Levitating Transport Systems
TRANSCRIPT
Automation World: David Greenfield 0:14
Welcome to the automation world get your questions answered podcast where we connect with industry experts to get the answers you need about industrial automation Technologies. I'm David Greenfield, editor in chief at Automation World. And in this episode, we'll be looking at levitating transport systems. Now joining me to explain this technology is Kristen Ballistrea, with B&R Industrial Automation, a manufacturer of automation technologies, and ABB's Global Center for machine and factory automation. So thanks for joining me, Kristen.
B&R: Kristen Ballistrea 0:47
Thanks for having me, David.
Automation World: David Greenfield 0:49
So, you know, we've been seeing this trend toward levitating transport systems developed over the past few years now. And it's really been fascinating to watch. So can you explain briefly how the shuttles on the Acopos 6D levitate and how they work in a machine or on a manufacturing line?
B&R: Kristen Ballistrea 1:09
Yeah, of course, I mean, the technology is super cool. I really enjoy working with it. B&R's Acopos 6D technology uses magnets magnetism to levitate. So outside of the PLC and the power supplies, there are two main components to this technology, we have the segments and the shuttles. And that's the terminology we use with the system. The segments are actually 240 by 240 millimeter squares that act as the stator of this of the standard servo. The other component is the shuttle that acts as the rotor of the servo. When you power the system on the magnetic field is actually induced and levitates the shuttle. So the position sensors inside of the segments can read the position of the permanent magnet in the shuttles. And this allows for closed loop control. So we actually have different size shuttles. But the shuttles themselves are permanent magnets. And while they're levitating, the shuttles can carry loads and materials with different operations within the manufacturing process.
Automation World: David Greenfield 1:59
Can you tell us more about the need for these levitating shuttles in industry? And by that I mean: What industry needs are they designed to fulfill or problems do they eliminate compared to the more traditional conveyance or track systems that we're all more familiar with?
B&R: Kristen Ballistrea 2:16
Of course, yeah, as we've talked to customers and potential customers, we're finding more and more applications for planar technology. You know, it's a newer technology. And so this is like the really fun part, right, where just new ideas are, keep coming at us things that we hadn't thought about before. But what we're finding is we find is technology is great for application, which footprint really matters, where you may need a clean system. And when you really need precision and flexibility in production. So Acopos 6D can give you the flexibility to move from smaller batches to larger batch sizes very quickly. And anywhere in between, that gives you the ability to manufacture custom product and manufacture a number of SKUs on the same system. And the amazing thing is we can do all of this with five micron precision. So this kind of precision and accuracy and six degrees degrees gives a lot of advantages for certain applications. So you know, we like to think of the Acopos 6D is kind of like the ballet dancer, it's precise, precise, smooth and flexible, rather than the sprinter that's pushing a lot of the same product out as fast as possible. So when you think about that, and because of that, there's a lot of applications we have seen in the pharmaceutical lab automation and last life sciences industries that really makes sense for this technology, that the technology works well for them because of the track and trace capabilities, the footprint size and the clean system. And I'll also add that we have anti-slosh capabilities. So if you think about it, we're able to control and six degrees of freedom. And we can control the motion private profile as well. So when you're going around a bend, we can control that niche making sure that powders liquids, and granules are actually staying level as we move it about. Now, we also have hygienic and aseptic shuttles for this industry specifically, outside of those industries. We of course worked with other customers in different industries, including packaging, EV battery, CPG, cosmetics and others. But really, when we're looking at applications, you know, we're concentrating on applications that currently use indexing tables, Flexlink, or modular conveyors or more traditional track systems. That's a really good place to start, especially if you don't need as much speed but could benefit from more accuracy.
Automation World: David Greenfield 4:24
So how fast can the Acopos 6D shuttles travel? And how much weight can they carry?
B&R: Kristen Ballistrea 4:30
Good questions. So we find that when looking at Acopos 6D applications in general speed normally isn't the driver. It's usually flexibility and precision being the driving factors for applications, but that being said the shuttles can travel up to two meters per second. So load acceleration and payload can also affect the maximum speed. The weight the shuttles can carry depends on the size of the shuttle. So we have different size shuttles. Depending on what application you're looking at. Our smallest what we call our standard shuttle is 100 to one mean millimeters by 120 millimeters and can carry point six kilograms worth of weight, the payload or shell can carry is directly related to the area of the magnets or the shuttles themselves. So currently we have done applications up to 3.6 kilograms in weight, but we have shuttles size for above 10 kilogram payloads. So
Automation World: David Greenfield 5:19
How do the shuttles know where they're going when they're moving around the track and how are they controlled?
B&R: Kristen Ballistrea 5:25
So we do have full closed loop control of each shuttle. So each shuttle can be given a unique path to go where they need to go. We have a library base that supports the development of projects so that each shuttle can be controlled easily. This library base is part of what we call our fleet management solution. Through this solution, we are moving towards a code free implementation of aka 60.
Automation World: David Greenfield 5:46
This almost begs the next question, what about collision avoidance? You've got all these shuttles moving around performing different tasks on the same planar surface? You know, with them all moving in potentially different directions, you know, to handle different tasks...How is that collision avoidance handled?
B&R: Kristen Ballistrea 6:04
Yeah, I mean, this is a question that we get very regularly and for good reason, right? Nobody wants to see their shuttles in their product running into other shuttles and other product. It's definitely not something you want to occur. But the good news is that all of that collision avoidance is actually handled in the firmware. So you really don't have to do anything to make sure that that doesn't happen. It's built into the system, each shuttle is able to monitor the position of all of its neighbors. And this allows the system to manage the shuttle so that they collisions just don't happen.
Automation World: David Greenfield 6:33
So given its capabilities, it seems like this could be a complex system to work with. So given that, you know, what kind of expertise is required to install and operate the Acopos 6D.
B&R: Kristen Ballistrea 6:47
Yes, the technology is really cool. And what it does, it seems like it would be complex, however, the hardware itself is pretty simple. And it's easy to put together in design to design and to put into a machine. So the segments are actually daisy chained together for communication and power. From there, we have a power cable that connects it to the power supplies and a communication cable that connects to the PLC, the users can operate the system from a push of the button on the HMI, we use our Automation Studio software package for programming of the system. To keep things as simple as possible. This is the same software that we use for all other B&R products. We are also continuing to add to the ease of programming through coming up with ways to be more graphical and modern. So we are doing this through our fleet management solution that I mentioned earlier. Throughout the year, we will be adding some really cool features to this fleet management tool, and how we go about programming the 60. So I just say like, stay tuned for more on that.
Automation World: David Greenfield 7:42
You know, in preparing for this podcast, I did, obviously some reading up on Acopos 6D. And I saw it mentioned that the system can reduce the amount of floor space needed for materials transportation. Can you explain how that works in a typical manufacturing production application?
B&R: Kristen Ballistrea 8:00
Yes, sure. And I would say no reducing the amount of floor space, that's a key selling point of this technology as well. But if you look at the different components of Acopos 6D, you know, you have segments, and you have shuttles that 240 by 240 millimeter segments allow you to build a tabletop design, rather than like your traditional race track that you might see and track systems and standard convenience, this tabletop design can help save a lot of space, and really help you put together a unique machine design concepts. So processes and other machinery can actually go around the table or overtop of the table, creating quite a bit of space savings there. Not only that, but with the tabletop design and individual control of the shuttles. It allows for every inch of the tabletop designed to be used for processing, you can also look at the high shuttle density of the 6D system. So we can actually have up to four of those 120 by 120 millimeter shuttles on a single segment at a time. Now that would take up the entire segment. And it's a lot of shuttles on the system. Obviously, that can create traffic problems, but it is doable, we generally recommend a 50% shuttle density across the entire the entire machine. So two shuttles per segment, and still a pretty high shuttle shuttle density for the system. And it really allows you to do a lot with a very small footprint.
Automation World: David Greenfield 9:16
So Kristen, you know like any technology on the factory floor, Acopos 6D obviously has to be able to interact with other plant floor systems. So how is integration with Acopos 6D handled?
B&R: Kristen Ballistrea 9:29
Yeah, so the Acopos 6D system can be integrated into other plant floor systems just like any other piece of equipment, we can use our PLCs and our field bus controllers to connect, integrate and communicate with other systems, whether there be in our systems or not. That being said, when designing 6D systems, we find that the most successful systems are the ones in which we look at the entire system and think of the 6D as really the center of it, instead of just an average afterthought. The Acopos 6D system is integral to the machine itself. It's not just convenience. It's a smart system. has many capabilities. So with it at the center, we can simplify and eliminate other operations. For example, whereas before, you might have used convenience to move a product to a station for weighing to detect if a product is there with 6D, you can actually do that with their with the integrated weighing capabilities. So you get rid of that process step completely. By looking at 6D as the center of the system, you eliminate the need for different process steps, you can shrink the footprint and simplify the overall process. So where you can just drop 6D in and integrate to existing plant floor systems, it's best if you really look at the technology and the capabilities and design everything around that.
Automation World: David Greenfield 10:37
You mentioned that Acopos 6D can integrate with systems that are not from ABB or B&R. Can you explain a little more about how it integrates with systems from other suppliers?
B&R: Kristen Ballistrea 10:49
Sure, we can use our field bus to connect and integrate with other automation suppliers. This is a very common request that we get across all of our projects within B&R so it's very common that the in our track systems in Acopos 6D specifically is used as a smart subsystem. So that means you know we use our our track or your our Acopos 6D We use a B&R PLC but with our field bus we can connect to really any other automation supplier out there very easily. So it's a motion subsystem and and we can play well with others. That being said, there are definitely advantages to using the ABB and be in our portfolio when integrating octopus 60 or any of our other track systems. If you look at ABB and B&R, we really do have a complete automation and controls portfolio, as well as a complete robotic portfolio. We can take the robot, whether it's a SCARA, a delta or others and integrate it into the B&R PLC for simplifies simplified control and tight synchronization. We can do the same with our vision and other aspects of the machine as well.
Automation World: David Greenfield 11:50
Can you provide some examples of industrial customers who are using Acopos 6D? And by that, I mean, you know what they're using it to do and how its benefitted them?
B&R: Kristen Ballistrea 11:59
Yeah, and you know, that's one of the top questions we get. And it's a difficult one to answer sometimes. And we do have quite a few industrial customers using the technology. However many of them are under NDA right now, a lot of that is because they actually view this technology as something that gives them a competitive edge. We do have a few that are public though. One is a company called KAO in Japan. It's a cosmetics application company that does dispensing capping and labeling for custom makeup products. So they're really doing it for the batch size one and the custom products. So it's giving them the flexibility to do that. We also have Bico Group in Sweden. So this one is pretty cool. And it shows how we can collaborate with ABB robotics in the lab automation and life sciences space. So they're actually using 60 to do bio sample management with labeling and storage. The 6D automates the process simplifies the track and trace of the samples shrinks the footprint and uses all six degrees of freedom at each process step. We also have U2/Unilogo, they have a machine that's doing flexible capping for cosmetics. So once again, you hear that flexible word in there. It's really key and in applications with 6D. Outside of the few that I named, we have use cases with a pharmaceutical company, a packaging company, and actually many others. We have quite a few machines that in systems that are going public in the month of May. So if you follow us on LinkedIn or on our YouTube page, you'll actually be able to view these really cool applications we've been working on.
Automation World: David Greenfield 13:25
Well thank you for joining me for this podcast. Kristen, and thanks of course to all our listeners. And please keep watching this space for more installments of Automation World Gets Your Questions Answered. And remember you can find us online at automation world.com to stay on top of the latest industrial automation technology insights, trends and news.
Companies in this Article
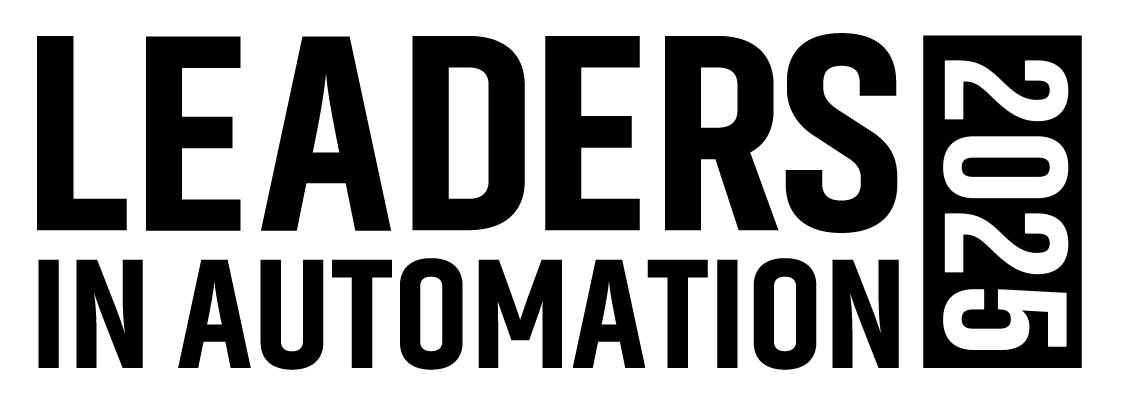
Leaders relevant to this content: