FT1A SmartAXIS Touch All-in-one HMI + PLC Takes Aim at Analog Applications
A human machine interface (HMI) connected to a separate programmable logic controller (PLC) is the standard system for machine automation. However, combining PLC processing and HMI monitoring and control into a single hardware platform is becoming a more available and popular option due to improvements and advancements in both hardware and software. This article compares the combined HMI+PLC unit with the separate HMI & PLC system and highlights where each excels.
Hardware Comparison
For decades, the separate HMI & PLC system has set the standard for industrial automation. It has only improved with time and remains an excellent choice for many applications. But in the past few years the combined HMI+PLC unit, with its all-in-one touchscreen interface and logic controller, has become available. It’s often a viable option for control and monitoring of smaller machines, process skids and HVAC systems.
With expanded analog I/O, temperature control, PID control and remote I/O capability, combined the HMI+PLC unit offers competition to the standard separate HMI & PLC systems.The components in the combined and separate options are industrially hardened and built to last. Each configuration is packaged to work well together, even though the separate HMI & PLC system is not physically combined into a single housing
The combined HMI+PLC unit has physical size benefits as it will always take up less panel space than separate units. The combined HMI+PLC unit also minimizes wiring because no connections need to be made between the HMI and the PLC, a single power source powers both the HMI and PLC, and only one network connection needs to be made to the outside world.
Separate HMI & PLC systems have extensive processor selections available with large memory capacity, well beyond what’s available with combined HMI+PLC units. However, more advanced combined HMI+PLC units have many of the data storage, math functions and string functions of separate HMI & PLC systems.
Software Solutions
In terms of the PC-based software packages used to program these platforms and systems, both combined and separate units are merging the HMI and PLC programming features into a single integrated package or all-in-one configuration software. These suites of software integrate the PLC programming software, HMI development software, and system configuration software in a single development environment.
Although progress is being made towards integrated development environments, in many cases programming software for separate HMI & PLC systems isn’t available as an integrated solution. Typically the same tag name database is shared, but the programs are physically separate for the HMI and PLC.
The combined HMI+PLC unit tightly integrates the HMI and PLC programming into a single suite of software. While well integrated, the PC-based programming software can still be two separate programs integrated together with configuration software.
The separate HMI can be one of two types. The first is a PC-based platform running third-party HMI software. This software can be either internally developed, or it can be purchased and configured. The second separate HMI type is an operator interface terminal, where the PC-based programming software is supplied with the terminal. The PC-based solution is more powerful, but it’s also more expensive and takes up much more space.
The PC-based HMI solution sets the standard from an operator interface standpoint with its wide variety of features, functions, options, sizes and display resolutions. The operator interface terminal solution is comparable to that found with the combined HMI+PLC unit.
Like the operator interface terminal, the combined HMI+PLC unit includes the animated screens, alarm display screens, message functionality, trends and bar graphs required to create a professional interface suitable for small-scale industrial automation applications.
Combined HMI+PLC units cut programming time as the single package eliminates the need to integrate the HMI to the PLC. The communication and configuration parameters are already setup and usable out of the box, while separate HMI & PLC systems must still be configured and handled to establish communication.
Both combined HMI+PLC units and separate HMI & PLC systems include the hardware and software to be successful in a wide variety of industrial applications, and both also have what it takes to connect to internal and external I/O, and to other devices.
Making Connections
With its long history, separate HMI & PLC systems provide strong external device integration, I/O, and communications options. Vendors provide a full range of analog, discrete, motion control and specialty modules to meet the needs of most any application. These modules are typically part of a local or remote I/O chassis.
Combined HMI+PLC unit has device and I/O options suitable for many applications, but more limited than separate HMI & PLC systems. However, the focused connections of the combined HMI+PLC units can provide a cost-effective option for small machines and systems, particularly those with limited I/O counts and no need for high-end functions such as motion control, vision system processing and robotic control.
Temperature inputs and PID capability are available in both combined platforms and the separate systems as is high speed I/O, but the HMI & PLC system option typically has a better selection of input types and higher I/O count. And while the combined HMI+PLC units typically have-high speed discrete inputs and outputs, separate HMI & PLC systems add extensive motion control capabilities and other advanced functionality.
There is an extensive range of communication options available with separate HMI & PLC systems, particularly when the HMI is PC-based. The combined HMI+PLC unit typically includes more limited connectivity, but often sufficient as RS232C/RS422/ RS485, USB, and Ethernet ports are usually provided.
Combined Unit Fills the Bill
There is significant overlap where the combined HMI+PLC unit and separate HMI & PLC system both provide a suitable automation solution. With smaller applications, the combined HMI+PLC unit has the advantage because it costs less, takes up less panel space, and takes less development time.
Good applications for the combined HMI+PLC unit include simple pump control, remote wells and booster stations, small process skids in oil and gas, and small compressor, chiller and refrigeration equipment. Small OEM machines and packaging equipment are also good applications for the combined HMI+PLC.
A bag filling machine or station is used to fill industrial bags with various types of materials. These bags are typically used to ship large amounts of product to other businesses, and are generally not suitable packaging for direct shipment to consumers or retail outlets.
The combined HMI+PLC provides the automatic cycle and process control required for a bag filler. The automatic cycle can free up the operator to tend to other plant operations. Once the operator attaches the bag, inflation of the collar/seal, feed system and material flow can be automated using the combined HMI+PLC unit.
Variable fill rates and impeller speeds can be controlled by the HMI+PLC based on readings from an electronic weigh scale. These readings can be transmitted through the scale’s analog output, and further information from the scale can be transmitted to the HMI+PLC through a digital data link such as Ethernet. Ultrasonic sealing can also be monitored and controlled.
The combined HMI+PLC unit provides a simple yet sufficiently capable integrated control system with an HMI for system status, recipe selection, manual control and fault message display. The HMI also allows fine tuning of the fill, densification and weighing processes to improve efficiency and performance.
With its discrete I/O and communication options, the combined HMI+PLC can control indexing and accumulating roller conveyors, and can provide interlocks to upstream and downstream material handling equipment. If required, encoders can be monitored and stepper motors controlled for the accurate positioning often required for material handling systems.
Although the combined HMI+PLC unit is a good fit for this bag filling machine, it’s clear the separate HMI & PLC system provide the greatest range of options, making it a better choice for large-scale applications such as this web conversion line.
Complex Machine Requires Separate System
Materials such as paper, plastic film, foil and cloth are usually produced in long, continuous sheets which are rolled to facilitate handling and transportation. Web converters take these continuous rolls of thin, flat materials (webs), thread them though processing machines, and convert or change the web to an intermediate form or final product.
This web converting line unwinds a thin film solar material and converts it into individual solar cells, tests the cells for efficiency, and then sorts the cells based on performance as measured by the test. The individual cells are then assembled into solar strings and packaged for commercial use.
It includes multiple axes of motion control to provide roll unwind, tension control, and precision indexing for use with laser etch, dispense, shear, final test and sort processes. This application also required Ethernet communication to an etching laser, two robots and three cameras. A separate HMI & PLC system was selected to control the processes due to the required precision motion, communication to vision systems and robotic part handling.
Upstream, this web converting line included a servo drive unwind system controlling tension in the web, and a second servo providing web edge alignment. The unwind servo followed the downstream cut-to-length system. The line was required to hold a high precision tension, control the web edge position, and accurately index the web material—so high-end precision motion control was required.
Just downstream of the unwind, the edge alignment servo positioned the edge of the web within the field of view of the laser and web find camera. Using generic Ethernet/IP, the camera was triggered, inspected the product, and provided the product position to the laser. The laser adaptively etched the edge of the product as part of the process, and once etched, the web was indexed.
Downstream, the product was found again using a camera triggered via Ethernet/IP. The web position was then communicated to the PLC and forwarded to a dispense robot to provide vision-guided dispense of an adhesive material.
Precision indexing and a high speed sensor were used to provide accurate and repeatable cut-to-length capability at the shear. Once sheared, an outfeed conveyor servo indexed the sheared product to a vision inspection system. After the product was dimensionally inspected, the product position was sent to a robot which was triggered to pick up product and place it in a tester. Following test, the product was robotically picked from the tester and placed in one of 12 sorted positions or in a reject bin, depending on the test results.
All of these operations were coordinated by the PLC, and all were monitored and controlled from the HMI which included machine status, set point adjustment and fault messages.
Conclusion
Combined HMI+PLC units and separate HMI & PLC systems each have their strong points. The separate system has the widest selection of configurations and processing power, setting it apart from most combined units. However, for small equipment and processes, combined HMI+PLC units should be considered because of their lower costs, smaller form factor and integration advantages.
>>For more information on this product, click here.
Latest In Home
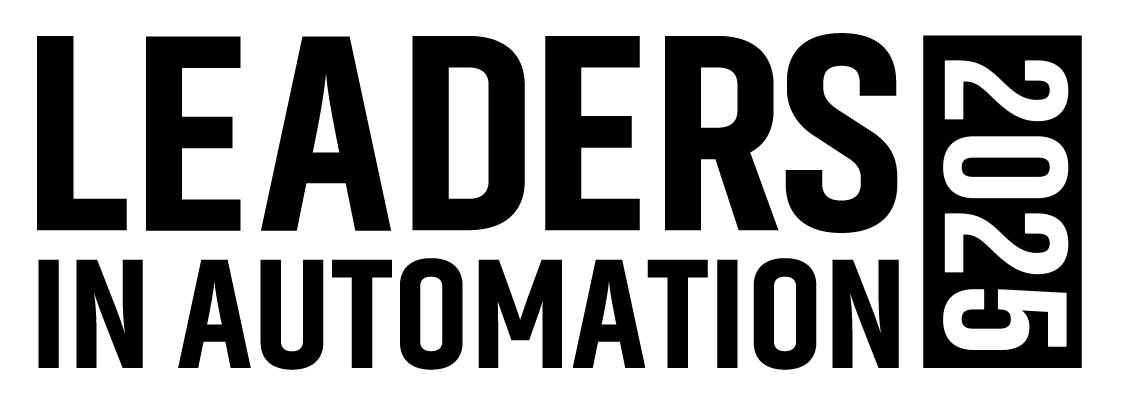
Leaders relevant to this product: