Pilz is expanding its portfolio for safe monitoring of brakes on vertical axes. Depending on the specific application and operating mode, various solution approaches are available, combining safety and economy. The offer ranges from a pure brake test and control of two high-performance holding and safety brakes through to redundant fall protection in accordance with Cat. 3, EN ISO 13849-1.
Complete, needs-based solution for risk reduction
Pilz offers two different types of solution for safe motion monitoring on gravity-loaded axes, based on the requirement: the safe motion solution PMCprotego DS combines a servo amplifier and safety card, guaranteeing a high level of safety for the user through various motion, stop and brake functions. Then there's the newly developed stand-alone safety relay PNOZ s50. It provides safe control and monitoring of two holding brakes or safety brakes. Both are designed up to PL e of EN ISO 13849-1 / SIL CL 3 of EN/IEC 62061 and can also be combined if necessary.
The potential hazard from gravity-loaded axes does not just depend on whether the operator is inside or outside the access-protected area. Inside the protected area there is an additional need to distinguish between "full" and "partial" presence, as well as between a brief and lengthy exposure beneath the load. Ultimately the manufacture must establish the required safety solution in advance by carrying out a risk assessment for each application.
A prerequisite for this is to determine the required Performance Level (PL); this is an obligation for each machine manufacturer in accordance with the Machinery Directive. It makes a statement about the degree of possible harm, the frequency and duration of exposure to the hazard and the measures required to reduce risk. It must take into account not just an emergency stop but also "Automatic" and "Setup" modes, with their respective safety functions.
Plug-in card with eleven safety functions
To enter an access-protected area when gravity-loaded axes are present, a cyclical brake test in accordance with Cat. 2, EN ISO 13849-1 must be carried out before the guard locking device is deactivated. This task is performed by the safety card in the safe motion solution PMCprotego DS, by initiating an additional load on the brake with 1.3 times the torque. This "Safe Brake Test" (SBT) is performed once in each production cycle or only every eight hours, depending on the risk assessment.
SBT is one of a total of 11 safety functions on the plug-in card. These include "Safe Brake Control" (SBC) and "Safely Limited Position" (SLP), which are used to monitor end positions. Both of these, together with the "Safe Brake Test" (SBT), are among the relevant safety functions for vertical axes. They go far beyond the "Safe Torque Off" (STO, removal of power) function that is integrated within the controller and significantly increase both safety and the plant's availability. Other integrated safety functions, which primarily concern setup, are "Safely Limited Speed" (SLS), "Safe Direction" (SDI) and "Safely Limited Increment" (SLI). Others, which mainly refer to process intervention, involve "Safe Operating Stop" (SOS), "Safe Speed Range" (SSR) and general measures such as "Safe Stop 1 and 2" (SS1 and 2).
All these functions meet the requirements of the Machinery Directive in accordance with IEC 61800-5-2 and are designed up to PL e of EN ISO 13849-1 / SIL CL 3 of EN/IEC 62061. Thanks to broken axis monitoring, the safe motion solution PMCprotego DS has an external encoder specifically so that mechanical fault exclusion is not required. The possibility of the vertical axis starting up while the safety gate is open is reliably prevented.
Safe control of two holding brakes
If there is only a low risk of hazard and the exposure time beneath the vertical axis is short, a safe brake test is sufficient. However, if the operator's whole body is completely underneath or the exposure time is considerably longer, a redundant fall protection device in accordance with Cat 3 of EN ISO 13849-1 is required both in automatic mode and during setup. As there is usually only one brake present on the axis or on the motor, then a second brake must be integrated and controlled simultaneously.
With the new safety relay PNOZ s50, Pilz provides a very efficient solution for safe brake control (SBC) for a case such as this. What's special is that the PNOZ s50 can control two holding brakes and/or safety brakes simultaneously, including brakes from different manufacturers. So there's no need for an additional control system and its corresponding wiring; but that's not all: the new safety relay can also be used to retrofit existing brakes. The safety relay is also equipped with a feedback loop to monitor the position of external brakes (open/ventilated).
The combination of the safety relay PNOZ s50 and the safe motion solution PMCprotego DS gives users a safe, overall solution, which combines functions such as safe brake test, safe control of high-performance brakes and cyclical function check of the brake's open position. In combination with PNOZ s50, PMCprotego DS monitors the drive-integrated safety function and simultaneously controls an external brake. As such the solution represents an intelligent, very efficient combination for all applications with the very highest safety requirements on vertical axes. Thanks to the high output current of 4.5 A, which is available at both outputs when the supply voltage is 24 VDC, it is now possible to control even high-performance holding brakes and safety brakes for heavy loads. Even peak currents of up to 6.5 A can be covered if necessary.
High energy efficiency due to reduced cycle times
As well as offering a high level of safety due to a fast shutdown of the power circuits, the PNOZ s50 also provides the option for a slow shutdown - depending on the control of the inputs. As a result, PNOZ s50 considerably reduces the brakes' switching noise. This is particularly significant in areas such as stage technology, where the background noise pollution should be as low as possible.
In order to reduce the cycle times and therefore improve the brake's energy efficiency, Pilz uses pulse width modulation to switch quickly between overexcitation voltage and a lower coil holding voltage.
Contactless and therefore non-wearing technology is also new. It reduces the reaction time and thus improves personal protection considerably. Just like other developments in the PNOZsigma range of safety relays, PNOZ s50 has a rotary knob to navigate through the menus and to set the required parameters. This saves time during setup, as neither a PC nor a software tool is needed.
Pilz is adding energy-efficient servo technology to its range of solutions for safety functions in the field of motion. In conjunction with an optimum design for the application, it is particularly energy-saving due to the high efficiency factor; in many applications it even exceeds the requirements of the international efficiency class IE 4, as specified by the standard. The servo amplifiers PMCprotego DS in conjunction with the synchronous servo motors PMCtendo SZ form the basis. They blend seamlessly into the flexible safety concept for complete solutions on vertical axes.
>> For more information on these products, click here
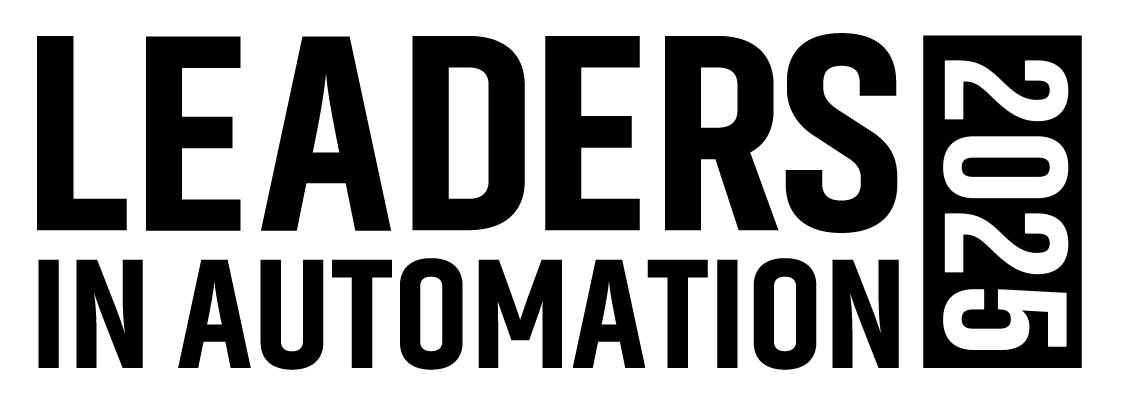
Leaders relevant to this product: