurement and construction organizations, and engineering/design tool providers) to work together in a much more collaborative and seamless fashion. In turn, this is made practical by the appropriate application of key open standards that are shared by all of these major communities. While the approach we are using should work for many, many key industries, for the near-term, we are intentionally focusing on those that are often collectively referred to as critical infrastructure. This includes integrated energy, public utilities, aerospace and defense, military and transportation. Since refining is simply a specialized petrochemical plant, we also are working with chemical and petrochemical firms. These industries are highly interdependent and they either all work together or they all suffer (along with the countries in which they reside).”The Initiative has been incorporating such technologies such as OPC, the open connectivity standard; ISA95, the standard for integrating control systems with enterprise systems; and MIMOSA—the standard for communicating maintenance and asset information. Lately, it has added connectivity to plant design lifecycle information using ISO 15926—“Industrial automation systems and integration—Integration of life-cycle data for process plants including oil and gas production facilities,” promulgated by the International Organization for Standardization (ISO).Johnston explains, “By beginning to work closely with the ISO 15926 team, we have added another critical element to the mix, as it appears to be emerging as the principal ontology for this sector, and serves as a way of gaining semantic alignment. MIMOSA and the ISO 15926 share key roles in cross-industry lifecycle management of the physical systems and physical assets which support the logical business processes typically described by industry specific markup languages. This approach actually provides suppliers with a practical way to ‘write once, use many,’ where much of the industry-specific elements of the work is defined by metadata.”Two traditional automation/controls suppliers participated with Open O&M—Rockwell Automation and Yokogawa. Also participating was a major player in the Engineering/Design tools market—Intergraph—and a couple of key specialty players—Mtelligence and INOVx. But Johnston sees a need for further expansion of the group.“Microsoft, Oracle, IBM and SAP all need to play critical roles in this effort,” says Johnston. “This is partly due to the fact that the automation suppliers have lots of difficulty telling a credible enterprise story. They need the IT giants to tell a credible enterprise interoperability story in a way that includes their key partners. Part of the credible version of the interoperability story must be a willingness to leverage open standards and an open information service bus concept as the keys to interoperability, rather than seeking to impose a proprietary hub-and-spoke model for integration. I believe that process is now getting underway with Microsoft, IBM and SAP. I hope Oracle will also join the solutions process with us in the near future.”The last part of the interoperability team was the Collaborative Research Center for Integrated Engineering Asset Management (CIEAM) from Queensland University of Technology, in Brisbane, Australia. It is chaired by Professor Joseph Mathew, who is also the chair of the ISO TC 108/SC5 technical committee on condition monitoring and diagnostics of machines. He has succeeded in helping to establish the Engineering Asset Management definition for EAM as a more interdisciplinary and engineering-based alternative to the Enterprise Asset Management term that has been in use since the mid ’90s. He founded the first Collaborative Research Center dedicated to this new definition of EAM as part of a public/private funded approach with the Australian government and major end-users such as Rio Tinto and Queensland Rail (the largest rail operator in Australia).“To remain a leading first-world country,” concludes Johnston, “the United States needs to lead in helping these standards to work together more efficiently. Interoperability must always start with people/culture issues, whether in an end-user organizations, standards bodies or suppliers. At one time or another, I have been in each community and I have also covered both the traditional Plant-to-Business (P2B) stack as well as the lifecycle engineering dimension. No single person or organization is smart enough or knowledgeable enough to do all of this on their own. We must work together. This is where I think the Open O&M Initiative has finally succeeded in helping to establish the needed level of collaboration and consensus within consensus standards organizations.”Come togetherMany people are working hard to achieve interoperability and open communications so that the performance loop can be closed to make manufacturing more important to the enterprise. This won’t work, though, unless engineers, IT professionals and manufacturing managers work together to demand these technologies from their suppliers and implement them.
Related Sidebar - Interoperability Line-upTo read the article accompanying this story, go towww.automationworld.com/feature-6214.
Subscribe to Automation World's RSS Feeds for Feature Articles
Companies in this Article
Companies in this Article
Sponsored Recommendations
Sponsored Recommendations
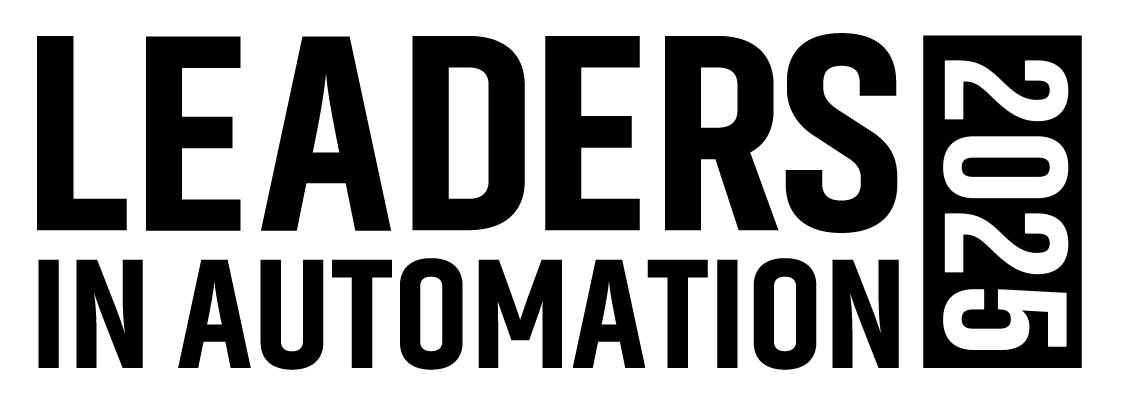
Leaders relevant to this article: