A flurry of merger and acquisition activity in the industrial sector recently brings up an interesting question: How does a manufacturer harmonize the disparate manufacturing operations management (MOM) or manufacturing execution system (MES) solutions? The benefits—and challenges—of doing so apply to any multi-site manufacturers whose plants have been in operation for a while, so advice from knowledgeable peers is helpful. However, the time immediately after a merger or acquisition may not be the best time to tackle such a project, says Bianca Scholten, principal consultant at Accenture (www.accenture.com) and author of two books, The Road to Integration and MES Guide for Executives.
“For benchmarking purposes and total cost of ownership, it may be interesting to consolidate MES systems but, in my experience, after a merger there are so many urgent things to do that this will not have the highest priority,” Scholten says. “The most urgent is that the facilities can continue working safely and efficiently. In some cases, that means that interfaces need to be made between the company’s central ERP [enterprise resource planning] system and the local MES systems.”
Companies do eventually seek operational harmony. Linde AG (www.linde.com), a industrial gases and engineering company with global headquarters in Munich, Germany, endured a complex history of takeovers, mergers and divestments since its founding in 1879. As of May 2011, its 48,000 employees were supporting more than 350 plants in approximately 100 countries; the company “had inherited legacy manufacturing systems from multiple vendors from multiple acquisitions,” said Lars Wallstén, head of performance systems for Linde AG.
What Linde management wanted, was “defined and common processes for all regions so that they all work in the same way,” said Wallstén. With regard to operations visibility, they also wanted “the local operator and Linde board to view the same information.” Wallstén spoke at the European conference of Manufacturing Enterprise Solutions Association (MESA) International (www.mesa.org) on the importance of “driving operating performance across the enterprise from a foundation of production data.” MESA International is a global community focused on improving operations management capabilities.
>> Visit bit.ly/awnews185 and read about new MESA research that shows how predictive and holistic plant operations metrics are more likely to produce bottom-line improvements.
Not surprisingly, each part of Linde’s business was satisfied with the MES solutions they had installed and were resistant to significant change. But the company’s management realized the need to standardize operating practices, production reporting and information flow across the enterprise to improve operational performance and decrease energy costs.
Other reasons to standardize across plants are to gain operational flexibility, and to have lower total cost of ownership for maintaining the applications: Fewer unique solutions require fewer people to support them, and you gain economies of scale if you reuse functionality built for one plant in several others.
Beware the obstacles
Accenture’s Scholten says once a company has decided to go forward with a harmonization plan, a number of obstacles may slow the process. In addition to using different solutions, a new site may also use different terminology for the same process or result. They may have historical data in a system and don’t want to lose it. “They may have custom-built solutions with a very good fit to their requirements, which makes them reluctant to change. And they may be using a different brand of MES, and actually have a better solution and/or be at a higher maturity level than the existing plants—which politically makes it very hard to take away that fine solution,” she says.
Also be aware that country-of-origin or corporate-culture issues can affect MES harmonization efforts. “To collect information from mulitple sites in an efficient way, we use Microsoft Excel tools with pre-defined questions,” says Scholten. “It already is complex to have people understand what kind of information you require and why. Then there also may be a language problem, which brings in a new challenge.”
Accenture’s teams have different native speakers available and site visits can be conducted in a mixture of several languages to ensure everyone understands each other, says Scholten. “Also, in some cultures, the people will not take the risk to make a mistake. Then you are very much depending on the higher-level people such as a plant manager to collect all the required information,” she adds.
>> Click here for Seven Essential Questions for MES Harmonization, according to Bianca Scholten, principal consultant at Accenture.
Start with a firm foundation
Linde AG’s approach to harmonizing its operations was to build a standard foundation of production data, which included company-standard data historian software. “We have more than four different vendors of historians in place with variable quality of installation and supportability, and many of our plants are not connected to any historian at all,” said Wallstén. “It would be extremely difficult and expensive to implement a global [MES] template in all these existing systems and then support them going forward.”
Linde management wanted a scorecard for performance indicators for safety, people, reliability and efficiency in the same software tool to facilitate follow up and root cause analysis. Structurally, Wallstén and his team decided that meant:
- Every plant must be connected to a data historian no matter what size. Data that is not available from the control system would be manually entered.
- Any solution must include the possibility for future interfacing to Enterprise Asset Management (EAM) and Enterprise Resource Planning (ERP) systems and safety reporting.
- The historian must store data for the lifetime of the plants.
- The data they needed to store included plant data (analogue values, digital values, calculated values), events (alarms and alarm logs, operator actions—elog software), process event limits (quality, process safety, and the like), and targets (on-line, daily, weekly and monthly).
“We concluded that no historian supplier used in Linde could deliver our requirements in one tool,” said Wallstén, “so either we buy one software for elog, one for alarm history, one for trending etc. or we select an open environment where we can incorporate all functions and try to get our supplier to bring in our functions over time.”
Linde chose Proficy iFix from GE Intelligent Platforms (www.ge-ip.com), Charlottesville, Va. The choice “boiled down to flexibility, cost and willingness from the vendor to develop functionality with them.” said Wallstén. “There are pros and cons with all vendors.”
In rolling out the new system, Wallstén said “it is a big change for operations to have such an important function in a central environment and not locally at the plant.” He said one of the most important success factors has been centrally defined global tags. “For example, instead of calculating spec power as FIC3201+if( FIC3202 >50; FIC3202 ;0)/UA9301, we use :(GOX1S3+GOX2S3)/PlantPower. This makes it possible to define calculation rules in one place and to be able to accumulate, for example, GOX production for Germany,” he explains.
MES template
Another approach to harmonizing MES systems is to create one integrated MES template that can be implemented at each plant on top of or within whatever system resides there. Accenture’s Scholten explains: “MES can be designed in such a way that the individual local characteristics are limited as much as possible and connections to the diverse equipment landscape can be handled through a local data historian. The ideal solution is to have only one MES template that provides a superset of functionality for the most extensive group of user requirements. The smaller or less complex factories can turn off functionality that they don’t need. Less mature plants get the possibility to enter data into the MES system manually as long as no control systems are available yet for automatic data collection. In a later stage, they can integrate MES with new control systems.”
“It is not so hard to understand that the ‘one size fits all’ concept is much more cost efficient,” says Scholten. “Remember that plant managers don’t have their cars custom made either. They choose a basic model and select a few accessories to assemble the car they like. In the same way, an MES template can take into account local differences, but the basis is already preselected.”
Recipes and reports can be standardized very well using industrial standards like ISA-88 and ISA-95, says Scholten, while the differences concerning equipment are handled by the lower level control systems. MES systems can usually be configured on the parameter level, so it will still be possible to take into account some minor differences using the same template, she says. “Local adaptations will always remain necessary, because a successful MES system must be tightly integrated with level 2 control systems that have a direct connection to the physical equipment.”
Scholten recommends grouping plants together and developing a template per groups of plants that look alike. “Build a landscape that consists of different modules and provide the possibility to use or not use all modules. Standardize on the level of reporting, way of working, master data and so forth. which in the end all needs to be supported by a system,” she says.
Seek balance
TE Connectivity (www.te.com) (formerly TYCO Electronics Ltd., with headquarters in Schaffhausen, Switzerland), sought balance among simplification, automation and standardization efforts when it looked at harmonizing MES among its global operations. This diverse electronics, electronic components, and networking products maker has a portfolio of 500,000 products produced at 97 manufacturing sites worldwide.
TE Connectivity’s Information Technology (IT) department was challenged with how to position MES systems in a global corporation. “There were a lot of local initiatives, often engineering-driven, which gave us high potential for innovations,” said Christian Brefka, manager of global MES applications for Tyco Electronics,” speaking at the MESA International conference in September 2010. These local solutions were usable only with special focus or were limited in scope, and lacked integration with corporate systems such as ERP.”
The company wanted workflows designed for the operator in an out-of-the-box solution that covered 80 percent of requirements, and had a flexible system architecture that could be configured instead of coded, said Brefka. They also wanted to collect information from devices and machines with as little user interaction as possible, and provide automated visualization of shop-floor documents.
TE Connectivity achieved these and other goals by installing two standard software packages. SAP-ME (formerly Visiprise) from ERP vendor SAP (www.sap.com) handles serialization, traceability and genealogy for eight product lines in China, two in the U.S. and one in Belgium. The MPDV/Hydra software from Germany-based MPDV Mikrolab (U.S. headquarters are MPDV USA Inc., www.mpdv-usa.com, Orland Park, Ill.) handles shop-floor data collection, machine data collection and more for 1,774 directly connected machines in plants in 13 countries.
The company also made use of the MES template concept, which had the following components, says Brefka: in-plant MES servers that are centrally administered and supported; data models/binaries distributed “everywhere”; module or enhancement activation handled “per plant”; and optimized distribution models.
Despite all the challenges, sometimes the harmonization process goes much easier than expected. “I am currently involved [with standardizing MES for] a chemical company,” says Accenture’s Scholten. “We first expected that in the 19 sites there would be all kinds of systems on the shop floor, and a lot of integration with the new ERP system would have to be realized. But in the end, there appeared only to be about two sites that were highly automated.” That meant there were fewer habits to unlearn, and standardizing on a single solution went more smoothly.
>> Wireless, Security, OEE and other topics were discused at The Automation Conference.
Companies in this Article
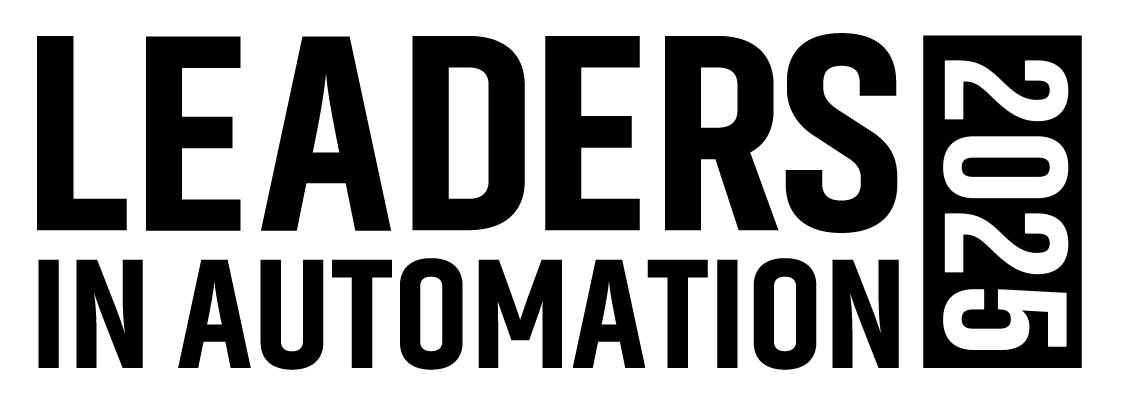
Leaders relevant to this article: