Pepsi Bottling Ventures is the nation’s largest privately held Pepsi-Cola bottler, operating 28 bottling and distribution facilities that serve more than nine million consumers across the United States. The company’s plant in Nampa, Idaho supplies four beverage-distribution centers in the Pacific Northwest and has contributed to the parent company’s successful operations with performance that ranks among the most efficient in the organization. It’s done so despite the fact that it is the smallest facility in the company’s nationwide network of bottling plants and has been in operation just five years.
One of the methods the plant uses to help it become so efficient involves the deployment of FactoryWidgets, a software package developed by Apex Software Development, a division of Apex Manufacturing Solutions in Boise, Idaho. The application is sold and supported by Software Toolbox in Charlotte, N.C. “Widgets” are simple, no-hassle and affordable mini-applications that display user-defined key performance indicators (KPIs) on desktop personal computers (PCs) without the need for thick client software or even an Internet browser.
“We’ve been using the FactoryWidgets for just a little more than two months and they’ve already been very well received by our people,” says Bacon. “They’re an unobtrusive reporting mechanism that people at all levels of technical knowledge can understand and use for monitoring real-time data for both primary and ancillary management needs.”
This is important, Bacon explains, because in the beverage industry “just to stay competitive, we have to run with leaner head count. The widgets allow us to set up both primary and ancillary tasks to run in the background right on people’s computers. When they need to check that data, they now can do it right on their screens rather than having to go out to the physical equipment, which frees up personnel time for more value-added tasks rather than occupying them with documentation and record-keeping.”
The Nampa facility is fairly typical in that it has Invensys Operations Management’s Wonderware human-machine interface (HMI) workstations on the plant floor that enable operators to interact with the production processes. Since the quality control staff works both on the plant floor and in the lab, they needed applications for both areas.
Widgets rule
If someone is out on the floor and something goes wrong, they can use an HMI console to see what’s going on and acknowledge alarms, start or stop machines or take whatever action is appropriate. While in the lab, however, they typically don’t need that level of detail or interactivity. They are collecting and analyzing running samples, filling logbooks and manually entering data into the Wonderware systems. It’s now easy for them to glance over at the FactoryWidgets screen on the lab PC. If they see something that needs attention, such as when an analog orb goes from green to red, they can click on the widget to link to more detail.
A WidgetServer is installed on the same server as the plant’s Wonderware Performance, Historian and ActiveFactory reporting systems. The data used to populate the widgets is collected primarily from the historian, which in turn gets its data from PLCs, Wonderware HMIs and Wonderware Performance reports. From that central hub, the widgets are initially served for users in the QC lab, on the production manager’s desktop and at the operations manager’s office, which is located remotely about a mile from the bottling plant.
“We started with quality control because it’s so critical to all our operations, both in terms of production operations and monitoring of environmental issues,” Bacon says. “We only have a half dozen people in the lab, which is the entire department for a factory of our size, and it saves them tremendous amounts of time. They no longer have to physically go out and check statuses such as water process settings or filling stations, but can monitor activities on-screen, right on their desktops. They can thus handle other tasks for their manager without worrying about where they are currently with a production run, so they can do a lot more developmental types of activities.” Hence the freed-up hour per day per person, he adds.
Improve audits
The Nampa facility will soon be using the FactoryWidgets to bolster its results for an annual corporate audit done by Pepsi Cola North America (PCNA) and for third-party audits done by the American Institute of Baking (AIB), which is useful in keeping customers informed about operation quality.
“Audits are becoming more prevalent in our industry and they’re getting more complex, so we think the FactoryWidgets definitely can play a role,” Bacon says. “Auditors always want to see more detail about not only the physical steps in a procedure, but how well you can verify that you’ve fulfilled the process.”
For example, they can now easily show in real time that the rinsing system is indeed activated through bottle stop engagement or disengagement. Having such a good visual presentation for an auditor or a customer helps them understand exactly what’s going on in the factory so they don’t have to be familiar with specific production operations, yet they can get a quick snapshot of what goes on.
“For a plant as small as ours, these types of tools are invaluable and since we have the right personnel, we’ll have the right types of tools we need to accomplish a lot without having to invest large amounts of capital,” says Bacon. “And that should help us stay one of the top plants within Pepsi Bottling Ventures.”
This process is part of a process or an application known as enterprise manufacturing intelligence (if linked to enterprise systems) or sometimes just as manufacturing intelligence. The online encyclopedia Wikipedia.org defines EMI as “a term which applies to software used to bring a corporation’s manufacturing-related data together from many sources for the purposes of reporting, analysis, visual summaries, and passing data between enterprise-level and plant-floor systems. As data is combined from multiple sources, it can be given a new structure or context that will help users find what they need regardless of where it came from. The primary goal is to turn large amounts of manufacturing data into real knowledge, and drive business results based on that knowledge.”
Improve performance
Paul Brice, who heads global marketing for the solutions business for Honeywell Process Solutions in Phoenix, defines the EMI space as a “solution area primarily in the manufacturing execution and collaborative production management space. Our solution came primarily with the Matrikon acquisition, combined with what we were already doing with Microsoft-based service-oriented architecture (SOA). The first part of the process is connectivity into the data. The second one involves abstracting the data and providing visualization.”
Brice cites the example of JoutCon Oy, one of Europe’s newest providers of board and paper sheeting services, which deployed Honeywell’s OptiVision manufacturing execution system (MES) at two of its production facilities to improve overall performance and maximize operational flow. Since the plant was new, it wanted assurance that it could meet both current and future paper and board industry requirements.
And, in fact, the JoutCon facility was able to upgrade and improve in several areas that included order processing and planning; sheet production and tracking; pallet labeling; inter-facility communication involving production lines, warehousing and delivery; process efficiency; cost of tracking production results; and reporting.
Founded in 2007, JoutCon Oy provides a wide variety of board- and paper-based remote sheeting services for the board and paper industry. The company, which is headquartered in southeastern Finland, produces 25,000 tons a year via a pair of production lines.
“Starting from scratch, we at JoutCon Oy had many options for building our production process,” says Tapani Lautamies, paper engineer and managing director. “We needed a partner that could distinguish itself immediately, and recognize our situation and the particular needs of smaller plants.” JoutCon was not only interested in getting its business off to the best possible start, but also remained keenly focused on implementing a company-wide strategy that would permit seamless growth, diversification and integration with its main contractors in the paper and board industry.
Lautamies says JoutCon found a partner that met its needs in Honeywell Process Solutions; one of Honeywell’s major strengths is the ability to adapt its offerings to customers’ specific needs. “We operate qualified production with very short production time,” he explains. “This requires high-quality processes in order to meet our demands for top-notch order management, production planning and reporting.” Honeywell’s OptiVision MES optimizes production, fixed costs and variable costs by maximizing manpower requirements, allocating fixed assets, managing working capital and prioritizing capital spending. OptiVision provides planning and execution at the corporate level and full manufacturing execution at the mill level.
The partners are so pleased with their relationship that JoutCon and Honeywell will take on a new challenge together. JoutCon plans to implement Papinet standard messages to communicate with its suppliers as well as with board and paper mills. The implementation of automatic order receiving and order status reporting will help the mills communicate order and production status while keeping production lines operating at proper efficiencies.
Honeywell’s Brice concludes, “For me the two big things about EMI are first not to underestimate content that comes from applications. It’s not just data to dashboard, but also human interaction around applications that captures a lot of knowledge. Then, second, realize trying to fill space between ERP and MES is still a challenge.”
It takes a village
Just as the Pepsi bottling plant saw the need to use manufacturing intelligence tools to have better preparation for quality audits, one pharmaceutical coatings supplier also needed a better way to provide waste treatment reports to the township. Alex Jushchyshyn, plant support engineer with Colorcon, a provider of formulated coatings and other excipients for the pharmaceutical and dietary/food/nutritional supplement industries, assembled a team to accomplish the project. It consisted of an application specialist from Milwaukee-based supplier Rockwell Automation; Rumsey Electric, a Rockwell distributor in Consohocken, Pa.; and process industries system integrator EZSoft, based in Malvern, Pa.
Jushchyshyn describes the situation: “The project was data collection regarding the waste treatment process in our West Point, Pa. plant. We needed proper reports to the township. We developed schemes of how to collect data in an efficient manner. High availability of the data is a must. Manual data collection had to be limited. Operators should be running the plant not running around with clipboards.”
The project started in 2010. “Our networking is fairly integrated, so we figured we should be able to get data at the desk,” says Jushchyshyn. “What we needed included one-click reporting, no data manipulation to get summaries, and more. The other big piece—the system had to be expandable. We needed to work with the IT group to understand the networking requirements so that people in various locations, from headquarters to the production plant, could all see the information. It also had to enable us to meet regulatory requirements.”
Jushchyshyn reports he has a good relationship with Rumsey Electric. The plant is standardized on Allen-Bradley brand products from Rockwell, and Rumsey has Rockwell-qualified people on staff, excellent facilities and insight into local integrators. “Our engineering group consists of just three people,” Jushchyshyn explains. “We can’t do it all ourselves.”
Marty Fallon, EZSoft vice president of sales says, Colorcon was looking at a single application, “but they needed it to be a global system. As the integrator, we worked with Tim McCain, Rockwell Automation industrial software regional manager, and the distributor and customer. We produced system architecture drawings and functional specs. The scope of the project included integrating Rockwell’s FactoryTalk Historian and VantagePoint software, compiling trend and daily reports, and upgrading some other systems along with AssetCenter.”
Jushchyshyn says that “a year later, it feels like we’re partners. We chose wisely, so we now have a very good integrator to call on and know we’ll get the right thing.”
The hardware architecture he describes as an instrument probe feeding data to a local PLC and a local display. Next the data goes to a corporate server some seven miles from the facility. The system includes DIN-rail mounted industrial PCs and Cisco Ethernet switches. “We have our own VLANs, so there are no collisions with our IP telephones. We had to balance our engineering requirements while satisfying the needs of IT. Our engineering group keeps track of eight servers—more than any other department outside IT,” he says.
In the end, Fallon says VantagePoint allows data to be presented from disparate systems and databases on one platform. Adds Jushchyshyn, “That was the real benefit. I could direct users to one interface for everything. I focus on things from an engineering perspective, but my bosses may not be as technical. So I wanted that single click where they can get the information they need. In fact, this is probably the first software package where I got what I asked for. I had five key points and got them all.”
Context is key
Dan Roessler, production management and execution suite manager of AspenTech, Burlington, Mass., a supplier of advanced process software, says contextualization is the key in EMI. The company’s KPI Builder allows customers to take information and put it into a meaningful form, relieving the user of the need perform an individual analysis. It’s also useful for performing overall equipment effectiveness (OEE) calculations and some preventative maintenance types of activities, such as telling earlier than usual when equipment will be failing.
Jeremy Suratt, product manager mobile at AspenTech, adds, that the company took a look earlier last year at how to enable customers to access more content more easily. “There is demand out there for instant gratification—getting access to information you use on daily basis faster, say on your smartphone,” says Suratt. “We’ve developed a couple of different apps. The product is new, but a number of customers are currently evaluating it. The reception is tremendous so far.”
Maryanne Steidinger, director of advanced application software at Invensys Operations Management in Lake Forest, Calif. defines EMI as “how to provide information that makes sense.” She adds it’s one thing to provide Web-based reports, but to make it so you can run not only operations but business is the key benefit. Another benefit comes from tying EMI to workflow. “With real-time information and workflow applications, you can actually do closed loop remediation.”
The definitions from industry insiders continues to point toward how EMI helps manufacturing leaders do better jobs running their plants. Chuck Pharris, senior director for manufacturing solutions marketing at SAP in Chicago says, “It’s not just about manufacturing execution, but it’s where the plant meets the world. In fact, it’s not just integrating a plant, it’s from idea to delivery—integrating the supply chain.”
Frank Platt, senior director for line of business manufacturing at SAP, adds, “The value proposition surrounds integration of all the systems for performance management and continuous improvement so operators and management can take action and drive key performance.”
Joe Rothman, Aegis Analytical chief technology officer (CTO) in Lafayette, Col., says, “Ten years ago, data access was a problem. Today, that’s pretty well handled due to numerous products and standard protocols. The key right now is bringing the data together, analyzing it and communicating. We look at this area as a set of concentric circles from business intelligence down to manufacturing intelligence, then to what we call process intelligence (PI). Specifically, PI produces sets of reports and analyses around KPIs, dashboards and portals that allow people to monitor how the process is going. Trouble is, KPIs don’t necessarily fix things. In a complex operation, they might tell you what happens, but not why. So overall, there is need to look at critical parameters that drive overall process and add that to the mix.”
Tadeusz Dyduch, product manager for manufacturing intelligence at Apriso, a Manufacturing Execution System (MES) supplier in Long Beach, Calif., says, “Customers want something homogeneous, not different pieces of software easy for IT to maintain. Most of our customers are automotive and consumer packaged goods manufacturers. People working there need to know how they are performing: indicators of quality, delivery and other metrics with some analysis of the why behind the numbers. Others need to be informed, but not constantly. Just prompted.”
Dave McCarthy, president of systems integrator TriCore in Racine, Wis., summarizes: “A company cannot improve performance unless it can measure it. EMI lets users gather information from disparate sources and fulfill any number of obligations to decision-makers within the enterprise, as well as customers who look to the company to deliver its brand promise.”
September 2011, How EMI Software is Helping Companies Dig
To read the feature article, visit www.automationworld.com/feature-929
Aegis Analytical (www.aegiscorp.com)
Apex Software Development (www.factorywidgets.com)
Apriso (www.apriso.com)
AspenTech (www.aspentech.com)
EZsoft (www.ez-softinc.com)
Honeywell Process Solutions (hps.honeywell.com)
Invensys Operations Management (iom.invensys.com)
Rockwell Automation (www.rockwellautomation.com)
SAP (www.sap.com)
Software Toolbox (www.softwaretoolbox.com)
TriCore (www.tricore.com)
Companies in this Article
Sponsored Recommendations
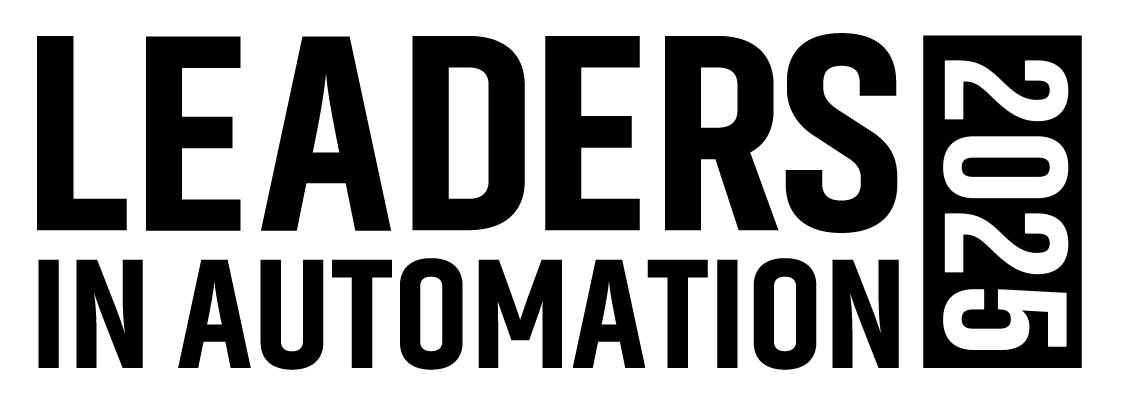
Leaders relevant to this article: